Watchmaking: How the Art of Precision Regulation Became a Science
Adjusting to new materials.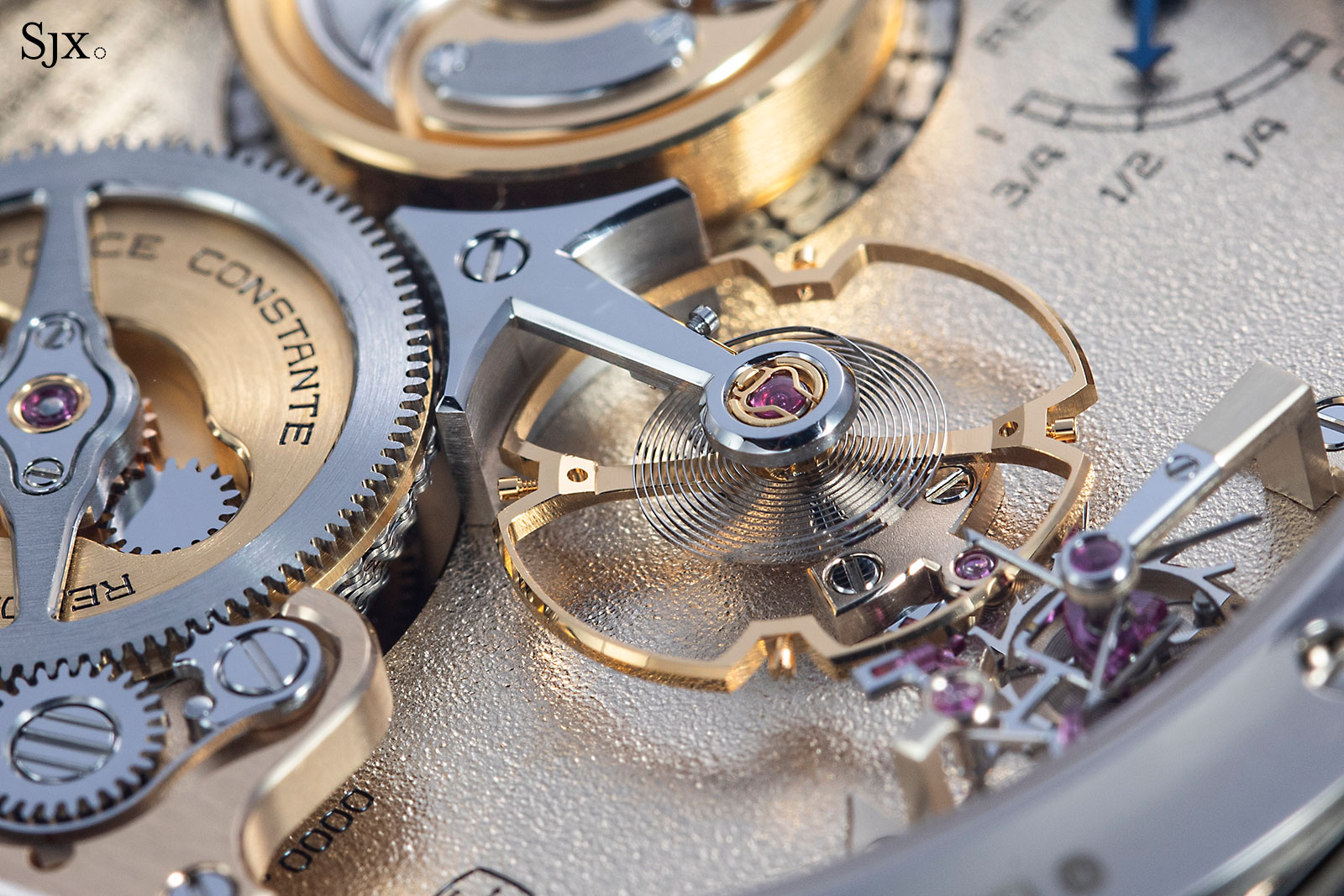
They were once the horological elite, credited with magical powers. The precision timers who tuned the watches for the observatory trials in the 1960s and 1970s are now a dwindling band in the twilight of their lives. In those days, when mechanical precision rather than mechanical complication determined the value of a watch, precision timing was a post-graduate discipline that took a lifetime to master.
Before he died last October in his 90th year, one old timer, François Mercier of Le Locle, described what he had to do to win prizes for his employers, initially Ulysse Nardin and then the hairspring spring manufacturer Spiraux Réunis.
First, he had to identify the most faultless spring, calculate and shape the terminal curve, pin it up to the staff of a previously poised balance wheel. Then he would shift balance screws by hundredths of a millimetre, adjust forces and inertia in micrograms, to move a fraction of a second closer to the unattainable goal of a true and constant time.
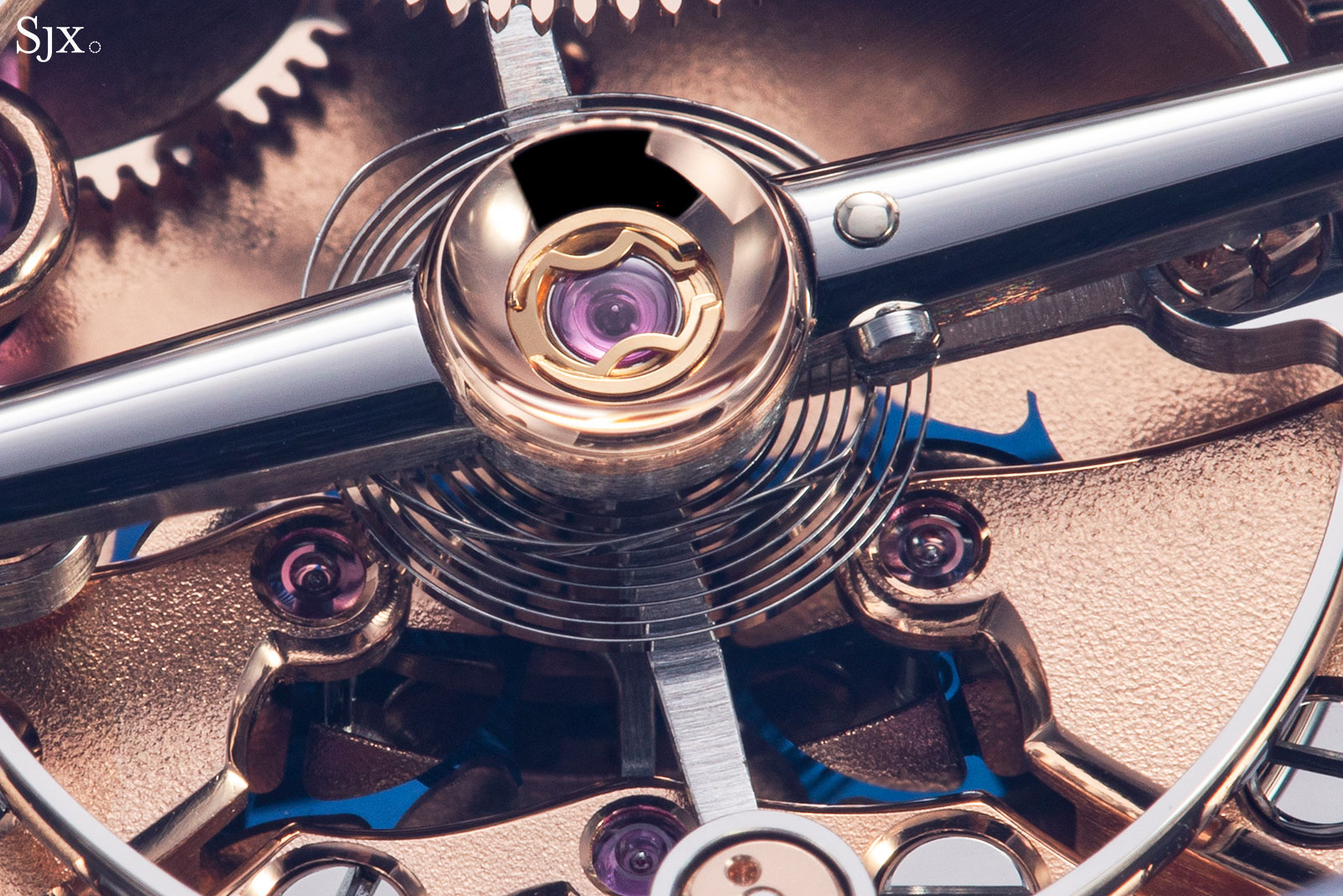
An overcoil hairspring in a contemporary Voutilainen Vingt-8
Temperature compensation
The biggest challenge was to compensate for the effects of temperature changes on the steel alloy springs of old. As the temperature rose, the spring would lose its elasticity and beat more slowly. Such springs needed a compensation balance made of two metals each having a different coefficient of expansion.
Rising temperatures would cause the cut ends of the balance rim to curl inwards, thereby increasing the rate of the balance to counteract the slowing spring. The timer had to adjust two small weights near the ends of the balance rim to ensure the rate of the balance wheel compensated exactly for effect of temperature changes on the spring.
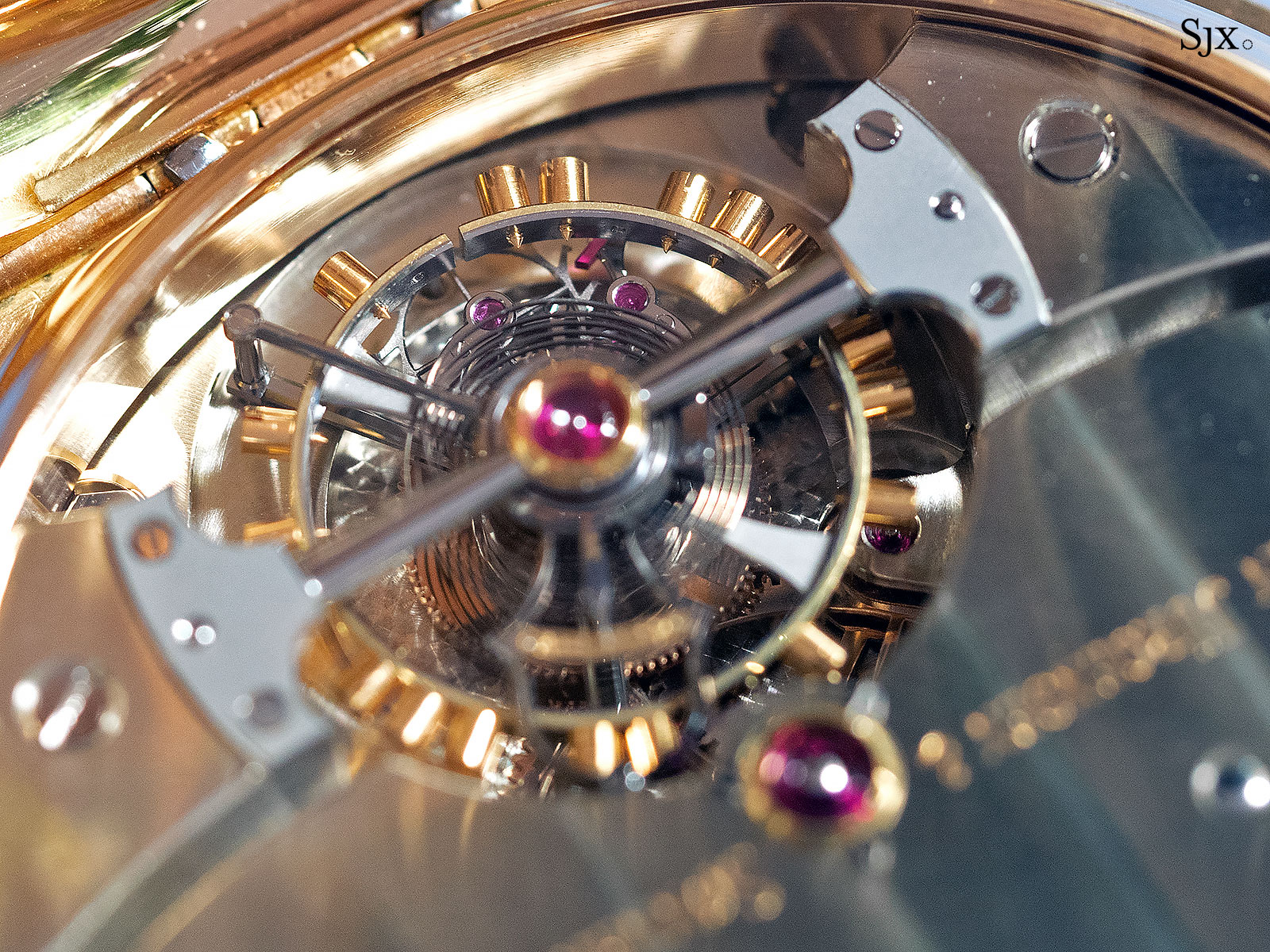
The split, bi-metallic balance in a 1980s Urban Jurgensen tourbillon pocket watch
However, the timer could only adjust the balance for the extreme temperatures, usually 8°C and 30°C. Yet balance wheels never behaved as predicted at the temperatures between. Known as the middle temperature error, this anomaly was the bane of the precision timer’s life.
François Mercier’s efforts were worth it. If his patrons won a prize, and especially if Spiraux Réunis beat its rival, Nivarox, he would get a bonus of a month’s salary. More importantly, he would win the admiration of his peers.
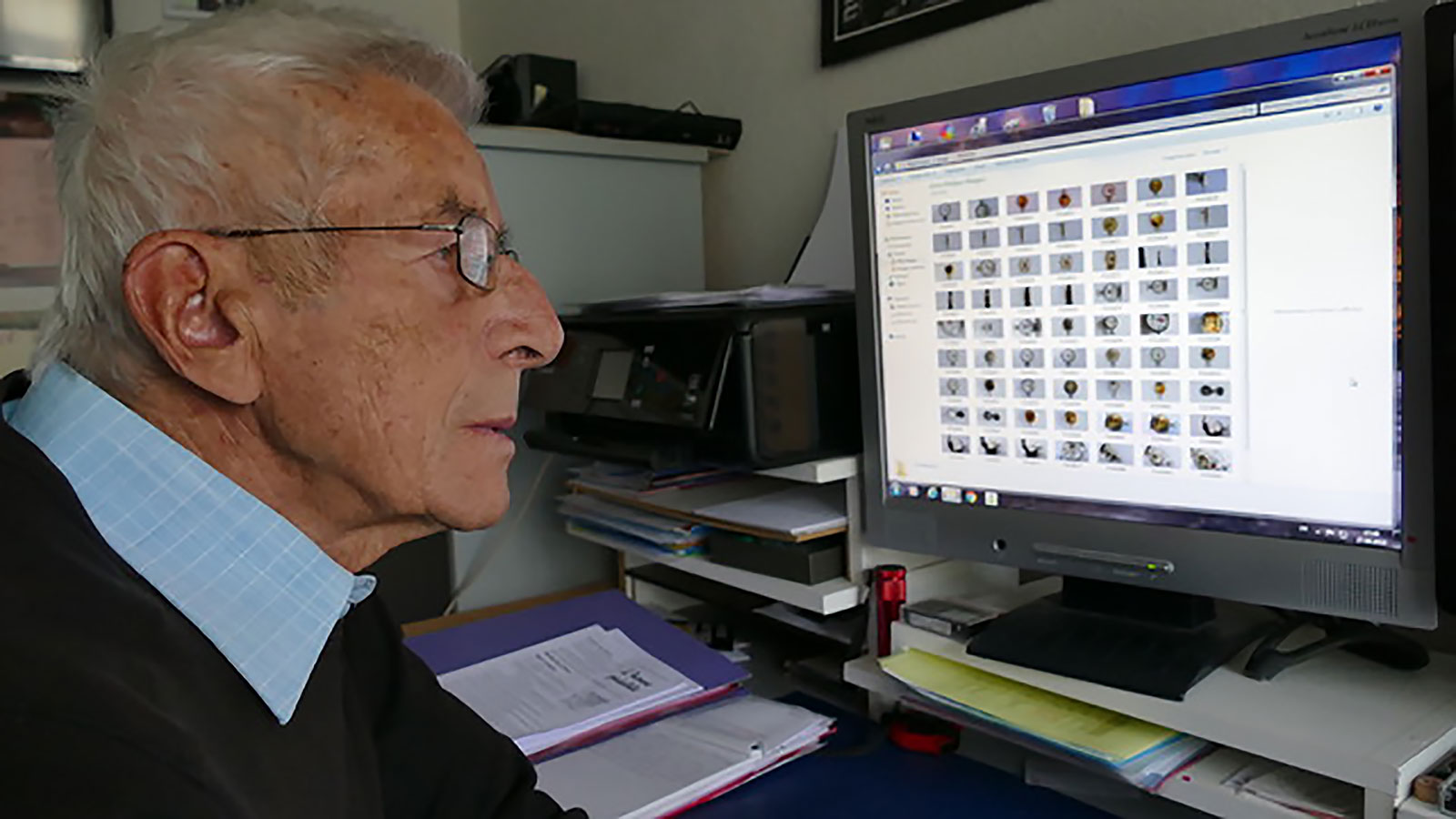
Francois Mercier in 2018. Photo – Francois Mercier
Just as quartz was bringing competitive timing trials to an end in the mid-1970s, Pascal Mottier was at horological school learning to adjust the kind of watches Mercier was working on — with 18,000 beat-per-hour compensation balances and steel springs. Today he’s a teacher at the Ecole d’Horlogerie de Genève (Watchmaking School of Geneva) and thus well placed to reflect on the changes to the precision-timer’s art.
He points out that precision timing is no longer a post-graduate specialisation but a six-month module in the four-year course to become a complete watchmaker. Science has made the modern adjuster’s job much easier than that of an earlier generation of precision timers.
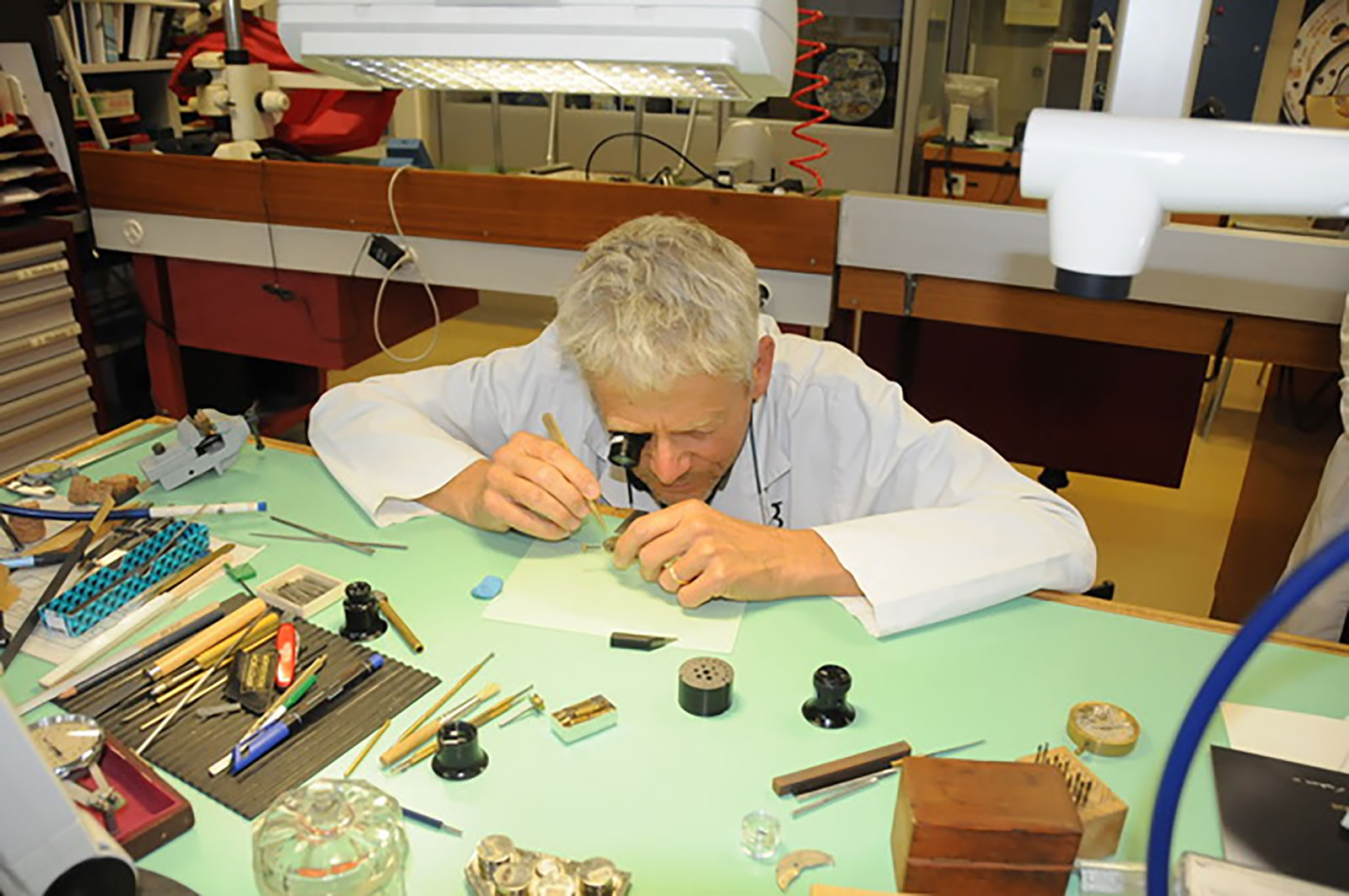
Mr Mottier at his bench. Photo – Pascal Mottier
“The main change is in the development of new materials, especially when it comes to temperature compensation” explains Mr Mottier. “Springs come in four grades and watchmakers can now choose between different alloys. The issue is no longer temperature compensation, but to find the best match for their balance-wheels.”
Mr Mottier reveals that Rolex gets around this problem by having all its springs made from a single casting of alloy. “If the springs all perform the same, Rolex can make all its balance-wheels the same according the consistent properties of the spring.” He remarks that the minimum size of an ingot is four kilos — enough for three to four million springs.”
The new springs mean there no longer any need for a complex split, bimetallic balance with screws. Today’s balance wheels are simple, monometallic, annular and made of Glucydur, a hard, non-corrosive alloy that is also stable at different temperatures.
Many brands are today vying to produce their own springs out of such materials as ceramics, titanium or carbon, instead of relying on the Swatch Group’s Nivarox springs. Brands which take precision and accuracy seriously, such as Tissot and Patek Philippe, use silicon springs, impervious to temperature changes and magnetic fields, and all identical.
Poising the balance
With the problem of temperature compensation solved, the role of the today’s watch adjuster is concentrated on poising the balance and pinning up the spring. “The correct poising and springing are fundamental because this is where almost all of the errors can be eliminated,” says Mr Mottier.
Poising the balance wheel means ensuring that its physical centre is as close as possible its centre of gravity, in other words that the wheel is balanced. A heavy point on the oscillating balance causes a pendular effect that will alter its amplitude and rate in different positions. A properly poised balance that is trued in the flat will mitigate the positional errors due to gravity.
To poise the balance, the wheel on its staff is rolled between two flat parallel knife-edges and will come to rest with its heaviest part downwards. The adjuster shaves off a few micrograms of material there or drills a tiny hole in the balance rim to ensure the mass is distributed evenly all around.
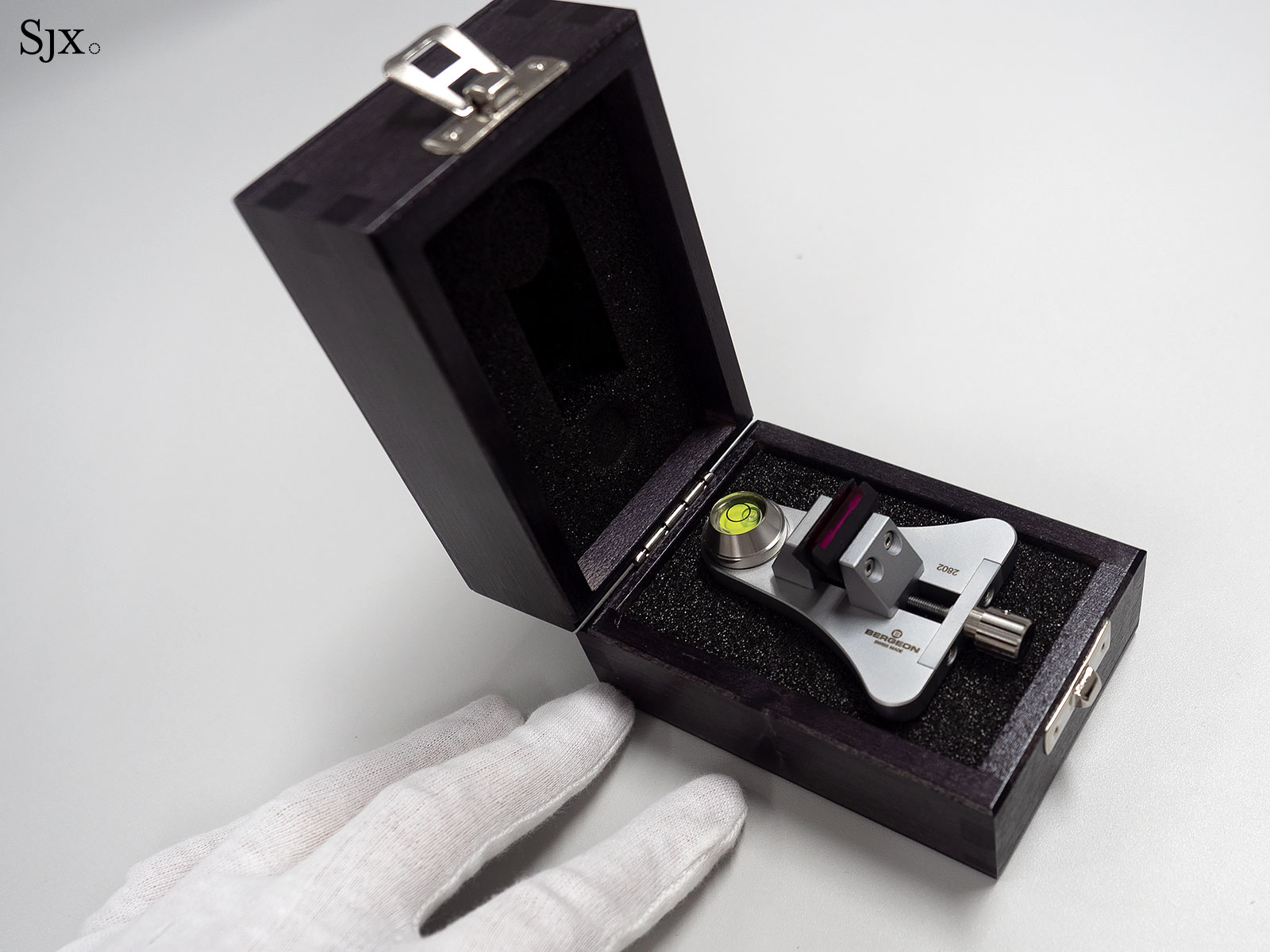
The tool for poising a balance with a built-in spirit level to first ensure the tool is flat before poising
“Nowadays this static poising of the balance is mostly sufficient,” says Mr Mottier. “Some adjusters might go further and poise the balance dynamically on its spring, but this is seldom necessary.” Dynamic poising is often practiced to counter any effect that pinning up the spring could have on the equilibrium of the balance.
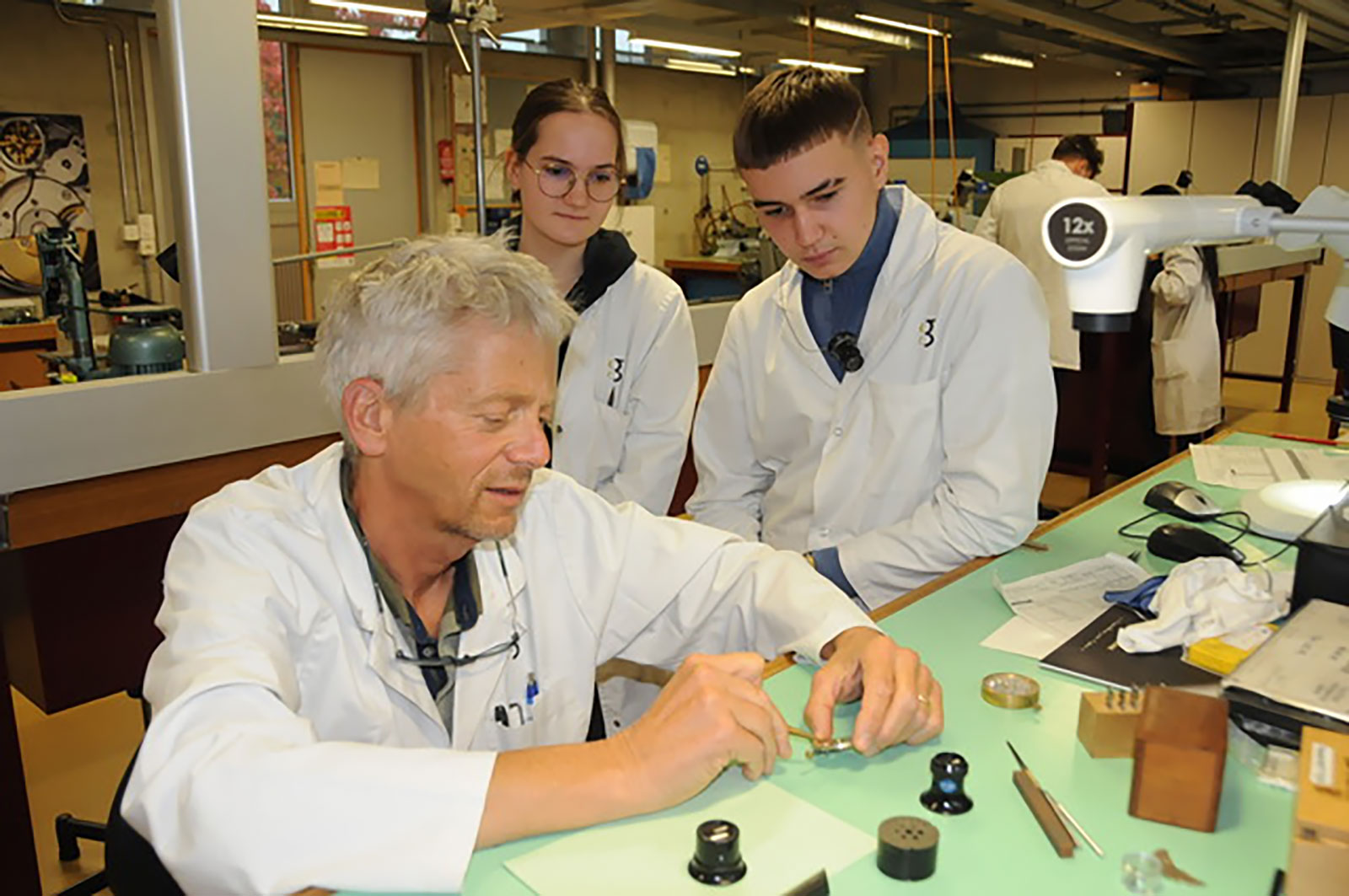
Mr Mottier with his students. Photo – Pascal Mottier
Index adjustment or free sprung?
The next step is counting the spring and pinning it up to the correct length on the balance-staff collet and the balance-cock stud — a mobile stud in the best watches. The adjuster will also need to know how to fashion a terminal curve on the spring to make it expand and contract concentrically.
Among the more delicate operations is the correct positioning of the curb pins that grip the spring close to the stud. Shifting them along the spring by the adjustment index changes the effective length of the spring, making it and the balance beat faster or slower. Special care must be taken to ensure the spring doesn’t flap about between the curb pins.
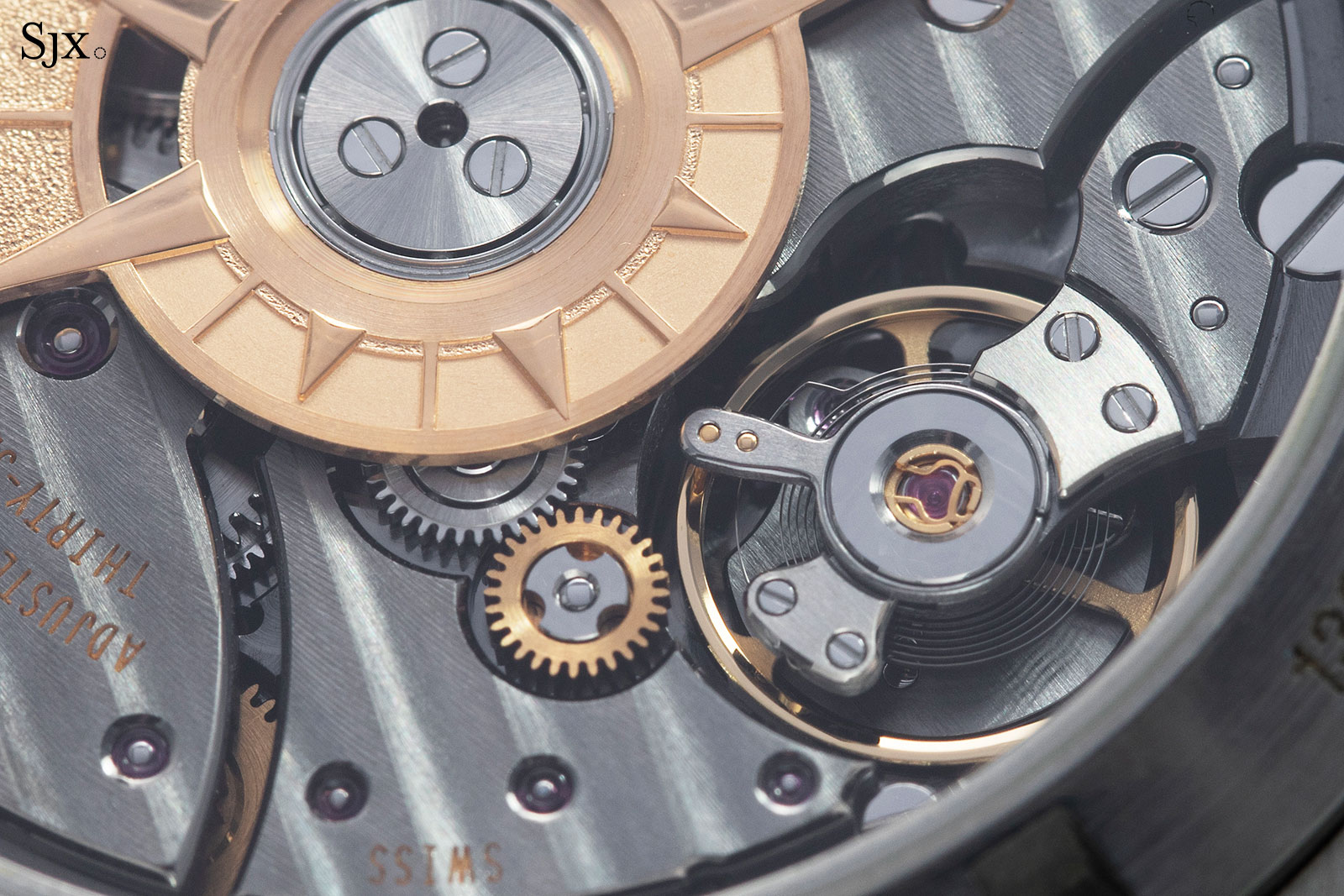
The Vacheron Constantin cal. 5110 DT with the twin brass curb pins visible in the steel regulator index
The free-sprung or inertia balance without an adjustment index was common in the best English watches of the late 19th century, but never really caught on in Switzerland until the 21st century. Patek Philippe had opened the way with its Gyromax balance in the late 1950s, but the rest of the industry was slow to follow.
Instead of effectively lengthening or shortening the spring with curb pins, the rate is adjusted by altering the inertia of the balance. Opposing pairs of weights along the rim are shifted inwards to make the balance go faster, and outwards to slow it down. Spinning skaters use the same technique by withdrawing or extending their arms.
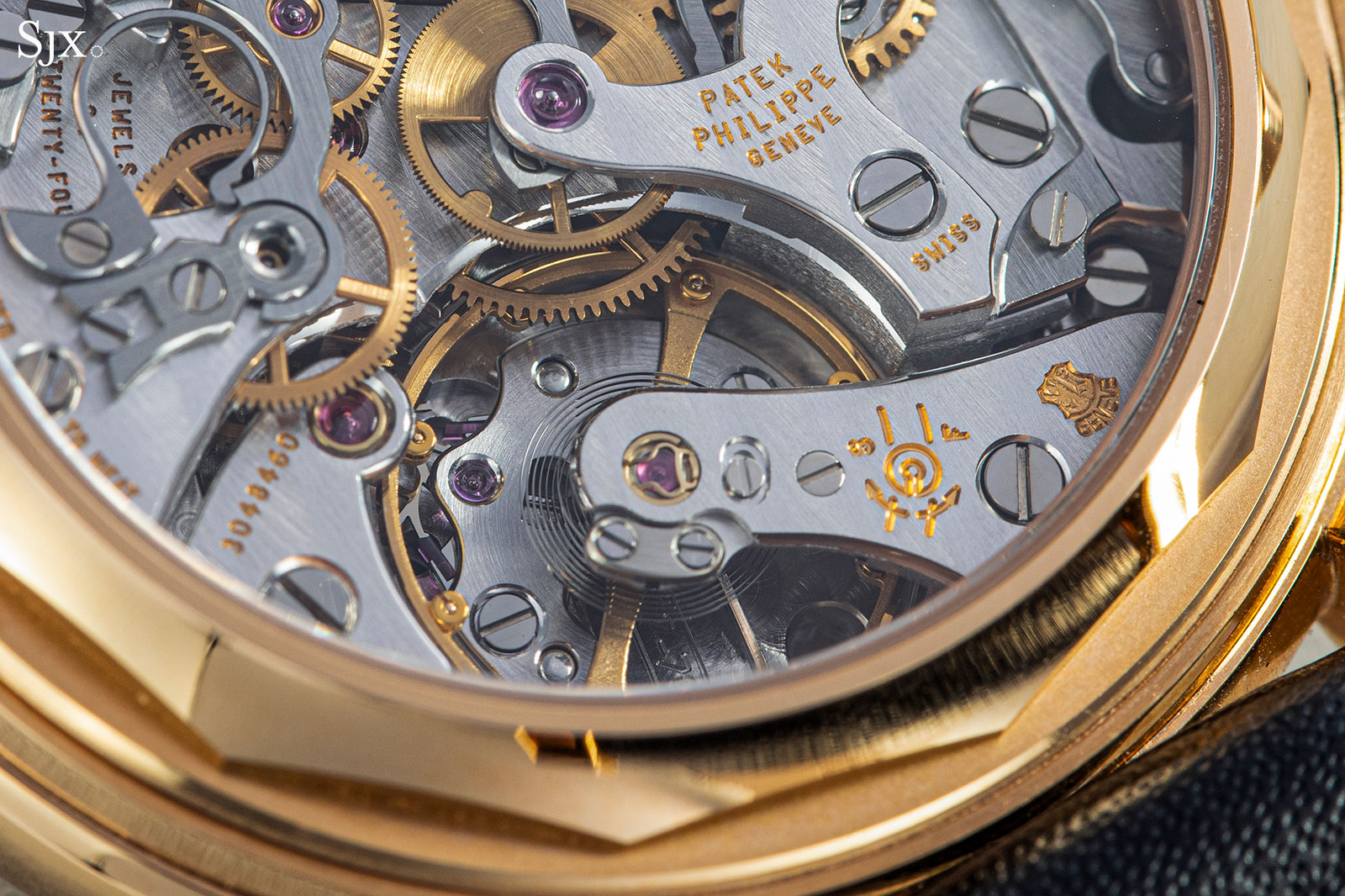
A Patek Philippe Ref. 3970 equipped with a Gyromax balance wheel with circular weights on its rim
In the right hands, the free-sprung balance can be made to regulate closely and hold its rate better than an adjustment index, which is susceptible to shocks. In the wrong hands, it has its drawbacks.
“Not all watch repairers are familiar with inertia balances when they service and adjust watches, and there’s a risk that they will mess up your watch,” says Mr Mottier. “Unless the opposing weights are moved by exactly the same amounts, the balance will go out of equilibrium.”
“A good watch adjuster develops a certain knack and certain techniques that come with long experience,” says Mr Mottier. He recounts that some precision timers would try to improve the crystalline structure of their springs by heating them to 100° for an hour or two.
It won’t be long now before watches will no longer need adjustment and one of watchmaking’s oldest skills will be lost. Pre-assembled regulating organs made of perfectly stable materials, calculated to work in isochronous partnership, are already being delivered to the assembly lines to be slotted into today’s mechanical movements.