Inside Akrivia – Artisanal Manufacturing in Geneva
Making watches with soul.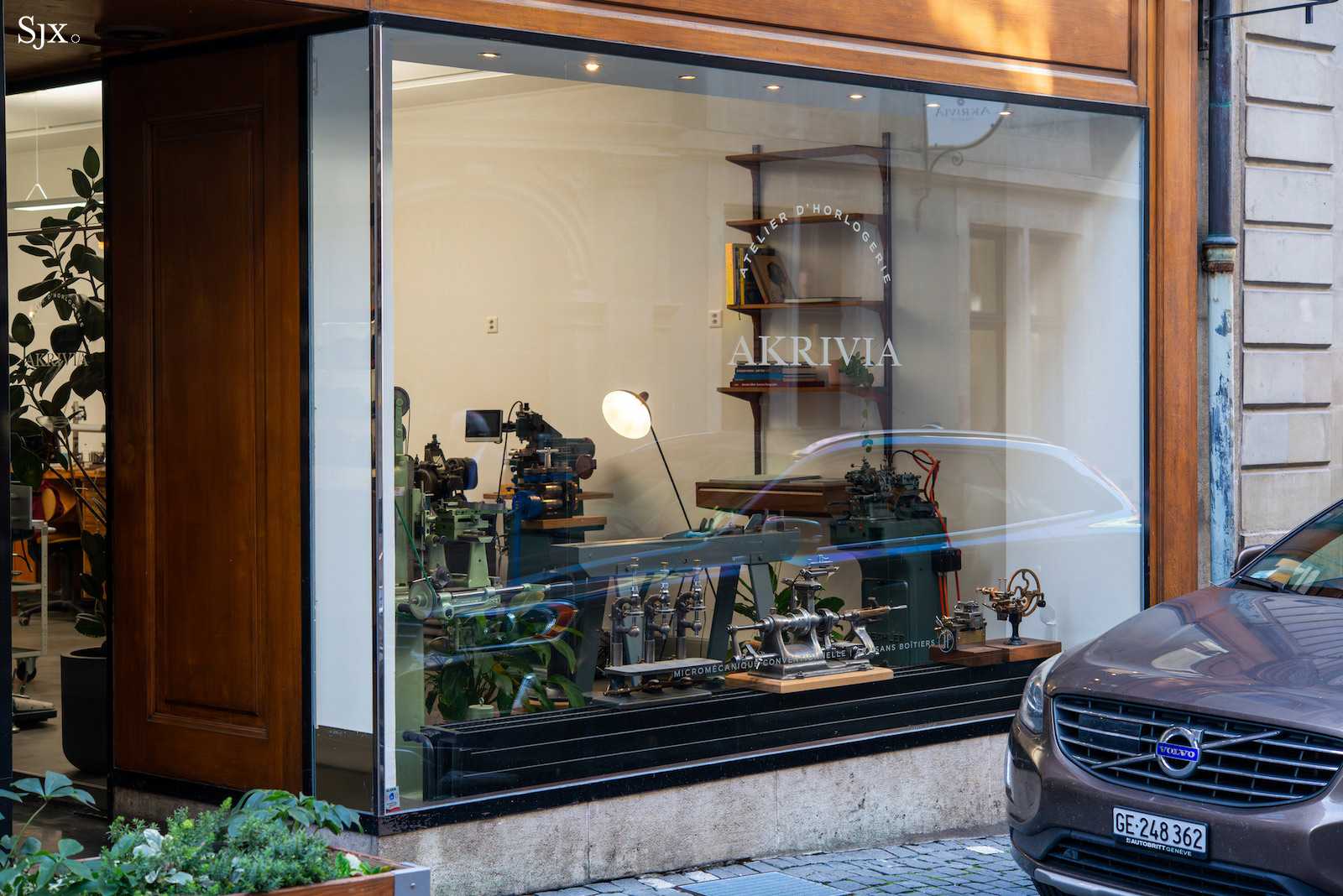
Followers of high-end independent watchmaking are likely familiar with Akrivia and its founder, Rexhep Rexhepi. Akrivia’s work, especially its finishing, has earned widespread acclaim and record auction results. Paradoxically the brand got off to slow start at its founding in 2012. Akrivia only rocketed to prominence with the launch of the Chronomètre Contemporain in 2018 and has been on the ascent ever since.
Now just getting into its second decade, Akrivia has achieved a level of success that often proves elusive to upstart independent watchmakers, many of which have come and gone in the past few years. This success is due to numerous factors, but key among them is the brand’s demonstrated ability to evolve and improve.
I recently had the opportunity to visit the brand’s workshops in Geneva’s Old Town to see how far Akrivia has come and get a hint of what’s in store for the future.
Akrivia today
Today, the brand employs 20 staff, up from just 10 in 2021. Considering its annual production of around 40 watches per year, this puts Akrivia in good company among the most artisanal brands in the industry.
It would be tempting to look at this headcount growth and predict that production will soon increase, but that’s not the case. While the team of watchmakers has grown slightly – it now stands at eight – most of the added roles are go bring more manufacturing capabilities in-house and accelerate product development, along with a few administrative positions.
Mr Rexhepi seems happy with the current size of the operation. It’s large enough to enable him to take on new projects, but small enough to keep admin and complexity to a minimum. Mr Rexhepi prizes the time he spends at the bench – prototype, building watches, and even doing servicing to diagnose problems – and the current size enables him to do just that.
Reliant on suppliers like MHC in its early days, the brand has made significant strides in recent years to bring the most critical operations in-house, so as to have greater control of the final product, and in Mr Rexhepi’s view, to imbue his watches with more soul. Components that were previously outsourced, such as cases, some movement plates and bridges, and straps, are now made in the brand’s workshops.
It’s hard to come up with an exact figure for how “in-house” Akrivia’s watches are today, since the percentage keeps increasing. But Mr Rexhepi and his team are pragmatic, and realise there are still some components, such as screws, that still make sense to source externally for now; his own team’s time is too valuable and better spent on higher value activities.
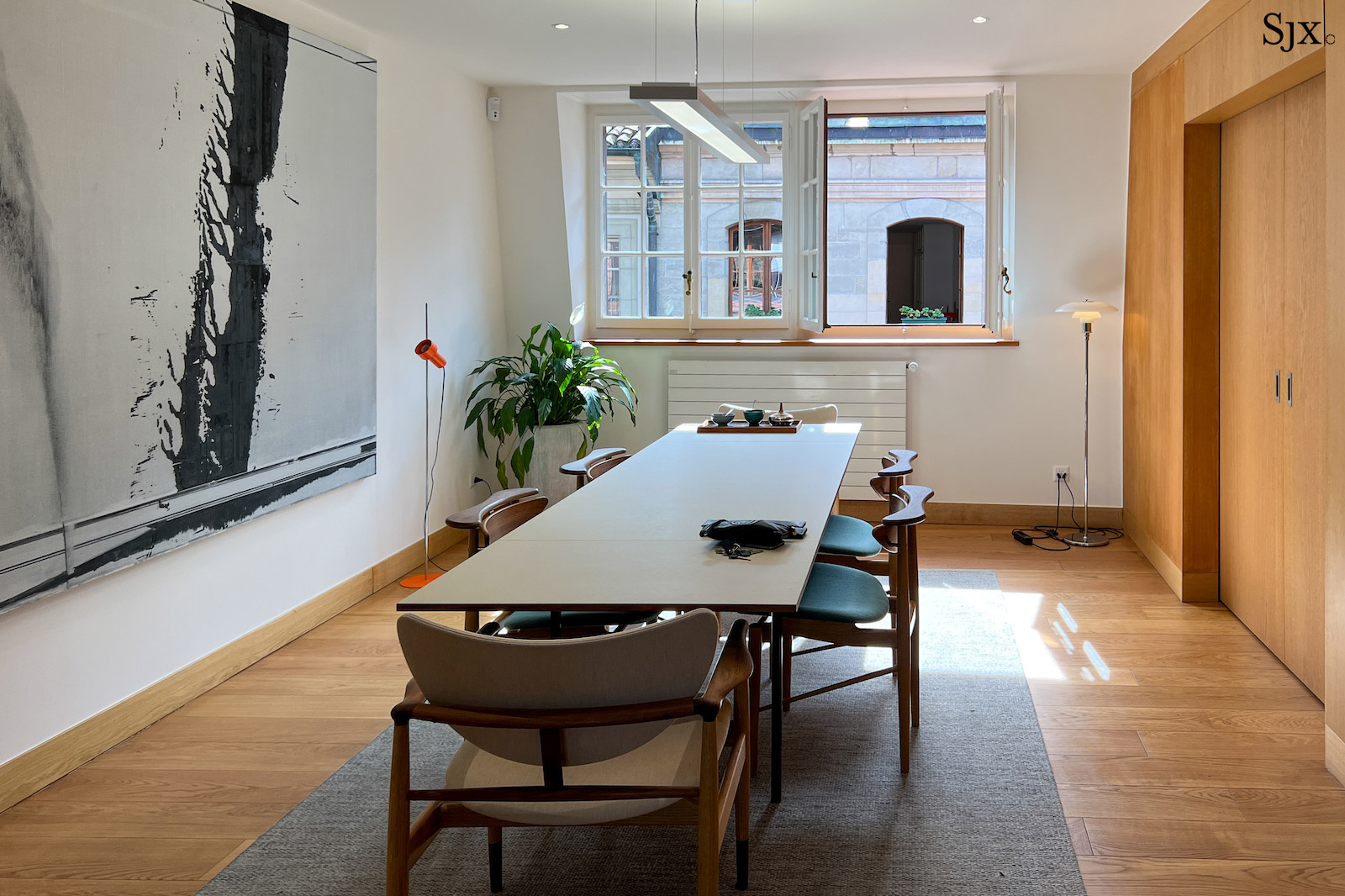
The client reception space
The brand currently operates out of four distinct premises, three of which are mere steps apart from one another, dotted along the historic Grand Rue in Geneva’s Old Town. The fourth is a small facility for micro-machining with several CNC machines that’s staffed by two operators who help produce certain movement components.
The newest of the four locations is an office that’s home to administrative staff and a large office for the technical bureau of engineers and constructors, along with a reception area to host clients.
The atelier
But the heart of Akrivia’s operation is the atelier. Situated at ground level on a quiet street, the open concept floor plan provides a unique spectacle for passers-by outside.
This is where each watch is finished, assembled, adjusted, cased, and tested by a single watchmaker from start to finish. In contrast to larger brands like FP Journe, which has a dedicated finishing department and where watchmakers start with a kit of finished components ready for assembly, the watchmakers at Akrivia are responsible for finishing as well.
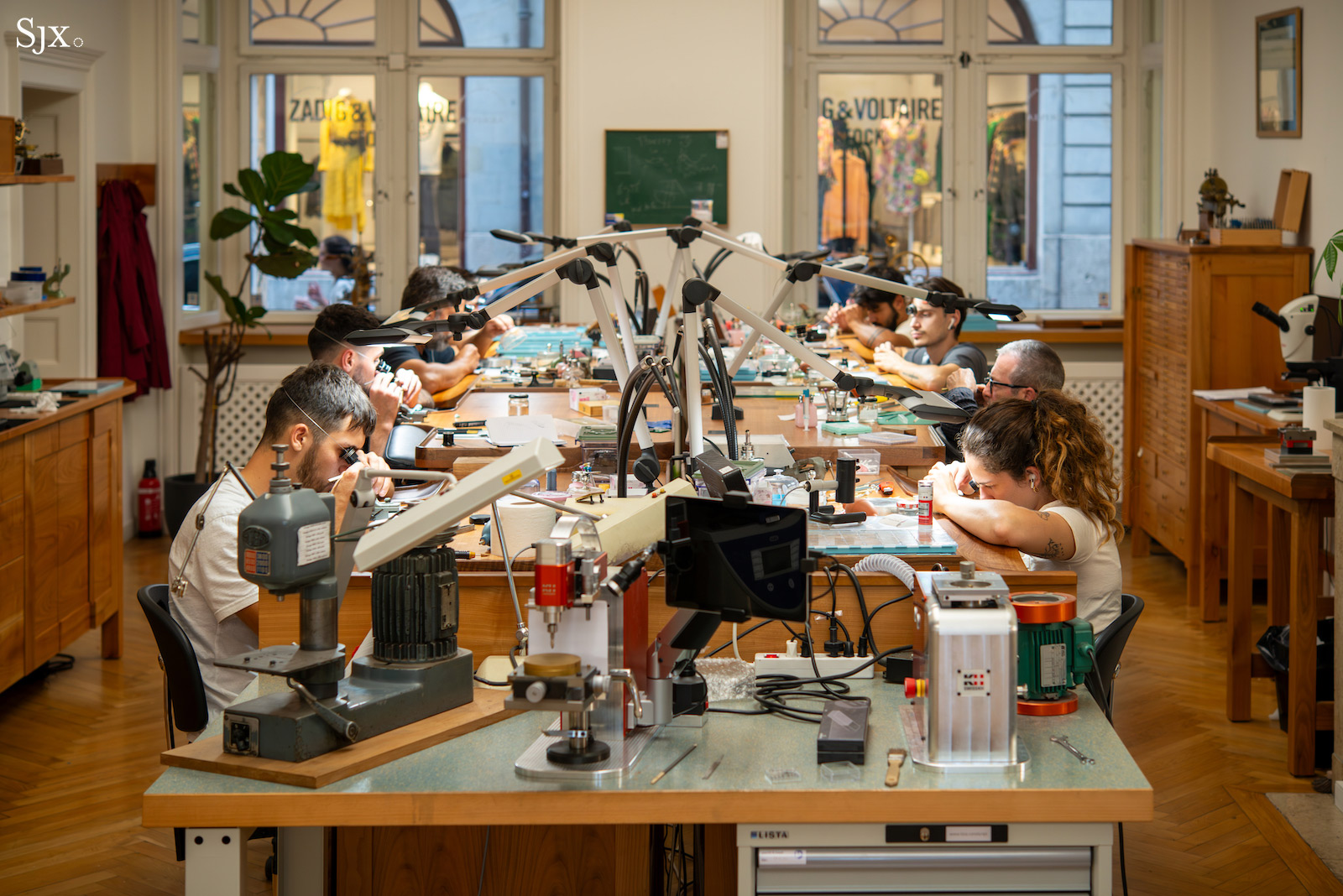
Akriva currently employs a team of eight watchmakers
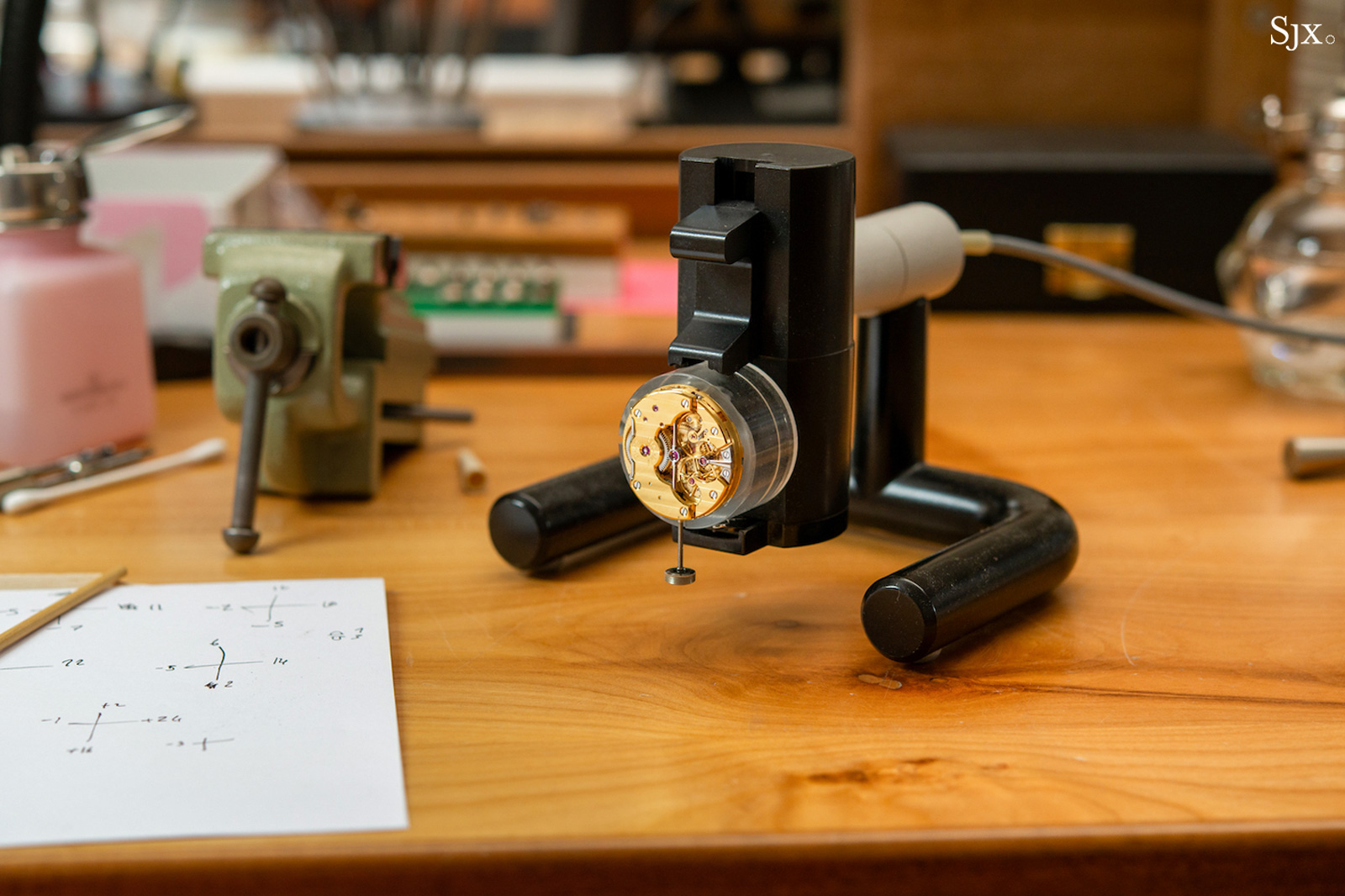
An AK-06 in progress.
Akrivia is perhaps most well known for the quality and style of its finishing. The house style is typified by wide, almost exaggerated anglage and extravagantly black polished steelwork. And critically, the brand never misses the chance to add an inward angle.
This makes watchmaking at Akrivia a very different job, and one that requires even more dexterity, patience, and skill than is typically needed to be a watchmaker. And there are not many people suited to it. The few that are tend to be discovered through word-of-mouth.
But for a certain type of watchmaker, this level of responsibility and ownership is a major benefit that cannot be matched by larger brands. And in an industry where upward mobility can be slow, brands like Akrivia give ambitious and talented watchmakers a place where they can accelerate their development and showcase their abilities.
I commented that by giving the watchmakers so much training and autonomy, Akrivia is likely training the next generation of superstar independent watchmakers; my host acknowledged this with a laugh adding, “Yes, but hopefully not too soon!”
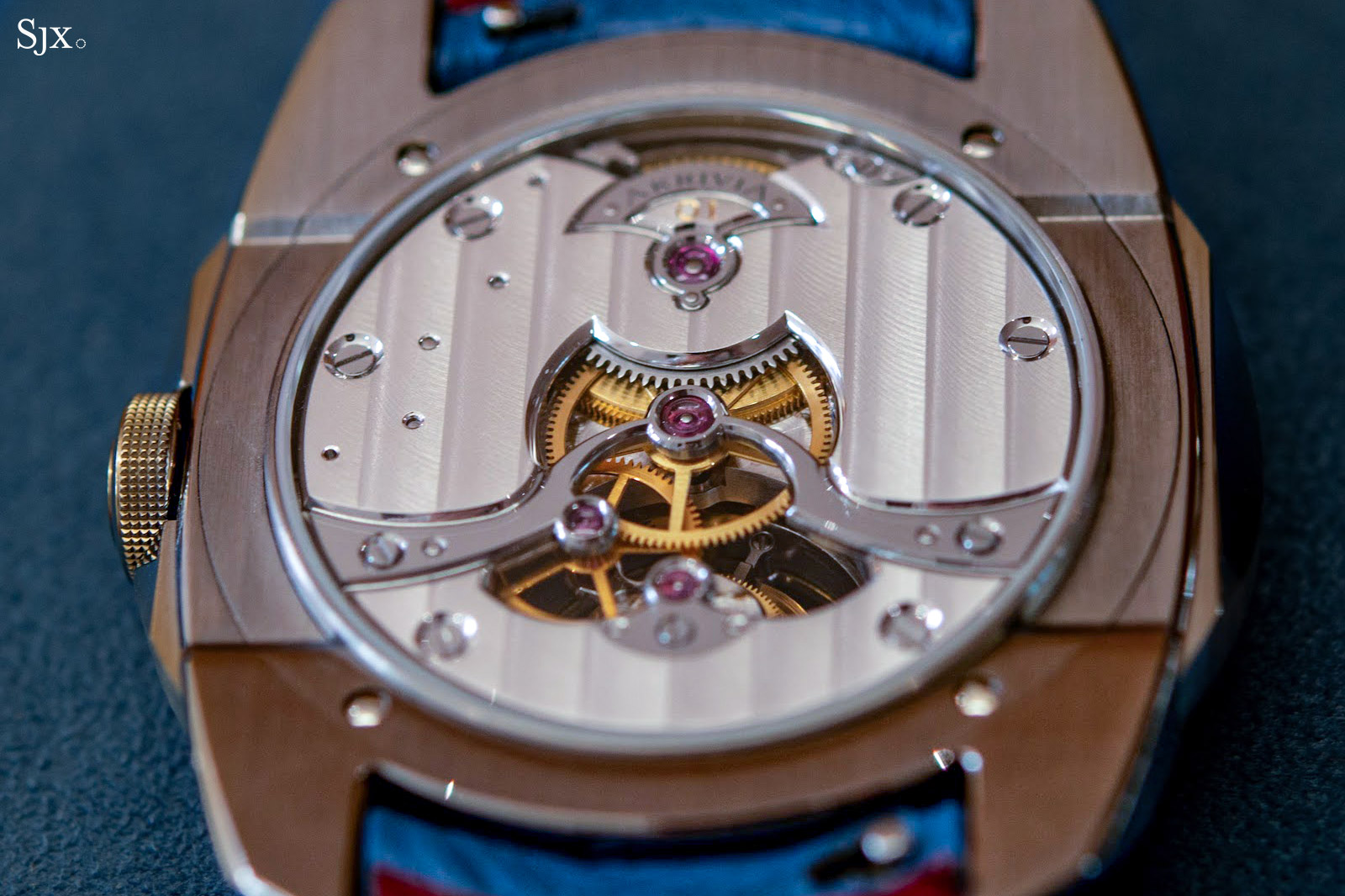
Akrivia never misses an opportunity to add an inward angle.
Akrivia x JHP
Akrivia made headlines in 2019 by attracting legendary case maker Jean-Pierre Hagmann out of retirement, to help make Akrivia’s cases and train the next generation in the traditional methods of case making. This was widely viewed as a milestone for Akrivia, which further contributed to the brand’s differentiated level of craftsmanship.
In the industry today, most watch cases are made using CNC machines, and the knowledge required to make cases by hand is slowly disappearing. After a storied career, Jean-Pierre Hagmann, widely known by his maker’s mark “JHP”, decided he had more left to give and is now an early morning fixture at the workshop, transmitting his lifetime of accumulated experience to two other case makers who have joined the team.
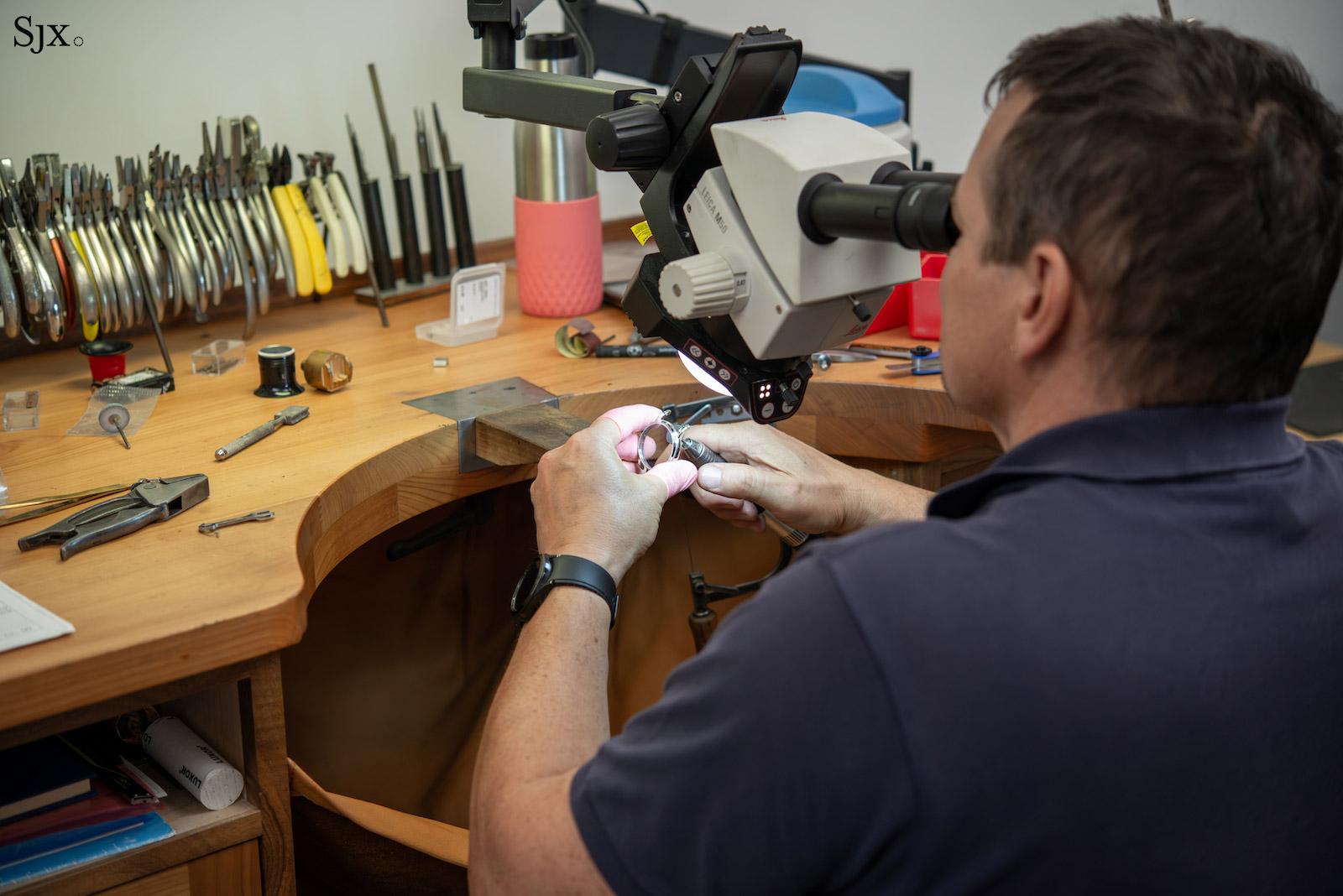
A platinum RRCCII case in progress
Since it opened in 2019, the case making workshop has roughly doubled in size, forcing a move to new premises further up Grand Rue, to an outstanding location across the street from the watchmaking atelier. The original space is being repurposed to become the brand’s strap workshop – more on that later.
Sharing this new space is the logistics office. Akrivia recently hired a logistics specialist for the first time, to help improve efficiency now that the team is getting larger.
With the assistance of lathes and other analog rotary tools, the craftsmen in this workshop produce cases for the RRCCII, as well as all future Akrivia watches and special projects like the recently introduced LVRR-01 Chronographe à Sonnerie. Making cases this way is slow but results in cases with more nuanced detail than those that are produced using CNC.
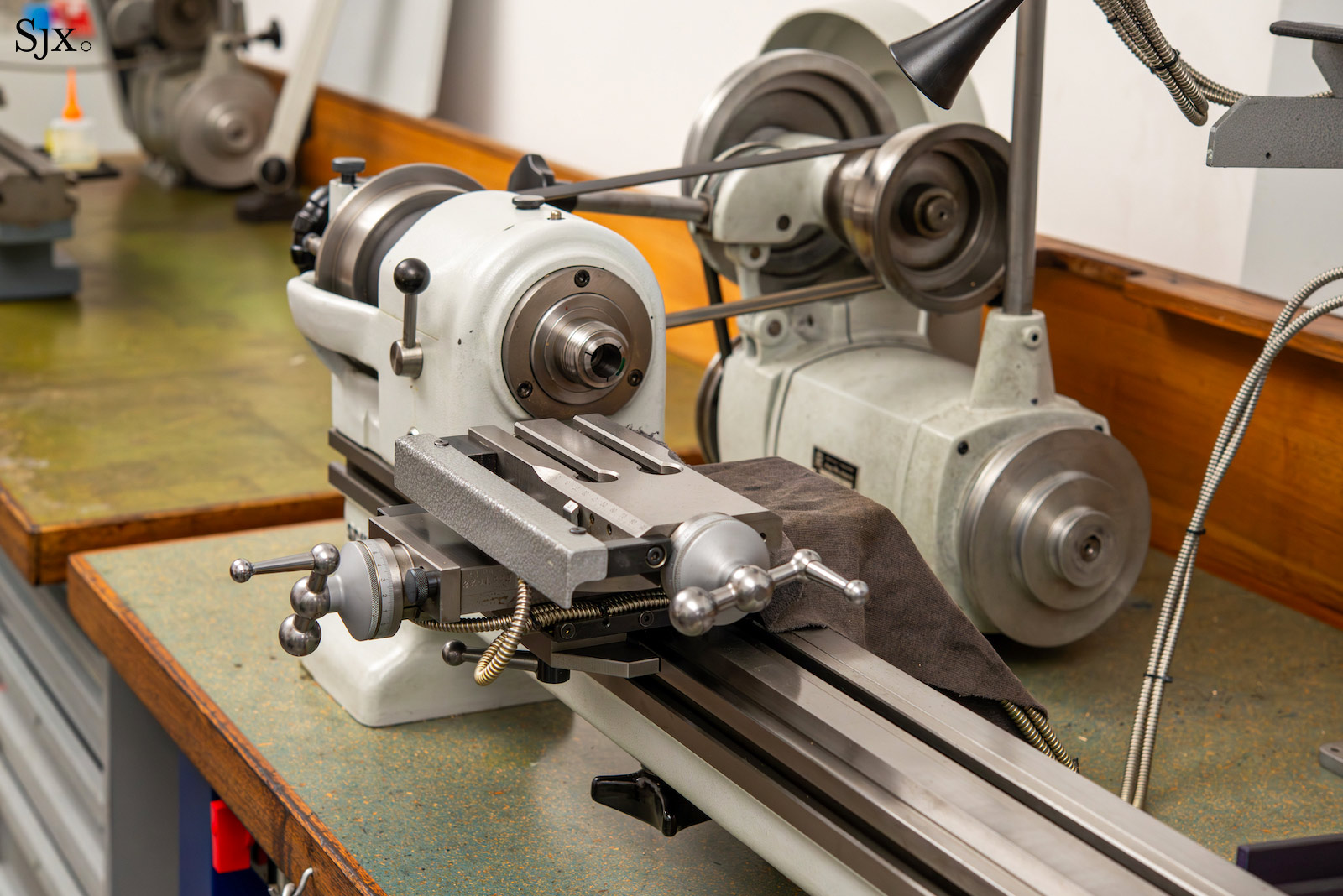
Not just a pretty face: this lathe is currently used to make Akrivia cases
The future starts now
Though Akrivia has now been producing watches for more than a decade, the brand’s best years remain ahead. In fact, Mr Rexhepi has a clear product vision that will keep the team busy for the next 10-15 years.
And Akrivia is building this future now. There are now four engineers working on-site in a new office above the atelier. Naturally, most of what they’re working on remains secret, but during my visit one of the engineers used a CAD program to demonstrate how they designed the return-to-zero functionality of the RRCA movement in the Chronomètre Antimagnétique for Only Watch.
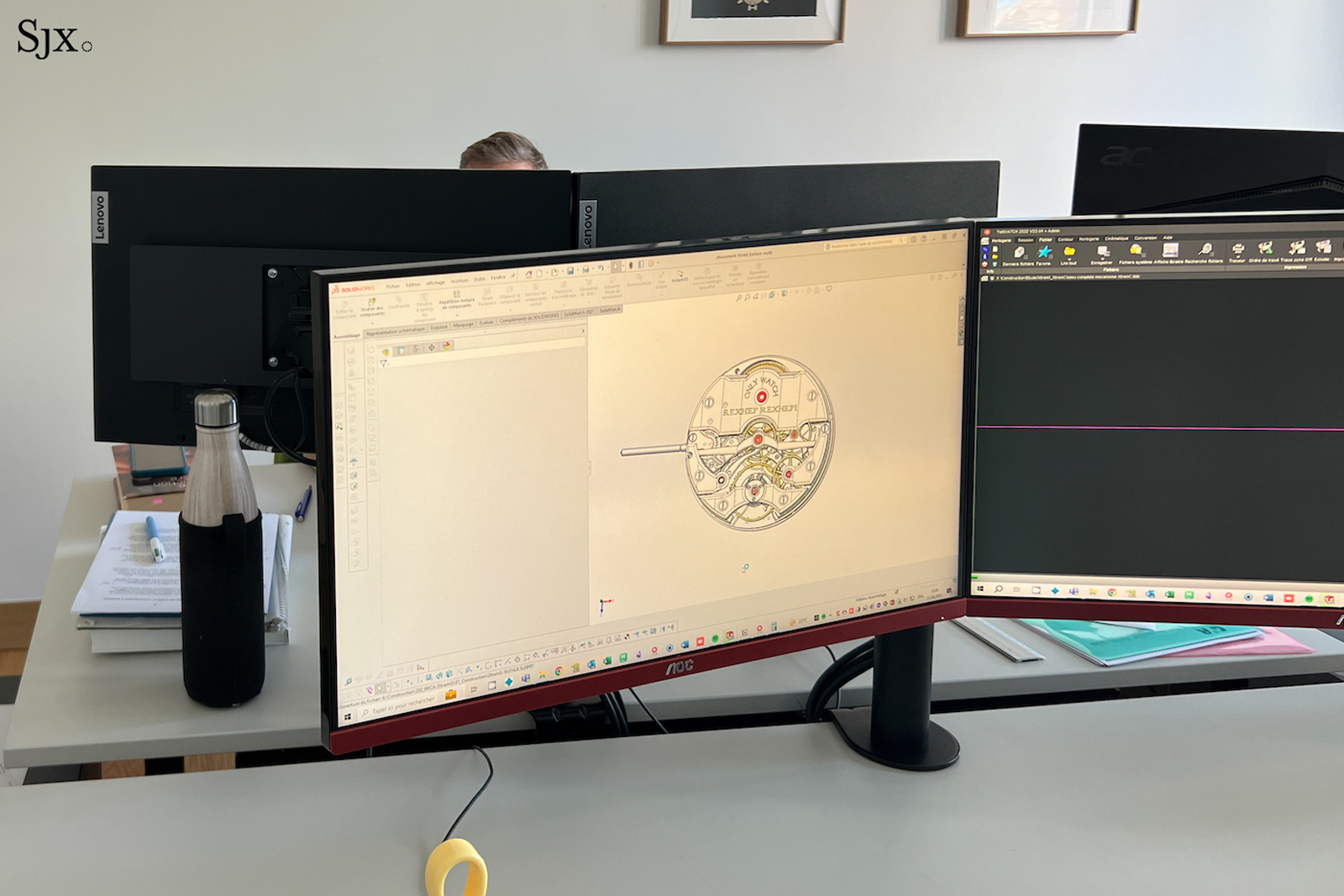
The RRCA in its digital form
Four engineers in a team of 20 is a lot of engineering horsepower for such a small brand, and a sure sign of good things to come. For context, MB&F employs seven engineers and has developed 20 different calibres in 17 years (some of which were created with external help). This emphasis on new projects is encouraging, and demonstrates a commitment to building a lasting business.
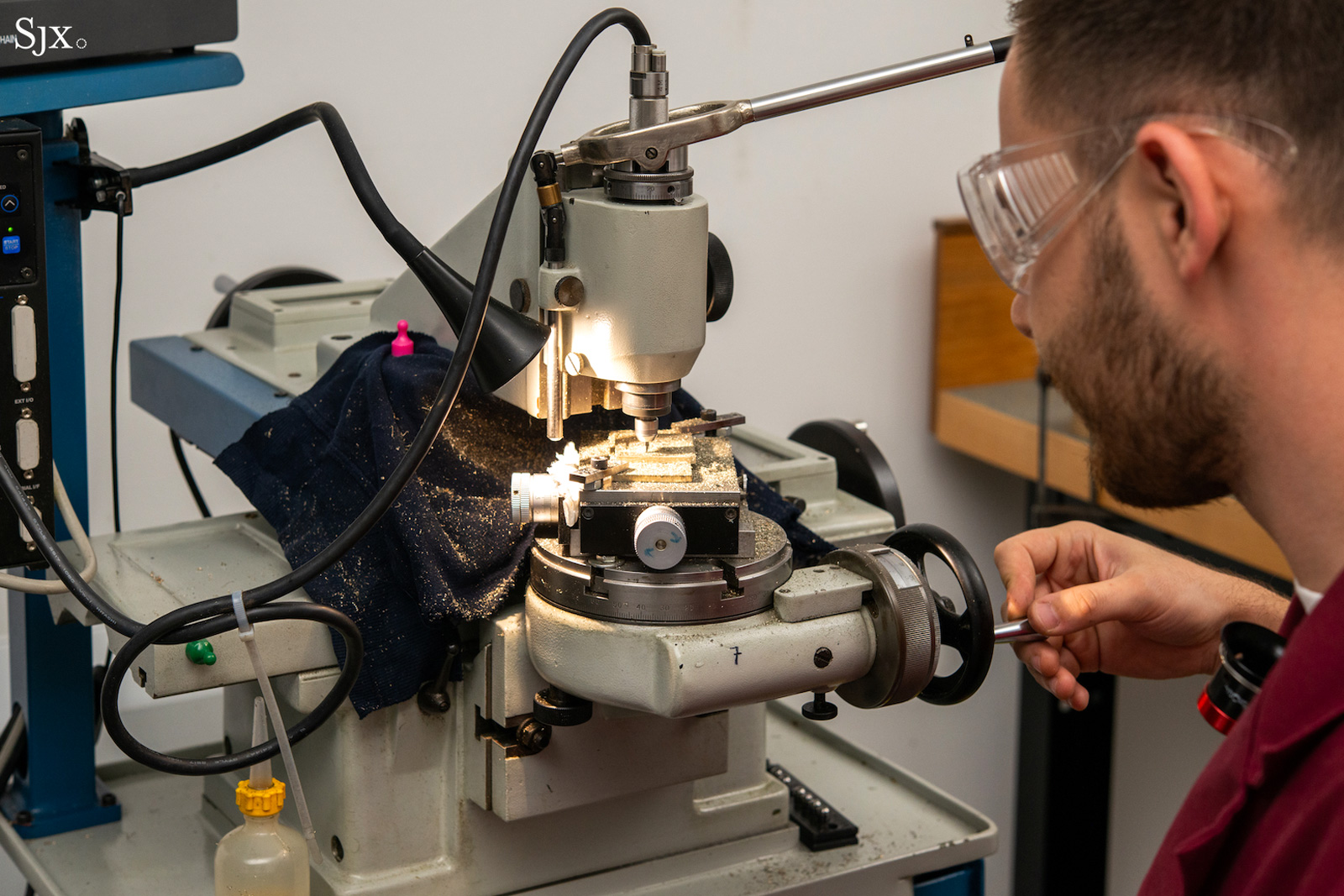
Prototyping at Akrivia
Akrivia is also able to bring its digital creations to life almost in real-time thanks to the prototype department, which shares the case making workshop with Jean-Pierre Hagmann and his team. Using lathes, jig borers, and other manually operated tools, machinists can readily produce one-off components to test new ideas; a capability missing from many industrial brands.
In-house straps
One of Akrivia’s most recent initiatives is its new leather workshop, where the brand is now able to produce its own straps in-house. This workshop was previously home to the case making workshop before its move up the street.
This gives the brand true creative freedom when it comes to meeting a bespoke request; they even have the capability to emboss a client’s name on the inside of the strap.
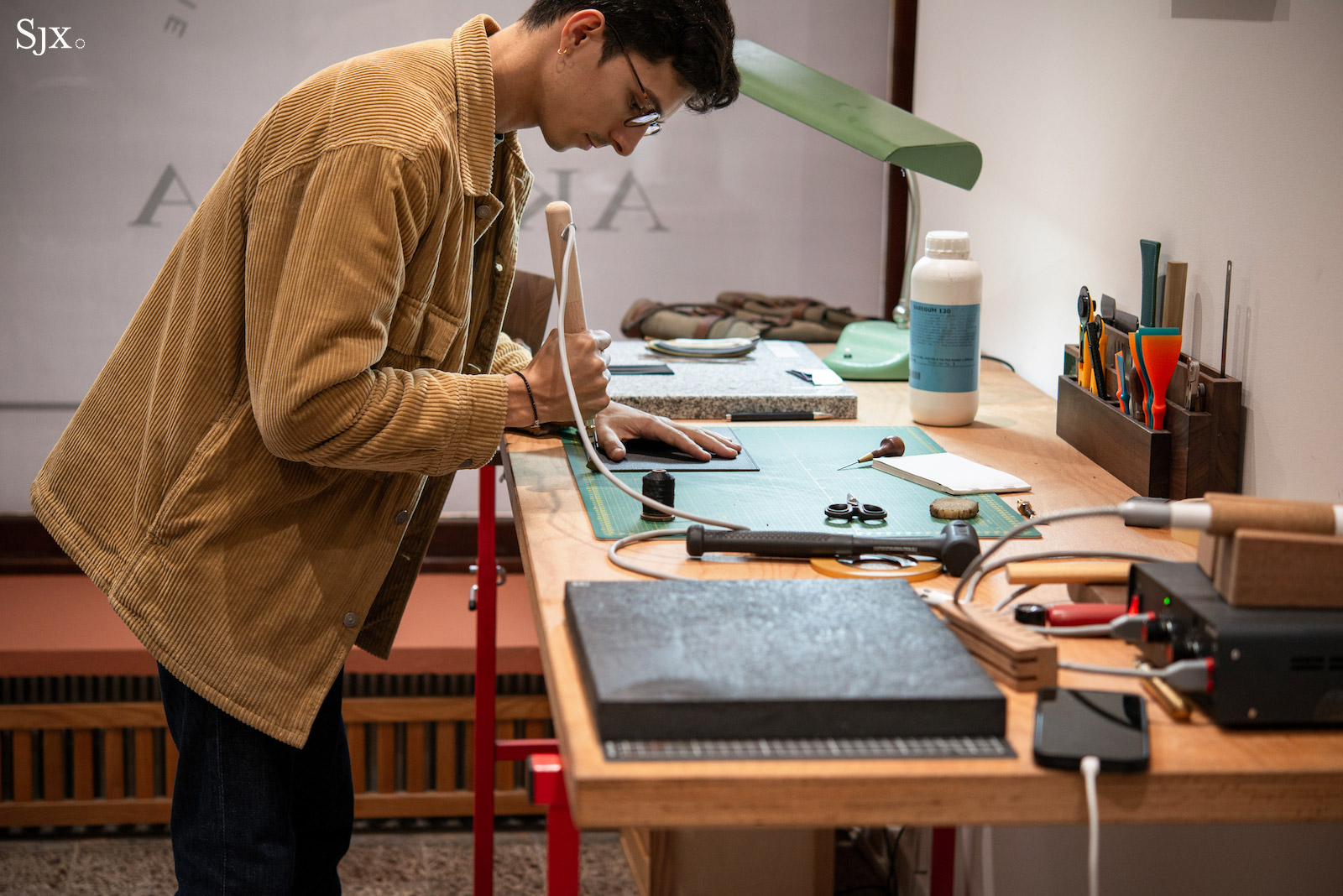
Alex recently joined the Akrivia team to lead strap production
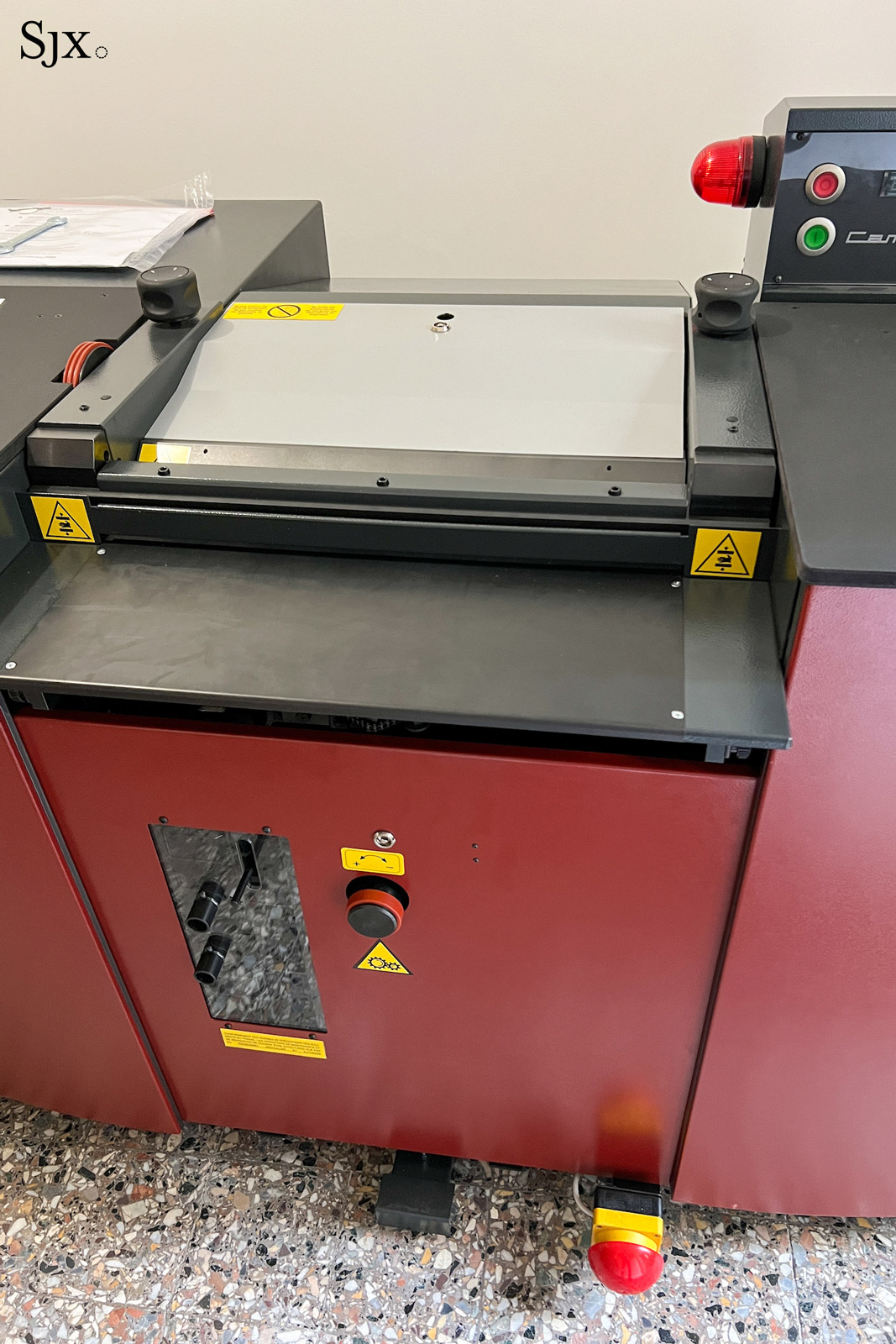
A machine for thinning leather
The strap making process is more complex than it might seem. In its raw form, animal leather is too thick to be turned directly into straps. For this reason, specialised equipment is used to slice the leather along its length – like a bagel-slicer but for watch straps.
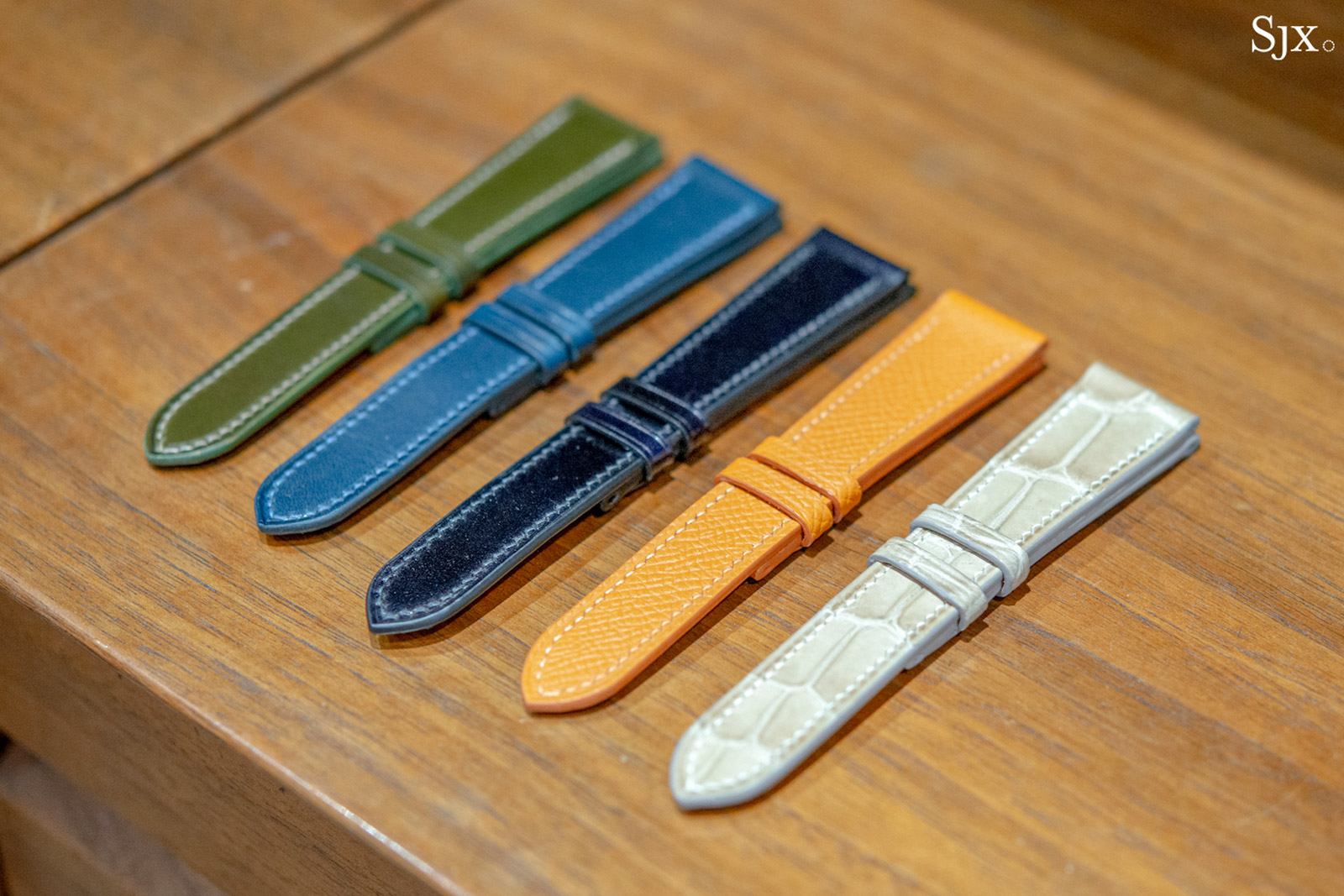
Akrivia-made straps
Summary
Akrivia has been around for more than a decade but has managed to maintain the energy of a brand that has just burst onto the scene. The watchmakers are young and hungry to prove themselves, and Mr Rexhepi has proven himself capable of delivering multiple successive hits.
The fact that Louis Vuitton chose Akrivia as its anchor collaboration to kick off its new independent watchmaking initiative is telling, signalling where the locus of influence has shifted in the field of independent watchmaking in recent years.
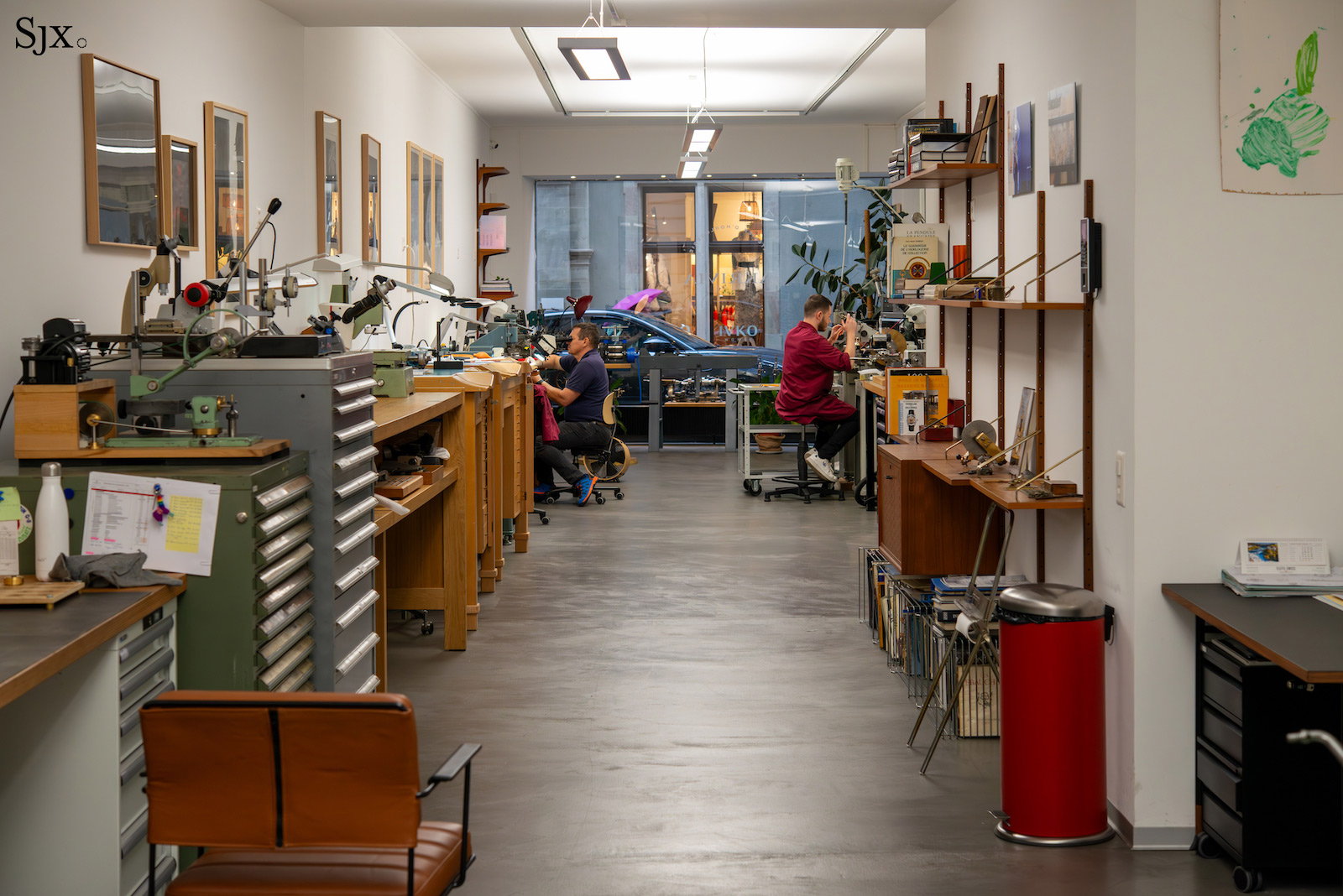
Putting real watchmaking on view.
Furthermore, the move to draw Mr Hagmann out of retirement has proven to be a significant differentiator in an increasingly crowded field. Not only that, it’s beneficial to the industry as a whole to have his wisdom passed down. It’s a win-win; collectors appreciate the craftsmanship and exclusivity of a JHP case, and are able to feel like they are underwriting the continuation of traditional craftsmanship in the process.
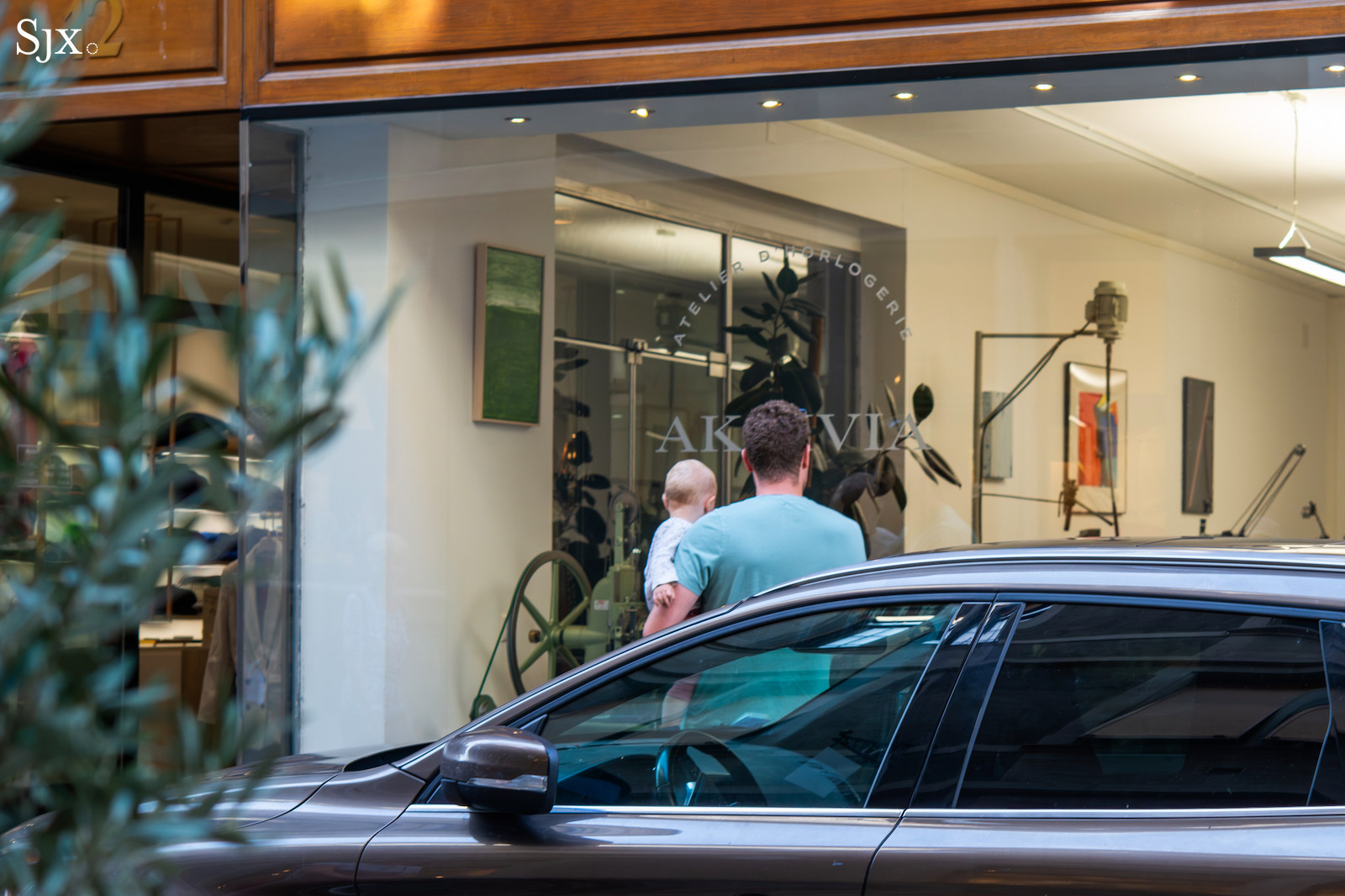
Passers-by taking a moment to enjoy the view into the case making workshop.
And then there’s the location. To a Geneva resident or tourist walking through the city streets, there’s not much to see in terms of real watchmaking. While Geneva’s Old Town is packed with watch boutiques, most production has moved to the suburbs; the district of Plans-les-Ouates, for instance, is nicknamed “Plans-les-Watch” due to the number of brands located there.
By setting up its atelier the way it has, with watchmakers and artisans visible at street level, Akrivia has added a significant cultural landmark to the map of Geneva. By involving the community in this way, Akrivia is promoting not just itself but the entire concept of artisanal independent watchmaking. And it seems to be working; every time I walked by, there were curious pedestrians lingering in front of the windows, visibly enthralled by the process of watchmaking. As a lover of watches, this warmed my heart.
Back to top.