In-Depth: The Longines Observatory Chronometer Cal. 360
When form truly follows function.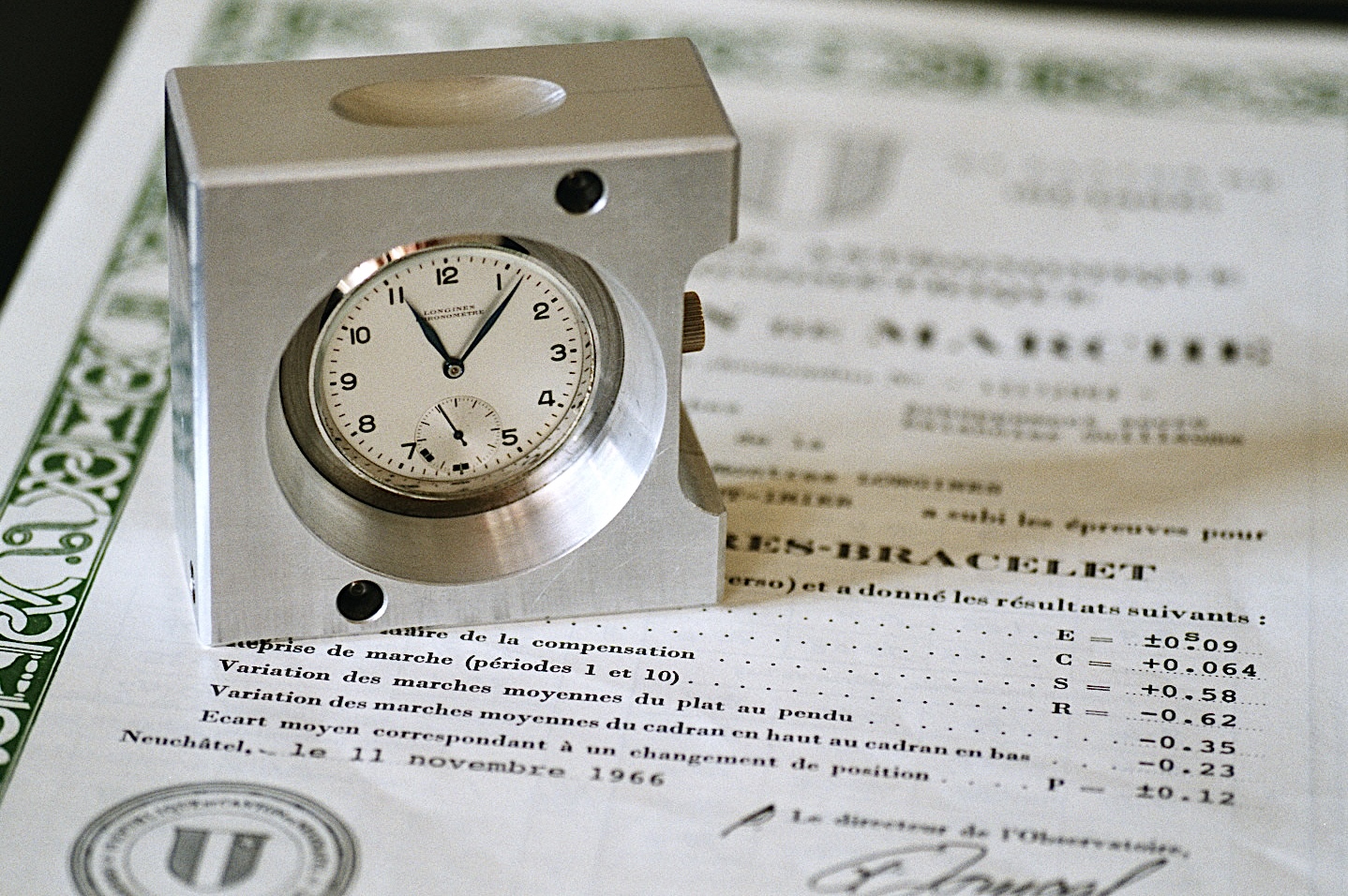
In the field of precision timekeeping, one inevitably encounters Longines with its multi-facetted and remarkably rich history.
The unwavering persistence of the firm’s celebrated régleurs and its long lineage of in-house chronometer calibres fostered Longines’ reputation for excellence in precision timekeeping, far beyond the borders of Switzerland.
The Saint Imier-based manufacturer ventured into precision chronometry as early as 1888, amidst the dawn of observatory chronometer competitions in Switzerland, when its cal. 21.59/60-based chronometer obtained an observatory-issued Bulletin de Marche, or rate certificate.
And after almost a century of steadfast participation in prestigious chronometry trials, the last Longines timepiece subject to observatory-governed testing, a cal. 262 based chronograph (movement no. 14’701’394), received its certificate in 1972.
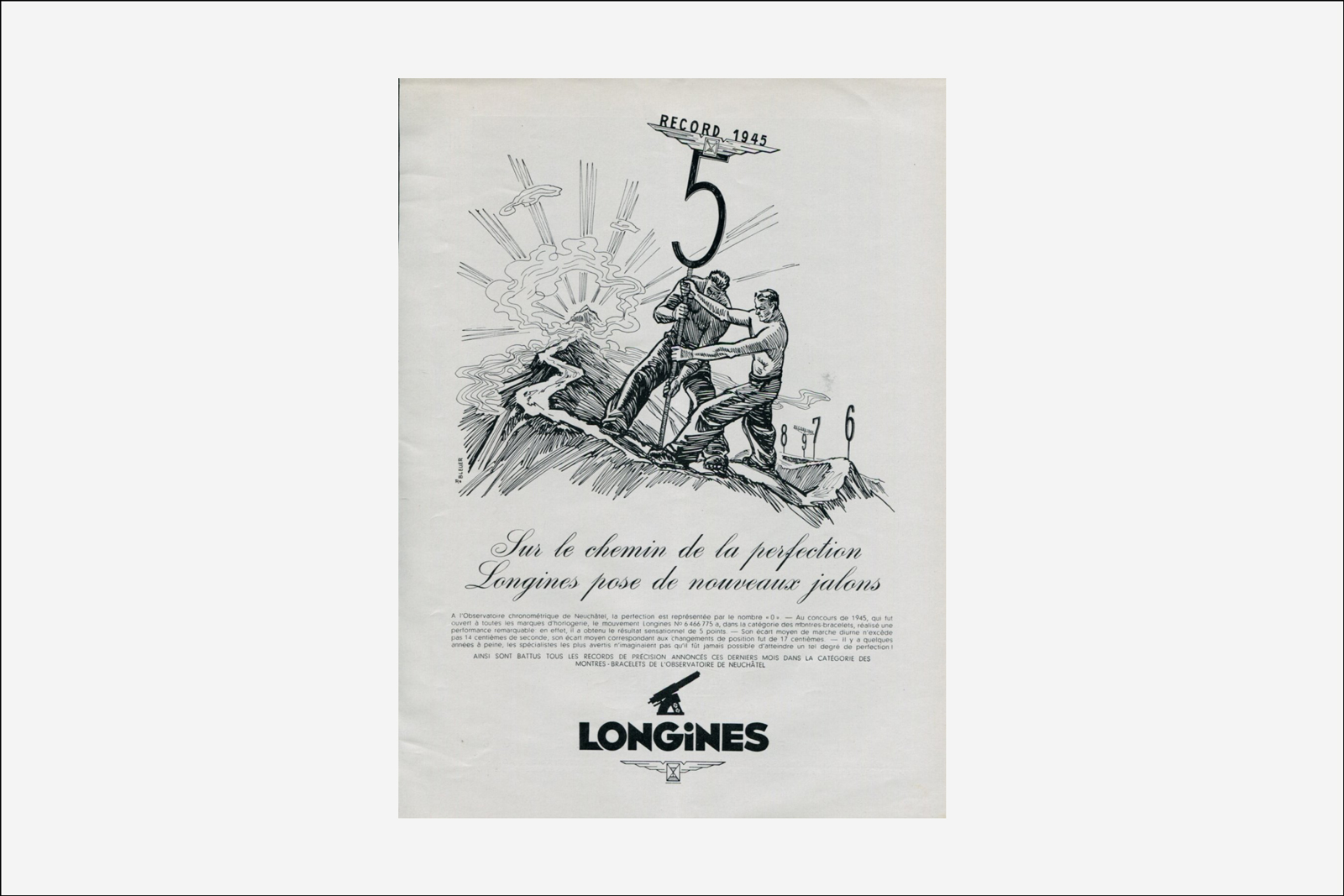
The Neuchâtel observatory announced its first chronometer contest on December 5, 1865. Eight decades later this Longines advertisement portrayed the observatory chronometer contests as an uphill battle, referencing the record of N=5.00 obtained by the wristwatch-sized cal. 15.68Z in 1945 at Neuchâtel.
Towards the end of the 1950s, a pure-bred competition calibre named the cal. 360 became Longines’ final masterpiece in the hard-fought race for glory in precision.
A proven workhorse that won countless prizes and accolades at both the Neuchâtel and Geneva observatory competitions, the cal. 360 was a purpose-built instrument, underlined by its sober, industrial, and uncompromising appearance. It is a micro-mechanical marvel in its own right and the polar opposite of a product of haute horlogerie that often focuses merely on pleasing aesthetics.

Three of the most successful régleurs de précision at Longines (from left to right): Fernand Wenger, Frank Vaucher, and Robert Chopard. Belonging to an elite club of highly specialized watchmakers, régleurs were masters in the precision adjustment of chronometers and arguably the most significant figures in the heyday of traditional chronometry. Several highly-accomplished individuals went on to become household names in certain parts of Switzerland.
A brief history of the cal. 360
As was the norm in the era before computers, the cal. 360 was designed with pencils and a slide rule, going from paper to the first batch of 40 movements in a mere seven months. It was a feat in movement prototyping that remains impressive even today, where computer-aided design and rapid prototyping are readily available.
The calibre first entered the competitive arena in 1959. In the line of duty, the cal. 360 set numerous records and ensured Longines’ reign at the top of the annual Concours chronométrique. The calibre dominated the field in the early 1960s, and its performance peaked in 1966 with an N-score* of 2.00.
With a total of 498 Bulletins de Marche, the cal. 360 claims the most number of successful submissions of any wristwatch-sized chronometer calibre between 1959 and 1967. In comparison, the total number of submissions across all calibres for other brands in the same period was as follows: Zenith, 377; Omega, 354; and Ulysse Nardin, 79.
*The N-score (short for Nombre de Classement) was calculated using a formula that incorporates various rate-related measurements. Ultimately the N-score describes the overall performance of a tested observatory chronometer and determines its ranking within the respective year of competition. N=0 represents the ideal but unattainable state of perfect timekeeping with no measurable deviation.
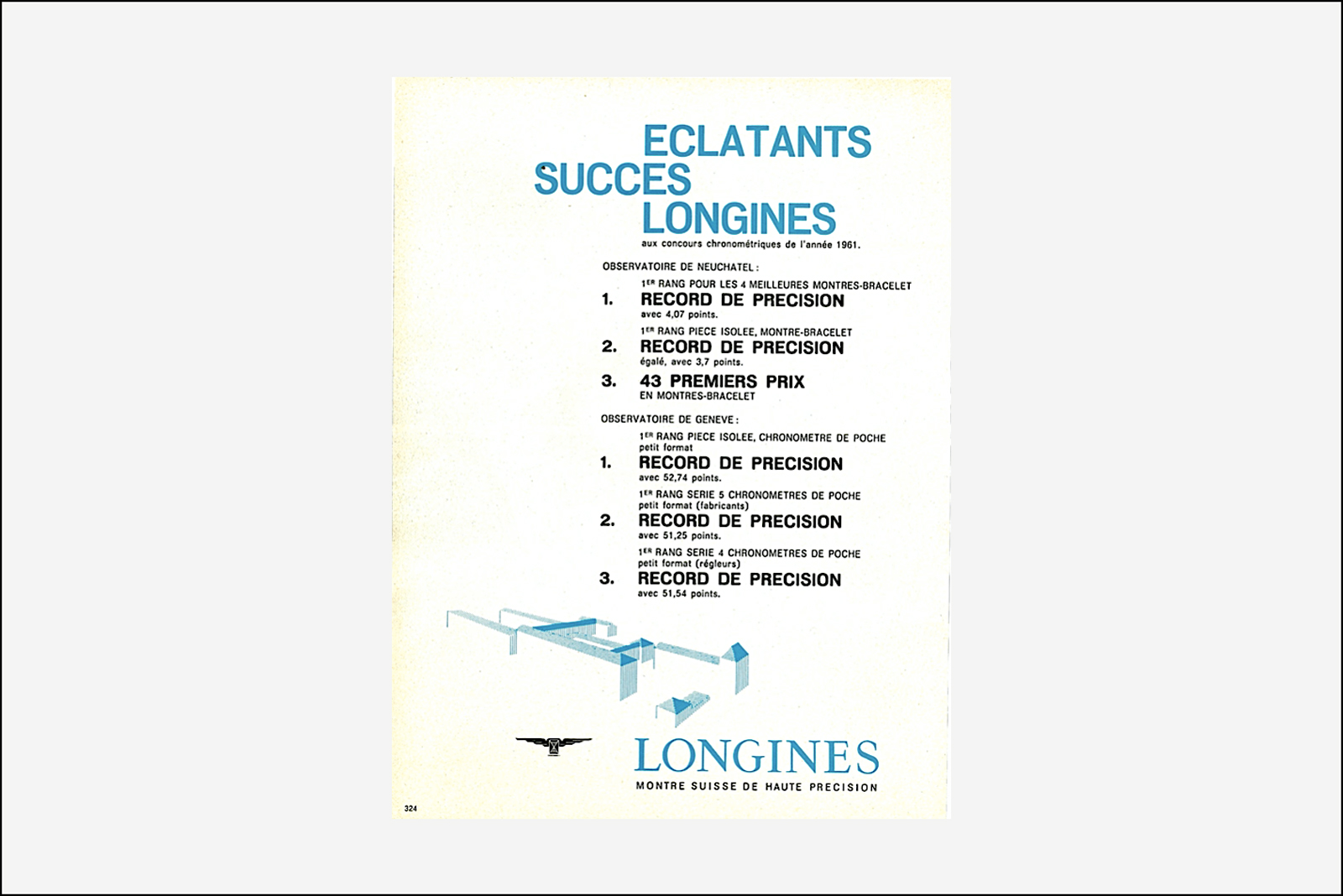
A full-page advertisement from 1961 that chronicles the impressive track record of the cal. 360 at the observatory competitions at Neuchâtel and Geneva. Notably, the cal. 360 was submitted for testing in two separate categories at the Geneva observatory, “Chronomètres de Poche petit format” (small pocket watches) and “Chronomètres-bracelet” (wristwatches) – maximising chances of success.
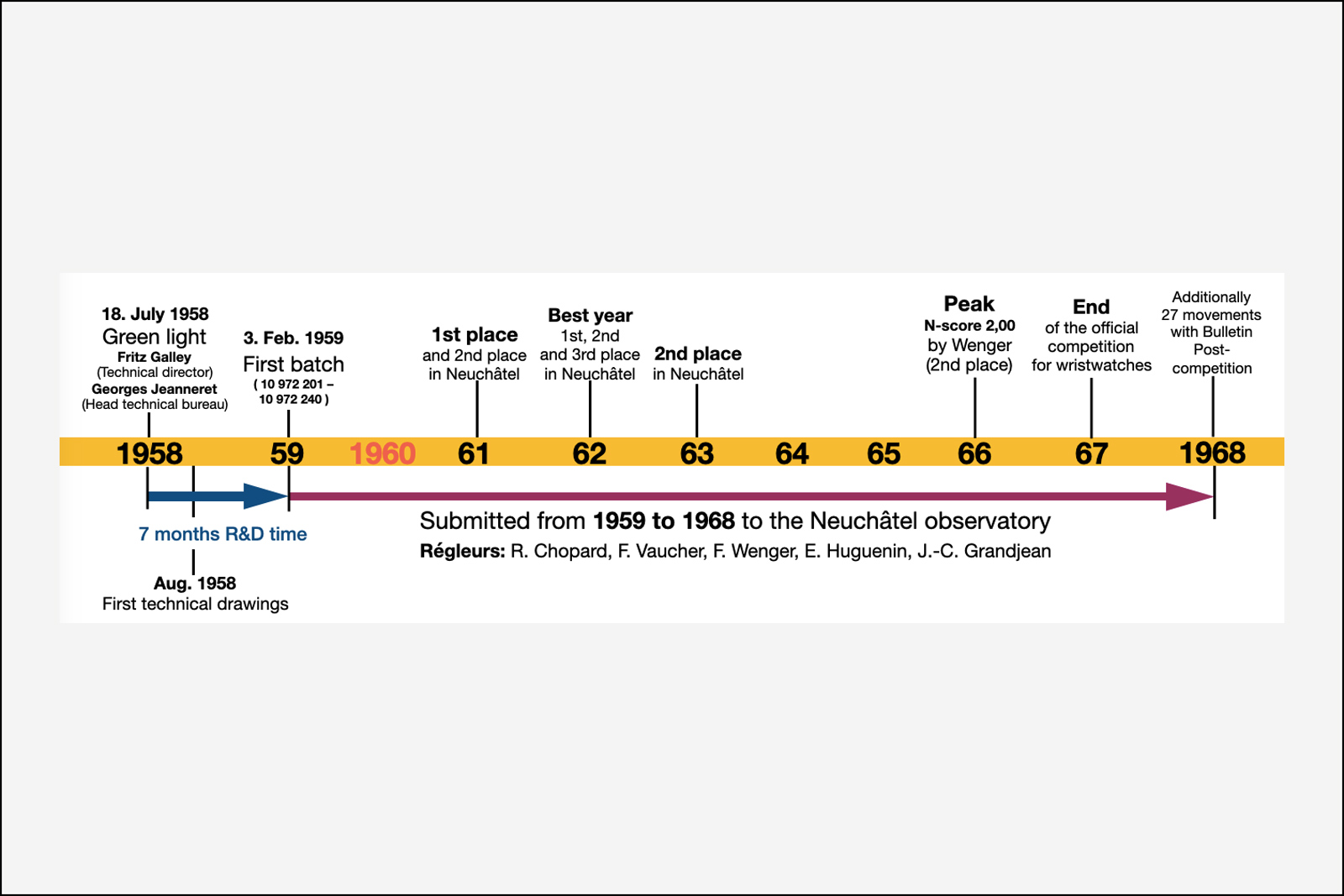
The timeline of key facts and milestones of the cal. 360
Technical features
Longines’ brilliant, out-of-the-box thinking in movement design and mechanical packaging resulted in a caliber that features an array of micro-mechanical peculiarities that pushed the envelope in chronometric performance, making it Longines’ top performer by a significant margin.
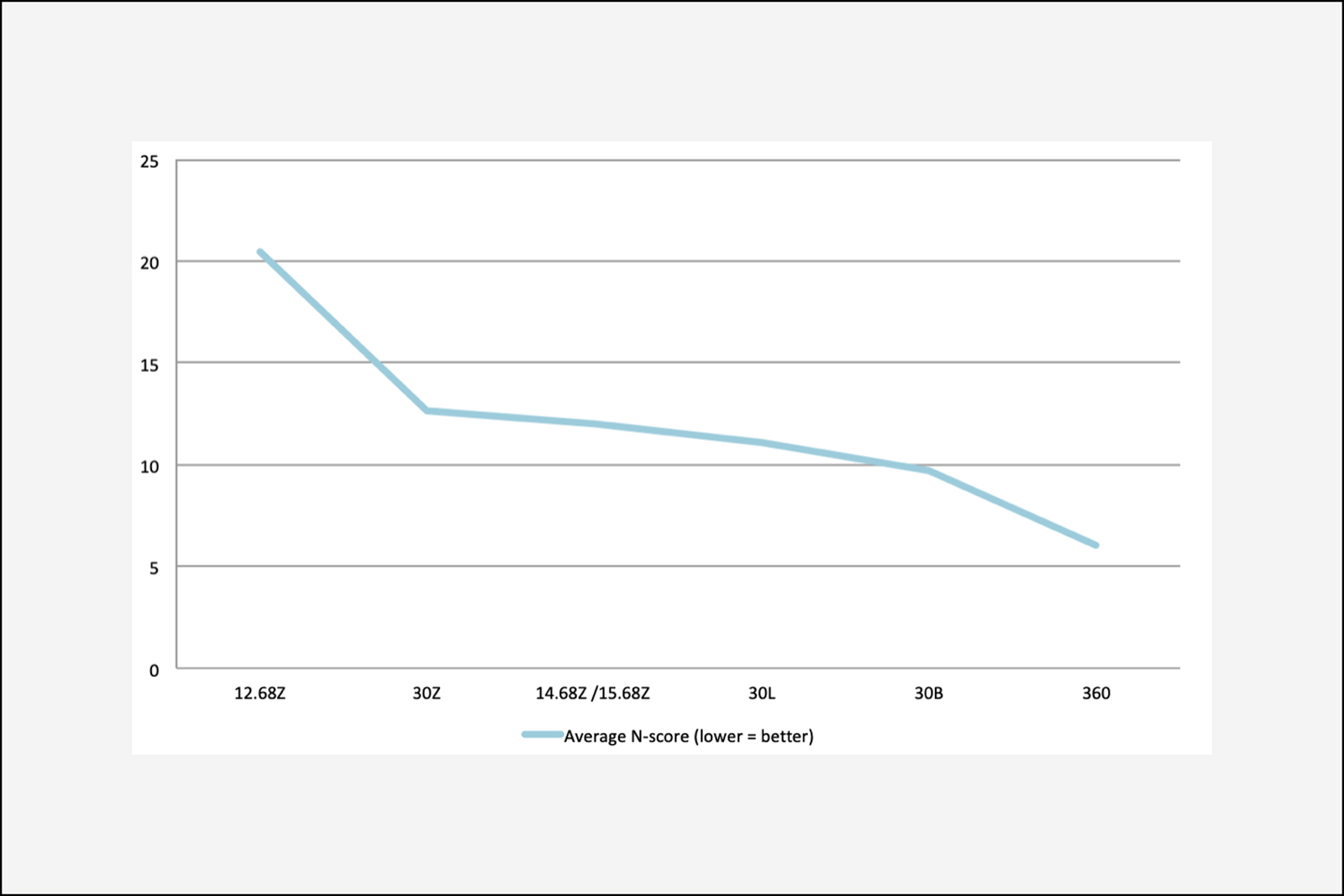
Comparing the performance of various Longines wristwatch-sized, observatory calibres submitted for testing at the Neuchâtel observatory.
High-frequency escapement
In the 1950s, wristwatch-sized chronometer calibers were rapidly drawing closer to a state of mechanical perfection, where an increase in chronometric performance was getting progressively more difficult to obtain.
Eventually, the performance at the competitions showed signs reaching a plateau (see graph above). To the rescue came game-changing improvements in lubricants – especially Moebius’ synthetic lubricant, Synt-A-Lube, developed in 1952 – as well as advances in metallurgy and manufacturing techniques, which suddenly allowed for an increase in beat frequency with sustained rate stability.
Fundamentally, an increase in frequency, and therefore the angular velocity of the balance, results in an oscillator that is less susceptible to external perturbations, which could negatively affect the rate (see section below “Connecting the dots”).
It was a paradigm shift in precision watchmaking, considering that prior efforts in improving the performance of the oscillator targeted primarily the balance diameter – bigger was thought to be better – backed by the knowledge that high-inertia balances were associated with improved rate stability, especially under static testing conditions, in other words observatory contests.
Longines had manufactured high-frequency chronograph movements in the early 20th century with the purpose of improving the measurement of elapsed time. An internal Longines document dated February 14, 1958 and authored by Fréd.-E. Pfister, the former technical director at Longines, describes a modified cal. 19.73 that was delivered in June 1914, which allowed for the measurement of 1/10th-of-a-second, and further refined to 1/100th of a second in 1916. However, it was not until the cal. 360 that Longines fitted a high-frequency escapement into a wristwatch-sized movement.
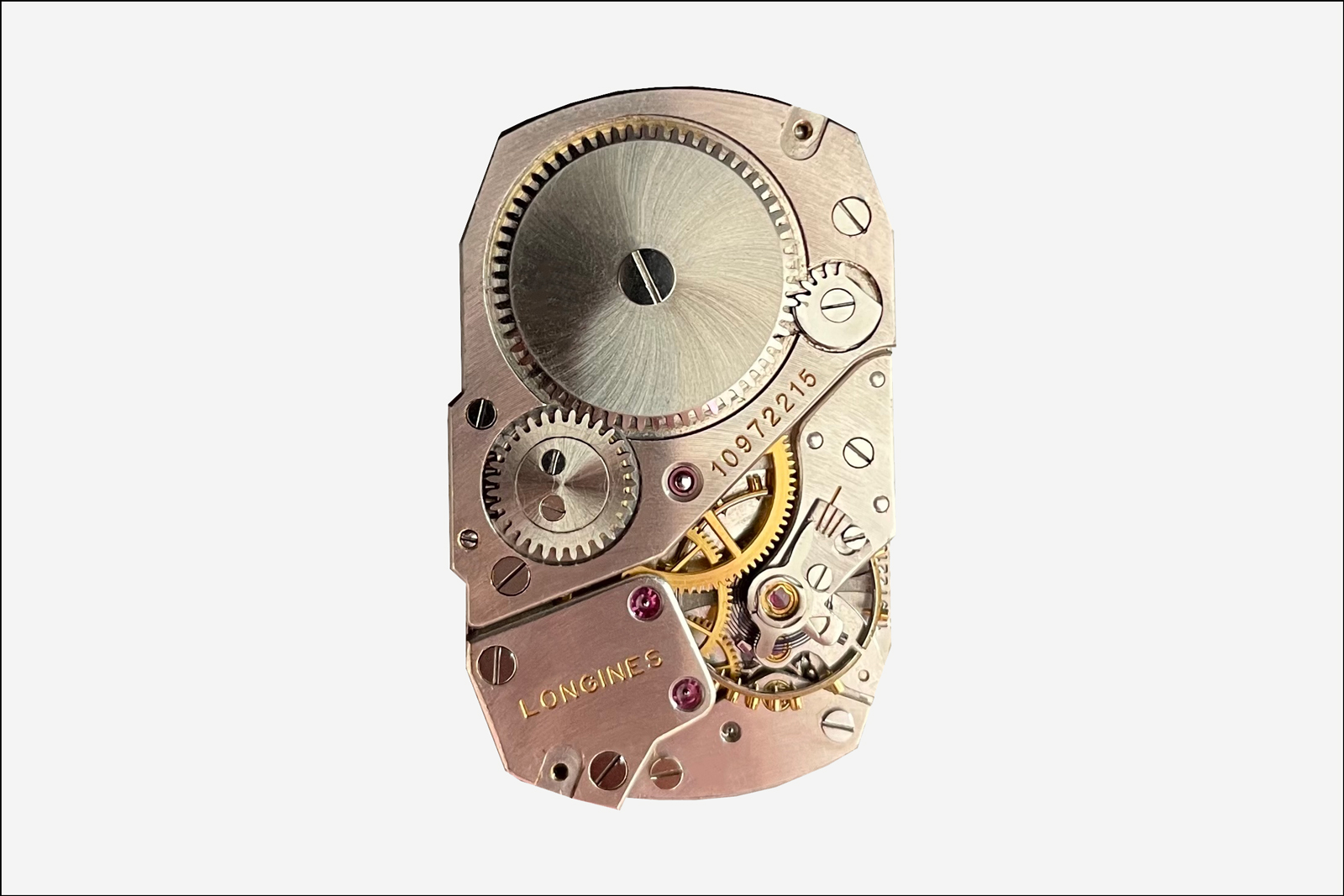
The cal. 360
Oscillating at 36,000 vibrations per hour (VpH), or 5 Hz, the cal. 360 was a breakthrough in precision watchmaking. In order to increase the number of revolutions of the conventionally-toothed escape wheel – it had 15 teeth – an additional wheel was added to the going-train, positioned between the fourth and escape wheel.
It was a technical compromise that increased friction and measurably decreased the efficiency of energy transmission. Furthermore, due to the additional wheel, the escape wheel would rotate opposite to its conventional direction. In order to ensure the correct rotation for the escapement, the escape wheel was mounted upside down.
On October 6, 1966, about eight years after the development of the cal. 360, Fabriques d’Assortiments Réunis (FAR), a maker of assortments (referring to the parts of the escapement and balance) in Le Locle, Switzerland, filed US trademark application no. 72255903 for an innovative high-frequency escapement, baptized as the “Clinergic 21”.
Compared to the escapement design of the cal. 360, the most significant differences of the Clinergic 21 are:
- The escape wheel has 21 teeth instead of 15, hence the name
- It has a 100-tooth fourth wheel
- The elimination of the additional wheel in the going train.

The under-dial view of the cal. 360
With the Clinergic 21, FAR had perfected the high-frequency escapement. For the first time in mass-production watchmaking, reliable operation at high beat rates of 4-5Hz could be guaranteed, ipso facto, the development of the Clinergic 21 had enabled the adoption of the high-beat escapement in the watch industry.
With the introduction of the Ultra-Chron (automatic cal. 43x) in 1967 to mark Longines’ centenary, the first high-frequency calibers were produced on an industrial scale in St. Imier. The in-house Ultra-Chron calibres utilised the Clinergic 21 and featured escapement components that were coated with a nifty molybdenum bi-sulfide dry lubricant, referred to as “filmogenic lubrication” by Longines.
Most importantly, the Ultra-Chron calibres offered unprecedented timekeeping performance for a mass-produced mechanical wristwatch. They were advertised as boasting “accuracy guaranteed to a minute a month”.
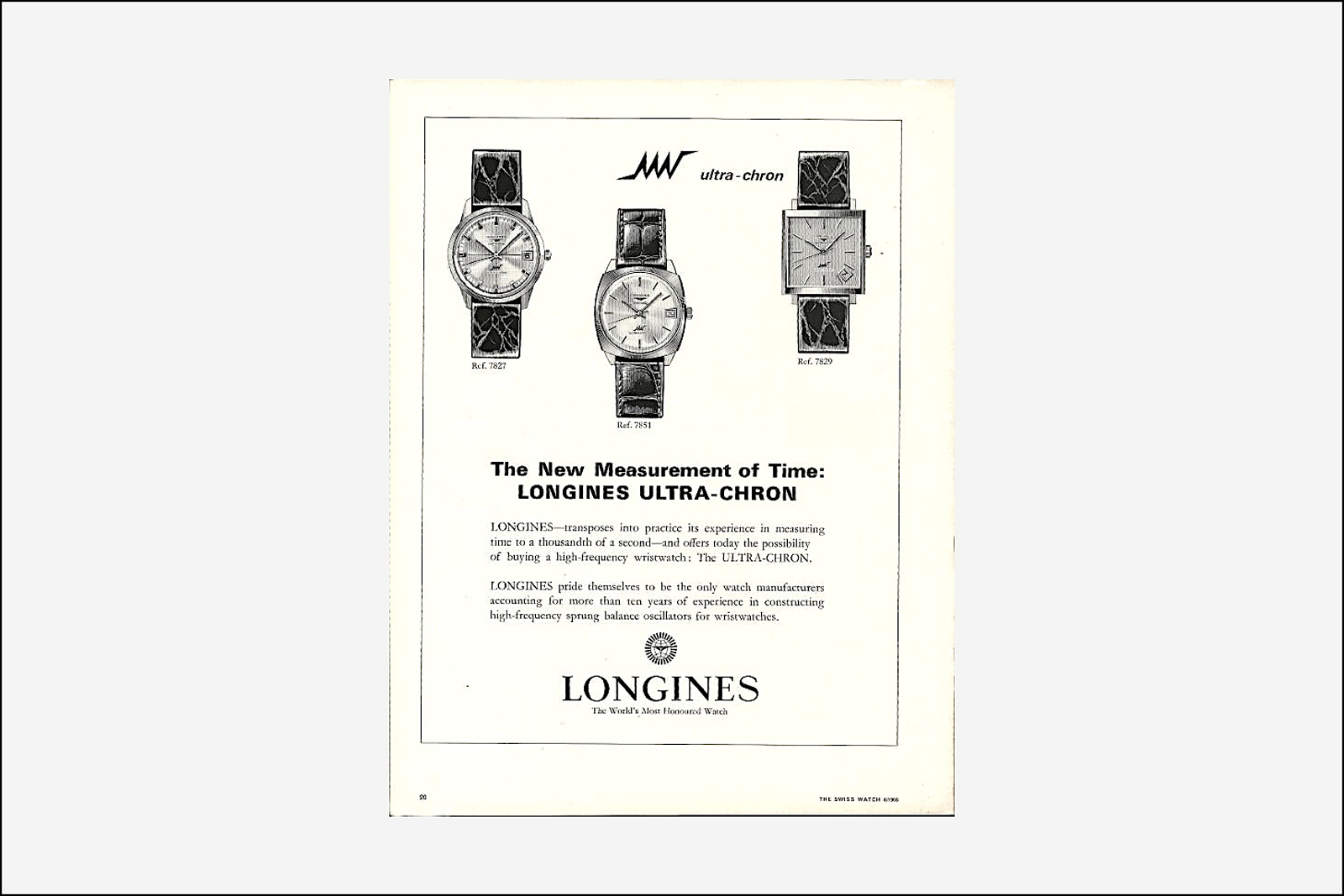
A period advertisement for the Ultra-Chron
Movement layout
With the chronometry competition of 1949, the Neuchâtel observatory introduced new limits for the wristwatch category (category referred to as “Bt”): a maximum movement diameter of 30 mm and a height limit of 5.3 mm. The maximum diameter resulted in a surface area of 707 mm² (=π15²), which was an equally accepted maximum dimension.
The rectangular shape of the cal. 360, which measures 705 mm² (~ 36 mm by 22 mm), was smartly devised for an optimum size of the balance wheel and mainspring barrel – crucial components for precision timekeeping.
It needs to be understood that any traditionally-constructed, round 30 mm movement can only house a mainspring barrel with a maximum diameter of just under 15 mm, slightly less than half of the movement’s diameter, since the centre wheel limits the size of the barrel. However, a rectangular surface of just below 707 mm² cleverly provides ample room for an oversized mainspring barrel.
Moreover, a clever design trick helped to further maximise the barrel diameter of the cal. 360. The centre wheel was moved roughly 1.5 mm in the direction of the balance, positioning it eccentrically and freeing up extra real estate for the barrel, a detail already found in Longines’ round chronometer cal. 30B, the predecessor of the cal. 360. (However, in the case of the cal. 30B, the cal. 360 combined a lowered escape wheel with a centre wheel that was relocated in the opposite direction towards the barrel, in order to increase the balance wheel diameter to a staggering 15.3 mm.)
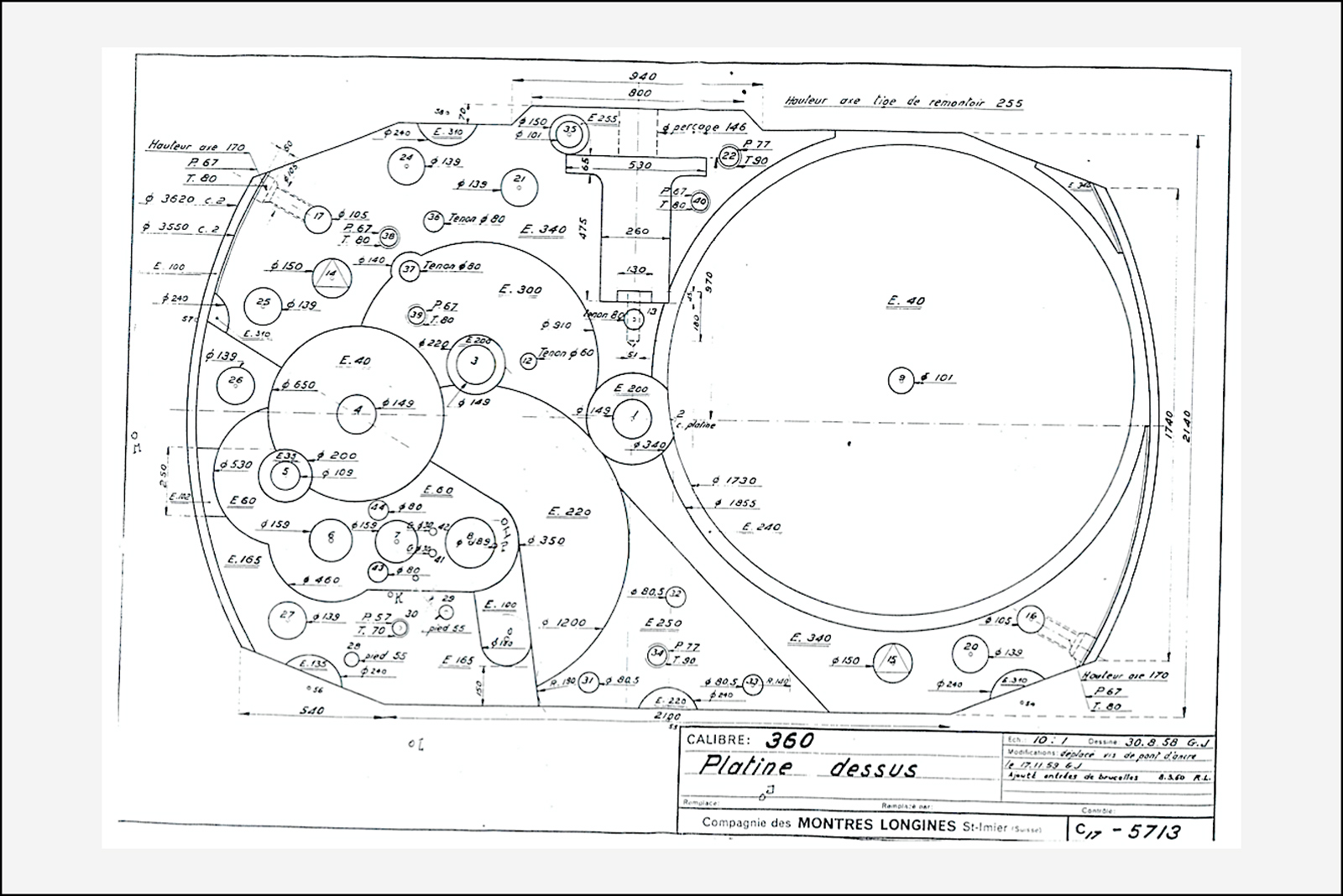
Technical drawing of the main plate of the cal. 360. Note the large mainspring barrel.
As a result, the barrel in the cal. 360 clocks in at an imposing 18.30 mm, considerably larger than it could be in a conventional round movement of 30 mm. In consequence, the mainspring can store enough energy to drive a substantially sized and fast-beating balance wheel while providing a prolonged, flat torque curve as the barrel unwinds.
Considering the fast beat rate, the surprisingly large balance was certainly a nod to the past mantra in chronometry where large and heavy balance wheels were favored. To put these dimensions in perspective, the 11.50 mm (including the screws) balance in the cal. 360 has a diameter equal to that of a full-sized balance inside a round, 30 mm chronometer calibre beating at a languid 18,000 VpH.
To package the generously sized balance into the rectangular movement layout, the escape wheel on the cal. 360 was positioned under the balance and closer to the centre of the balance. Such a lowered escape wheel is a distinct feature that can be found on the cal. 30B, the predecessor of the cal. 360, but also on other important wristwatch-sized chronometer calibres from other makes, including the Omega GD, Peseux cal. 260, and Zenith cal. 135. As a result, the pallet fork and escape wheel were kept as small, short, and light as geometrically possible in order to lower inertia and increase the efficiency of the purposefully delicate and lightweight escapement.
Connecting the dots
The high moment of inertia (l) and angular velocity (ω) of the balance wheel results in a notably high angular momentum (L=Iω), especially when compared to balances found in calibres with the same surface area.
Based on the law of conservation of momentum, the increase in angular momentum yields an increase in stability within the oscillating balance-spiral assembly, thus improving timekeeping performance (An increase in angular momentum is followed by an increase in resistance to changes in the direction of the axis of rotation, i.e. an exerted external torque needs to be higher to cause significant perturbations).
The above derived chronometric advantage is equally reflected in an increase of the so-called Quality Factor (Q) of the oscillating organ, which is largely determined by its frequency, but also a product of friction and mass.
As a measure of the efficiency of the oscillator, Q is recognised as a strong indicator of the inherent chronometric potential of a movement. The Q of a standard mechanical wristwatch caliber usually does not exceed 200 (in the dial-up position), while an excellent wristwatch-sized chronometer beating at ≥4Hz can more than double that number to 400-600. For comparison, a low-cost quartz watch resonating at 32,768 Hz achieves a value of 100,000 – a 250-fold increase in Q (see figure below).
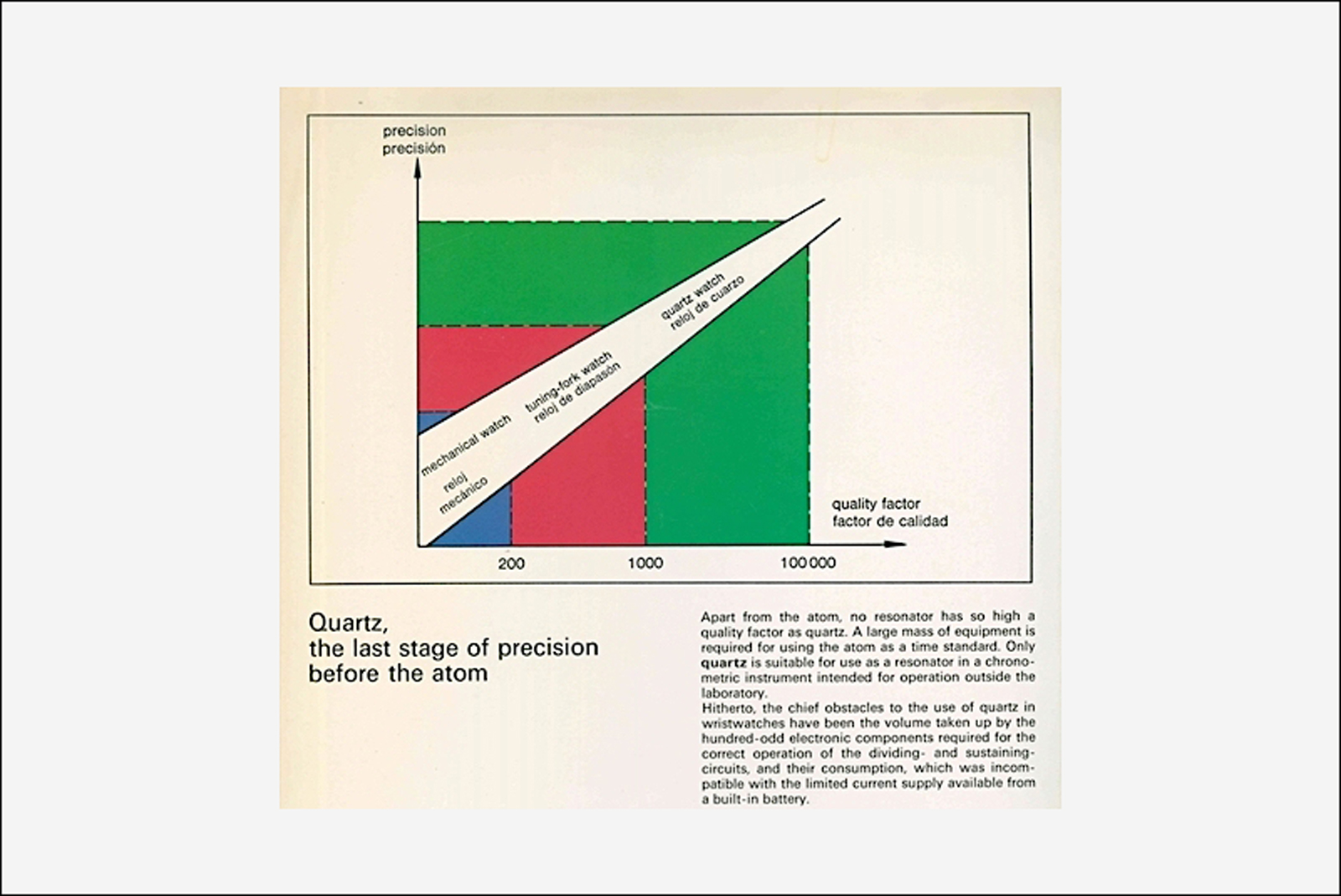
Longines Ultra-Quartz sales brochure from 1970 visualising the concept of the Q-Factor
Generally, shorter oscillations (i.e higher frequencies) are correlated with smaller deviations in rate. For that very reason, the novel low-amplitude, high-frequency oscillators of today, that are based on compliant mechanisms, including the monolithic silicon oscillator of Frederique Constant, show exceptionally high Qs and have become the benchmark in mechanical precision chronometry.
It is important to note, that the real-world performance of any mechanical watch depends on a host of factors, beyond Q and the angular momentum of the oscillator.
Observed variances
Based on Longines’ ledger entries, a grand total of 200 cal. 360 movements were manufactured between 1959 and 1963, in four distinct batches, referred to by collectors as series 1-4. It is assumed that the total number produced was slightly higher, due to potential non-numbered or unregistered prototypes.
Regulator design
Depending on the movement series, three distinct regulator designs (Types 1-3) are known.
Type 1 – Adjustable stud
This design is found on all first and second series movements. The type 1 is comprised of an adjustable steel mounting with an integrated hairspring stud carrier that is affixed on top of a cut balance cock. The component can be shifted on the balance cock, which enables easy adjustment of the stud (beat error correction), and centering of the balance wheel.
Type 2 – Clamp
Discovered on an early third series movement that had retained the cut balance cock found on movements from the first and second series. However, the Type 1 regulator design was replaced with an aesthetically pleasing, non-adjustable polished steel component that holds the stud in a fixed position.
The looped design clamps the regulator lever from both sides via friction and improves adjustability. Interestingly, the same clamp design without the integrated stud-holder can be found on various Longines calibers, i.a. cals. 22L and 22A.
Type 3 – Fixed stud
Appears at the beginning of the production of the third series (some early third series movements retained the Type 1) and is seen throughout the run of the fourth series.
The stud carrier is integrated into a regular-shaped balance cock – hence it is fixed. An elongated component is mounted on top of a conventional regulator arm, with the purpose of clamping down and generating constant, but adjustable, friction, thereby improving adjustability.
Hairspring
The cal. 360 was equipped with an overcoil hairspring with Grossmann inner and Phillips outer terminal curves – these rarely seen inner curves were often referred to by régleurs as the courbe du coeur, or heart’s curve. Two terminal curves force the hairspring to “breathe” concentrically and shift the hairspring’s centre of gravity (COG) towards the balance axis allowing for isochronous oscillations and minimise positional errors of the balance wheel-hairspring assembly.
Predominantly, a classic steel hairspring paired with a split bimetallic Guillaume type balance can be observed across all batches of the cal 360. However, Invar, 18k palladium, as well as auto-compensating Nivarox hairsprings in combination with a Glucydur (the trade name for a beryllium-bronze alloy) balance wheel, have also been noted.
Balance wheel
Most cal. 360 movements were equipped with a Guillaume balance wheel (GBW), the de facto standard for observatory chronometers, while a handful of early first series movements feature monometallic, Glucydur balances.
The GBW is constructed of an outer brass and inner nickel-steel (Anibal) rim laminae and offers excellent temperature compensation – provided that it was prepared by skilled hands. The primary and secondary temperature errors were important criteria at the observatory competitions and had a significant impact on the final ranking of the tested chronometer.
The régleurs consistently championed the use of the GBW, even long after metallurgically more advanced, monometallic balances with exceptional hardness, low magnetic susceptibility, and close-to-zero thermal expansion coefficients were commonplace in mass-produced movements. Why?
The widespread use of the GBW at chronometer competitions was driven by its predictable behaviour and the much favoured, high degree of adjustability in terms of temperature compensation (by moving temperature screws or weights on the balance). In contrast, a Glucydur balance and its auto-compensating hairspring can not, and does not need to, be adjusted for temperature compensation since the entire assembly is virtually non-susceptible to thermal influences. Consequently, the temperature behavior and performance would not lie at the hands of the régleurs and merely depend on the inherent quality of these components.
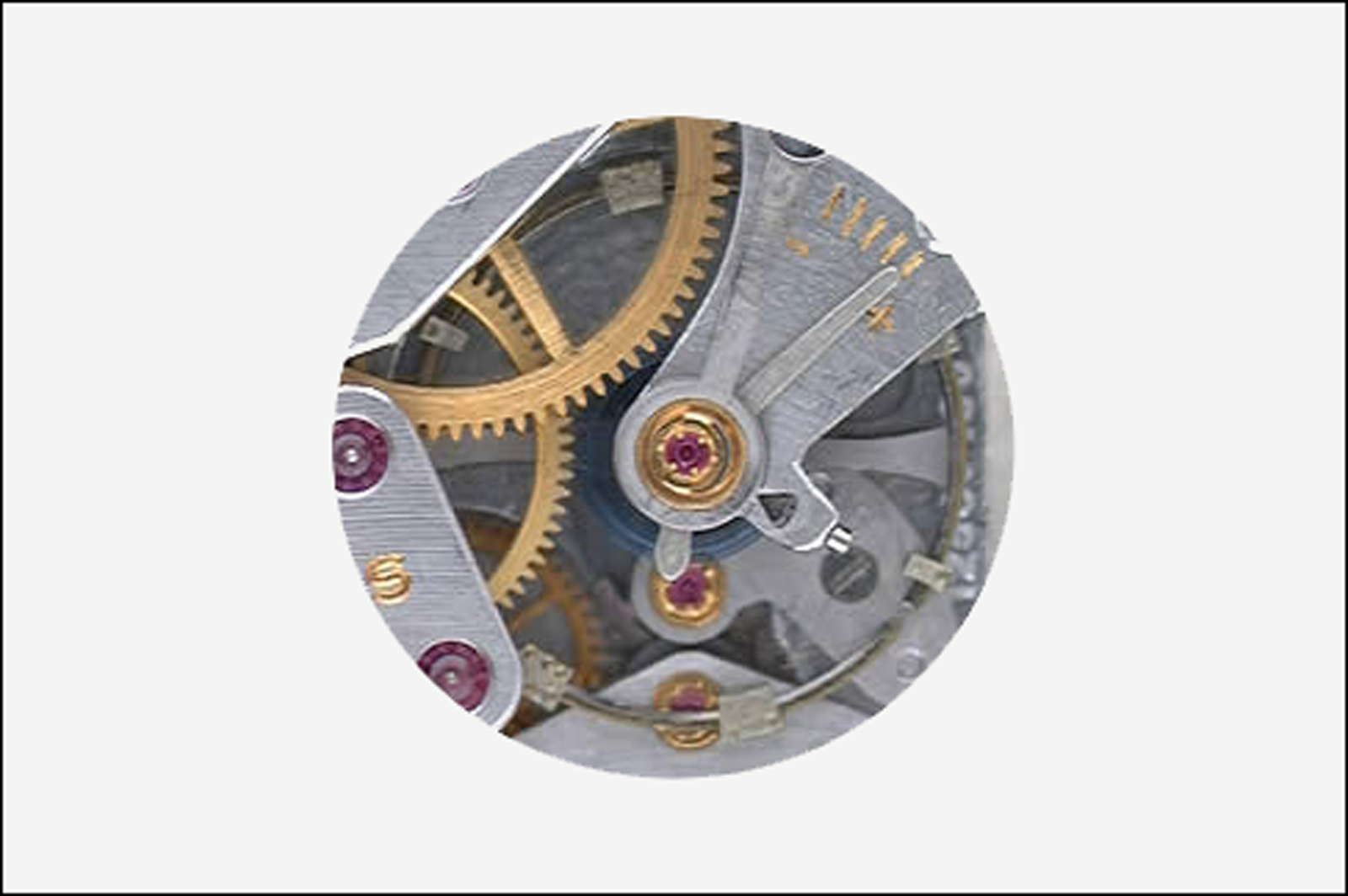
An experimental Guillaume balance with adjustable weights – such balance wheels have their origins in traditional marine chronometers. The adjustable weights can be moved along the balance rim in minute increments, improving temperature compensation
Jewelling
Most interestingly, the cal. 360 features Girocap or Duofix shock protection throughout the entire escapement (balance, pallet fork and escape wheel).
Such shock protection was an unusual sight in observatory chronometers, considering that it was long believed that the associated mechanical play would have a detrimental effect on timekeeping.
However, it was acknowledged that finely polished pivots – the balance staff pivot of the cal. 360 is just 0.05 mm in diameter – required protection. Furthermore, elastically-mounted jewel bearings would improve oil retention in the fast-rotating pivots of the high-frequency escapement and simplify the adjustment of pinion end shake – all clear advantages that outweighed the initial concerns.
Dial
Indicated by the “ZJ” (short for “Zélime Jacot”) stamp on the reverse, the dials were exclusively manufactured by the Saint Imier-based Flückiger & Cie, today a subsidiary of Patek Philippe. Various Flückiger order numbers for the cal. 360, including 1’6320 and 5139 have been observed.
The restrained, printed dials are signed “Chronomètre” right below “Longines” – a lesson in Swiss understatement. That pared-down design was used on several observatory calibers predating the cal. 360, including the cal. 30L, 30B, and 30Z. However, being 34 mm in diameter, the cal. 360 dial is the largest of the four.
Some dials from the third and fourth batches show a distinct, round cutout in the dial, directly positioned above the critical jewel setting of the balance staff in the main plate. This enabled the régleur to assess the oiling status without having to lift the dial.
As with many competition-chronometer dials, the black markings applied to the lower section of the subsidiary seconds are evidence of submission for observatory testing. These markings were meant to be picked up by a simple light-sensitive phototube linked to an Omega-developed optical time recorder (OTR).
When the second hand covered the white slit on the marking, the minuscule change in emitted light was detected by the phototube, which in return triggered the OTR that instantly recorded and printed the time.
Prior to 1956, chronometers were manually timed to within 1/10th of a second. Subsequently, the introduction of the OTR system enabled time measurements to 1/100th, and later to 1/1000th, of a second.
Case
The movements were mounted eccentrically in their inner casing due to the offset position of the caliber’s centre wheel. The outer case, a square block in either aluminum or wood, allowed for safe transportation and testing in five different positions.
First and second series movements were, with some exceptions, cased in hardwood. Whereas the solid aluminium alloy case appears on all pieces of the third and fourth series.
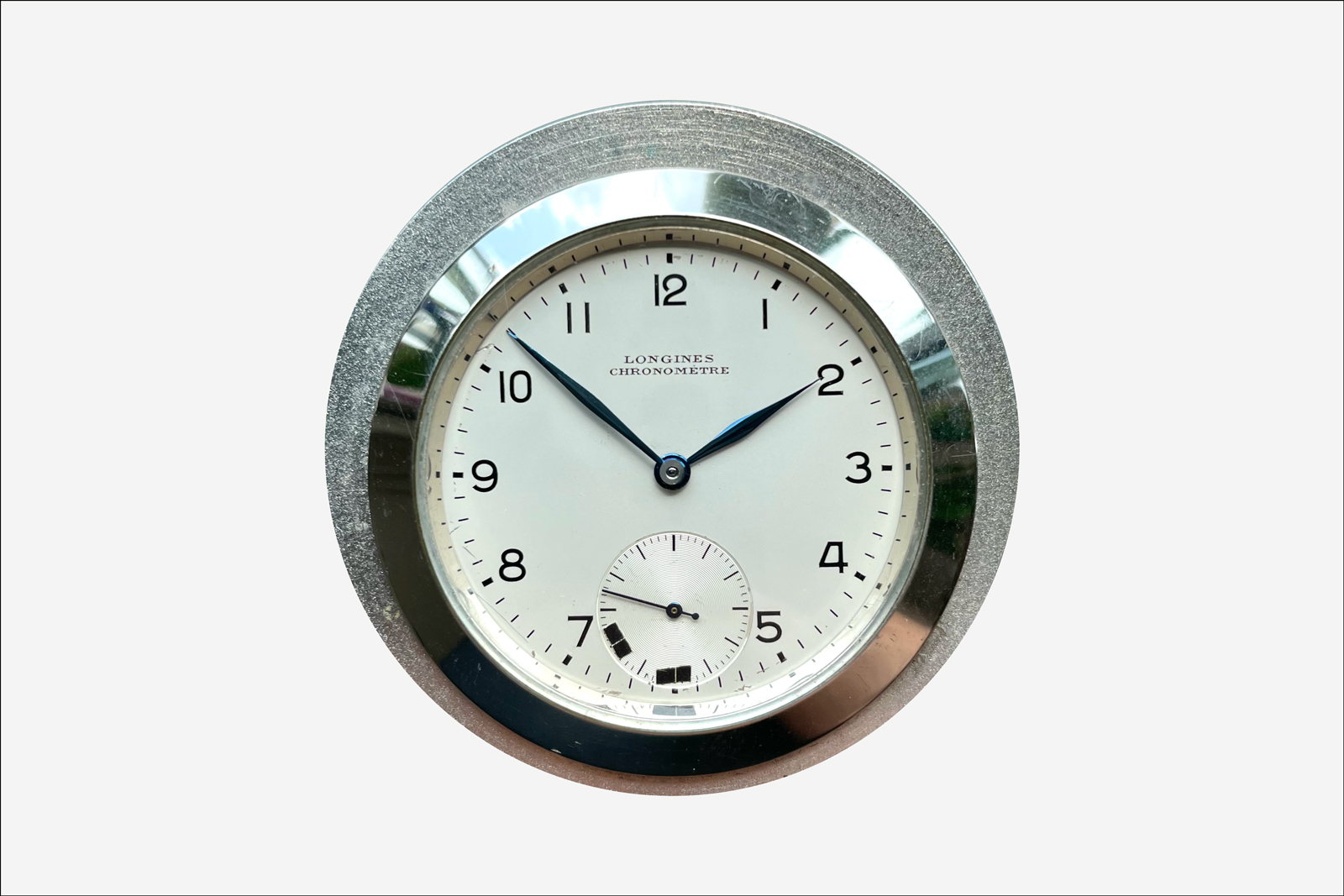
The inner casing was identical on all series. Note the difference in the space between the dial and case at the top and bottom – indicating an eccentrically-mounted movement. Timing marking were applied to the lower sections of the subsidiary seconds.
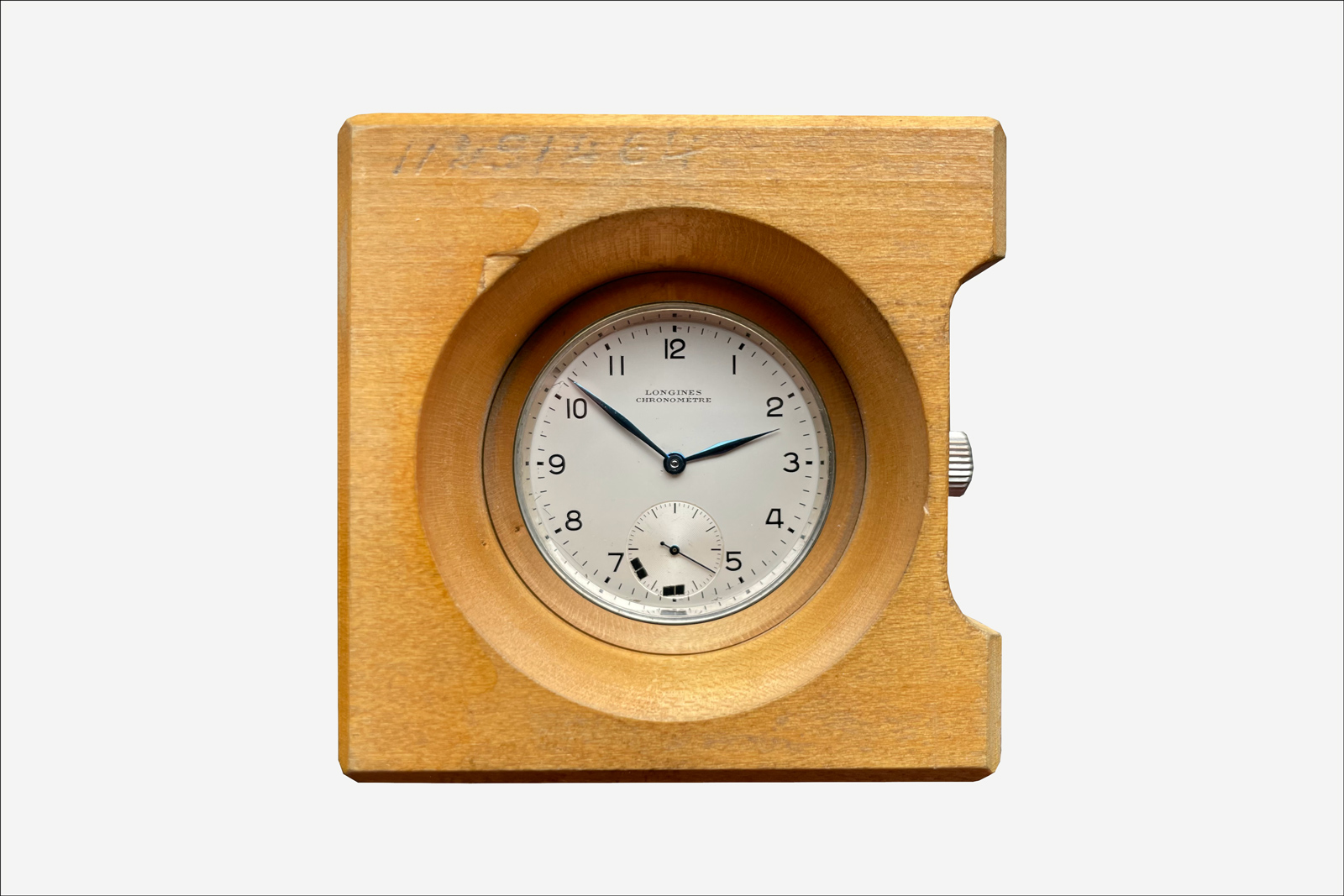
Outer case made of hardwood, measuring 70 mm by 70 mm by 36 mm
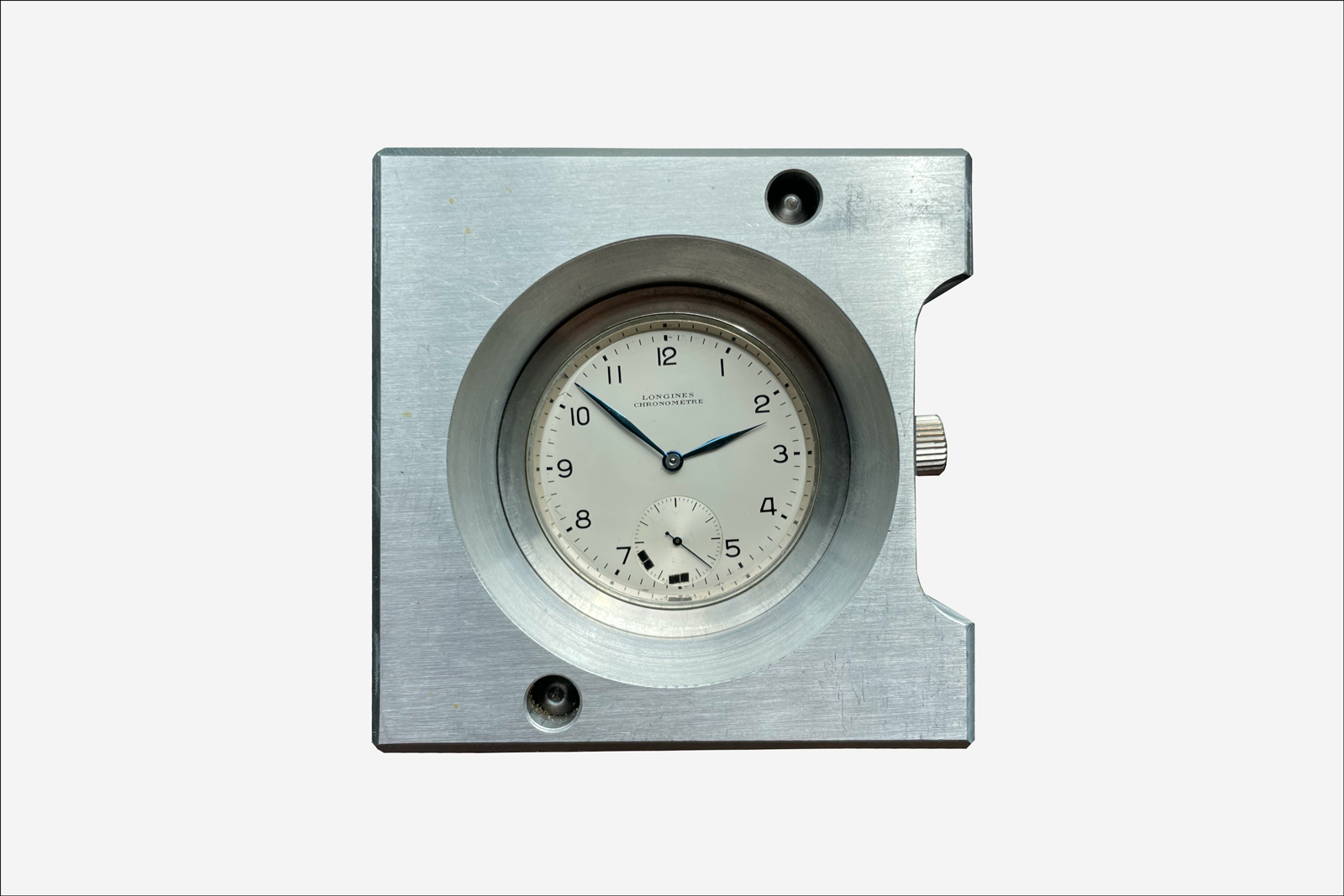
Or aluminium alloy, 70 mm by 70 mm by 32 mm
Crown
Later metal-cased pieces mostly feature a flat, cylinder-shaped crown, while earlier movements cased in wood were usually equipped with a crown that has a pronounced tapered collar.

The early crown with a tapered collar (left) and the later flat crown
A word of caution
Deviations from the established features for each series have been observed across various examples of the cal. 360, for instance a Type 1 regulator on a third series movement. Why?
The same movements were submitted multiple times for testing in consecutive years, and as a result, such movements were often significantly reworked and re-adjusted by the technical department and the respective régleur. Hence, most deviations from known conventions are legitimate and should not negatively impact collectibility.
A curious case
Evidently, the cal. 360 was never intended for large-scale commercialisation and the consumer market, although a single wristwatch-cased cal. 360 has surfaced. The piece is part of the permanent collection of the Longines museum in Saint-Imier.
A quirky-looking piece with a top-mounted strap, bullet-shaped lugs, and a brilliantly designed dial made by Flückiger & Cie. (stamped “22552 ZJ”). Furthermore, an internal Longines document describes a potential second example: a physicist received an unspecified watch with the cal. 360 for extensive “in-field” testing in 1968.
Final words
The caliber 360, a from movement, owes its prominent rectangular shape to the relentless pursuit of chronometric performance and as such, exemplifies the well-known design principle of form follows function.
The cal. 360 has marked Longines’ final march, up the high grounds in precision chronometry – a micro-mechanical tour-de-force from a bygone era that came to an undignified end with the arrival of quartz technology in the mid 1960s. Ultimately, the cal. 360 needs to be recognised as a horological milestone that paved the way for high frequency in mass watchmaking.
This article will also be published in the Longines reference book for collectors that is scheduled to go to print in late 2022. It’s been reproduced in advance here with the permission of the book’s authors as well as Longines.
Back to top.