In-Depth: Inspiration and Creation of the Grand Seiko Thin Dress Series
Behind the design.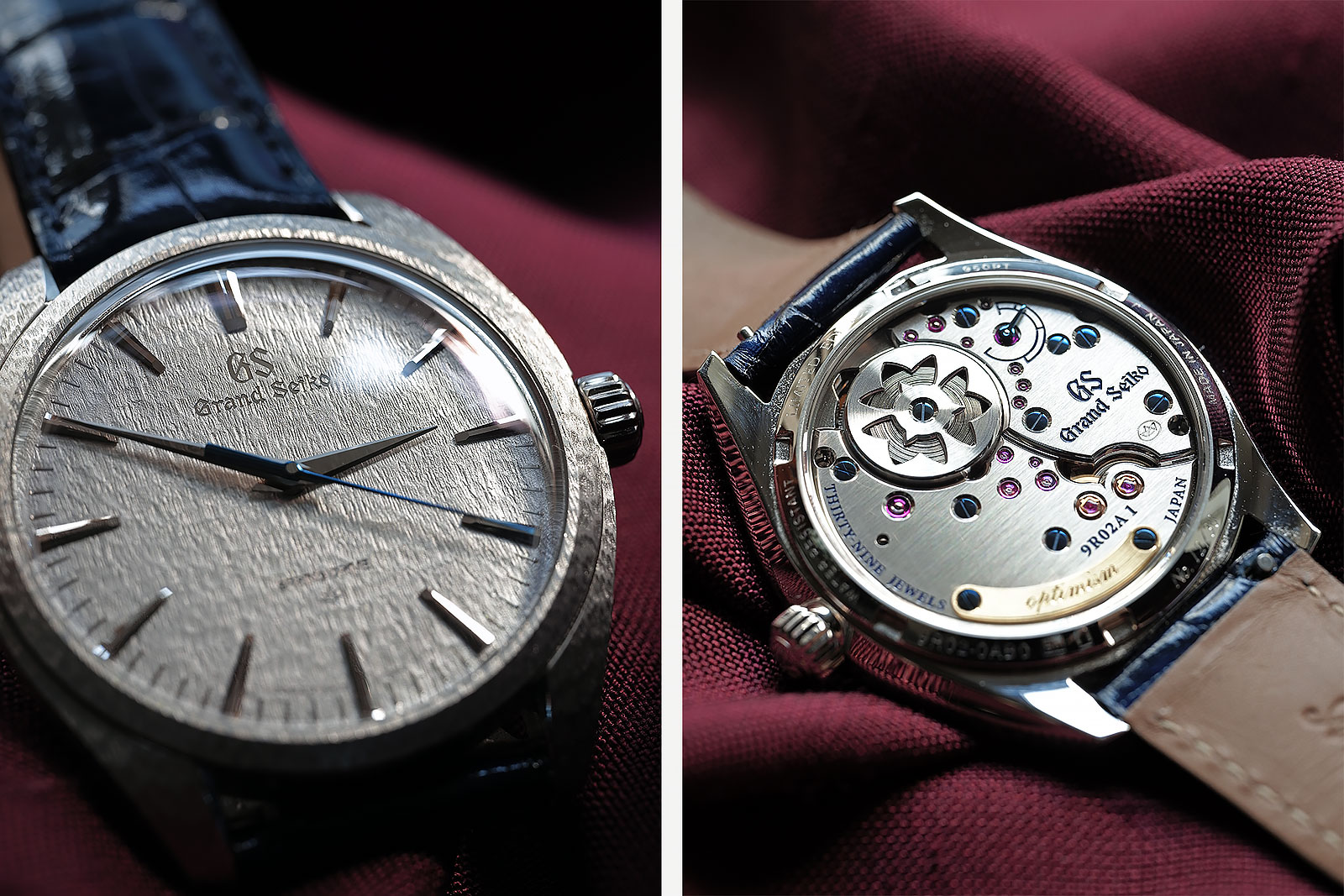
Earlier this year, I paid a visit to Seiko’s headquarters in Ginza, Tokyo. I was there for two reasons.
One was to present my Ideal Watch Size Survey to their design, product and development teams. The other was to find out more about a particular Grand Seiko I had recently purchased, the SBGZ001. Launched in 2019 to celebrate the Spring Drive’s 20th Anniversary, the SBGZ001 is an extraordinarily finished version of the Grand Seiko Thin Dress Series from the Elegance collection.
What started as a few questions from a collector ended up being a dive into how a significant new line of watches at Grand Seiko was born.
In the interest of full disclosure: The Armoury, which I own, has been a retailer of Grand Seiko in Hong Kong for about six years now. I have been collecting Grand Seiko for about nine years. Neither the SBGZ001 nor the SBGY003 detailed in this article are available for sale at the store. But they are special so I wanted to delve further into their creation.
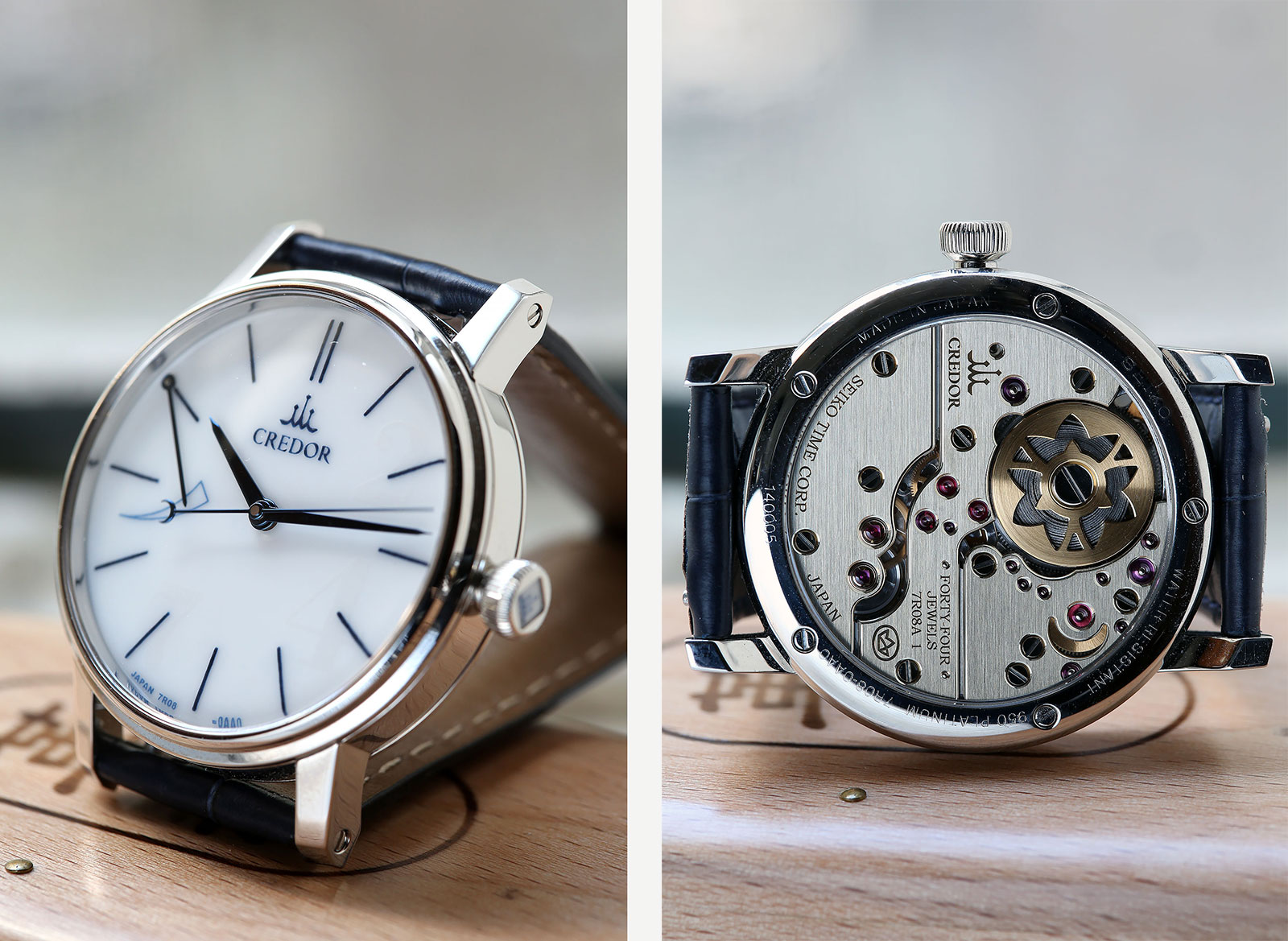
The Credor Eichi I, 2013
First some background. Back in 2013, I bought a Credor Eichi I, a well-known watch in certain circles for its exceptional finishing. It was made in the Micro Artist Studio (MAS), a division within the Seiko-Epson Shiojiri plant where all the cutting-edge high horology – namely Spring Drive movements – is designed and made. That includes things like the Credor Minute Repeater, the Grand Seiko 8 Day Power Reserve and the Credor Eichi II.
I toured the facility in 2014 and visited the MAS, a series of rooms nestled underneath the staircase in the main building. The studio is made up of a very small team of less than 15 people, but what they make there is truly exceptional. I eventually let my Eichi I go to another collector but I still wanted to own a piece from the MAS.
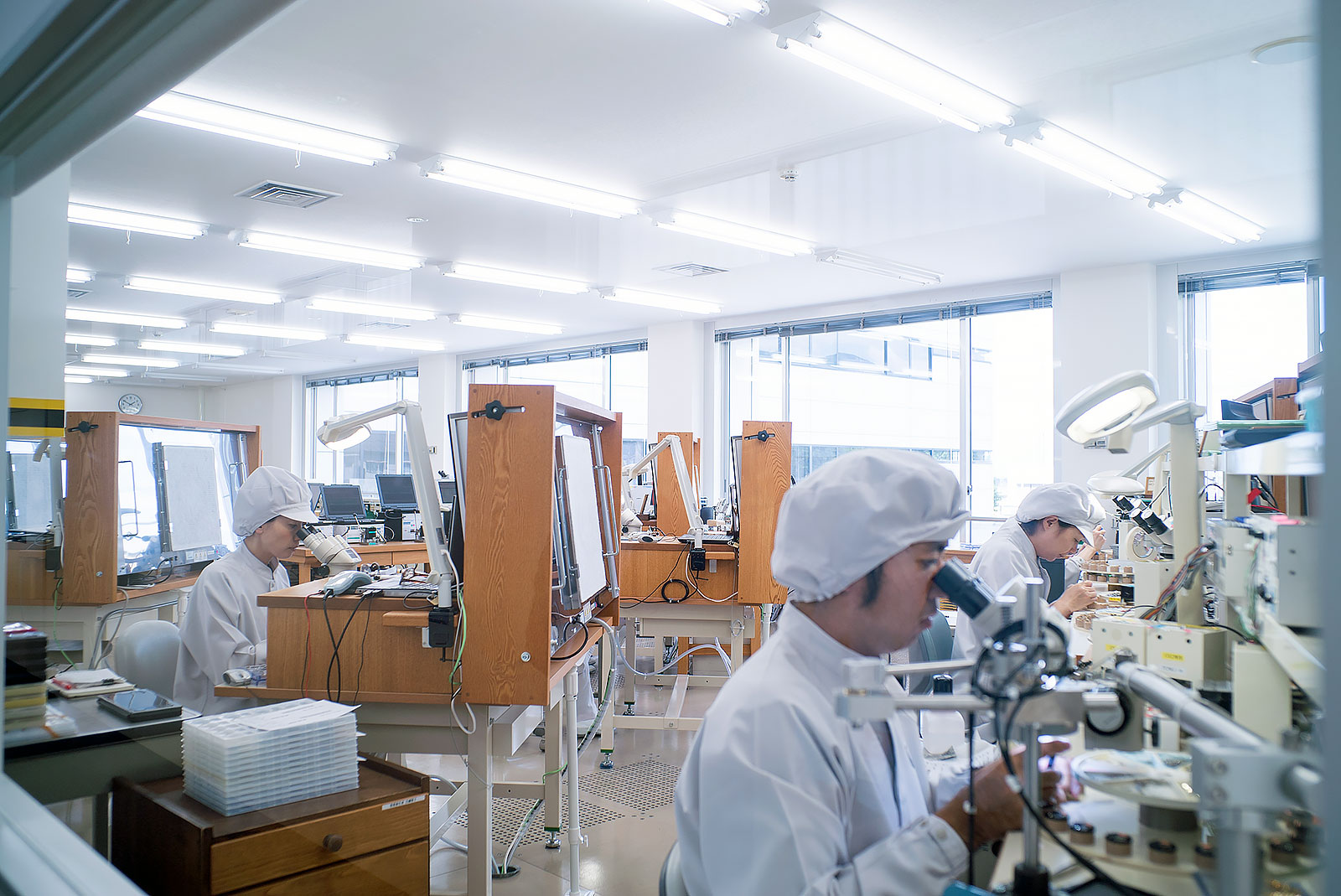
Spring Drive movement assembly at Seiko-Epson in Shiojiri
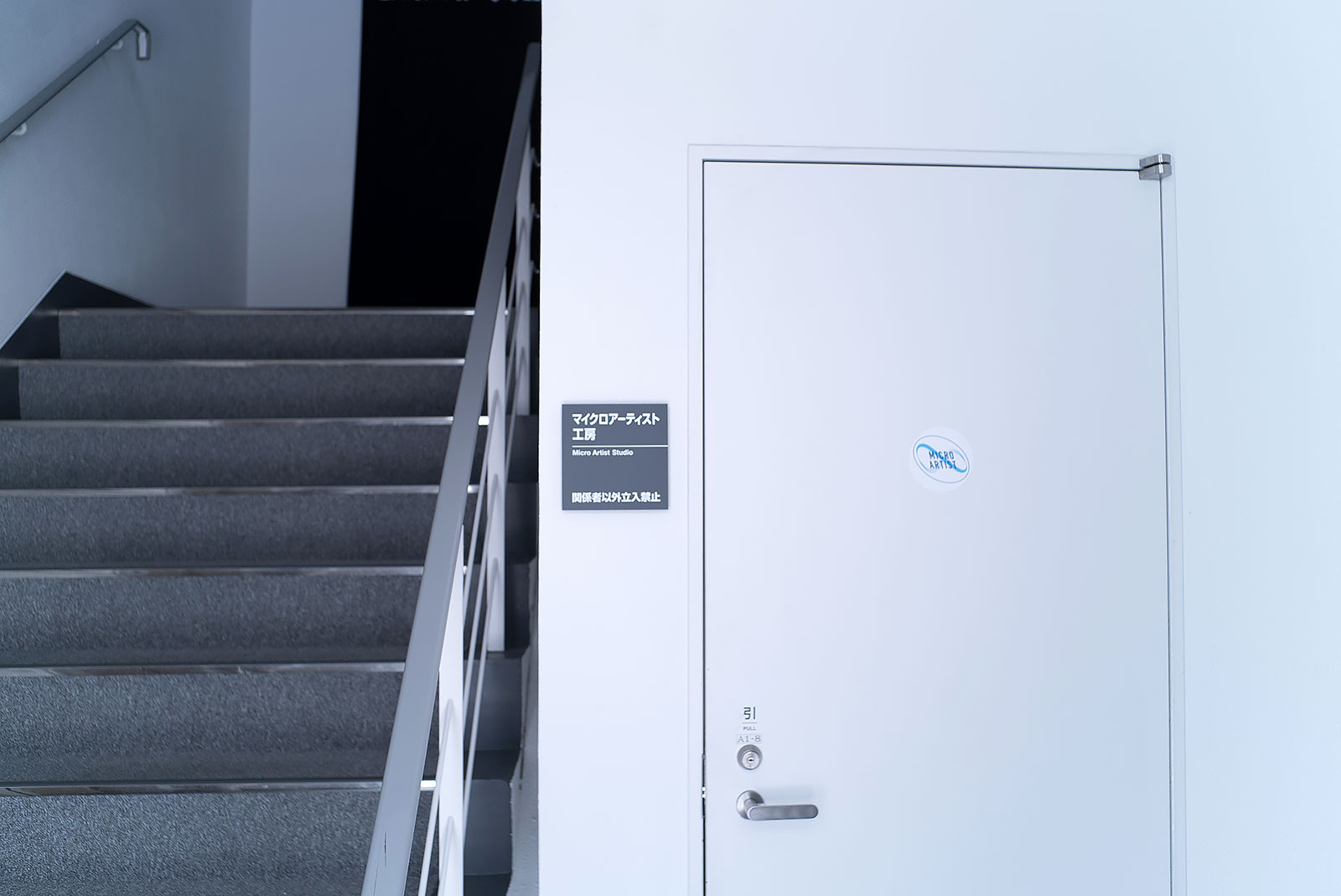
The entrance to the MAS
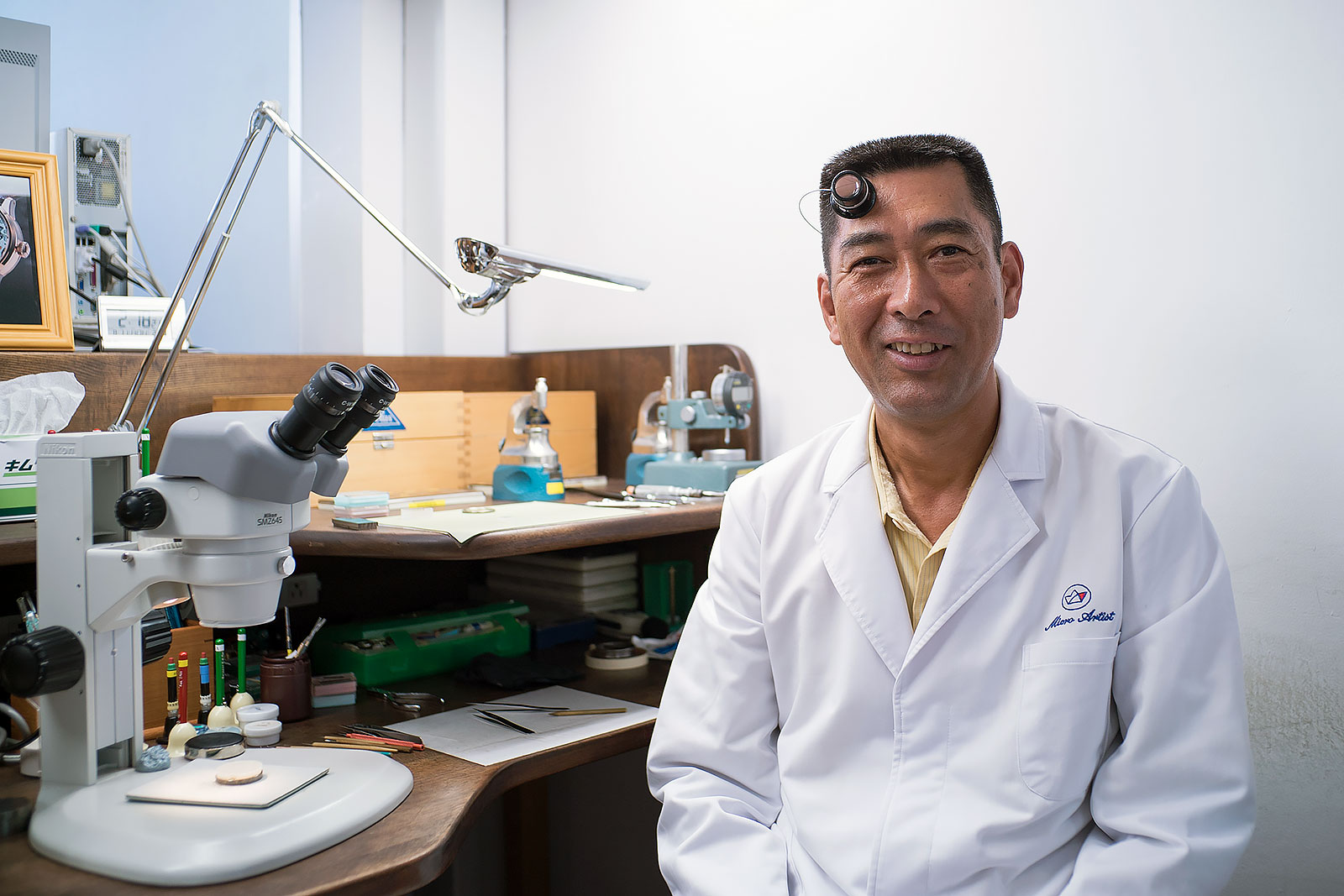
Yoshifusa Nakazawa of the Micro Artist Studio
When the SBGZ001 was announced last year, I put my name down for one immediately, as only 30 pieces would be made. It was somewhat nerve-wracking making a purchase from press photos only but I am glad I took the chance. The piece is magnificent in person.
How does a watch like the SBGZ001 come about? This question cannot be answered without first understanding how new Grand Seiko products are born.
The elegant contest
Seiko has a large watch design team that works on various designs for the company across all the brands of Seiko, ranging from Prospex to Credor. Of that group, a small number are Grand Seiko specialists.
In 2018 the head of marketing, Norihito Hara, who takes care of the Grand Seiko product range as a whole, and Shinichiro Kubo, senior manager of design, decided to create a new Grand Seiko dress watch, named “Thin Dress Series”. As a new model, it needed a new design language, something that had Grand Seiko’s DNA but also had a distinct new direction.
An internal competition was held and three designers submitted their concepts, supervised by Kubo-san. A young, talented designer named Kiyotaka Sakai won the competition. Sakai-san won the competition because his design successfully connected to Grand Seiko’s historical designs. Because the new watch would be part of theSpring Drive’s 20th Anniversary commemorative editions, it was important the design was respectful of its origins.
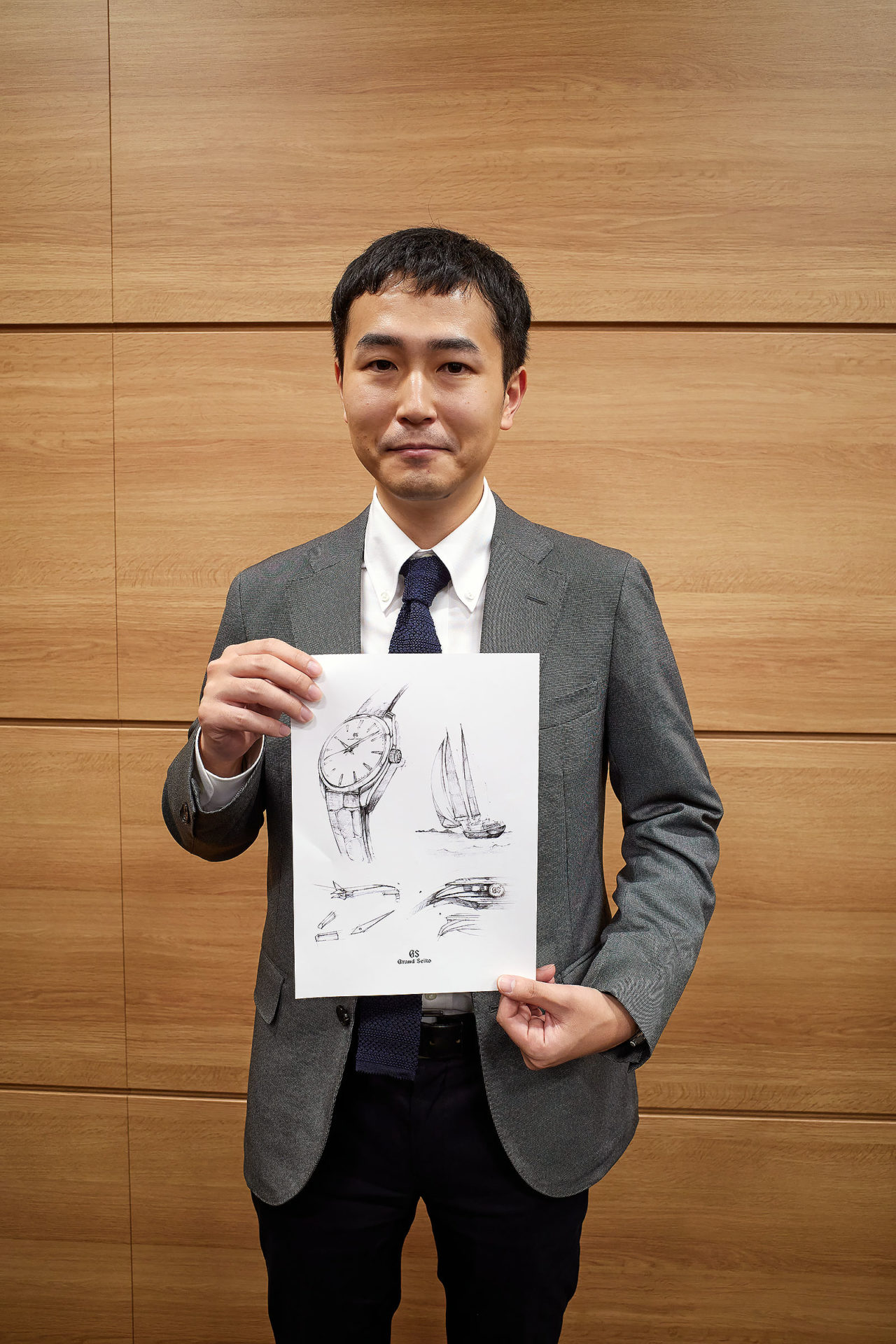
Kiyotaka Sakai
As the watch was meant to be a dress watch, it was important for the watch to slide easily underneath a shirt cuff. Sakai-san’s concept was to emphasise an extremely slim case.
The case retained Grand Seiko’s round case sides at three and nine o’clock but introduced something fresh in the design: a gentle curvature when the watch was viewed in profile, with both the case and the crystal in harmony. The overall effect is reminiscent of a wind-filled sail, organic and light in its appearance.
Sakai-san’s initial design became the core elements of the Thin Dress Series, with the case and hour markers he designed being used throughout the line. Sakai-san also has a number of complete watch designs in the Thin Dress Series. The first to be introduced were quartz models, SBGX329 and SBGX330, both released in Japan in 2018.
But he was not the only designer working on models in the Elegance line. In 2019, the first mechanical watches sold globally were unveiled, the SBGK002, SBGK004 and SBGK005 – designed by Nobuhiro Kosugi.
The same year, Sakai-san’s signature designs were unveiled, a variant of the Thin Dress Series and the same basic design in two guises: the SBGY003, a stainless-steel, limited-edition Spring Drive, and the SBGY002, a yellow-gold version with a Snowflake dial.
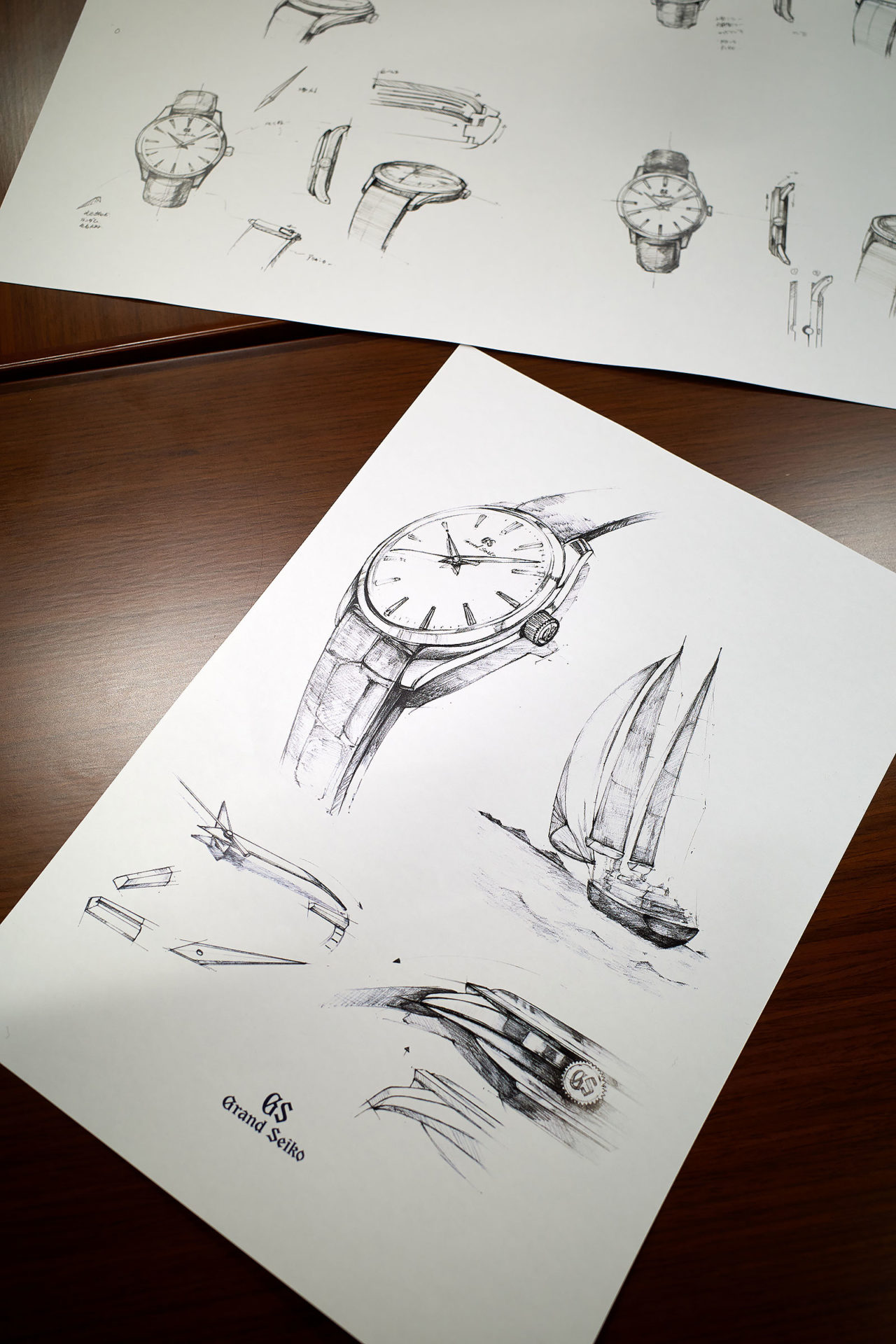
Kiyotaka Sakai’s sketches for the Grand Seiko Elegance
Thin Dress Series details
Thinness is one of the defining features of the Thin Dress Series. One challenge was having the domed sapphire crystal in harmony with the overall curvature of the watch while minimising its thickness. That was solved when Grand Seiko developed a new crystal design that has a slight dome in the centre and a deep radius at its edge, a shape optimised for visibility and also coated with an anti-reflective layer on its inside surface. The slight dome to the crystal is a nice nod to the acrylic crystals on vintage timepieces.
New, thin movements were developed, in mechanical, quartz and Spring Drive versions, most notably the Spring Drive 9R31, which is found in the SBGY003. The 9R31 is a manual-wind Spring Drive, doing away with the rotor found in a self-winding movement and shaving precious millimetres off the thickness.
Hara-san proudly touted that the 9R31 has a power reserve of 72 hours, as is the case for all current-generation Grand Seiko movements. The generous power reserve is a practical feature that takes into account its role as a dress watch. Such a watch might not be used over the weekend but it will still be accurate and ticking come Monday – a most considerate feature.
Grand Seiko is famous for its beautiful hands but the sheer size of the hands and resulting weight is often overlooked. Though slim, the 9R31 musters sufficient torque to drive the hefty, sharply-finished hands, an impressive technical feat. The hands are usually dauphine style with five facets: the top surface and all four edges, which give the hands a bevelled finish.
The hands and markers were refreshed for the Thin Dress Series, giving them a delicate, narrow shape. They have only three facets – the top and two of the longer edges – giving the hands a thinner, more elegant look. The sleek, elongated minute hand is also very slightly curved at the tip to provide necessary clearance under the crystal.
Designer Sakai-san’s hope is that the watch will be used for important occasions. So even though the design is legible and simple, he wanted the smallest details of the dial to be eye catching, hence he designed the markers to be wedge shaped so that light would reflect off of them in unexpected patterns.
For the dial of the SBGY003, Sakai-san was inspired by light shining through foliage. The dial was stamped with a sun-ray pattern radiating from the centre and covers most of the dial surface, enclosed by a fluted minute track on the outermost edge. It is a beautifully subtle touch and connects back to Sakai-san’s thinking of the watch being for occasions, while keeping it highly legibility, and thus having especially fine details.
If you handle the Spring Drive watches in the Thin Dress Series, you might notice a clever visual trick in the case design – the underside edges of the case are concave, making the case seem even thinner. The concave lower edges on the watch case are carefully polished, reflecting light in such a way that the thin watch seemingly floats on the wrist. You often see this trick used in laptop design, where the lower edge of the device curves inwards towards the base.
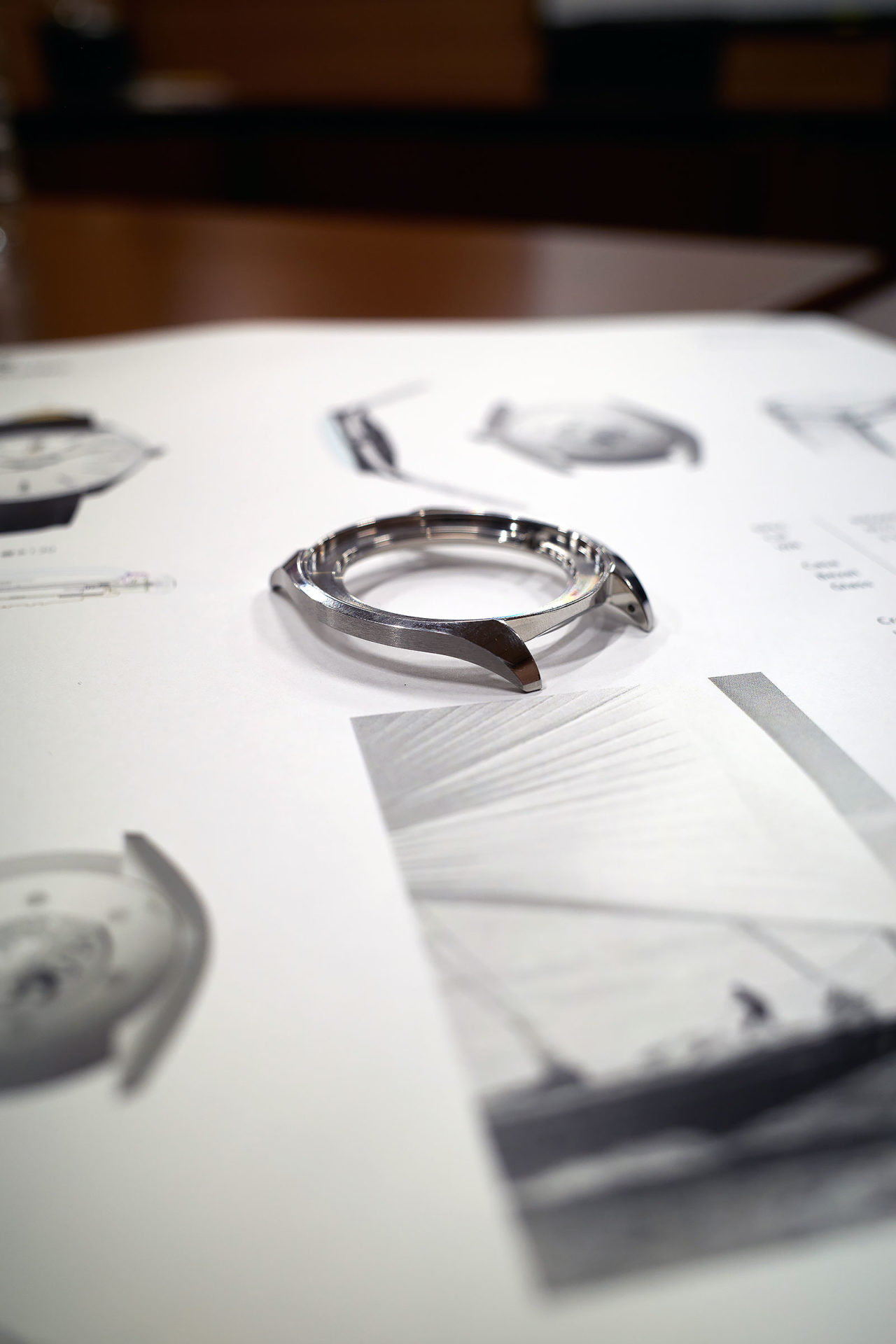
The case of the Spring Drive Thin Dress Series
The SBGZ001
With the foundations of the Elegance line established, the MAS version of the Thin Dress Series came next, the SBGZ001.
The watches of the MAS are designed by Kazunori Hoshino, who has been responsible for all the MAS releases from the Eichi II. In Hoshino-san’s mind, the goal of the MAS is to study and improve upon traditional techniques of high-end watchmaking.
With the SBGZ001, his starting inspiration was the old hammered finish cases that Grand Seiko made in the 1970s. He likes to imagine what watch designers at that time might have done with the modern facilities the MAS has today.
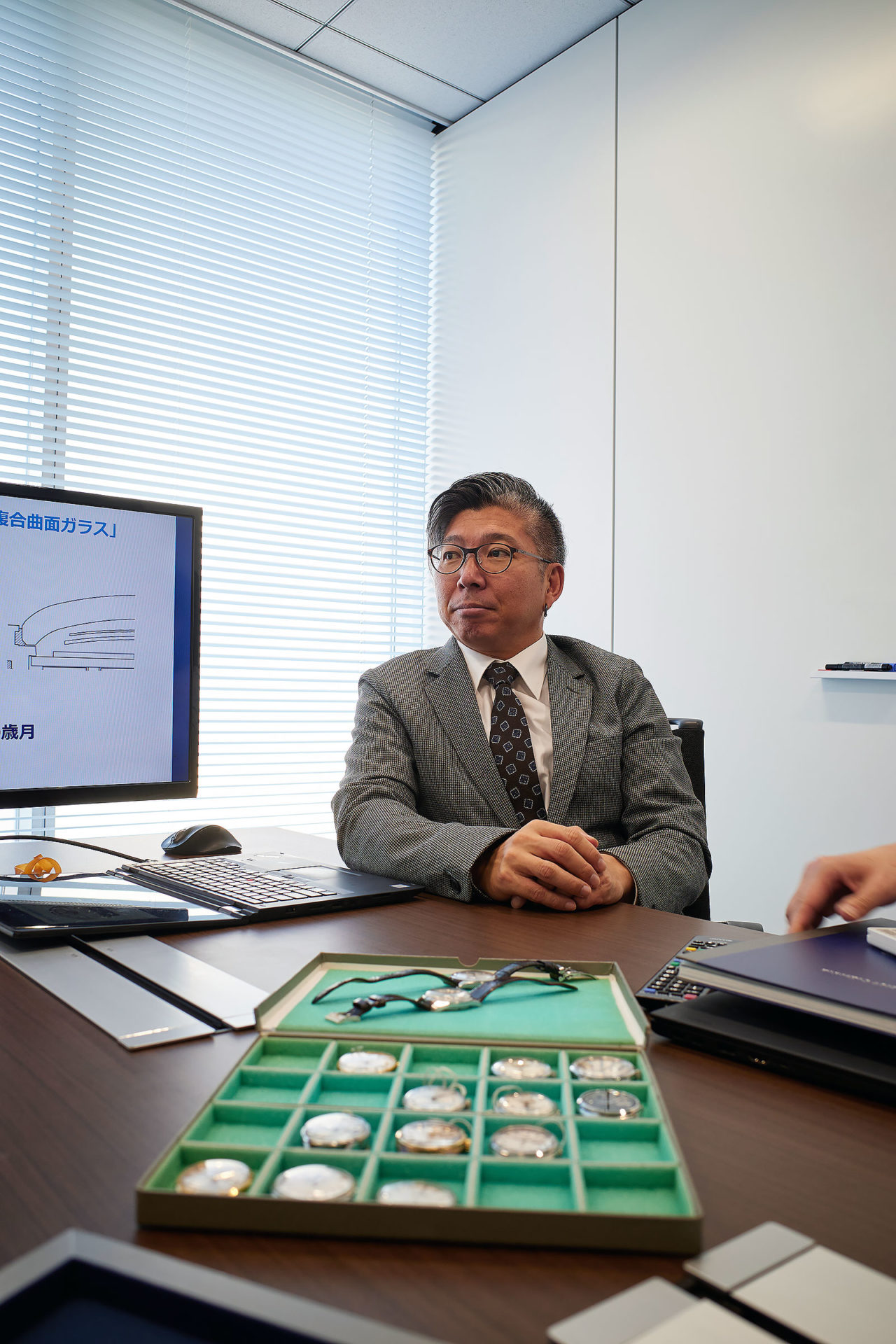
Kazunori Hoshino
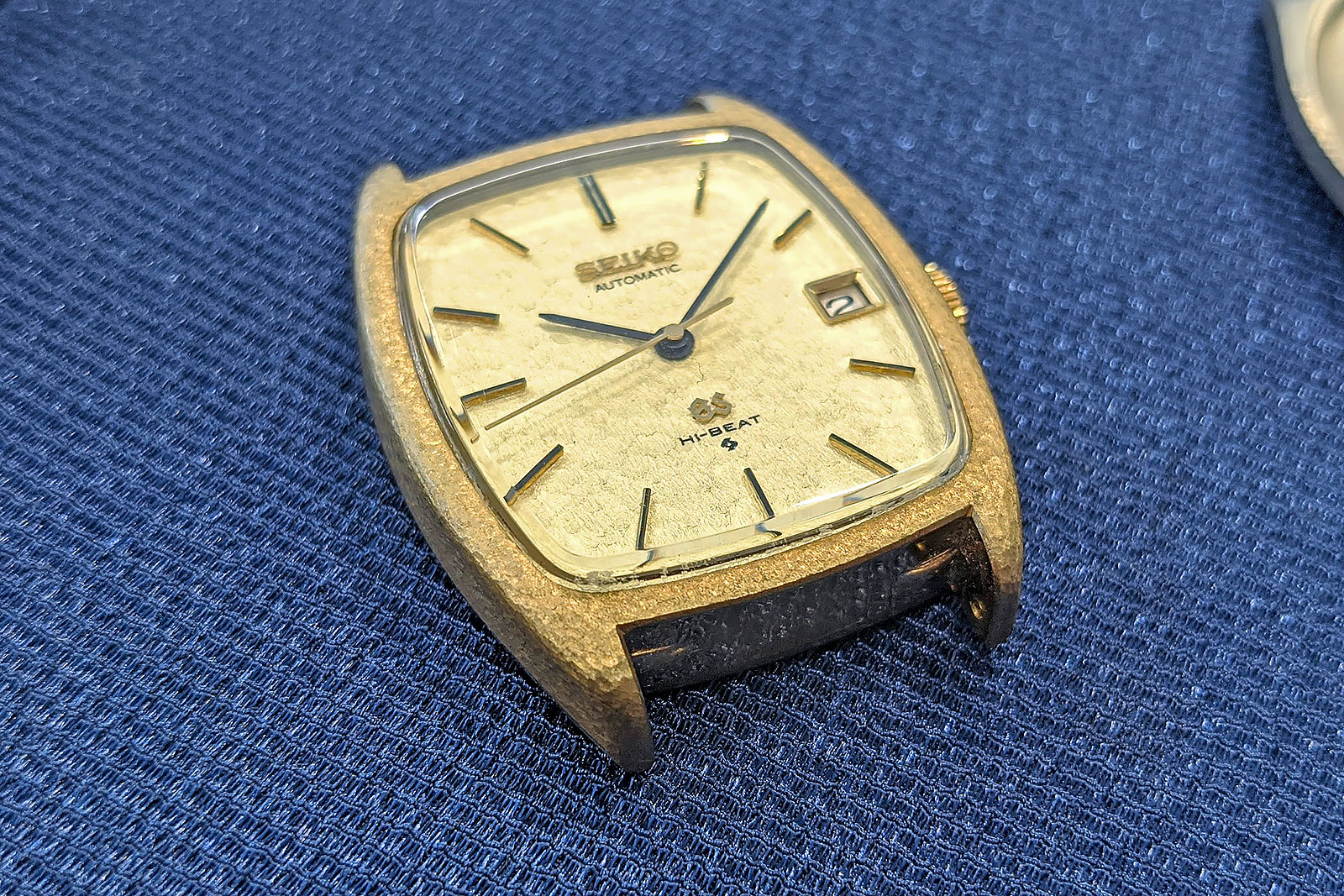
From Kazunori Hoshino’s archive, a Grand Seiko 56GS from 1971
After prototyping his initial idea, he felt there was an opportunity to modernize the decorative case finish by combining the MAS with an iconic modern-day Grand Seiko, the Snowflake, which is named after its snowflake-like dial finish, created by a proprietary stamping technique. Hoshino-san wanted to take the Snowflake to a new level and the result is the SBGZ001.
The SBGZ001 case starts out as a fully-polished platinum case, then engraved with the distinctive snowflake pattern over the main outward-facing surfaces. The engraving is done by hand with a very fine electric drill, similar to what dentists use.
In photographs, the snowflake pattern appears like fine bumps, somewhat like orange peel. In reality, it is a startling thing to behold, with minuscule, defined grooves carefully applied to create a repeating but organic pattern that has clearly been done by hand, so no two cases are alike.
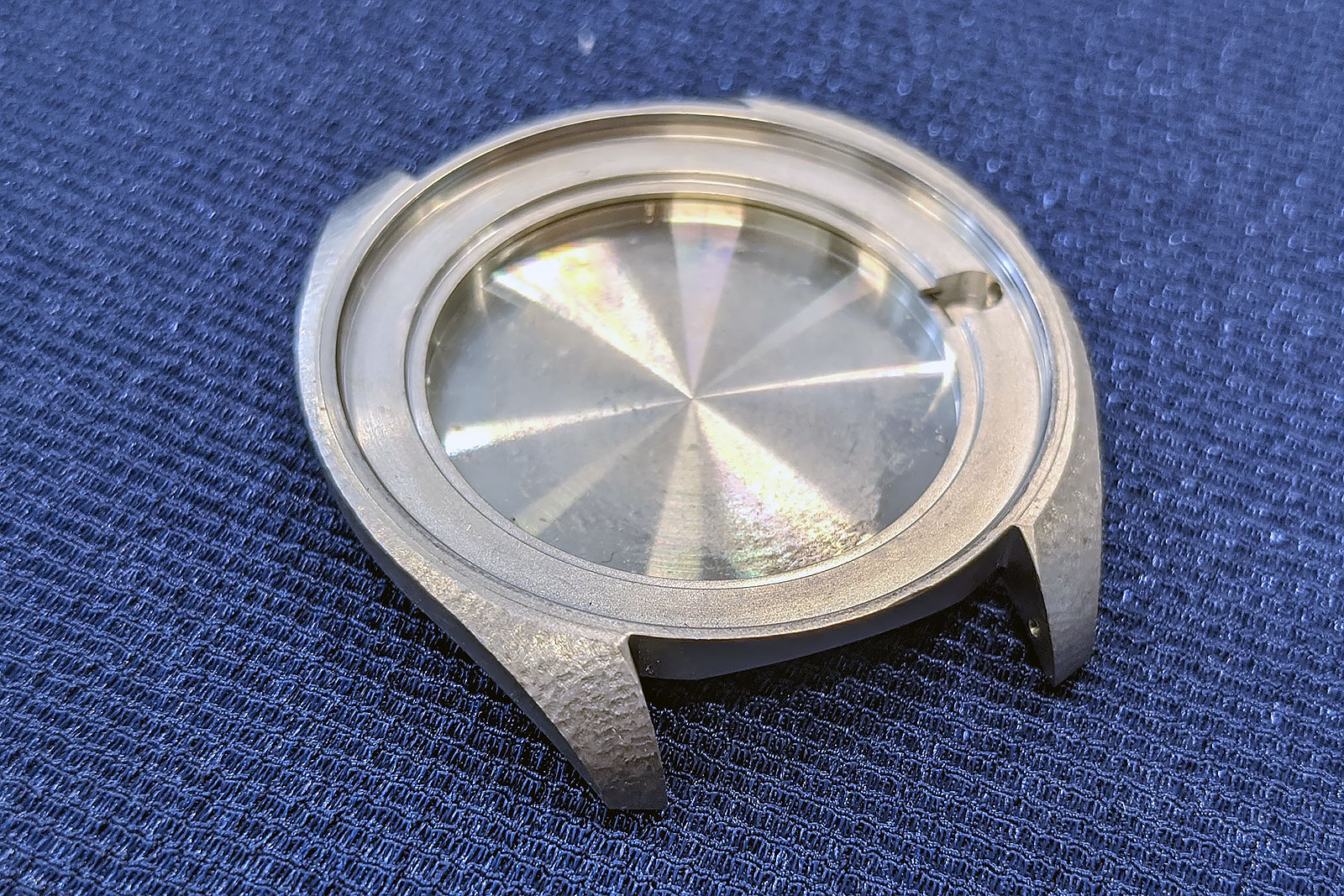
An early prototype case for the SBGZ001 with a different, textured finish
What I am even more struck by are the parts that are not engraved. It takes remarkable skill to engrave on curved surfaces like the lugs, while leaving other areas absolutely untouched and their edges still sharply defined.
Whereas the snowflake-engraved areas of the case have a matte finish, there are tiny facets purposely left in their untouched, polished state so that they stand out in beautiful contrast. These facets are on the lower edge of the bezel as well as a tiny bevel on the inner edge of each lug.
The dial of the SBGZ001 is engraved with a pattern that’s similar to that on the same, giving it an appearance that is quite close to the standard Grand Seiko Snowflake. But on the SBGZ001, the logo and text at six and 12 o’clock are engraved on dial rather than printed.
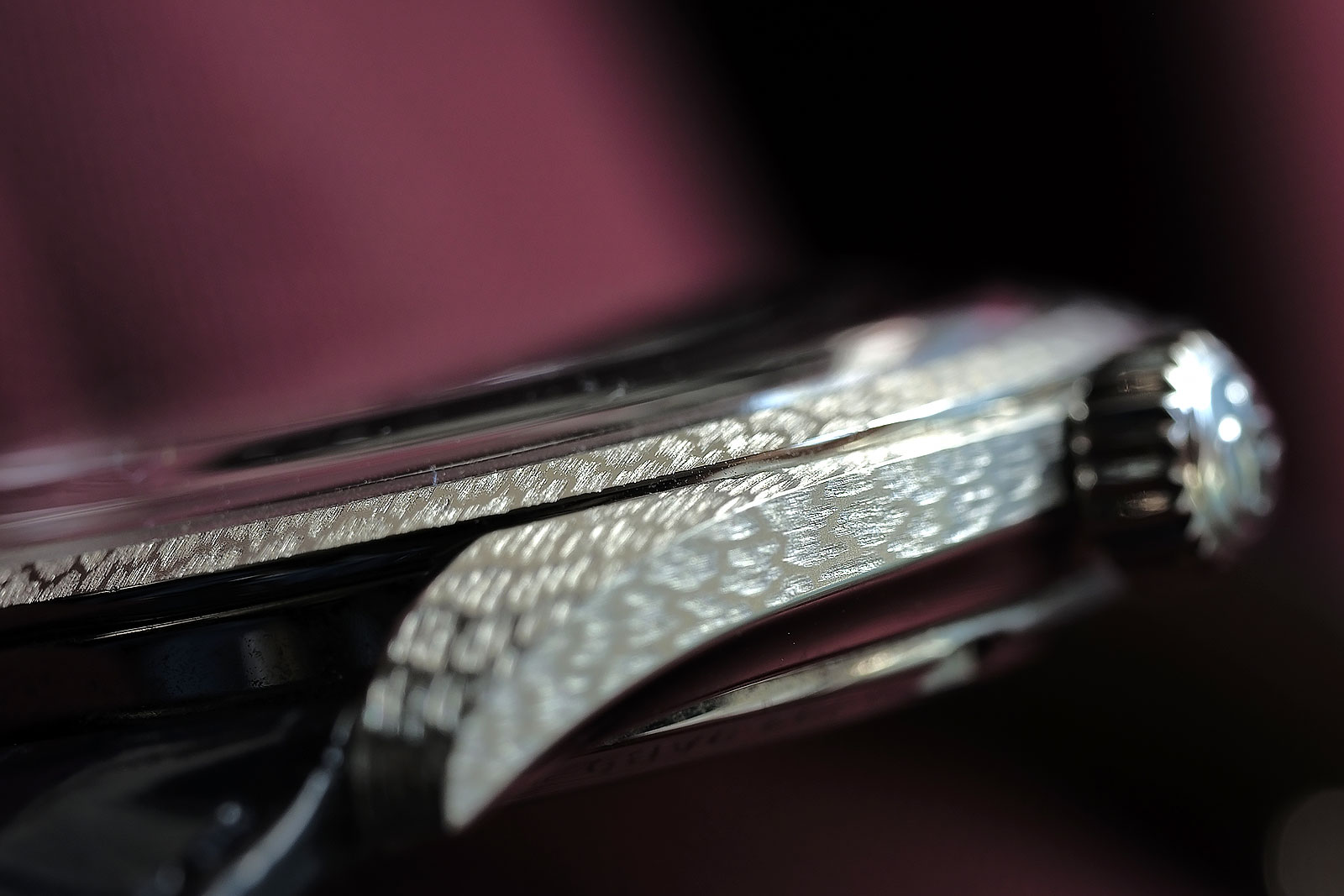
A close up of the polished edge between the bezel and case side of the Grand Seiko SBGZ001
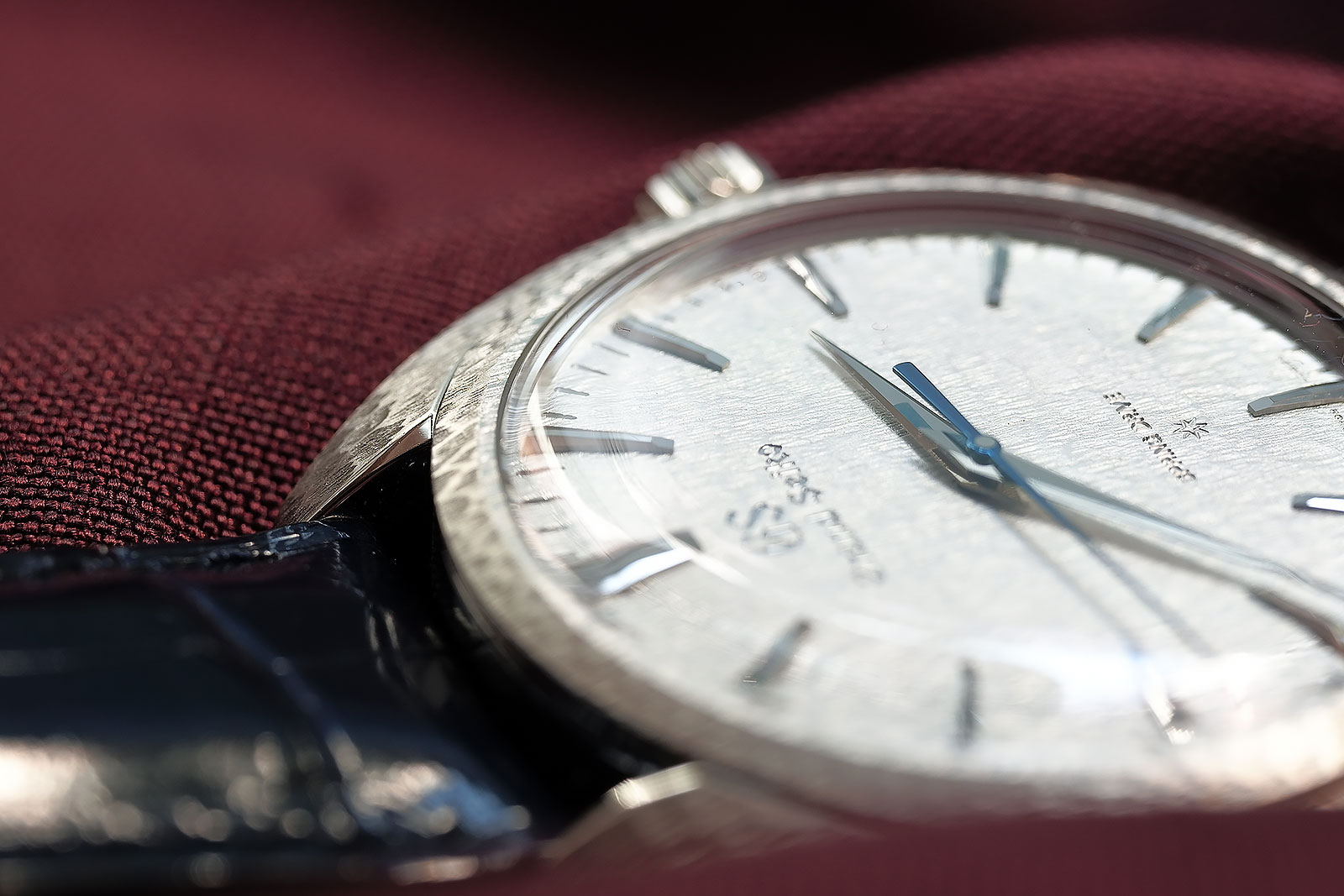
Closeup of the tiny polished facet at the inside edge of the lug of the SBGZ001
Compared to the Eichi II, which is powered by a similar movement, the movement of the SBGZ001, the 9R02, is not just decoratively enhanced but there are improvements under the hood as well. For instance, the new movement has an 84 hour power reserve, rather than the 72 hours in the Eichi II, thanks to twin mainsprings and an improved Torque Return System that recycles excess energy to partially re-wind the mainspring.
And though they share visual similarities and were unveiled at the same time, the 9R02 was developed independent of the movement in the SBGY003, the 9R31.
The 9R02 is the work of the MAS, while the 9R31 is made on the standard production line at Shiojiri. So the 9R02 is significantly finer, with extensive hand finishing that easily puts it in the highest echelons of the craft and on par with Philippe Dufour’s outstanding work.
The barrel containing the mainspring is open-worked in the shape of a bellflower, an emblem of Shiojiri. All edges feature generous, polished bevels, while the plates have a delicate straight grain for the surface finish. Holes for screws and rubies are countersunk and polished, and screw heads shine an iridescent blue.
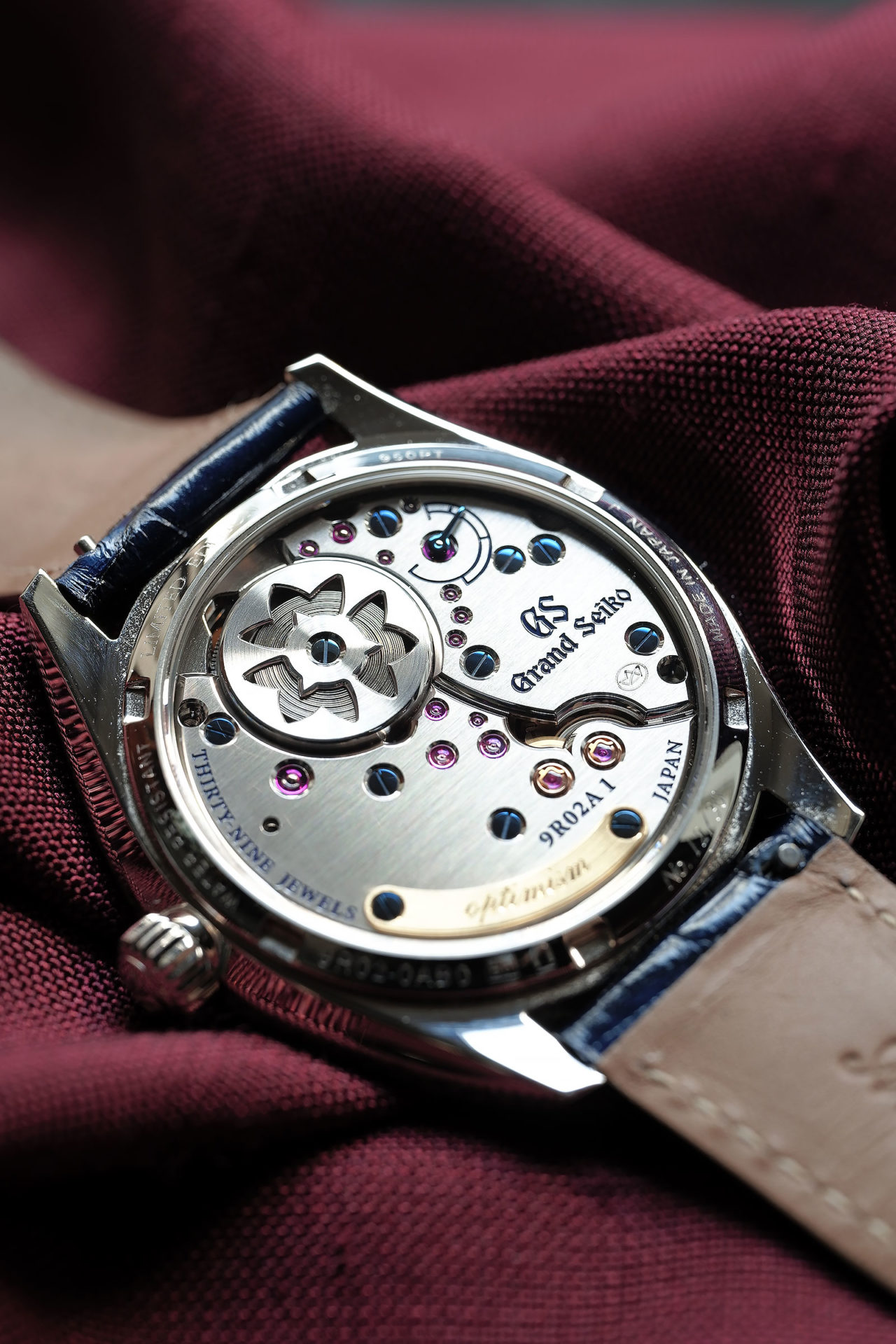
The 9R02
I was curious why the Spring Drive movement has never had its mechanics more exposed. Instead most of the workings are hidden beneath large plates. Hoshino-san explained that more of the movement cannot be exposed because the quartz crystal is very sensitive to light, and it must be carefully sealed.
Like the movement in the Eichi II, the 9R02 movement has its plate split at the flywheel so there is at least some action visible. But the more ordinary 9R31 does not have this special feature, and instead has a full plate that covers everything.
A lovely touch that Grand Seiko has offered to owners of the SBGZ001 is the opportunity to engrave a word or two on the gold plaque on the movement. I chose “optimism” – something always handy to have.
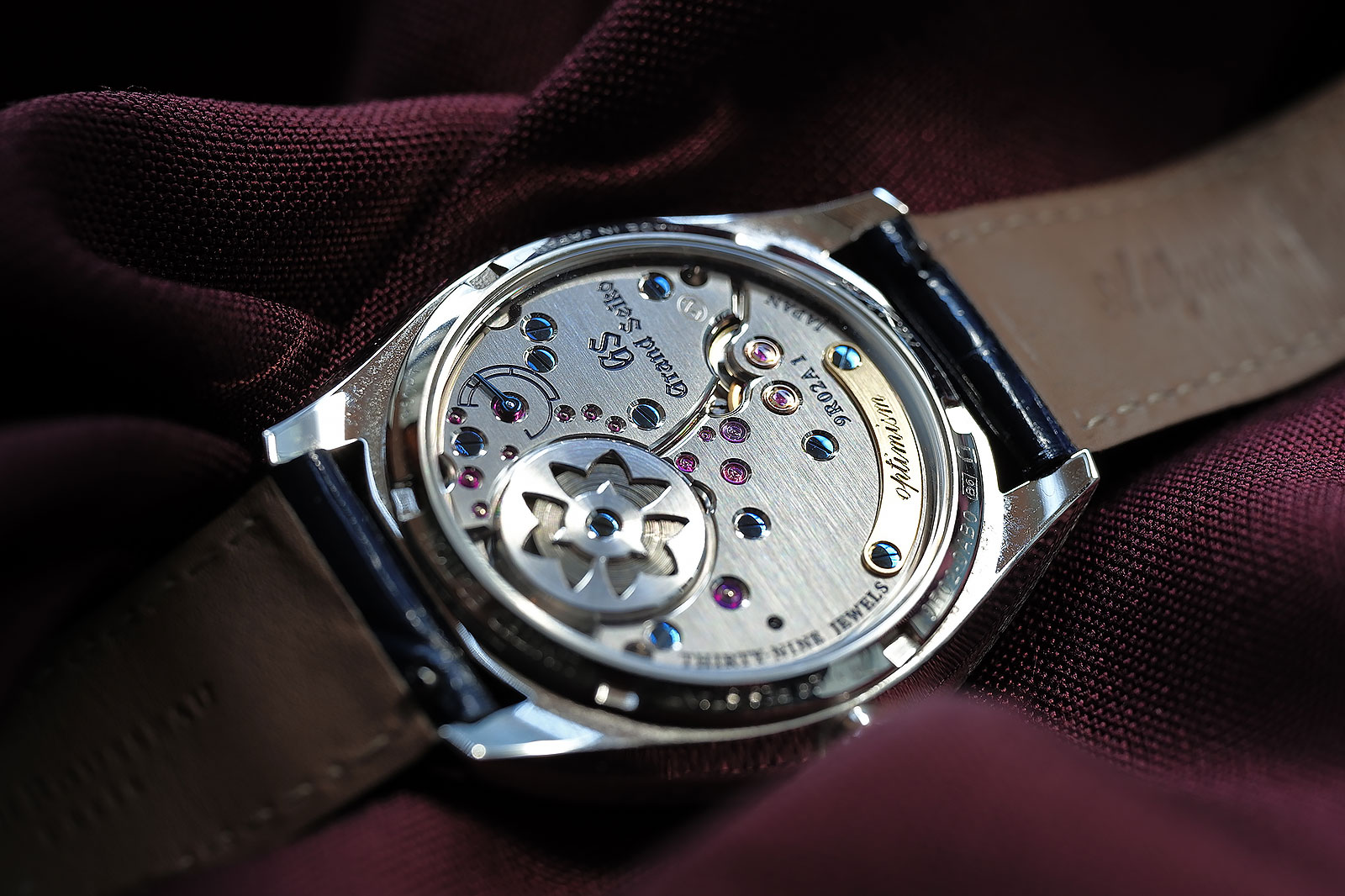
Close-up of the engraved “optimism” plate
As Hoshino-san and I ended our conversation, we discussed his favourite aspect of the SBGZ001. He said it was being able to make a watch that had the dial and case in unity. He added that it was unusual for a designer to have so much flexibility in what they were designing. In most brands, at least some parts must be sourced elsewhere, putting limitations on what can be done. Grand Seiko makes virtually everything in house, meaning product design does not need to start by accounting for a specific source or supplier.
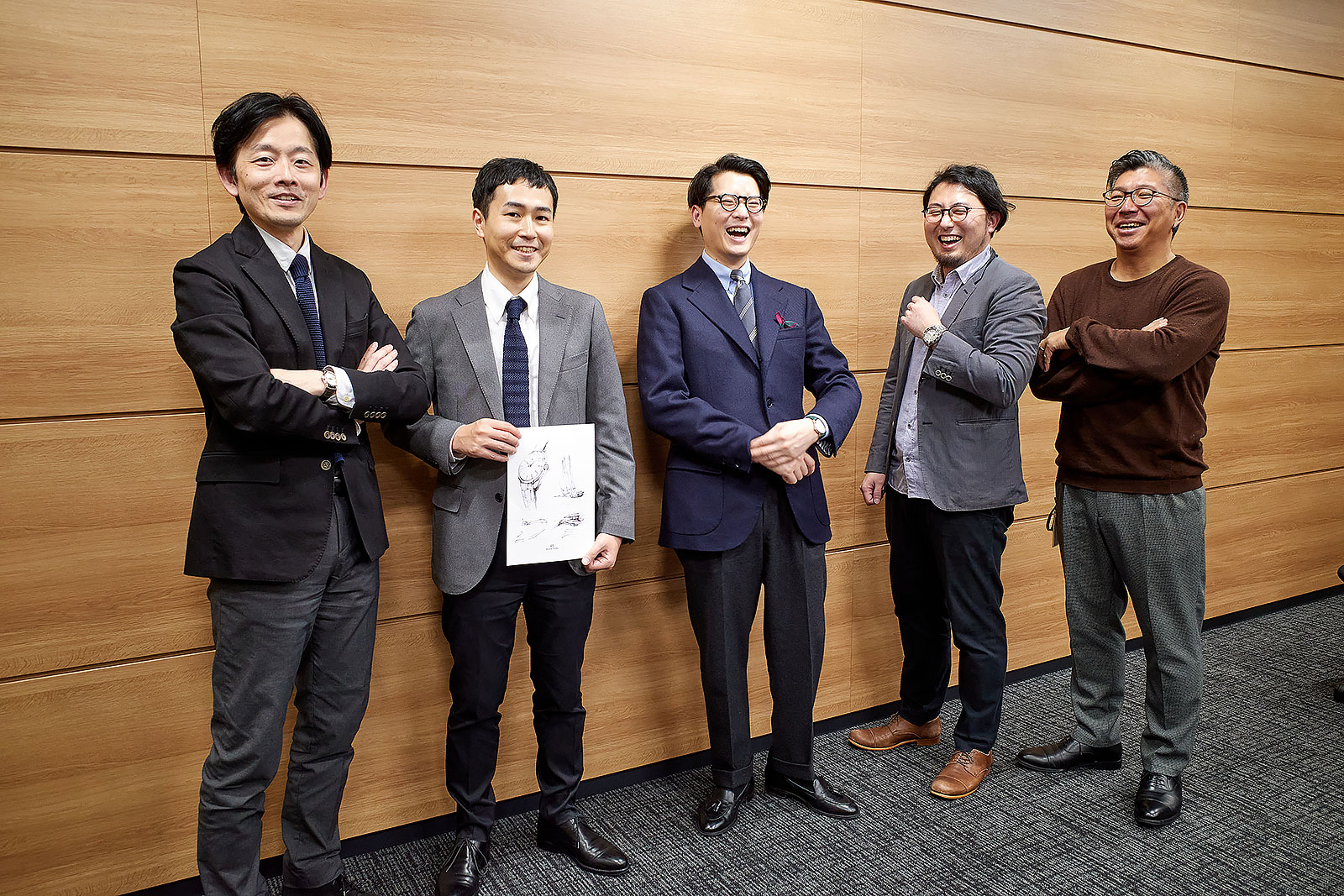
Members of the Grand Seiko design team (from left to right): Junichi Kamata, senior manager of design; Kiyotaka Sakai, designer; Mark Cho, author of this article; Yugo Hibayashi, designer; and Kazunori Hoshino, Micro Artist Studio designer
My own speciality is high-end bespoke craftsmanship in men’s clothing and accessories. I work with individual craftsmen and the scale of what we do is very small, sometimes less than 50 items are produced in a year by certain craftsmen.
I conducted the interviews for this article over two days and was fortunate to have spent extended periods of time with various people at Seiko. It was eye opening to see how products are born in a large company, with the input of various groups of people. It was also reassuring to see that despite Seiko’s size, a product could still be the baby of a very specific person, and Seiko still produces things that are exceptionally made by individual craftsmen on a small scale.
Above all, there is an independent streak to Seiko that I truly admire, one that makes ample room for ingenuity and craftsmanship. It allows technologies like Spring Drive to be created and watches like the SBGY003 and SBGZ001 to be made.
Addendum: I also made a short video on the topic, which you can find on Instagram. And about the movement of the SBGZ001, SJX has written about it definitively here.
Special thanks to Kinuyo Sakata of Seiko for her support in making this article.
Back to top.