Up Close: Biver Automatique
A simple watch executed elaborately.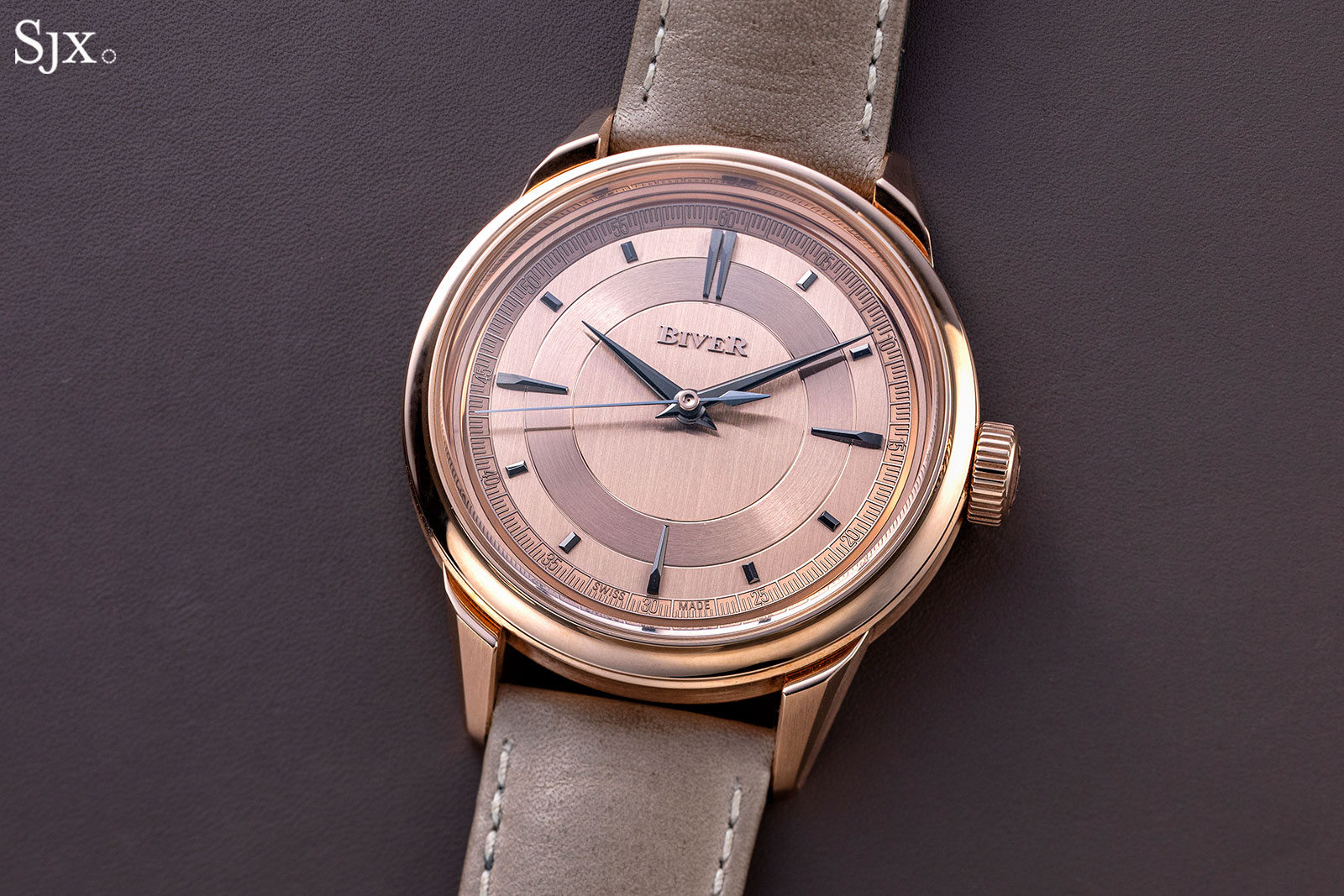
The second watch launched by Biver, the Automatique is a three-hand time-only, functionally simple but elaborately executed. Even the base model has a surprisingly complex dial, but the Automatique is really all about the JCB-003 movement, which is a micro-rotor calibre that ranks up there as one of most impressive recent self-winding movements.
Established by Jean-Claude Biver and his son Pierre, Biver got its start with a far more complicated watch, but the Automatique is arguably more impressive because it’s a simple watch executed in a complicated yet cohesive manner.
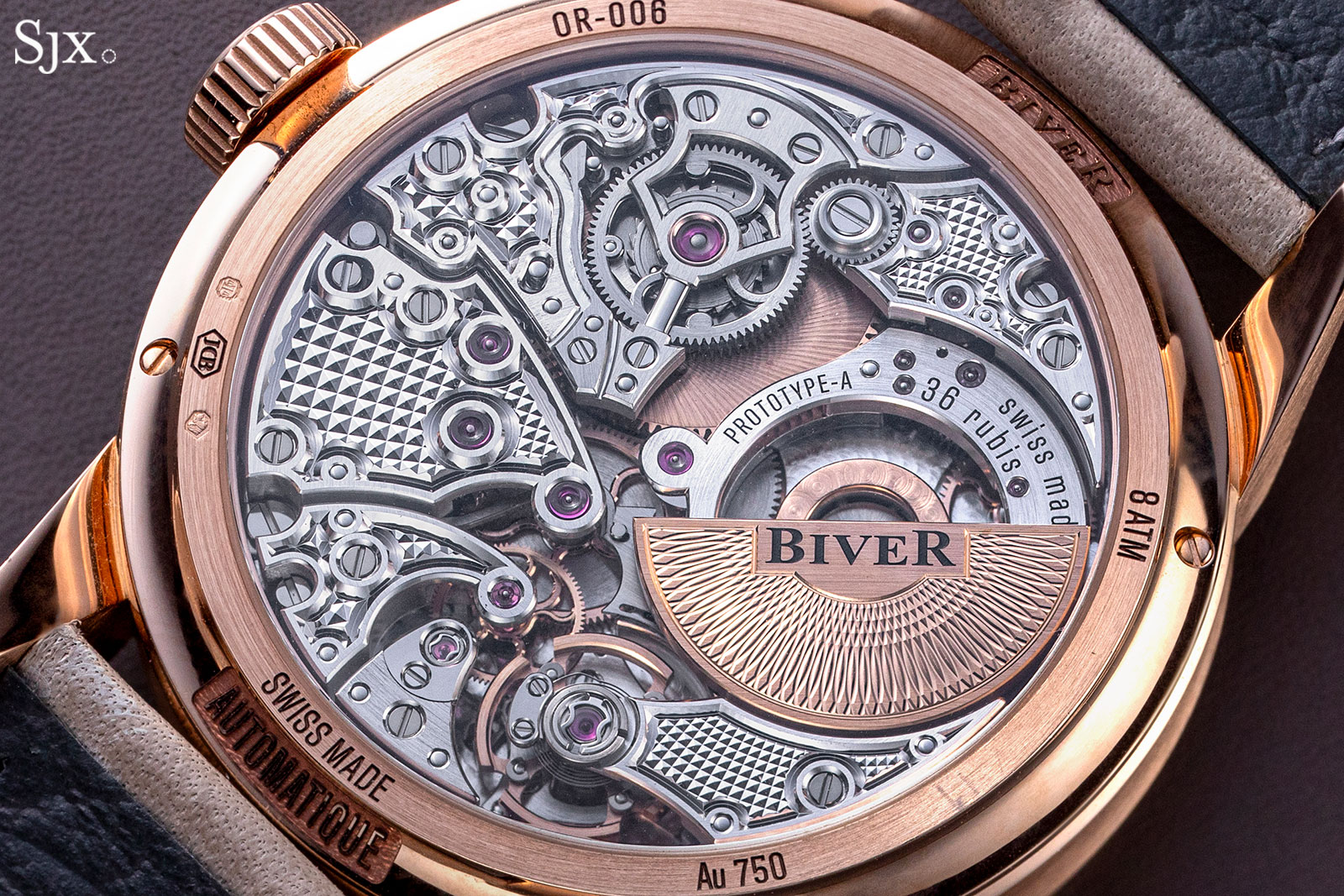
The JCB-003
Initial thoughts
Yet another time-only watch with a dressed up movement and hefty price tag – the formula feels a little worn out now. So the Biver Automatique surprises on the upside. I like it. The design is appealing and cohesive, while the movement is impressive.
In contrast, when Biver debuted with the Carillon Tourbillon minute repeater, I thought “the quality is unmistakeable, the aesthetics are lacking”. The Automatique lives up to the same levels of quality – and maybe even more – but it is instinctively appealing, even considering the price.
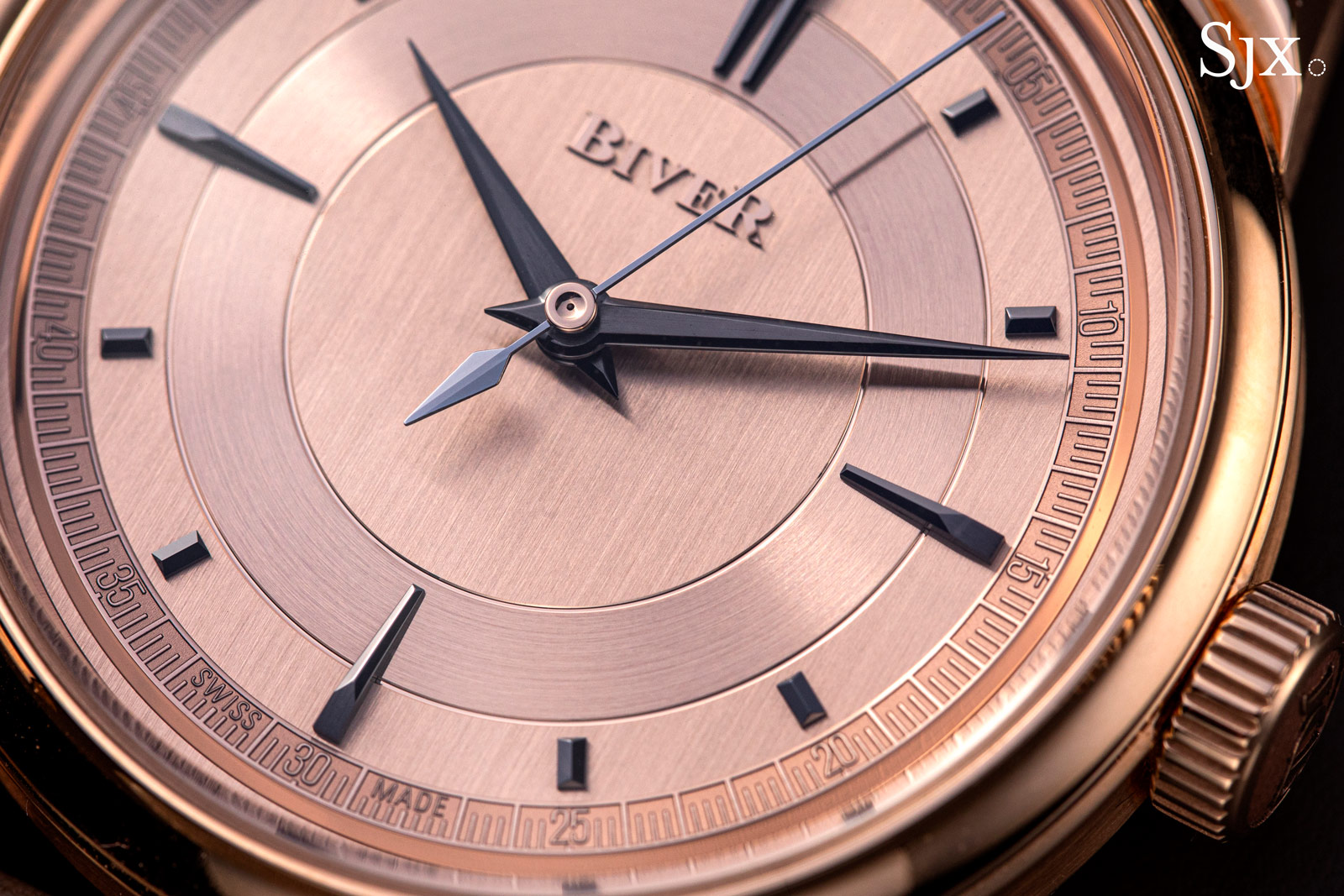
The solid gold dial of the entry-level version in rose gold
Even though Biver is not an artisanal independent brand in the conventional sense of the word since neither of its founders are watchmakers, the JCB-003 movement is executed to a standard that equals many artisanal independents. The construction is thoughtful and sophisticated, while the finishing is top class.
If anything, the JCB-003 has too much decoration. The construction already incorporates numerous aesthetic flourishes like a grande sonnerie-style winding click, giving it an eye-catching level of visual complexity for a time-only movement.
But the visual landscape is further complicated by the guilloche on the bridges, which I would have done away with in favour of traditional surface finishing like striping or frosting. I am sure guilloche is more time consuming and expensive than Côtes de Genève, but I prefer a simpler bridge finishing for its visual lightness.
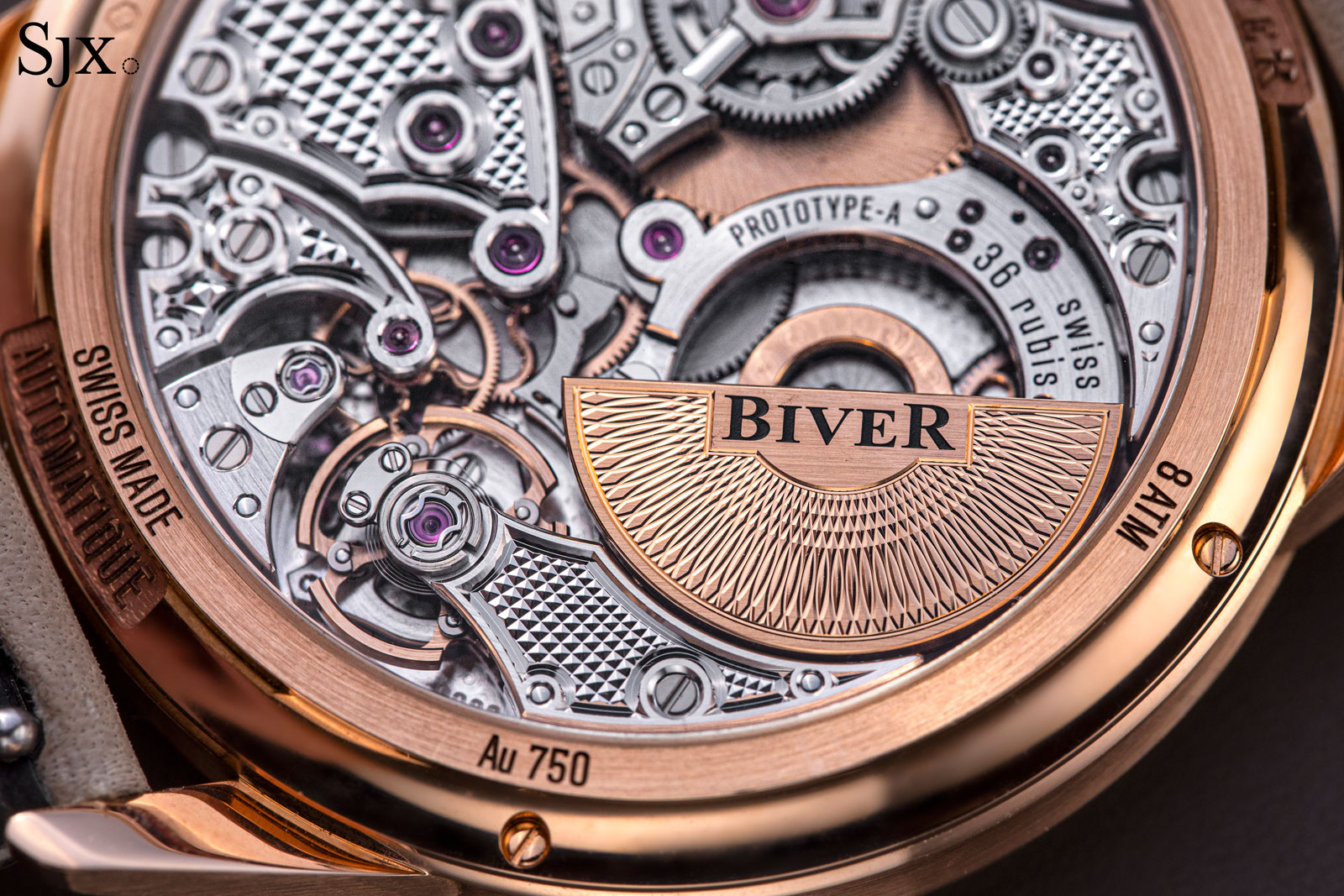
The JCB-003 with its solid gold micro-rotor that’s engine turned just like the bridges
On the outside, the Automatique has a cleaner aesthetic. It actually employs the same design elements as the repeater, but on a smaller scale and simpler format, where the styling simply works better. Although the design is clearly vintage inspired, both in the case and dial, it still manages to feel original and distinctive.
There are actually two distinct designs for the dial of the Automatique dial, which debuts with two sub-lines, a basic model with a solid gold dial and the Atelier Series that has dials in a variety of mineral stone.
Even though it’s simple to a degree, I prefer the base model as I find the dial design more interesting. The base model has a relief minute track and hour marks of alternating length. On the Atelier Series, the applied elements of the dial are plainer, as the mineral stone itself is the centrepiece.
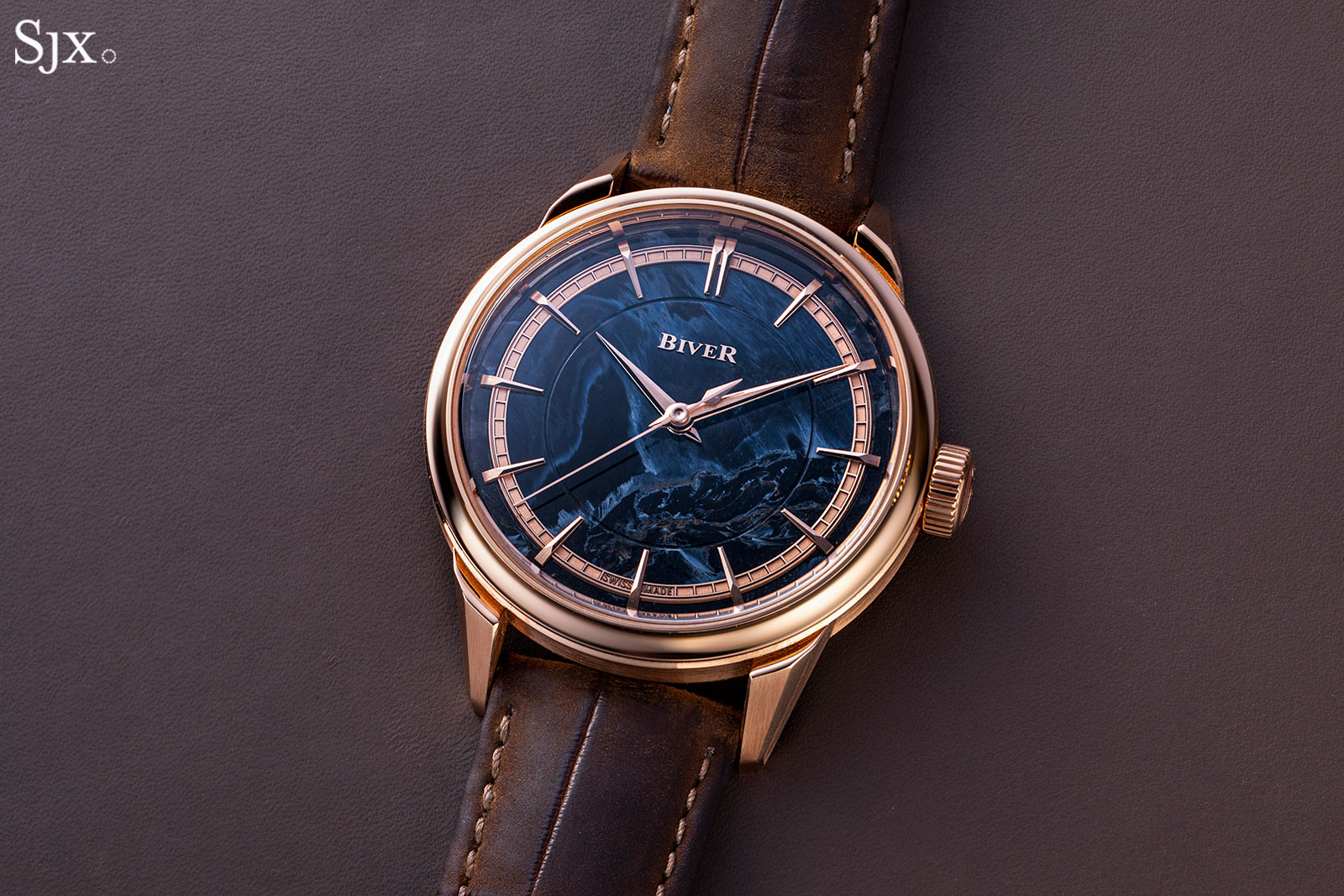
The Atelier Series with a pietersite dial
The Automatique starts at CHF75,000 in rose gold on a strap, with mineral stone dials and bracelets naturally costing more. Considering the high quality, the price is fair, even compared to the independent watchmaking competition.
In fact, I consider the Automatique the most compelling offering in the ultra-high-end automatic category because it has the most appealing design and arguably the best executed movement in the segment.
That said, CHF75,000 is a lot of money, but that reflects the state of the wider industry, rather than Biver. High-end mechanical watchmaking is expensive, oftentimes too expensive now, but that is another discussion entirely.
On a personal note, I am actually glad I like the Automatique, simply because I respect Jean-Claude Biver. The fact that he isn’t a watchmaker is perhaps one of the weaknesses of the watch, at least for the wider public. Given today’s mania for “indies”, I can imagine people falling over themselves to buy an Automatique if it was the creation of a stereotypical “independent”. But despite not being the result of a lone watchmaker, it still feels like an authentic creation of a father and son steeped in watchmaking.
Finely detailed
The Automatique is essentially a scaled-down Carillon Tourbillon, and the reduced size boosts its appeal. Measuring 39 mm in diameter and 10 mm high, the Automatique has good proportions that make it easy to wear. In fact, the case feels thinner than it is thanks to the design.
Interestingly, despite the svelte dimensions, the case is water resistant to 80 m. It’s not practically useful in any way, but 80 m is a substantially greater depth rating than the 30 m typical of dress watches.
The case design is vintage inspired, but still original, with all of its elements coming together in a distinctive design. The vintage inspiration explains the familiar silhouette, especially in the lugs.
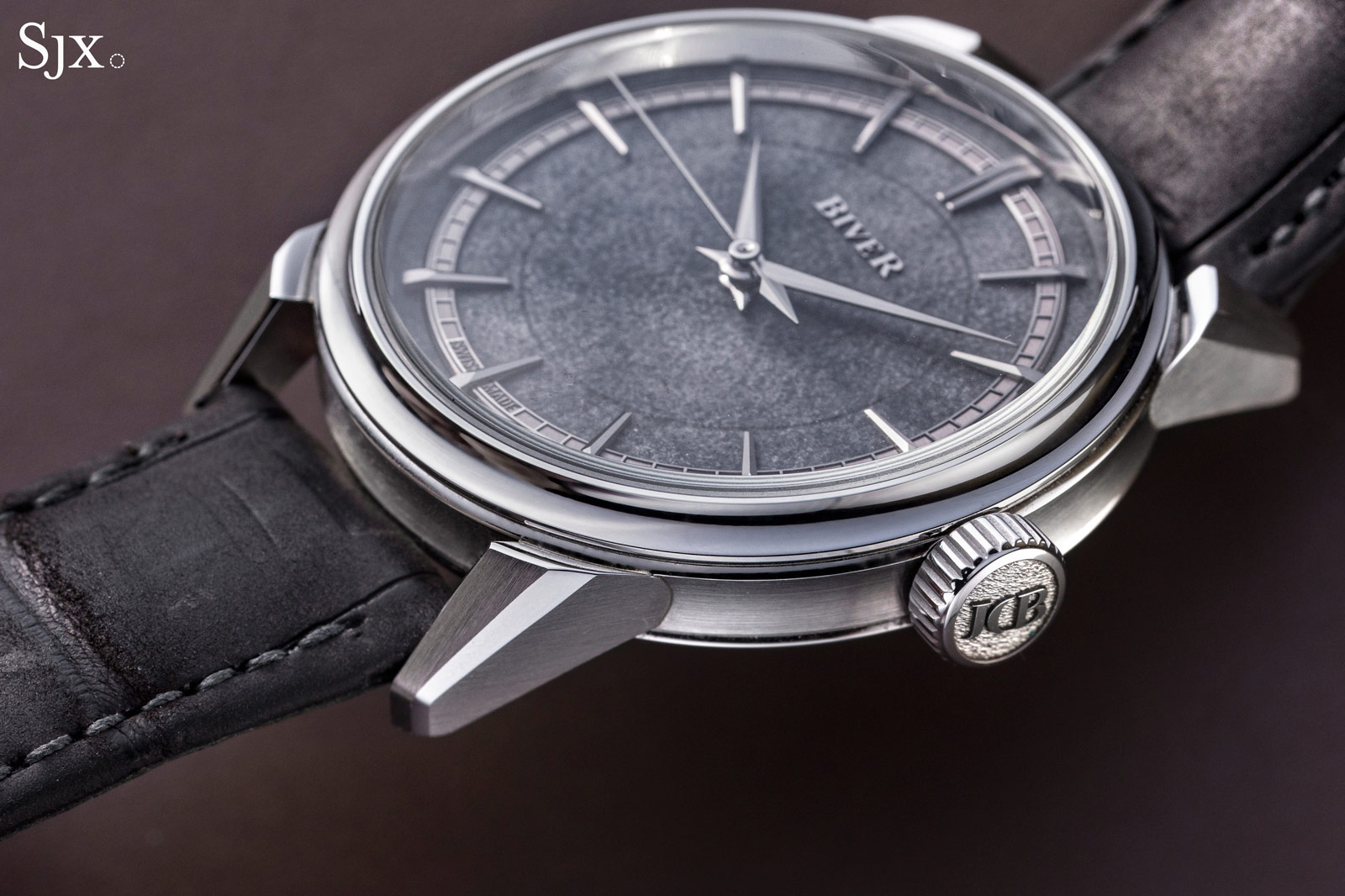
Especially in profile, the lugs evoke the ref. 1579
The lugs take inspiration from the Patek Philippe ref. 1579 “anse a ragno“, which translates literally as “spider lugs”. This vintage chronograph reference is defined by its angular lugs that had been reimagined for the Automatique. Jean-Claude himself owned one of the rarest examples of the ref. 1579, one of three known in platinum, for many years, explaining the basis of the design.
Each soldered to the case by hand, the lugs are comprised of angular facets that show off the case finishing. The lugs sport brushing and mirror polishing, with flat surfaces and sharp edges.
The thinness of the case is due to the concave case band that echos the round base of each lug. The bezel and back are also concave, all of which accentuate the thinness of the case. And the concave bezel also serves to frame the dial.
All variants of the Automatique share the same case, but there are two distinct lines of dials: Atelier Series and standard (though even standard is fancy).
Both share the same design language of a “sector” design, which makes the dials are obviously vintage inspired than the case. Still, the dial designs manage to avoid being derivative, thanks in part to the fine detailing. The dials stand out for the high quality of details, even on the standard series.
The Atelier Series employs mineral stone dials, which has become something of a signature for Biver. The Carillon Tourbillon was launched with several types of mineral stone dials, and more recently gained dials in guilloche obsidian or mother of pearl.
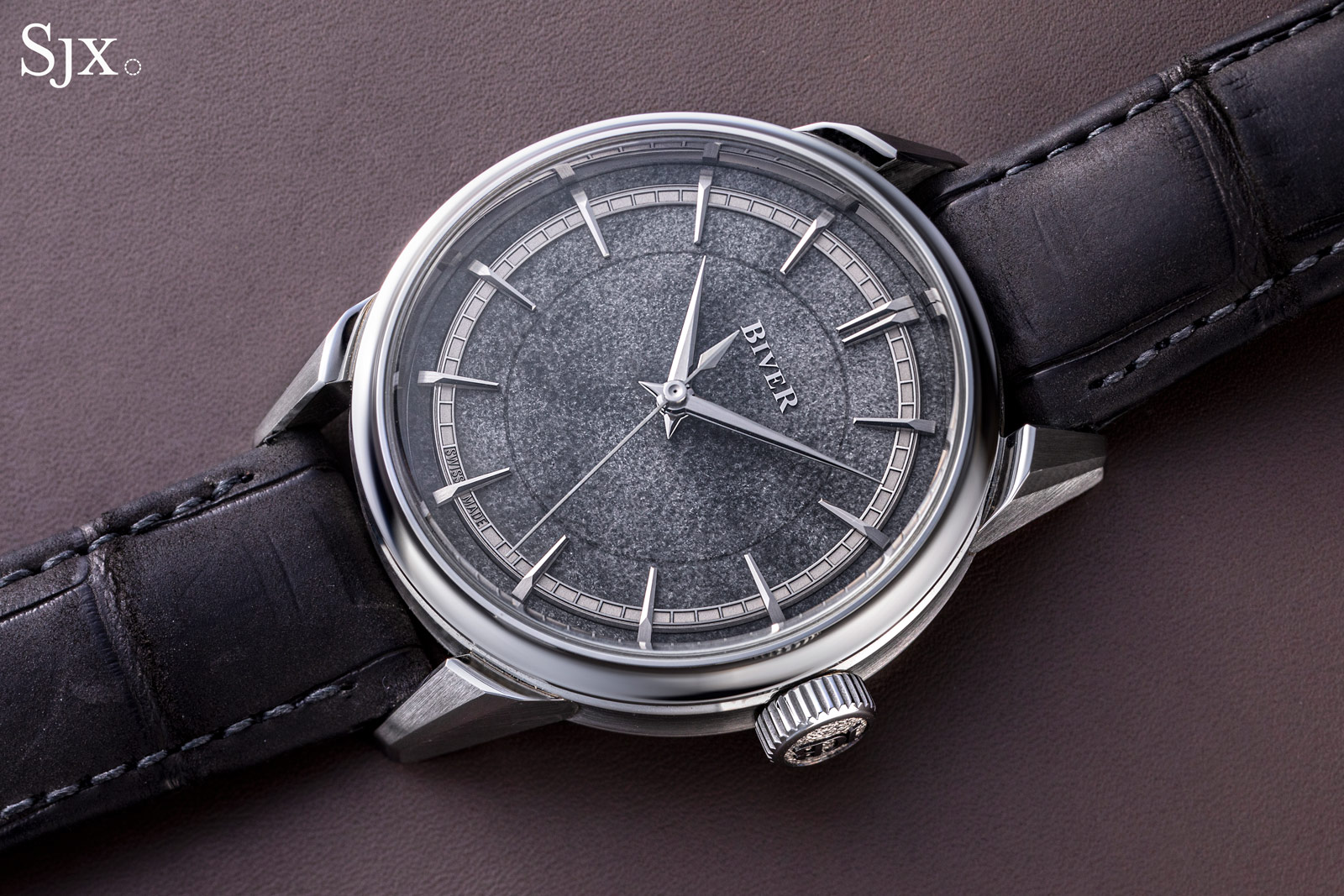
The Atelier Series in platinum with an obsidian dial
The Automatique Atelier Series continues the brand’s inclination towards mineral stone, but in time-only format. Obsidian and pietersite are the two options available at launch, although more stone varieties will be arriving in the near future.
Essentially a mineral stone base with applied solid gold elements, the dials share the design language of the standard series, but look more modern. This is largely due to the hour markers, which are all of equal length, and the applied railway minute track.
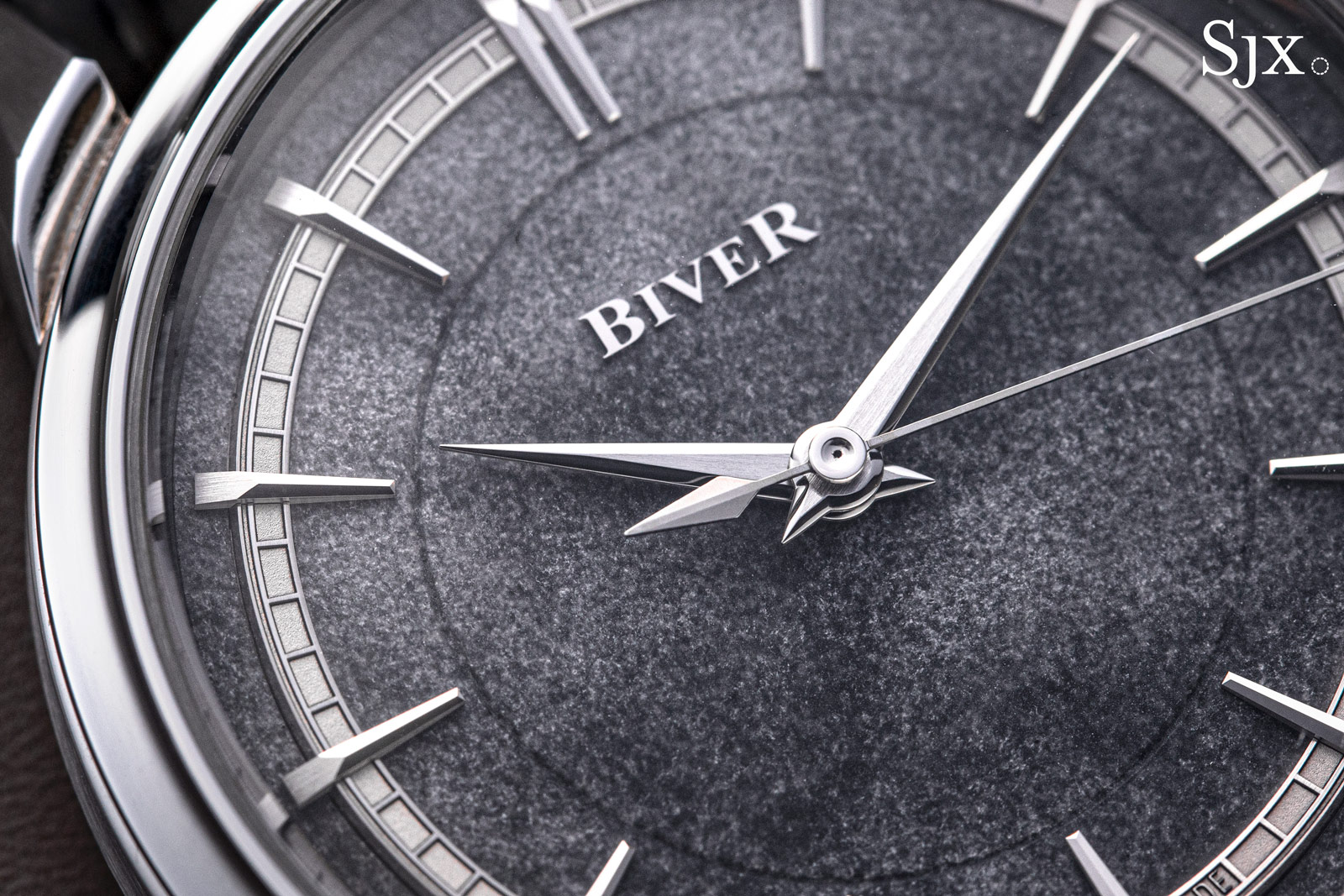
The obsidian dial
Notably, the sector-like design is achieved by carefully working the stone: each stone dial is a single piece with a carefully milled channel on the inner circumference to create the “sector”.
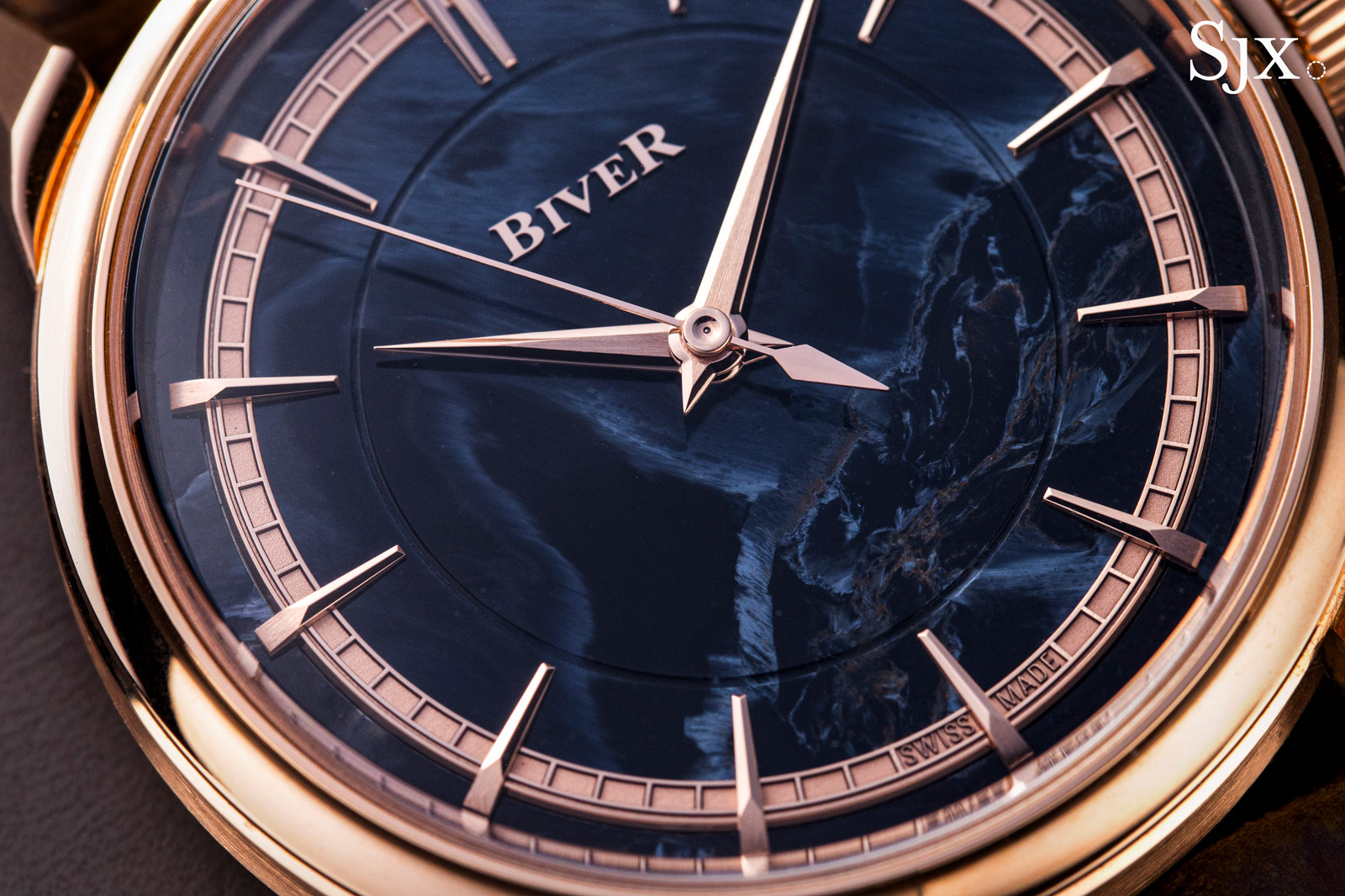
Also known as chalcedony, pietersite has a pronounced marbling
The quality of the mineral stone dials is high, but I very much prefer the solid gold dials found in the standard series. While stone dials are surely more difficult to produce, the gold dials are more appealing in terms of design and finishing. The gold surfaces allow for more nuance in the finish, while also having the extra detail of the relief railway minute track.
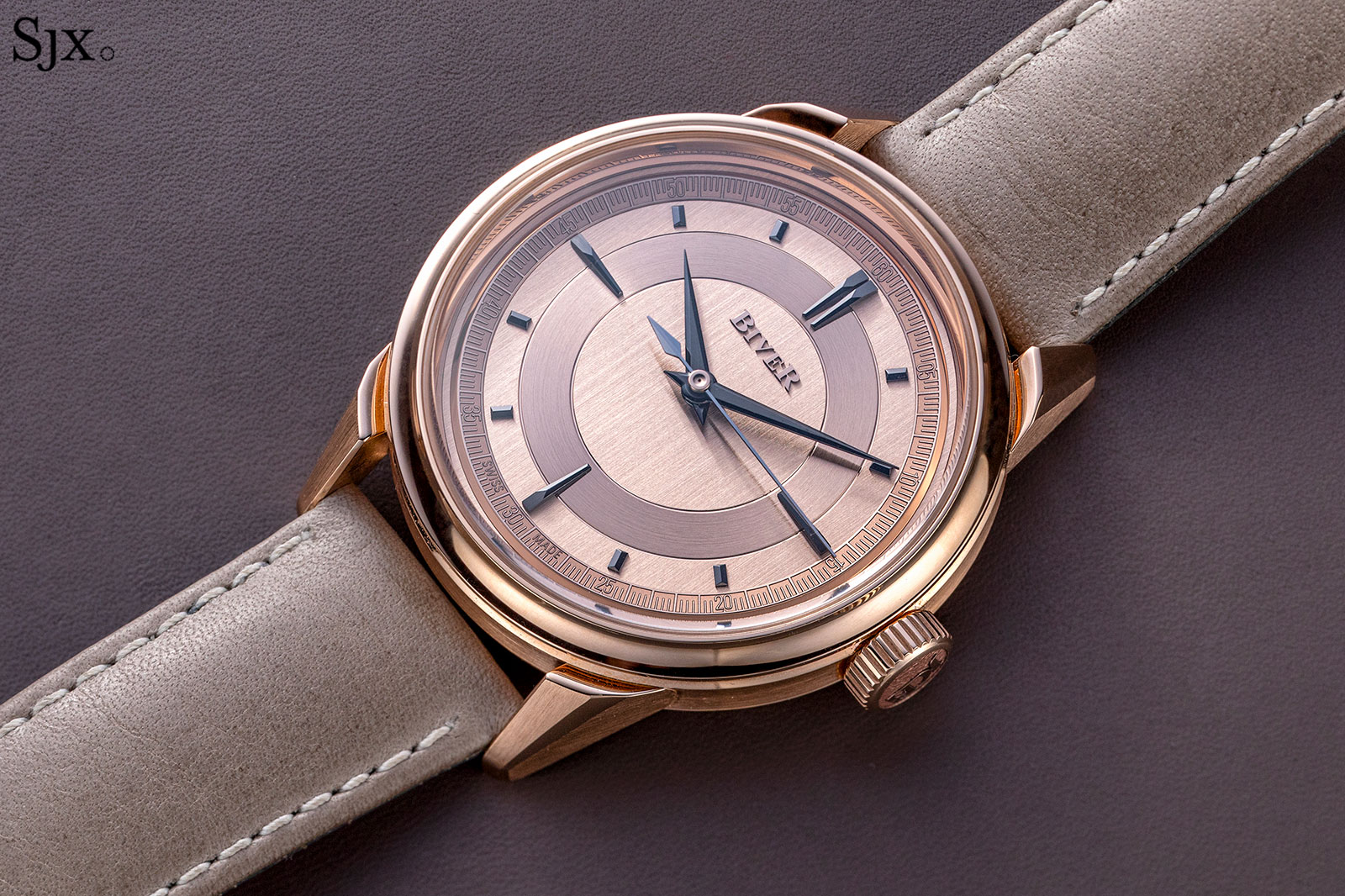
The rose gold model gets a rose gold dial
Despite being “entry level” for Biver, the standard series models have unusually refined dials. The standard model employs a one-piece solid gold dial that appears two tone thanks to alternating vertical and concentric brushing. With each dial section separated by a sharply-milled border, the two-tone effect is pronounced and adds to the dial’s character.
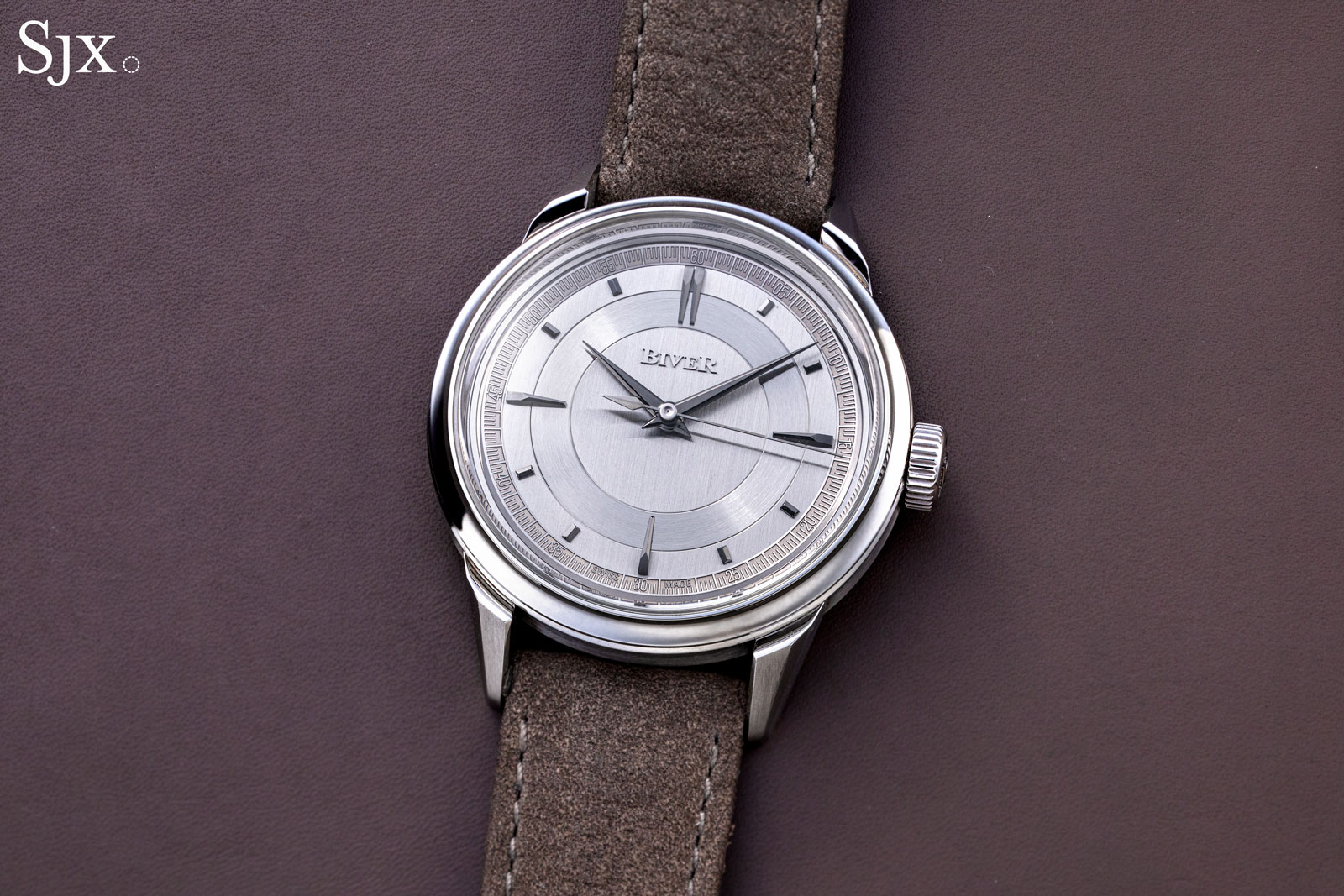
While the platinum version has a white gold dial
The dial gets more interesting up close. Also solid 18k gold, the applied hour markers are facetted and feature alternating brushed and polished faces, echoing the lugs. The hands are similarly finished and likewise solid gold.
And then there’s the railway minute track that is also solid gold with the scale in relief. The relief markings brings to mind the micro relief text employed by Greubel Forsey.
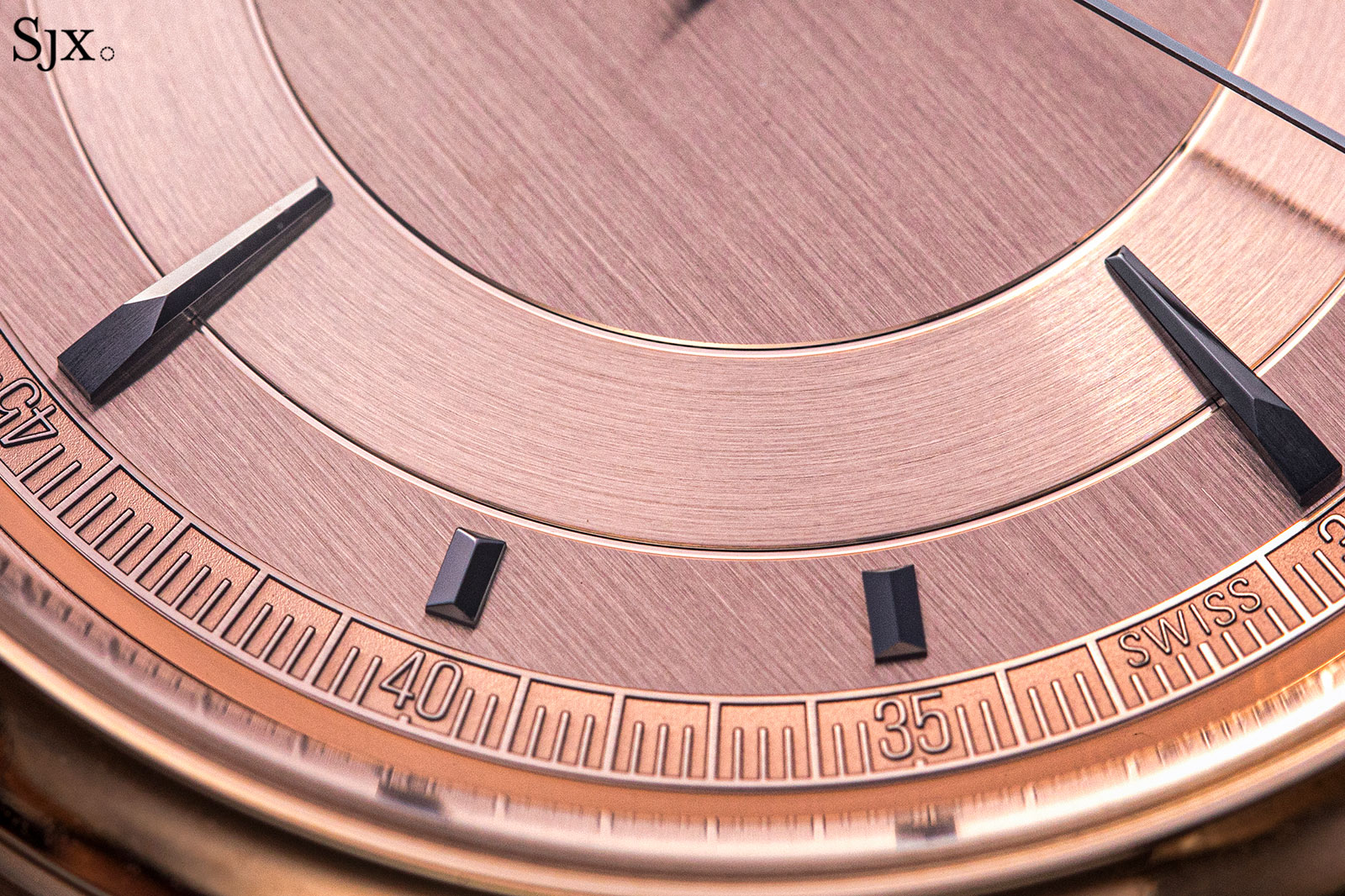
The railway minute track is a separate solid gold ring
The JCB-003
As the model name implies, the Automatique is mostly about the self-winding movement inside. The JCB-003 was developed by Dubois Dépraz, a movement and complications specialist most famous for its modules, most notably the perpetual calendar and chronograph. Its client list spans the industry, ranging from Richard Mille to TAG Heuer.
As a time-only calibre developed from the ground up, the JCB-003 is atypical of Dubois Dépraz. It surprised me, because the movement isn’t what I expected of Dubois Dépraz.
(NB: The movement pictured is a prototype that is not entirely clean or perfect, but it is still very, very good.)
The JCB-003 was conceived as a high-performance automatic with a long power reserve – 65 hours in this time-only version – that can serve as a base for complications. To that end, it was also designed to be slim, allowing complications to be added on while retaining a manageable thickness. This contributes to the thin case of the Automatique.
As expected of a slim, high-end automatic, the JCB-003 has a micro rotor that winds bidirectionally thanks to reverser gears. It’s also equipped with a free-sprung balance fitted with four regulating weights.
The balance has a relatively small diameter, but that is the norm for self-winding movements of this type due to constraints of space and power reserve. However, it has an interesting proprietary design that maximises the balance diameter, which theoretically optimises inertia and thus chronometry.
The movement, however, covers more than just the basics of a high-end calibre. It was clearly designed to incorporate maximum technical and decorative ornamentation – in the best way possible though some of it feels excessive.
One of the standouts is the grande sonnerie-style winding click that is integrated into the barrel ratchet wheel. This is the only automatic movement with this feature that I can recall. Mechanically it doesn’t do that much more than a simple click, but it adds to the visual complexity of the movement.
And the winding click isn’t implemented in the traditional manner, but instead sits under an exceptionally intricate steel bridge that manages to combines almost all the known techniques for finishing steel parts.
Another striking detail are the wave-form spokes of the going train wheels. The spokes are also chamfered, right up to the inward angles, and the faces of the wheels circular grained. These sit under finger bridges that are reminiscent of pocket watch movements.
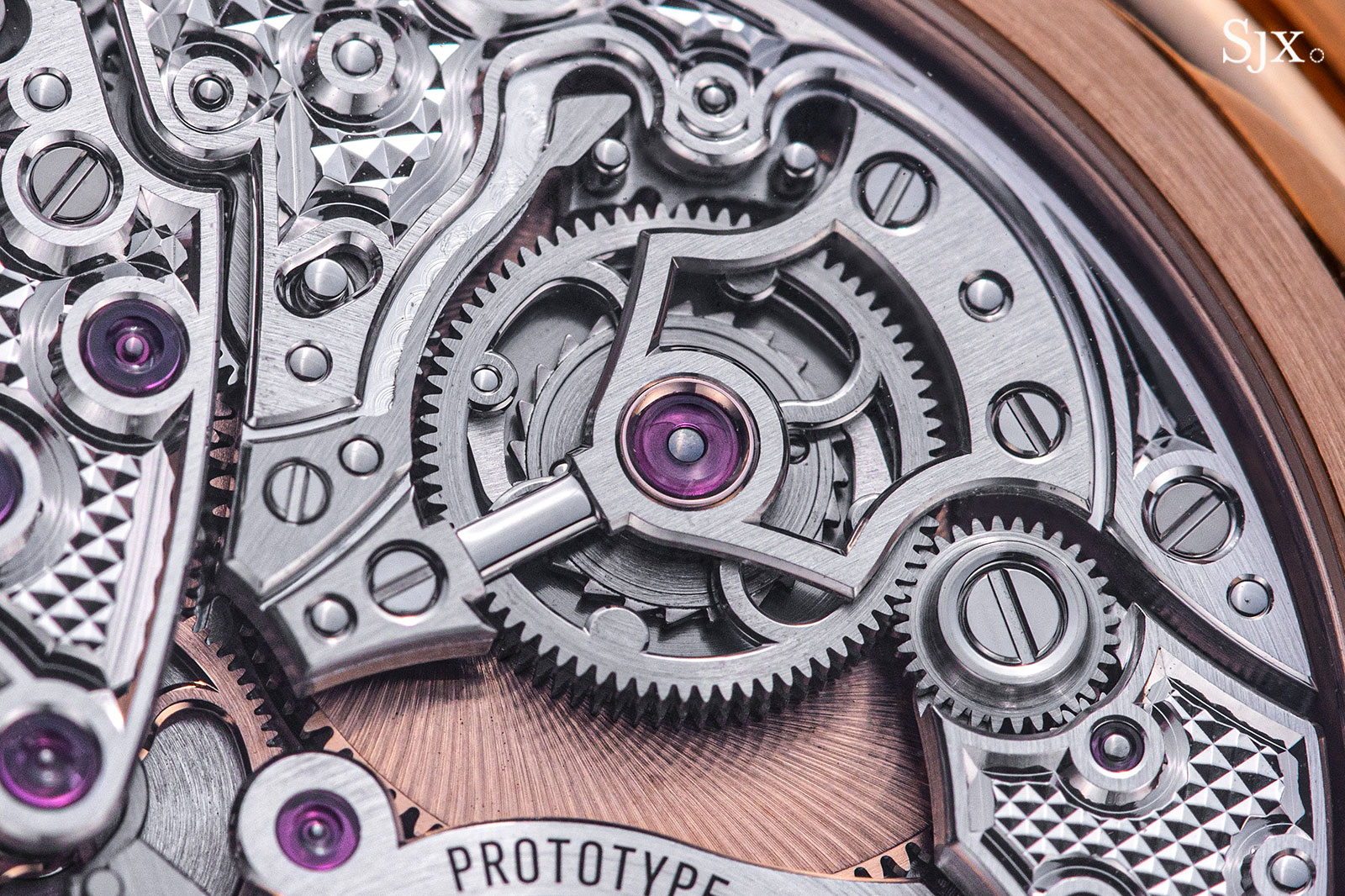
The grande sonnerie-style winding click is visible under the spade-shaped bridge
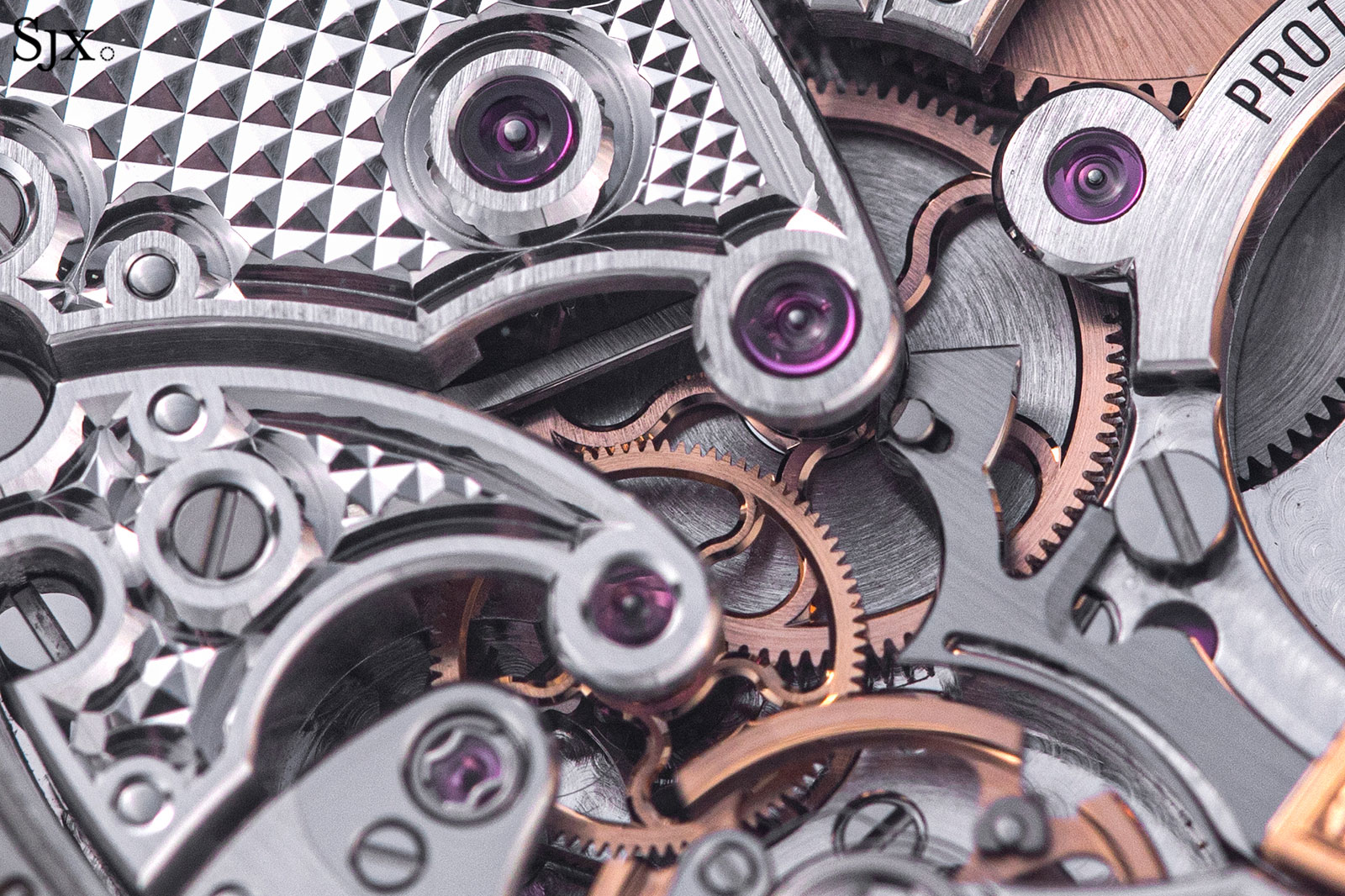
The spiral arms of the gears that make up the going train sit under finger bridges
The only aspect of the JCB-003 that I would do differently is the clous de Paris guilloche on the bridges and cock. The engine turning is outstanding, and according to Biver, done entirely by a hand-operated straight-line engine, making it all the more impressive.
But the guilloche is one decoration too many for me. The movement looks too busy, which distracts from many of the finer details, of which there are many. Conventional striping, or even more basic frosting, would create more contrast with the rest of the movement.
Despite the busy appearance, the JCB-003 still feels cohesive. Unlike other ornately executed movements that feel like a confused assembly of high-end elements, the JCB-003 is greater than the sum of its parts (and would arguably be even greater minus the guilloche).
Leaving aside the fanciest elements of the movement, the JCB-003 also does the basics well. Steel parts are either straight grained or black polished, while bridges are all bevelled along their edges. All jewels, pins, and screws sit in polished countersinks. Screw heads are polished and chamfered, while visible pins are polished.
Concluding thoughts
The Biver Automatique is a simple watch realised in the most elaborate manner possible. Many of the constituent elements are disparate, but everything comes together in a logical, appealing watch that is impressive in the hand. It does have a big price tag, but lives up to the expectations set by the cost. In fact, it exceeds expectations in some ways, which is an uncommon achievement.
Key facts and price
Biver Automatique
Diameter: 39 mm
Height: 10 mm
Material: Platinum or 18K rose gold
Crystal: Sapphire
Water resistance: 80 m
Movement: JCB-003
Functions: Hours, minutes, and seconds
Winding: Automatic
Frequency: 25,200 beats per hour (3.5 Hz)
Power reserve: 65 hours
Strap: Leather with platinum or rose gold buckle, or five-row Biver bracelet in either platinum or rose gold
Limited edition: No, but limited quantities for the Atelier Series
Availability: Direct from Biver or at authorised retailers
Price: Starting from CHF75,000 for gold case on strap, up to CHF121,000 for platinum with obsidian dial on bracelet (prices exclude taxes)
For more, visit jcbiver.com.
Back to top.