Explained: Barrels, Mainsprings, and the Trade-off Between Power Reserve and Energy
Parallel vs. in-sequence.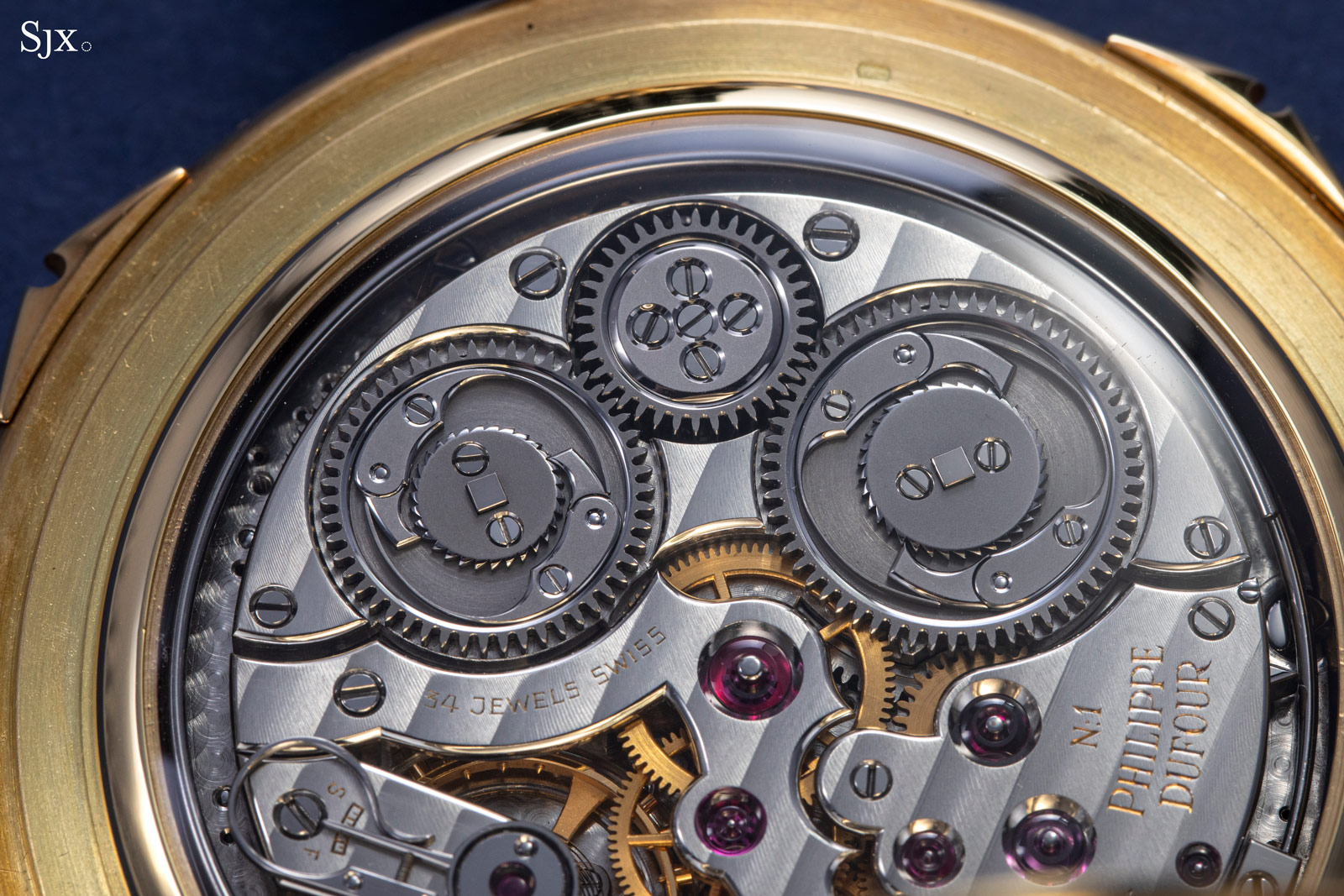
Every mechanical watch employs at least one mainspring barrel as its energy source. When a watch is wound, the coils of the mainspring tighten, storing potential energy which is then slowly released through the gear train to the escapement.
The mainspring is enclosed in a toothed barrel, essentially a drum covered by gear teeth. As a result the barrel is often considered to be the first wheel of the going train.
Although one is the norm, two or even more barrels can be employed, typically to generate more energy. Double barrel movements usually feature two mainsprings kinematically linked in one of two ways: in parallel or in series. The number of mainsprings, energy stored, and power reserve are illustrated with equations (1), (2), and (3):
As described by equation (1), the energy of a single barrel E is a function of its torque, angular discharge velocity and running time (autonomy).
Linking two identical barrels naturally means having twice the energy, so 2E. By convenient association, equation (2) exploits the available energy to double the torque sent to the gear train, while equation (3) takes advantage of the total energy by doubling the running time.
Parallel barrels
The parallel arrangement of barrels embodies equation (2), which delivers twice the torque, increasing the energy available to run the movement (but not increasing the running time).
Here two barrels unwind at the same time on a centre pinion connected to a second mobile of the going train. An embodiment of the parallel linkage is illustrated in fig. 1.
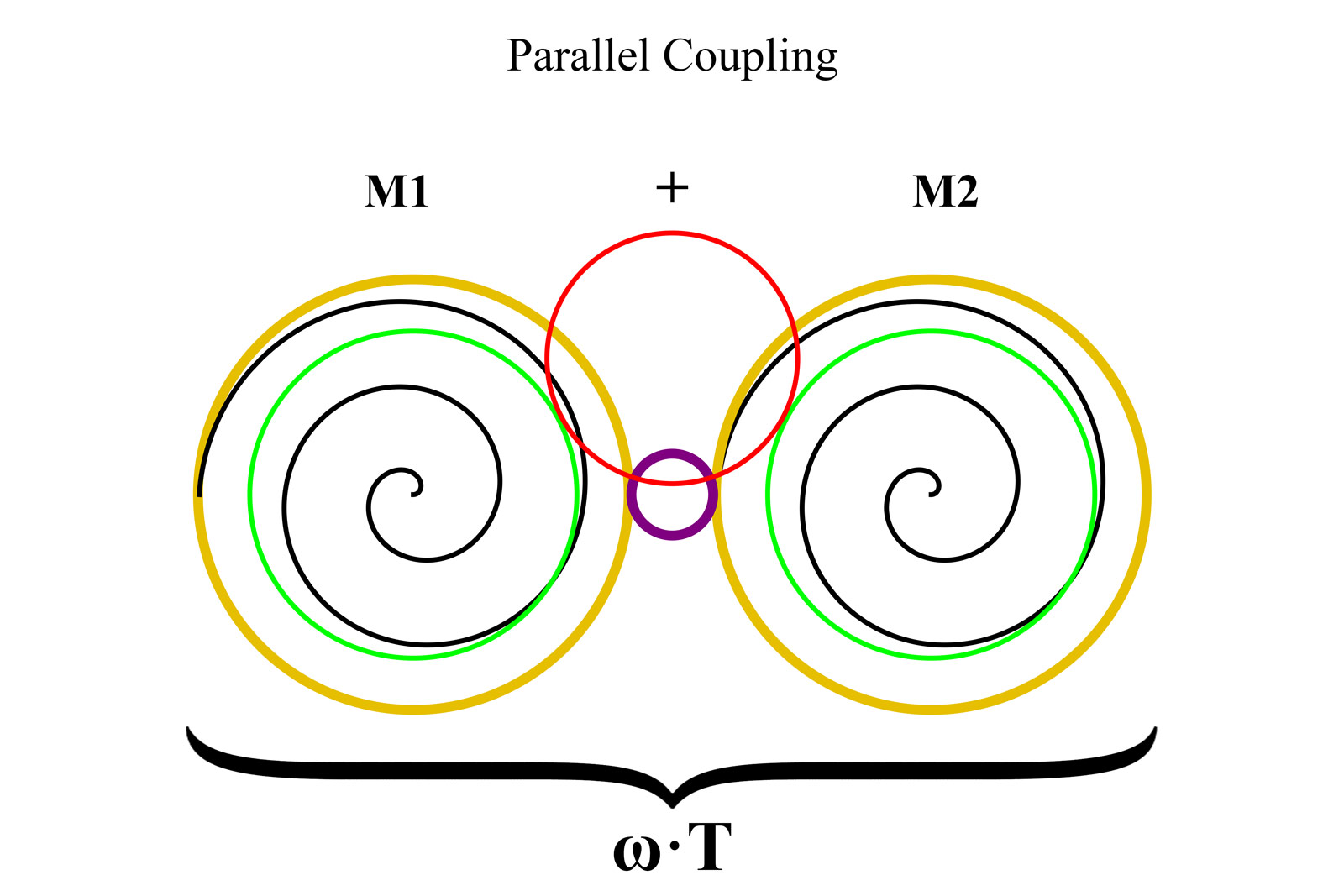
Fig. 1 – Outline of a parallel linkage between two barrels
The two mainspring barrels (yellow) act on the centre pinion (purple). The mainsprings (black) are each connected each to an arbour and ratchet wheel (green). The two ratchets are connected by a crown wheel (red), itself linked to a winding system (not depicted).
In this set up, identical barrels are wound at the same time and at the same rate, and then discharge their energies simultaneously. The two barrels have the same developing speed and running time, but their torques cumulatively add up in turning the centre pinion. The equal pressures exerted by the two barrels from opposite sides on the pinion tend to cancel out, contributing to the parts’ longevity.
The utility of the parallel setup lies in the fact that the power transmitted to the balance is much greater than in a single-barrel movement, which greatly improves chronometry. Consequently, many vintage and modern precision timepieces rely on two barrels unwinding in parallel, ranging from 19th century Breguet pocket watches to contemporary F.P. Journe wristwatches like the Chronometre Optimum.
Two barrels working in parallel are also useful for a watch that features a particularly power-intensive complication – like the MB&F LM Thunderdome. The Thunderdome needs not two, but three, barrels coupled in parallel to deliver the necessary energy to power the fast revolving, multi-axis tourbillon.
Barrels in series
Equation (3) that delivers increased power reserve is associated with barrels arranged in series. Two barrels working serially (or in sequence) deliver torque equivalent to just one barrel at any point in time, but as they unwind one after another, the respective running times add up for longer autonomy overall.
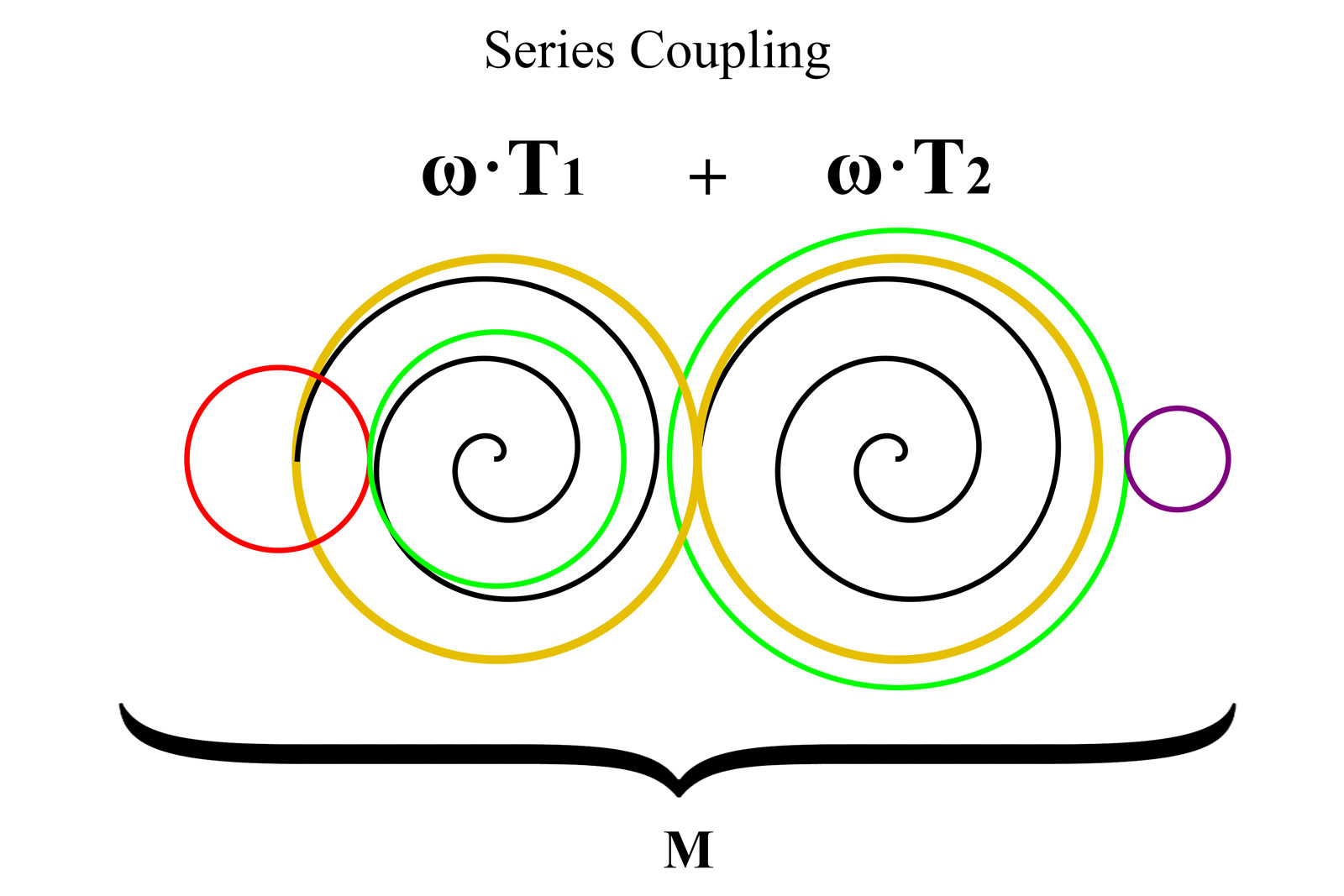
Fig. 2 – Outline of a series linkage between two barrels
The basics of serially-coupled barrels can be observed in fig. 2. A crown wheel (red) engages with the ratchet wheel (green) of the first barrel (yellow). The two barrels are geared directly to each other by their toothed drums.
The mainspring in the second barrel is linked by an arbour to its ratchet wheel (green) that is larger in diameter than the barrel. This oversized ratchet wheel connects to the centre pinion (purple).
When the watch is wound through the dedicated system, the first mainspring (black) winds up and turns its barrel wall, followed by the second mainspring winding up via the geared drum. The energy is discharged via the second barrel’s arbour, through the oversized green gear to the going train via the centre pinion.
In short, the barrels are wound one after another when the movement is being wound, and then the barrels unwind one after another when the movement is running.
The two mainsprings’ respective numbers of developing turns are cumulative. They unwind at the same rate, but one after another, meaning their respective discharge times are also cumulative. As a result, the running time of the watch is doubled, even though the torque delivered to the gear train is at any given moment equivalent to a single barrel’s output.
Such series coupling is mostly used in long power reserve movements, for example the IWC 52000 family with a seven-day power reserve, or at the extreme, the Hublot MP-07 with its nine barrels and a 40-day power reserve.
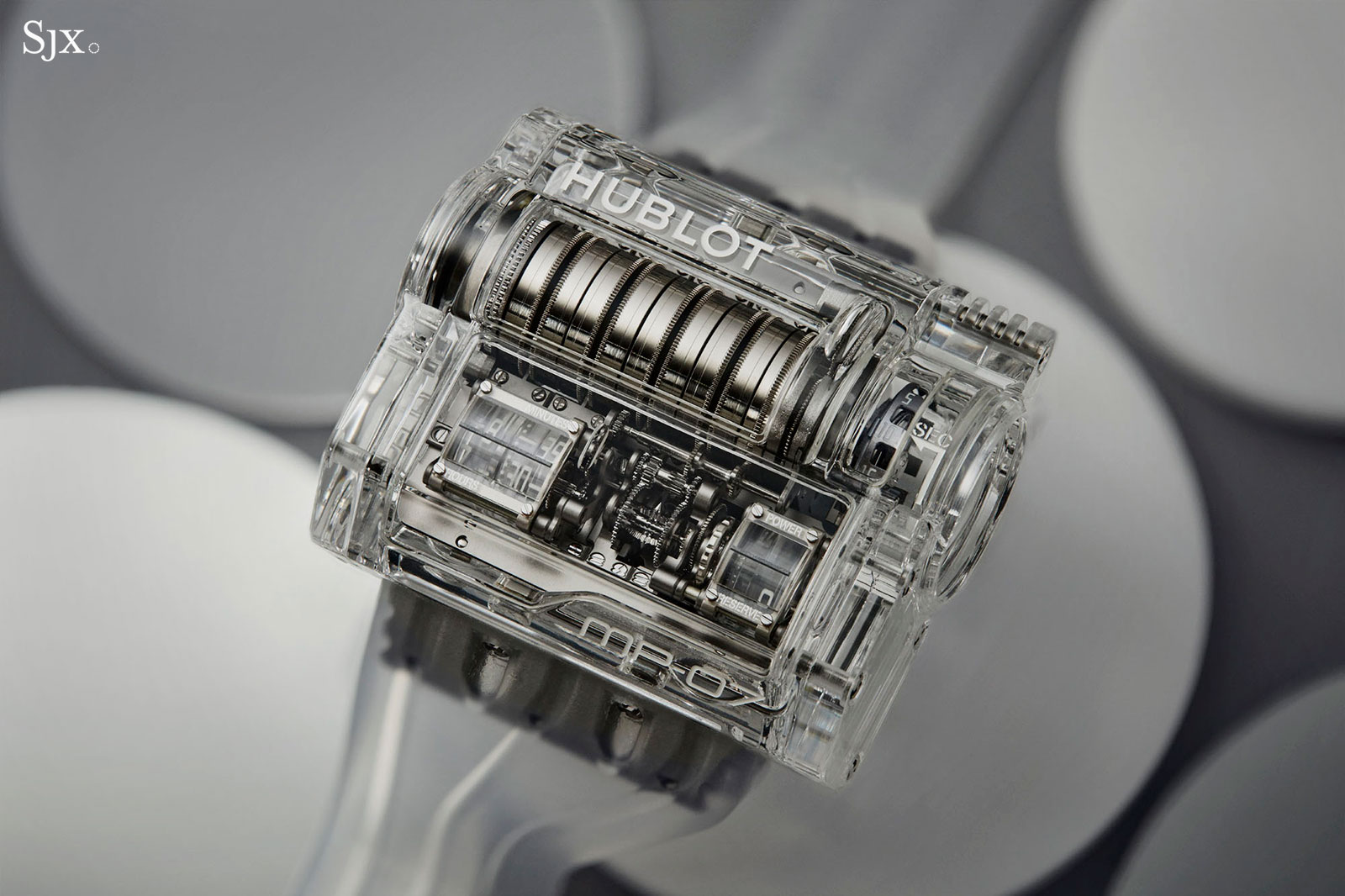
The Hublot MP-07 with nine barrels arranged concentrically across the diameter of the case
A single large barrel can also lengthen a watch’s power reserve, but it would affect timekeeping due to fluctuating torque reaching the regulating organ.
Any sort of mainspring delivers high torque when fully wound, then settles for a median value for most of its running time, before dropping off as it is nearly empty. These variations in torque are more pronounced for big barrels.
A timepiece with a long power reserve (say more than three days) running on a single large barrel would probably run fast for the first day, reasonably well for the next two to three days, then experience a severe drop in rate.
One solution is a constant-force mechanism to even out the uneven torque, as used in the Lange 31 which employs two enormous mainsprings for a one month’s worth of power reserve.
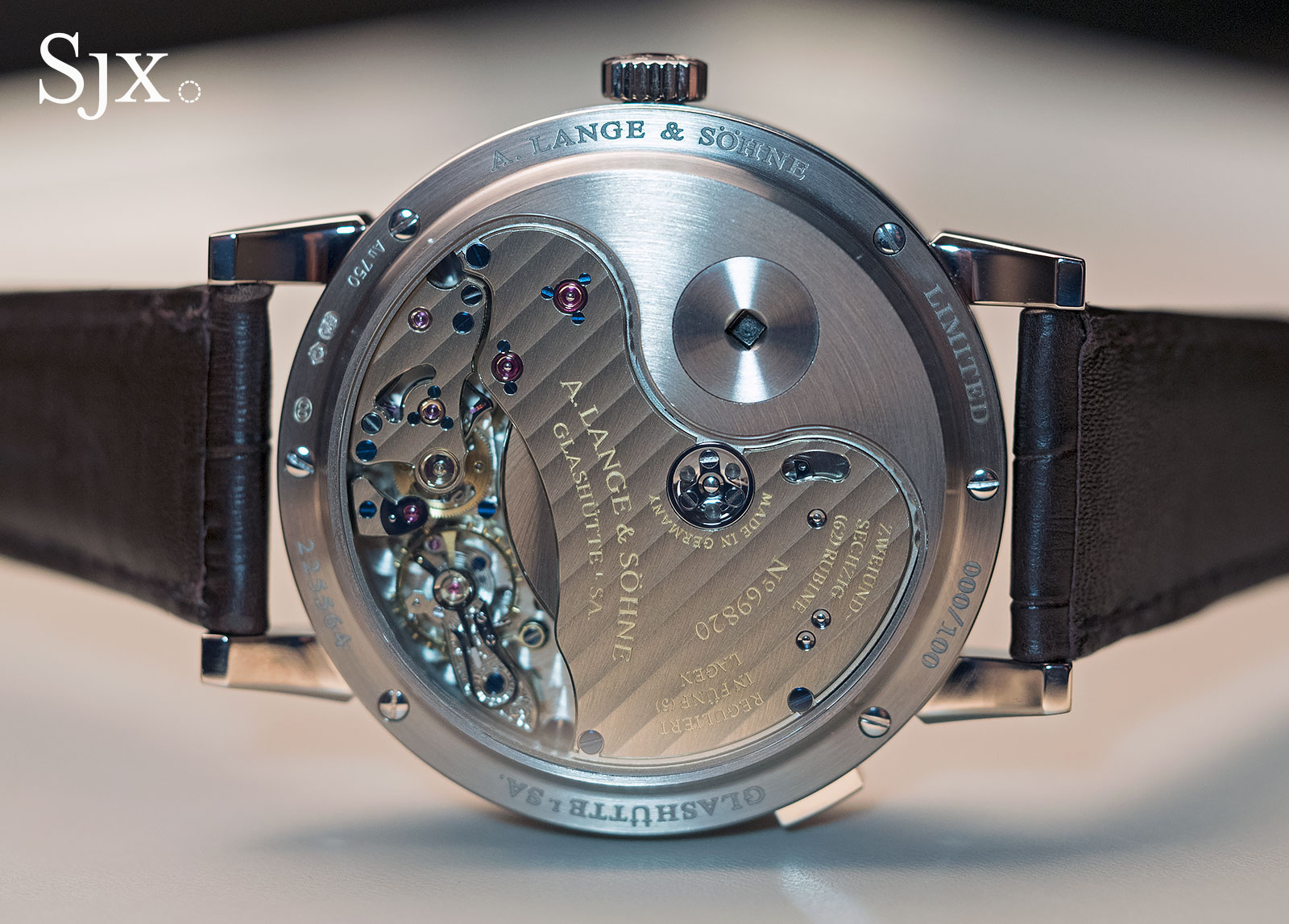
The Lange 31 features two huge barrels stacked one on top of the other, each containing a mainspring over 1.8 m long
Sequenced barrels, on the other hand, exhibit a much flatter torque curve over the course of their running time, and perform more consistently than each of the individual barrels operating separately.
As a result, some movements utilise smaller barrels coupled in series. Here the goal is not to extend the power reserve, but employ smaller or shorter mainsprings with less energy output. Sequential smaller barrels work at higher revolving speeds but deliver lower and more consistent torque than a single mainspring with an equivalent power reserve.
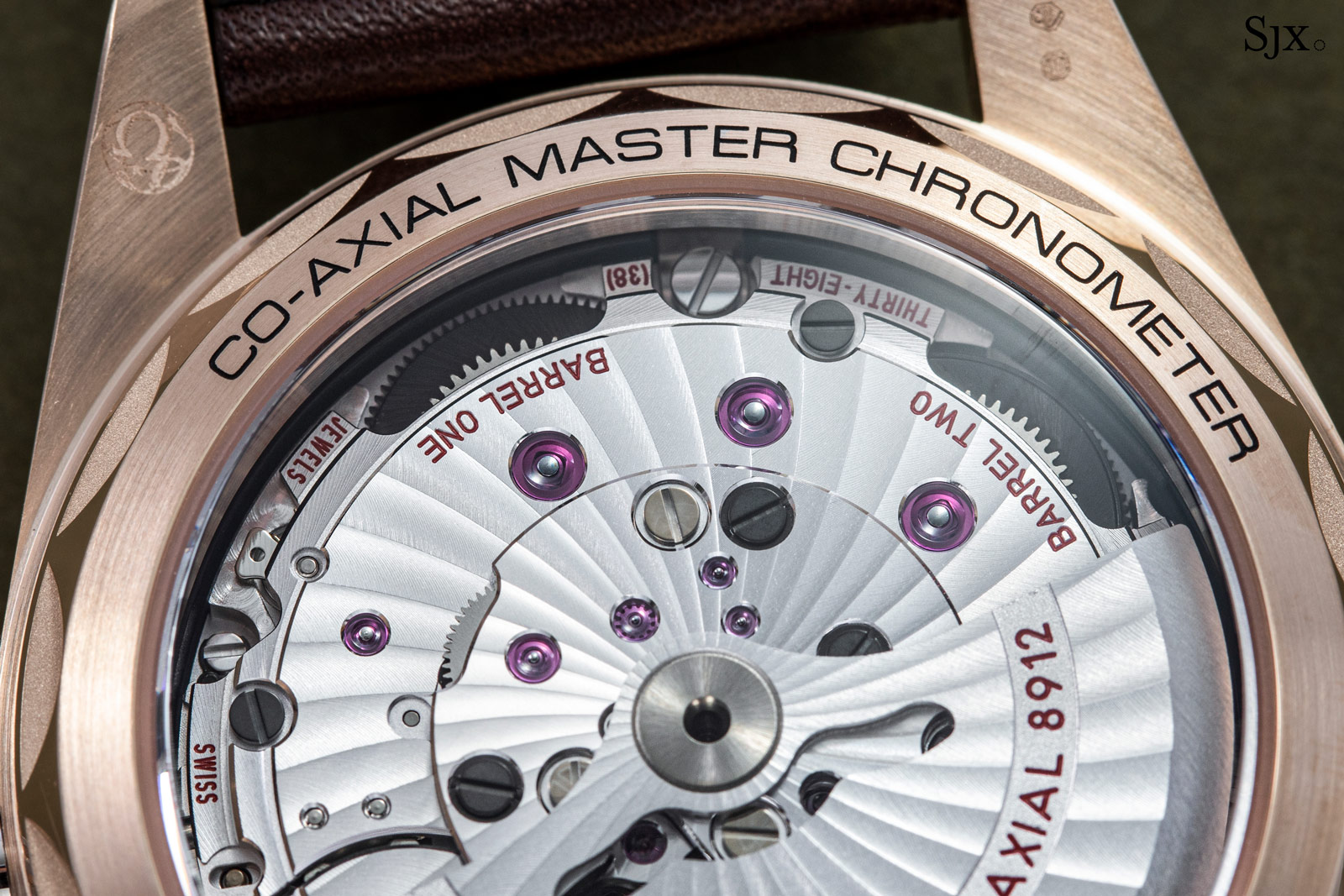
The Omega cal. 8912 with its helpfully labelled barrels “One” and “Two”
This approach is thought to increase a movement’s longevity, as the strain on the going train is smaller. The Longines L.990 and most last generation Omega co-axial movements make use of this principle in their construction.
Back to top.