Having made a name for himself as a guillocheur, Joshua Shapiro has taken things a step further with the launch of the Resurgence, the most thoroughly American-made wristwatch since 1969.
The Resurgence offers several features that are unique within the increasingly crowded field of high-end independent watchmaking. It is a customisable product that offers an almost unlimited number of dial, case, and movement combinations; it’s possible that no two watches will be alike. Almost every aspect of the watch, from the elaborate guilloche dial, engine-turned case, and customisable in-house movement, is surprisingly interesting and original.
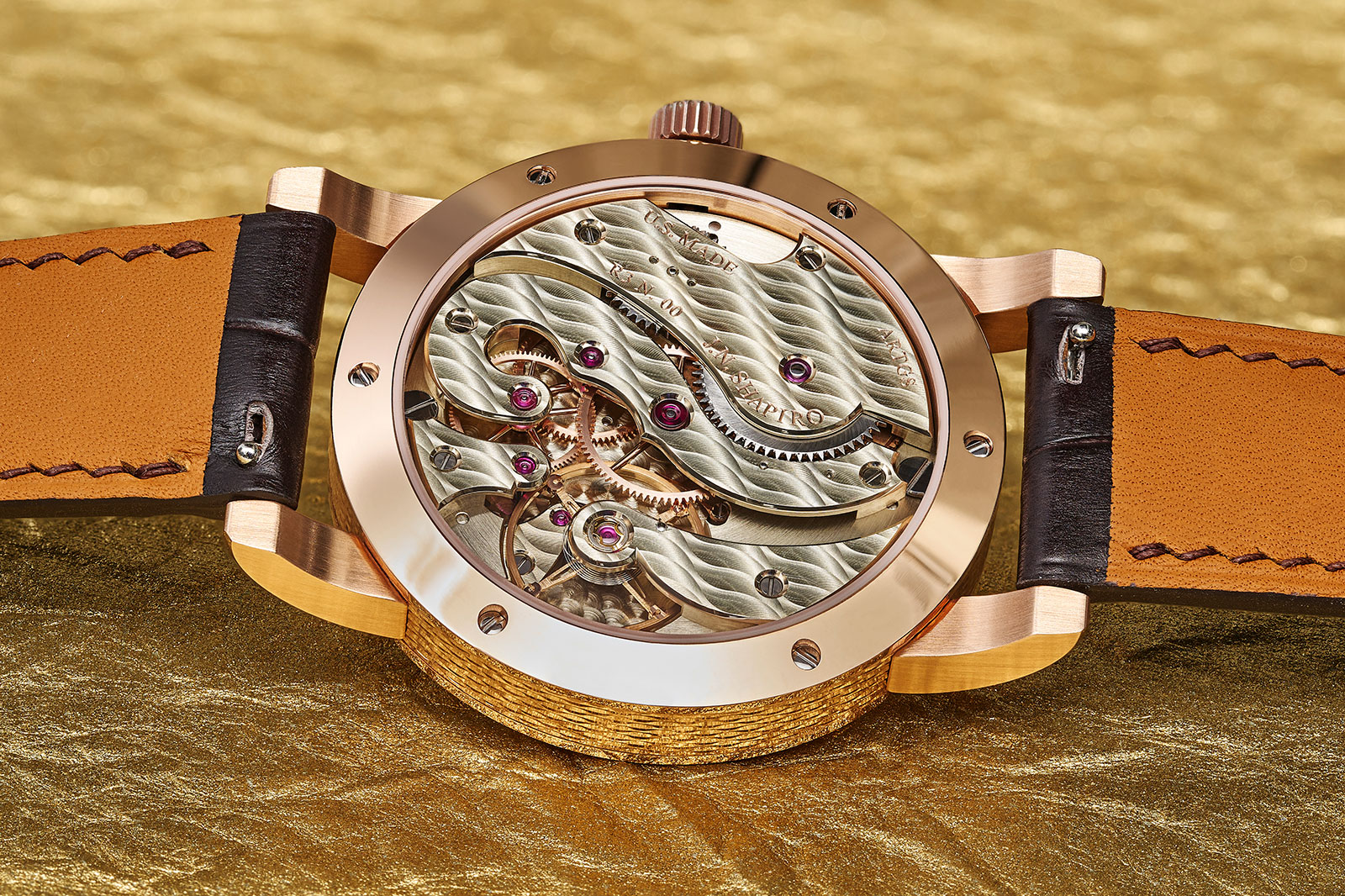
Initial Thoughts
I first met Joshua in 2019 after the launch of the Infinity Series, and even then he was keen to discuss his vision for creating an in-house American-made movement that would live up to the quality of his guilloche work. But I must admit the Resurgence has exceeded my expectations, especially in terms of finishing.
As a guilloche specialist, Joshua does not disappoint with the multi-part guilloche dial. Its construction reminds me of the dial found in the Roger W. Smith GREAT Britain, a one-off watch made in 2015 for the British government’s tourism campaign of the same name. But while the construction is similar, the Resurgence dial possesses its own aesthetic that steps out from the shadow of Swiss or British-style guilloche.
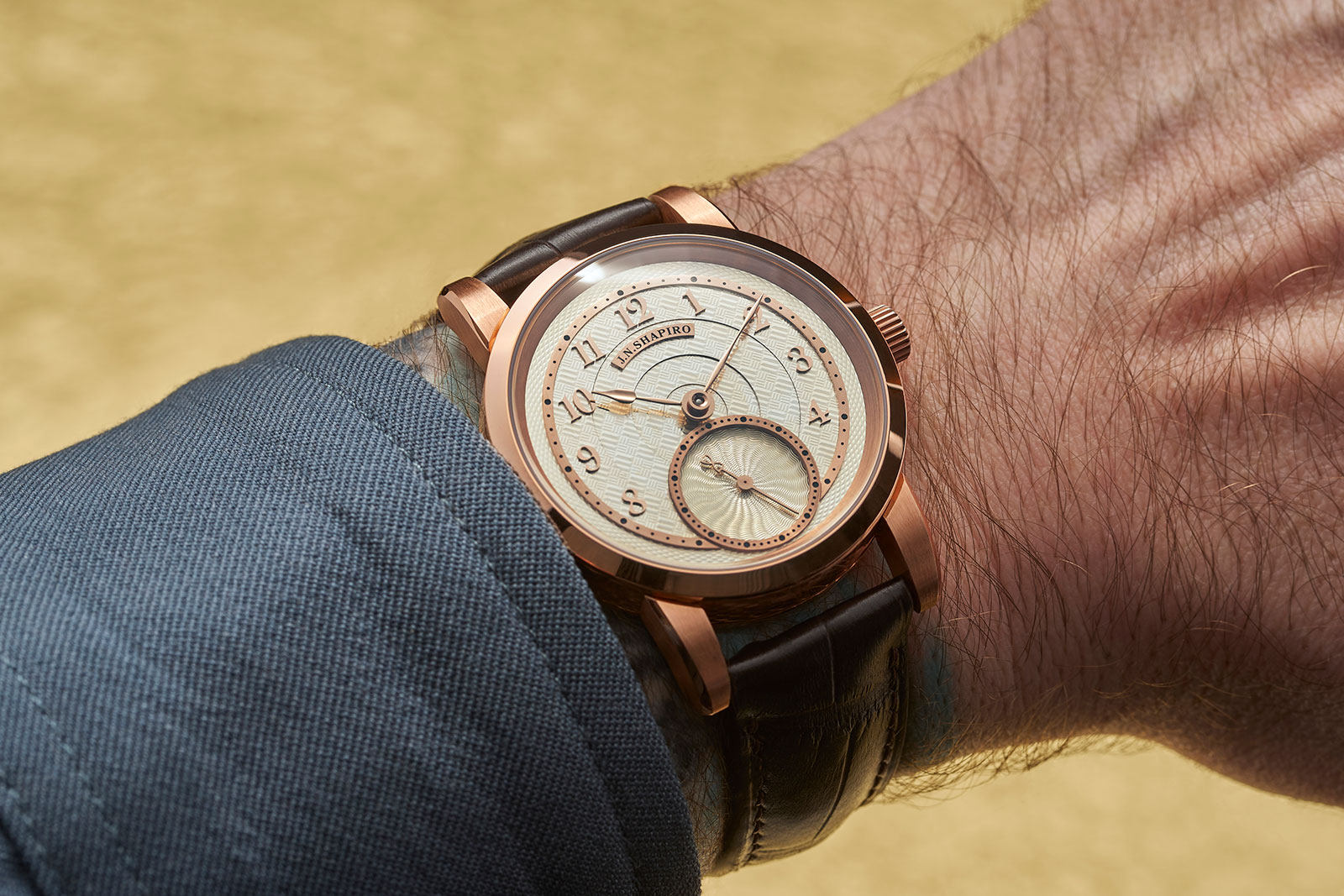
At US$85,000 in gold and US$70,000 in steel, the Resurgence is priced at the upper end of the spectrum for high-end, artisanal time-only watches. This is partly justified by the customisable nature of the guilloche work on the dial and case and costly American labour. On average, each Resurgence requires in excess of 300 watchmaker-hours to finish.
Within the context of American watchmaking, the price put the Resurgence between the time-only watch of Oregon-based Keaton Myrick and the Pennsylvania Tourbillon from RGM, which has been the standard-bearer for high-end American watchmaking since the 1990s. But the Resurgence arguably takes the concept of “Made in America” slightly further than its peers, making it an impressive and investment-heavy achievement that arguably justifies the steep price.
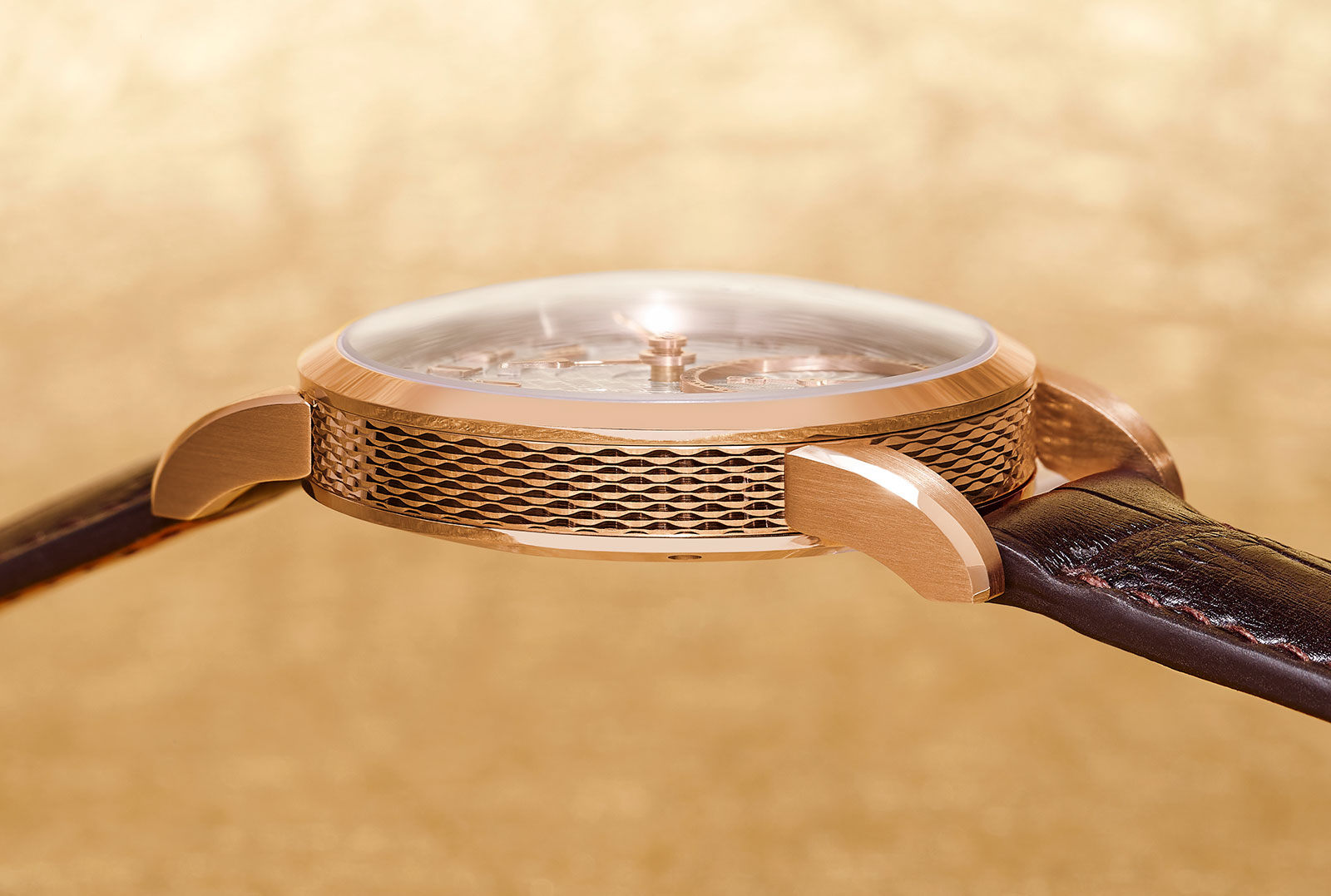
American made
Once a watchmaking powerhouse that forced the Swiss to adopt mass production, the American watch industry started to fade in the early 20th century, ultimately dying out when the Hamilton watch factory closed in 1969. Over the last 30 years, there’s been a renewed interest in making mechanical watches domestically. Several American watchmaking firms have sprung up, the first of which was RGM, founded in 1992 in Pennsylvania (near the old Hamilton factory).
But because the industry was dormant for such a long time, there remains an absence of domestic suppliers for many key components. For this reason, contemporary American watchmakers tend to rely on at least some Swiss components, especially for wheels, pinions, and escapement components. For the Resurgence, it was important to Joshua and his team to make these components in-house.
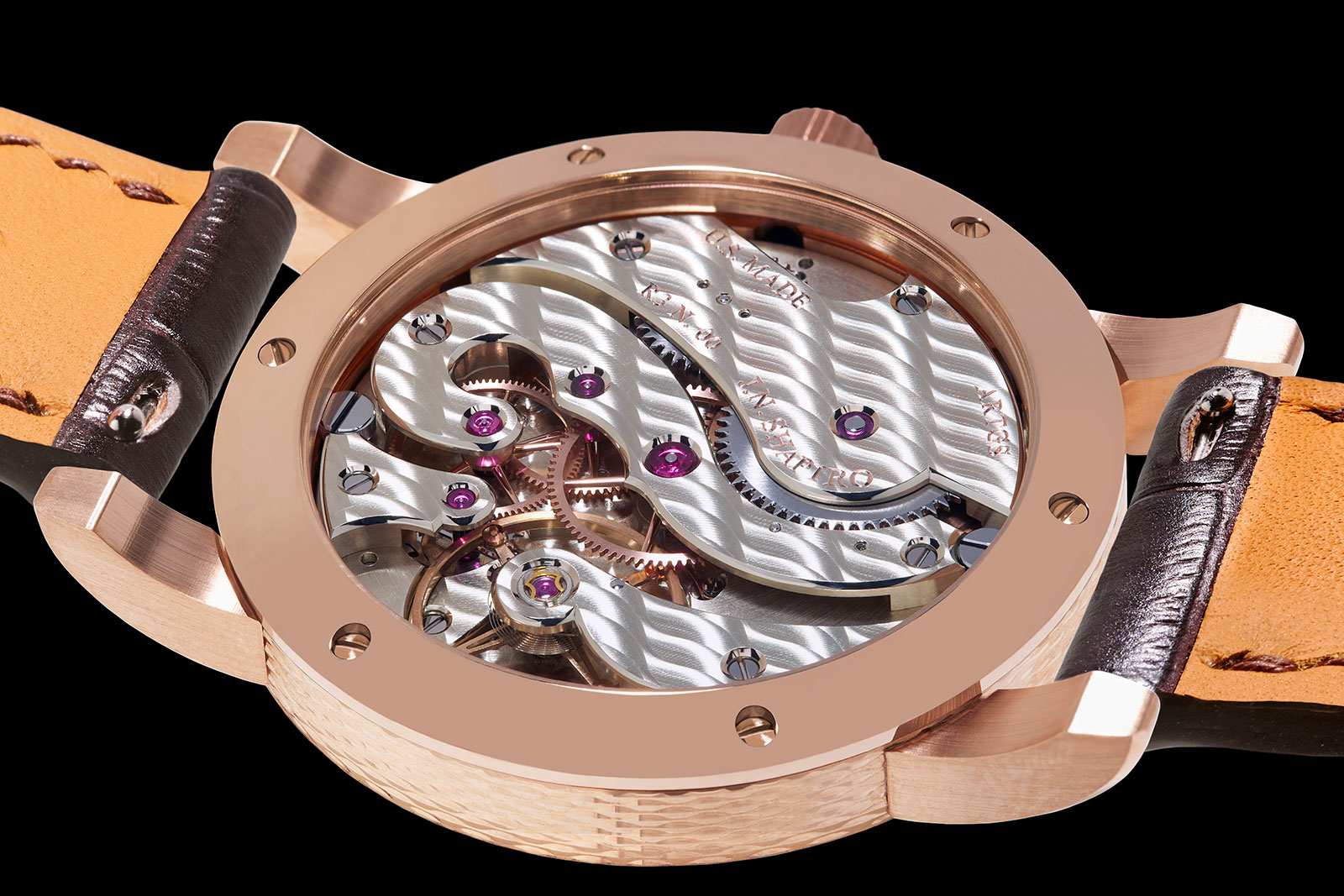
J.N. Shapiro includes an itemised breakdown of the origin of each of the 180 components used in the watch – 148 of which are currently produced in-house – making the Resurgence the most transparently and comprehensively American-made watch since Hamilton shut its doors. The percentage of US-made components is likely to increase even further by the time of production, since the brand is currently evaluating domestic suppliers for jewels (which constitute the bulk of the imported parts count).
It’s worth noting that the “US Made” label is one of the most stringent in the world, requiring “all or substantially all” of the components to be made domestically. In comparison, “Swiss Made” only requires 60% of the manufacturing costs to be incurred in Switzerland. For this reason, many prominent Swiss watchmakers view the “Swiss Made” label as too nebulous. In this context, meeting the requirements to be “US Made” is impressive.
Maximalist guilloche
As expected from J.N. Shapiro, the fine guilloche work takes centre stage. Naturally, the brand’s signature micro-basket weave pattern, known as the Infinity Weave, is featured prominently on the dial.
The elaborate dial is composed of 20 individual components, each of which can be customised to the owner’s taste. The dial components can be engraved with different guilloche patterns, or a single pattern that runs across the different layers.
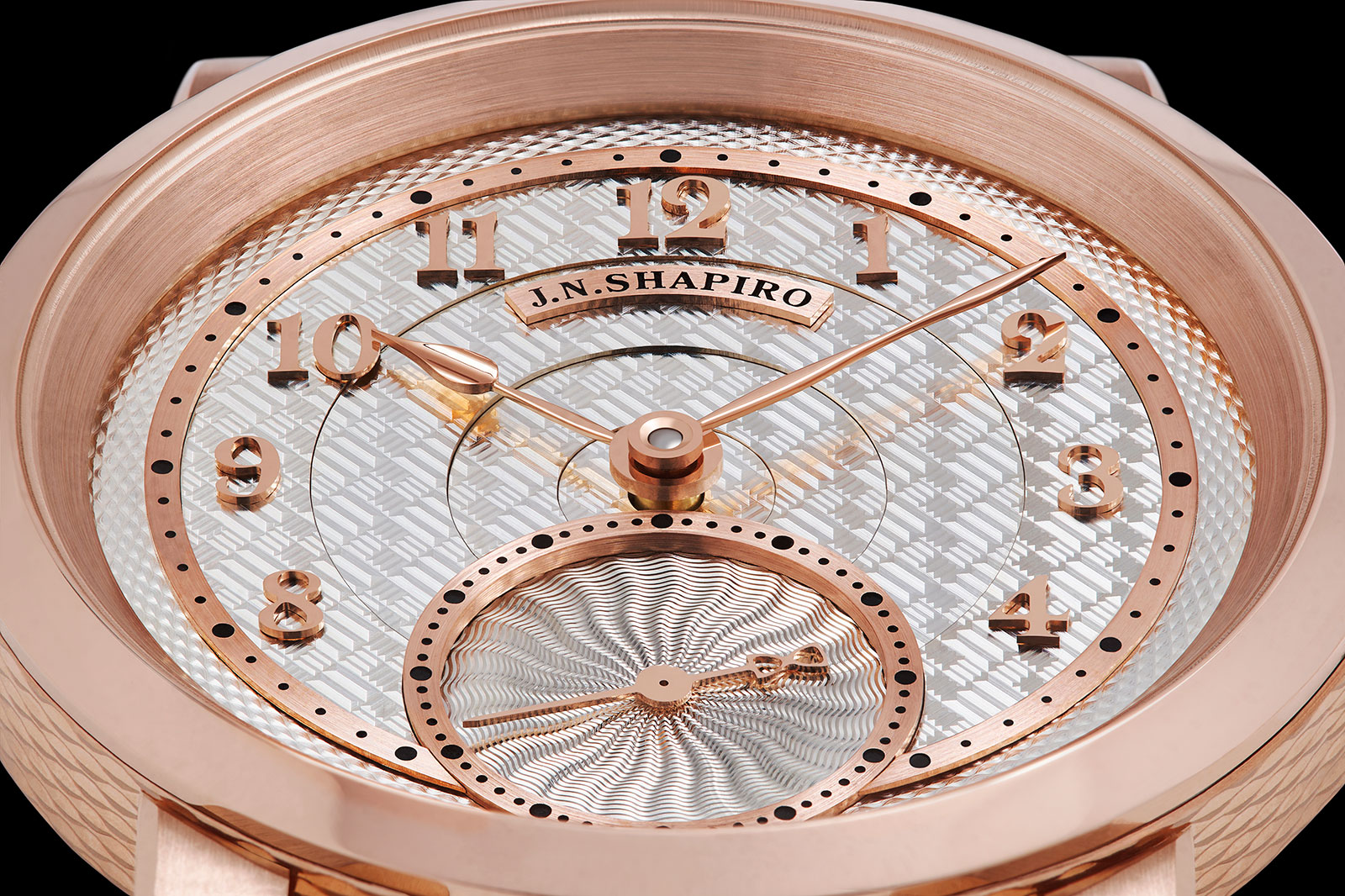
It may seem counter-intuitive, but the single-pattern dials are far more challenging because any misalignment between the concentric layers would be immediately obvious. In order to ensure that the patterns start and end in exactly the right place to align with the patterns on the adjacent layer, each layer is painstakingly aligned down to one micron.
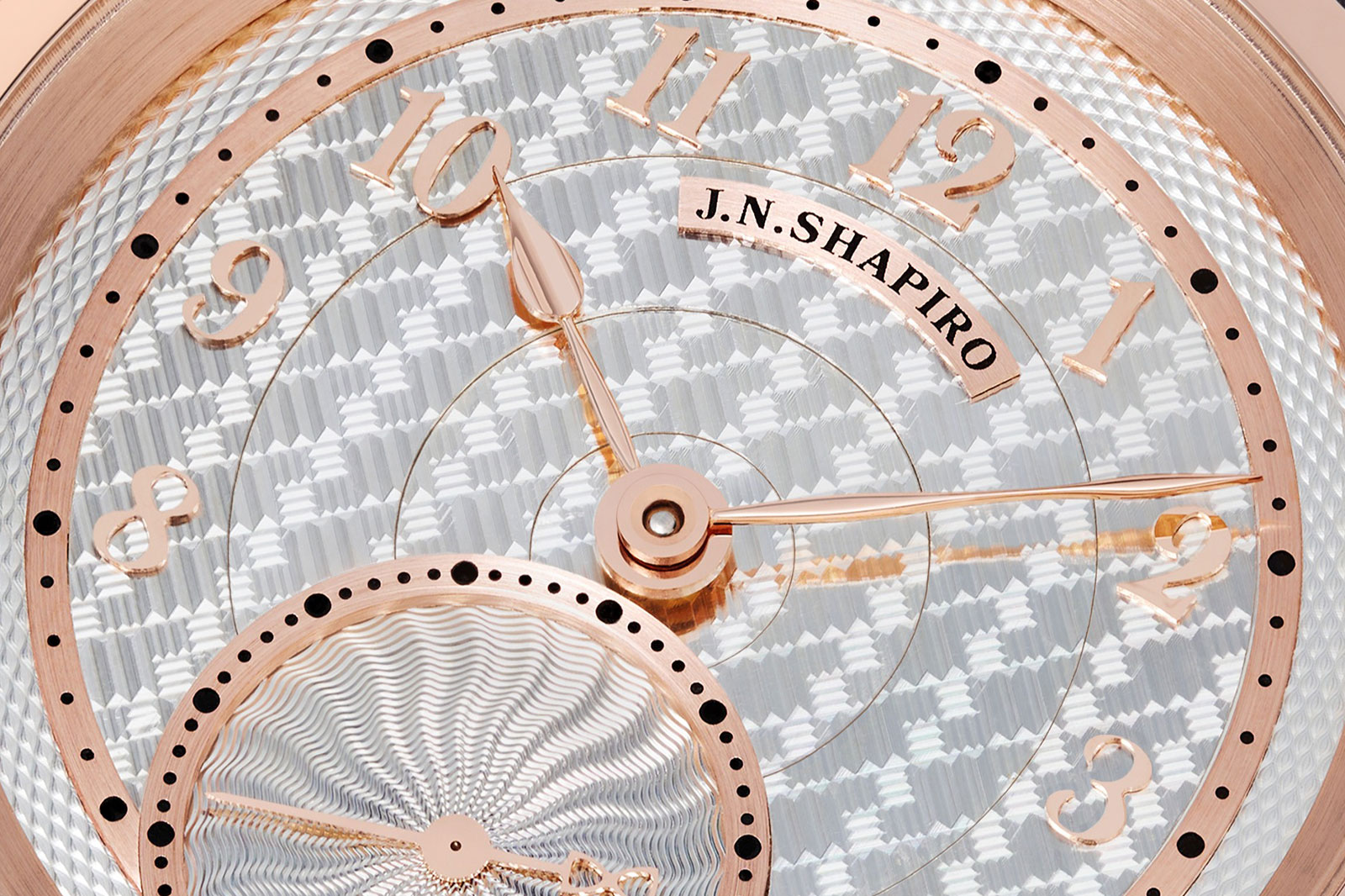
But guilloche found not just on the dial, but also on the case band – an industry first – which is turned on the same rose engine as the dial. Joshua gained proficiency turning circular components by making rings, and he has now applied this expertise to the watch case. To achieve this, the lugs are produced separately and attached after the caseband has been engraved (a detail that means a mixed metal case is a possibility).
The 38 mm case is available in a variety of metals, including white or rose gold, steel, tantalum, and zirconium. Notably, the white gold alloy he uses includes palladium, which makes the alloy more expensive but means that the case does not need to be plated with rhodium in order to achieve a bright white finish.
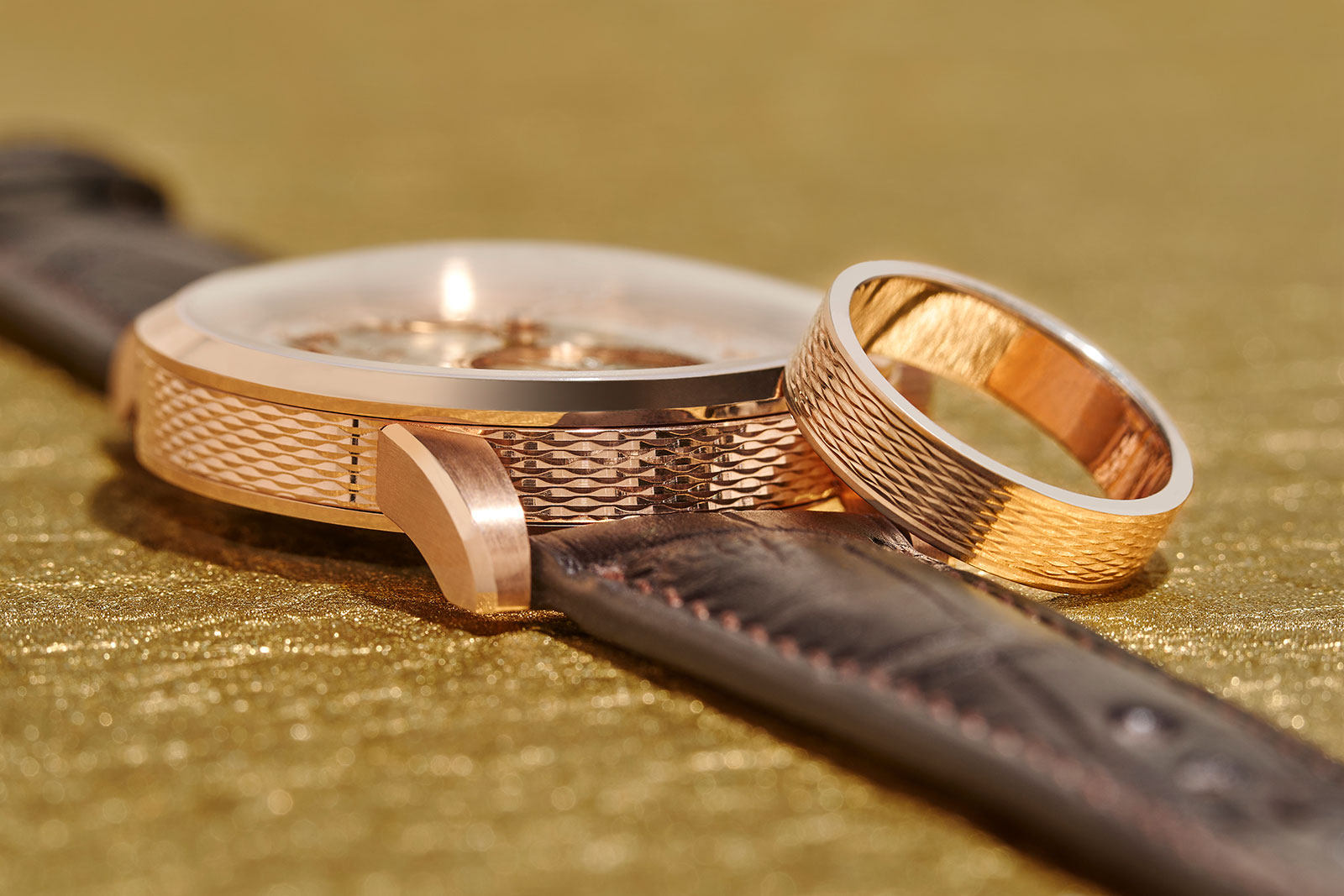
In-house and distinctive
But arguably the biggest upgrade is the movement, which is now made in-house in California. The Infinity Series relied on the UWD 33.1, a high-end movement made Uhren Werke Dresden. While the UWD 33.1 is a fine movement, Joshua’s vision was always to create his own, American-made calibre.
This required a major investment in equipment and time, to produce parts like the escapement, pinions, and pivots. According to Joshua, the most difficult part of making a movement from scratch was learning to make “all the small steel parts that you can’t see through the case back.”
Because these components are so difficult to make and are typically hidden within the movement, making them in-house is not a commercially attractive option for most watchmakers. For this reason, most independent watchmakers, and even some historic Swiss brands, outsource these components to specialists.
Full control of the manufacturing process gives J.N. Shapiro the ability to offer three different bridge layouts for the movement. From a technical standpoint, the three variations are identical, but collectors have the option to choose from a traditional layout with finger bridges, a curvy layout with a large S-shaped train bridge, or a cubist-inspired layout with straight bridges.
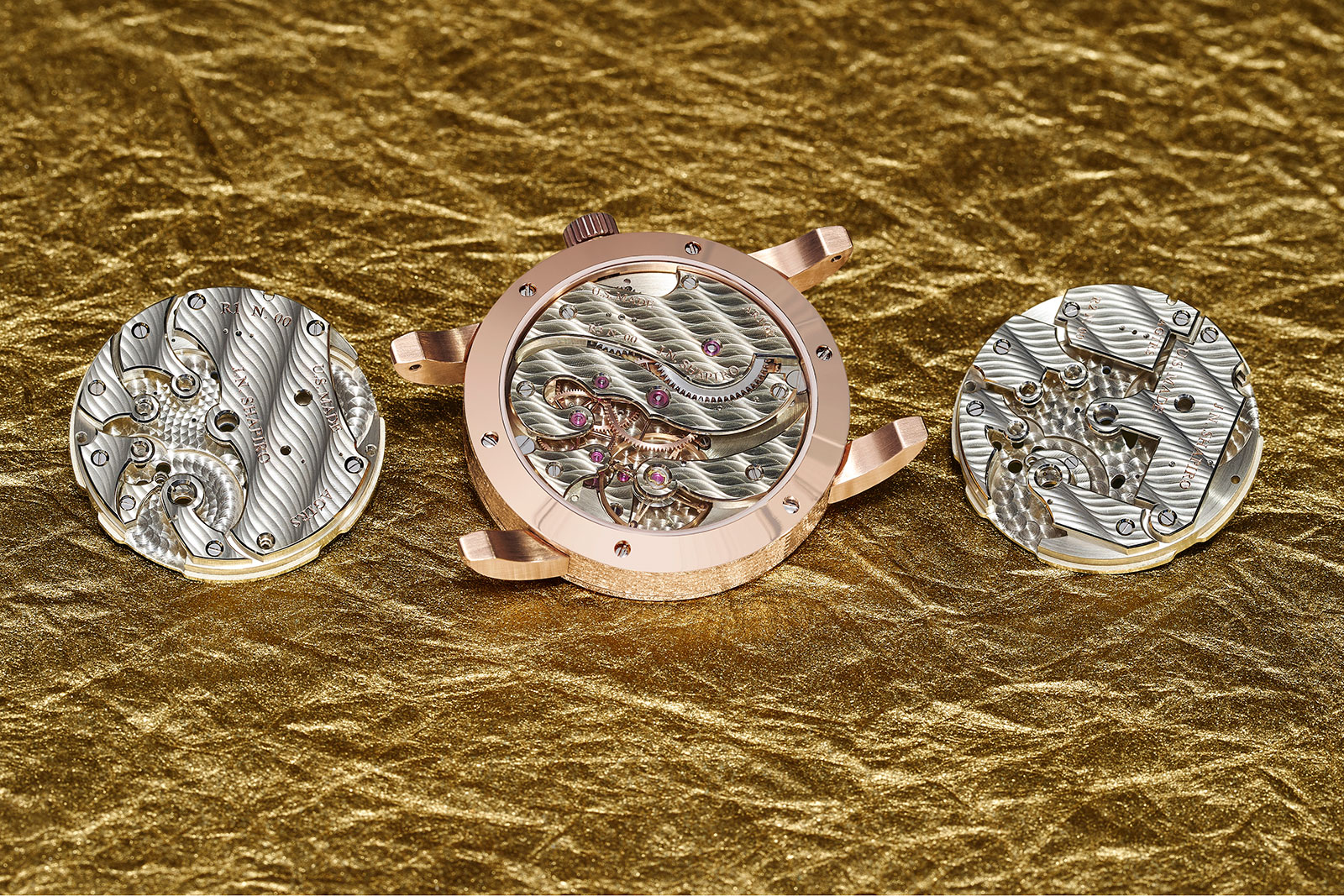
Notably, J.N. Shapiro is the only brand that is currently offering collectors different options for movement layout, and this level of customisation multiplies the number of possible configurations by a factor of three, increasing the odds that every Resurgence watch will unique in some way.
Regardless of configuration, the bridges are made from German silver, also known as maillechort, and the finishing is distinctive and top-notch. The base plate is finished with perlage, while the bridges are attractively decorated with damaskeening, a distinctly American style of patterned finish that was popularised by the 19th-century American watchmakers that J.N. Shapiro is honouring with the Resurgence.
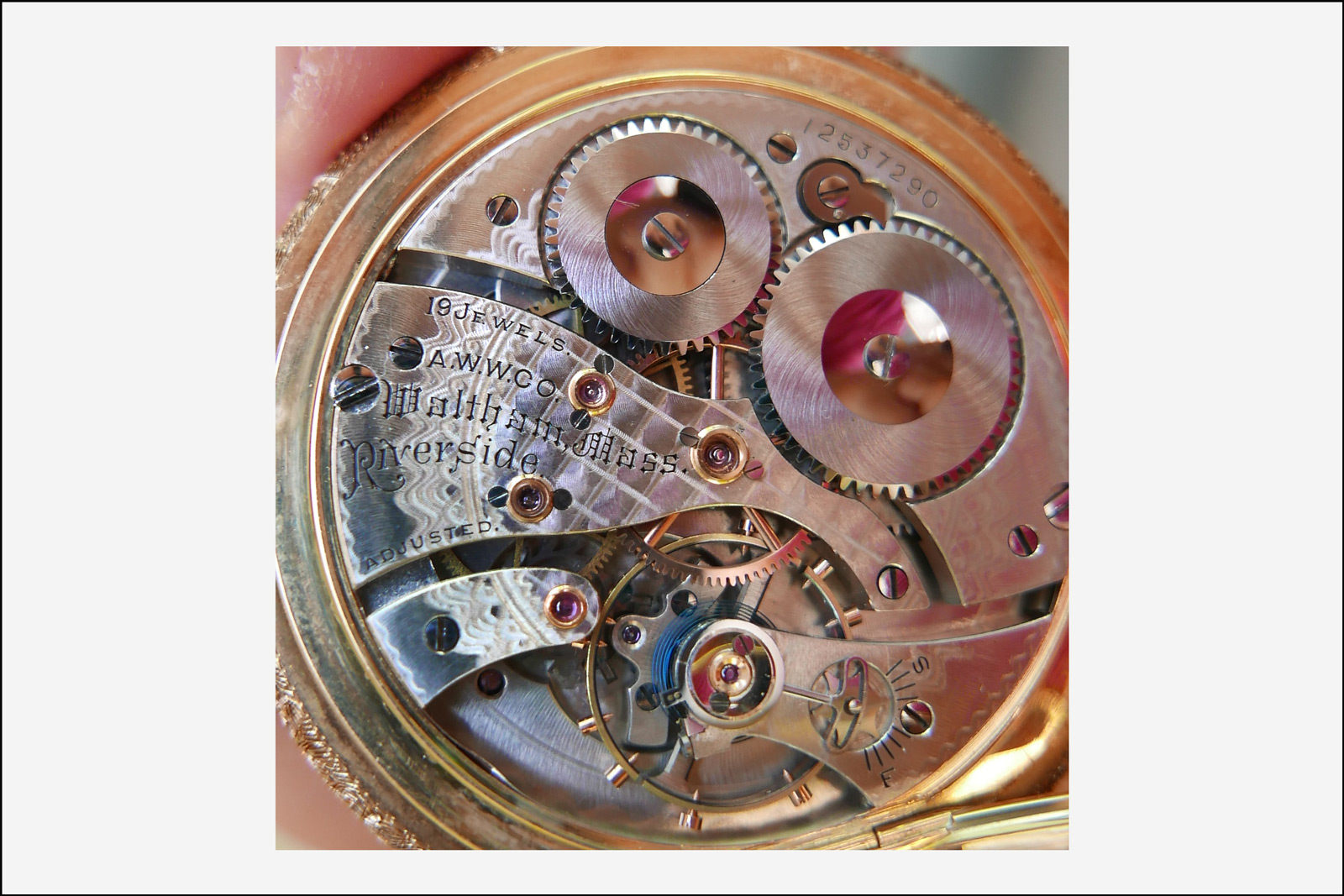
Example of damaskeening on the author’s Waltham Riverside from 1903.
But despite the American roots, the finishing has been updated to the standards of contemporary Swiss haute horlogerie. The bridges are finished with wide, mirror-polished anglage with crisp inward and outward angles. The most complex bridge style (the cubist design) features 14 inner angles, which take two to three hours each to finish by hand. The countersinks for the screws and jewels are also very wide and executed to a high standard.
There are two watchmakers on staff that do anglage, one of whom has a background in engraving. To acquire the skills needed to do inward angles in-house, the team trained with Nathalie Jean-Louis, a Swiss movement decoration specialist who spent six years at Greubel Forsey and now runs her own finishing workshop that also offers training.
Even the wheels receive an unusual degree of hand finishing, with fully rounded spokes. The spokes of the wheels are cut in the CNC machine, but the final, rounded form can only be achieved with tedious hand polishing.
The team evidently takes a lot of pride in their work: the movements are all signed with “ARTGS”, which is the first letter of the last name of each of the five full-time watchmakers who work on the Resurgence.
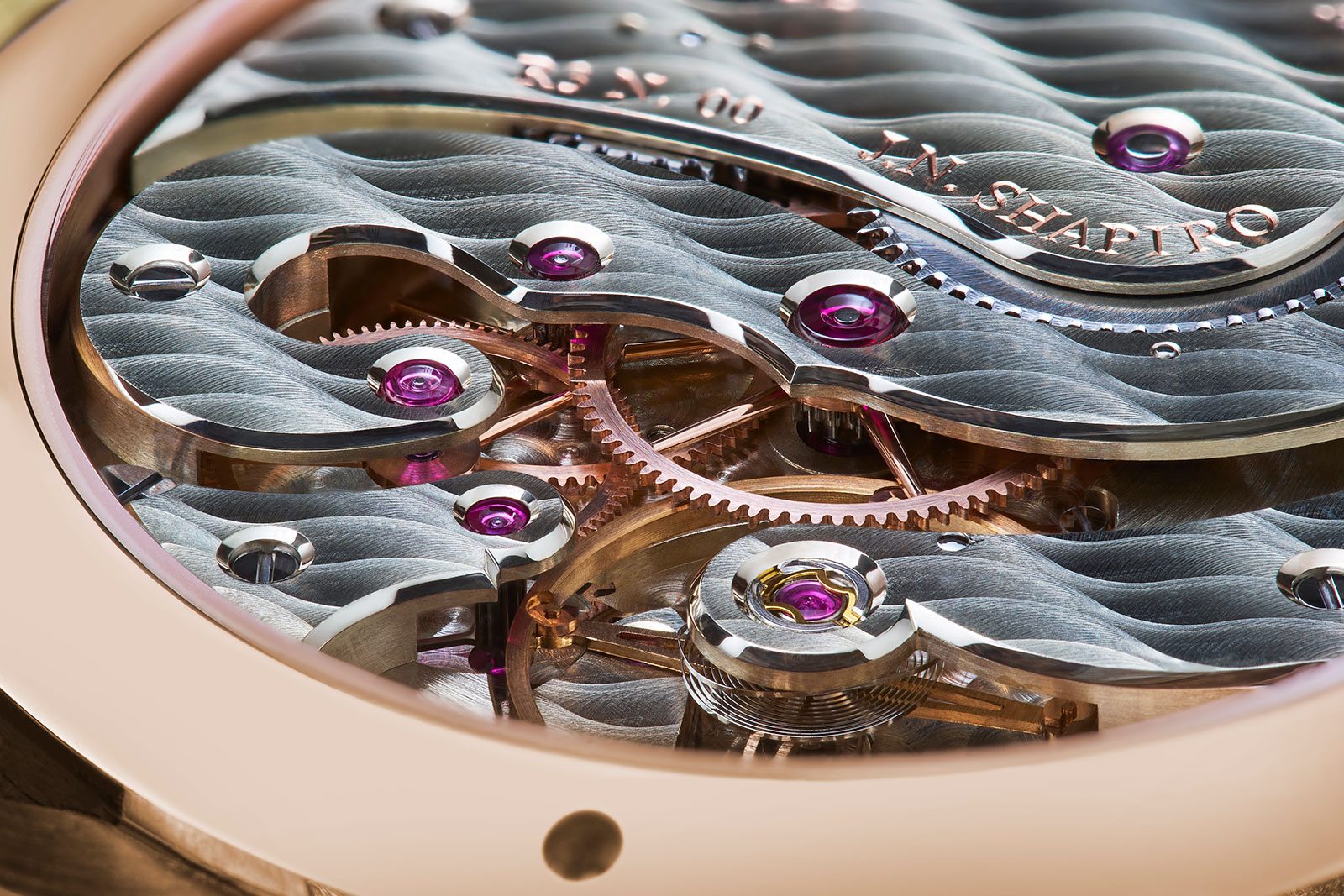
Further evidence of the ambition of Joshua and his team is the use of a free-sprung balance and an overcoil hairspring. Currently, J.N. Shapiro obtains flat hairsprings from Switzerland and relies on two watchmakers on staff who form the overcoils in-house.
The flat hairsprings are supplied by Precision Engineering, the Neuhausen-based sister company to H. Moser & Cie. that provides hairsprings and escapement components to many high-end independent watchmakers, including Laurent Ferrier and MB&F.
To fully appreciate the extent of J.N. Shapiro’s new in-house capabilities, it’s worth noting that many of Precision Engineering’s other clients buy complete escapements, including the hairspring, escape wheel, lever, and balance wheel. In contrast, J.N. Shapiro only buys the hairspring; the rest of its components are made in-house.
Impressively, J.N. Shapiro is already experimenting with US-made wire for the hairspring and hopes to produce hairsprings in-house as early as year-end. Based on what the brand has already accomplished, I wouldn’t bet against them.
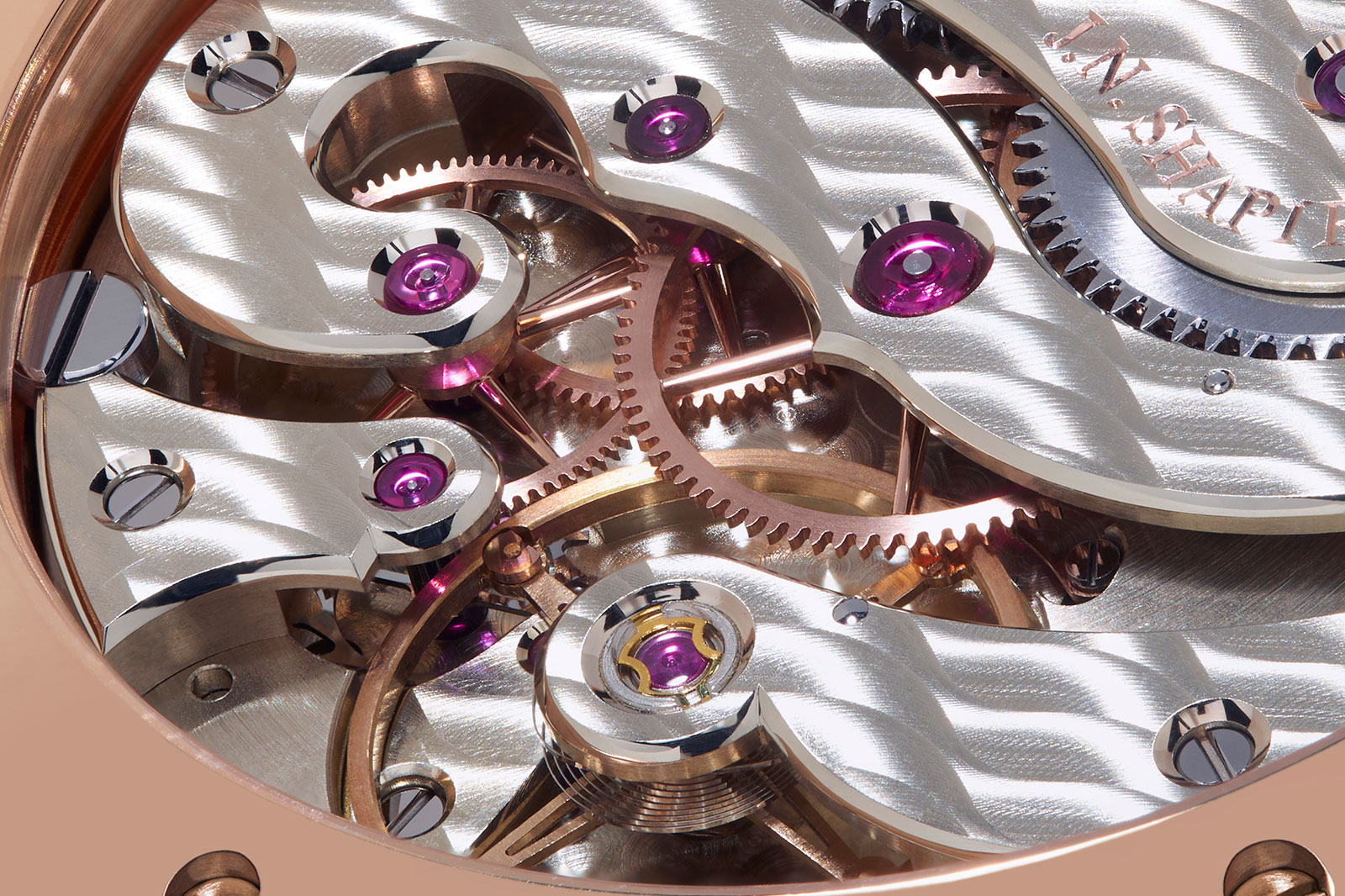
Key facts and price
J.N. Shapiro Resurgence
Diameter: 38 mm
Height: 8.7 mm (not including crystal)
Material: 18k white or rose gold, tantalum, zirconium, or stainless steel
Crystal: Sapphire
Water resistance: 30 m
Movement: Resurgence
Functions: Hours, minutes, and seconds
Winding: Manual
Frequency: 18,000 beats per hour (2.5 Hz)
Power reserve: 48 hours
Strap: Bespoke strap and material
Limited edition: No, but production capacity is limited to around 30 watches per year
Availability: The first delivery is scheduled for late 2023
Price: 18k gold – US$85,000; tantalum – US$80,000; zirconium or stainless steel – US$70,000
For more, visit Jnshapirowatches.com.
Back to top.