Explained: Dial Making at Rolex
From electroplating to PVD and more.
One aspect of a watch that is often overlooked — but ironically the one that is front and centre — is the dial. While often conservative in terms of design, Rolex is perhaps at its most expressive in the details of its dials, which blend classic elements with modern touches, all accomplished by modern manufacturing techniques and finishes.
Even though a dial may seem simple on its face compared to the moving parts of the movement, dials are complex. Much goes into making a high quality dial, the dial blank, applied ornaments, surface finishing, gold indices, and more recently even grand feu enamel.

A diamond-set dial for the Oyster Perpetual Day-Date
Unsurprisingly Rolex takes dial making very seriously. Reflecting its long-term vision, Rolex has invested tremendously in every aspect of manufacturing wristwatches, including producing its own dials.
Dial manufacturing of the highest quality, and at scale, is a challenge few have truly mastered. Rolex accomplished that with a dedicated dial-making facility in the Chêne-Bourg district of Geneva, located about 15 minutes from Rolex headquarters, where some 500 people work exclusively on dial conception, prototyping, and production. Notably, the Chêne-Bourg facility also does gem setting as well as the production of Cerachrom components like the GMT-Master II bezel insert.
In-house dial making has given Rolex control of the entire process, allowing the brand to innovate, even in rethinking the very foundation of a dial, namely its attachment to the movement. We’ll delve a little into what goes into a Rolex dial.

The dial making factory at Chêne-Bourg also produces cloisonné enamel dials
Rethinking the basics
Rolex has innovated in ways big and small, ranging from materials science to case construction, and it has done the same with its dials by completely redesigning the method of affixing the dial to the movement.
The vast majority of watches feature dials that employ soldered pins on their reverse known as “feet”. These tiny pins fit into dedicated slots in the movement plate, then screws are tightened against the pins, locking them in place and securing the dial to the movement.
Feet are fragile and can bend if mishandled during service. A bent pin means the dial will not sit properly on the movement, requiring the watchmaker to adjust the feet manually. That, in turn, can result in the feet breaking off entirely. And then there’s the fact that each pin is tightened by a screw, which adds work to the assembly process.
Rolex solved all of those problems by constructing its dials differently, relying instead on an entirely different fixture system. European patent number EP2743783B1, filed by Rolex all the way back in 2012 (but only granted in 2022), describes a lip-like ring (grey) that extends from the underside of the dial plate (yellow). The ring also incorporates elastic apertures 10 and symmetric cutouts 5.

Fig. 1 extracted from European Patent EP2743783B1. The patented dial construction; note the notch 25 on the base plate that slots into cutout 5.
When the dial is assembled on the movement, the elastic portions of the ring pass over the rim of the movement plate, snapping into place and latching the dial tightly onto the movement.
Because of the new dial construction, the movement has to be modified: the base plate incorporates notches on its circumference 25, which fit into the dial ring’s cutouts 5. This movement construction can be found in Rolex’s latest-generation movements, including the cal. 32xx family.
Assembled in this fashion, the dial is kept securely in place by the compression of the elastic blades in the dial ring. This guarantees the dial will be in the correct orientation relative to the movement and eliminates the possibility of broken pins. Models like the Perpetual 1908 feature dials with this inventive construction.
Clearly more difficult to manufacture than a classic dial with feet, this innovative dial construction also requires adapting the base plate of the movement to accommodate the dial fixture. Together, they dictate substantial changes to industrial manufacturing processes – a large investment but one that pays off over time. In the long run, the novel dial construction assures the sturdiness of the dial, streamlining assembly and subsequent servicing.

One of the newest dials designed by Rolex, the guilloché dial in the Perpetual 1908
The finishing techniques
For the owner of a watch, the most important aspect of the dial is its aesthetics. And a good portion of a dial’s appearance depends on the treatment for its surface, which typically falls into three categories: electroplating, physical vapour deposition (PVD), and lacquering.
Dial blanks start off as metal discs of either brass or gold. Brass is more widely used since it has ideal mechanical proprieties – malleable, non-ferrous, and machinable – allowing it to undergo many surface treatments. Gold is used for more specialised dials, since its added malleability is well-suited to enamelling or gem-setting.

Aside from brass and gold, Rolex also employs more exotic materials for dials, including meteorite
Typically, the first step in dial treatment is electroplating. Electroplating, also known as electrodeposition, is a common process employed in many industries that bonds one metal to the surface of another through electrolysis, in order to create either a decorative or protective layer. The technique is applied to uses as diverse as jewellery production to the minting of coins, and even integrated circuits.
At Rolex, brass dial blanks are electroplated in gold and nickel baths, creating a layer that assures corrosion resistance. This does not determine the final colour of the dial, but creates an optimal surface for subsequent decoration.
The next step creates the dial that the consumer sees, when blanks are finished with one of three primary methods: lacquering, PVD, or electroplating.
Lacquered dials have a distinctive lustre and depth, especially since lacquer is coated with a final layer of clear varnish. The versatility of a lacquered finish means such dials can be found across the Rolex catalogue, from Professional sports models like the Submariner and GMT-Master II to the classic Day-Date.

An example of blue lacquer applied to dials

Evaluating various types of green lacquer and matching them to dial drawings created by the Design Department
Historically, lacquer was applied by hand, layer by layer in a time consuming process where the artisan has to wait for each layer of lacquer to air dry before applying the next.
At the Rolex dial-making facility, lacquer is applied by airbrushing in a clean room in order to eliminate dust particles. Once the lacquering is completed, the dial is covered with a coat of transparent varnish, then polished to a deep gloss.
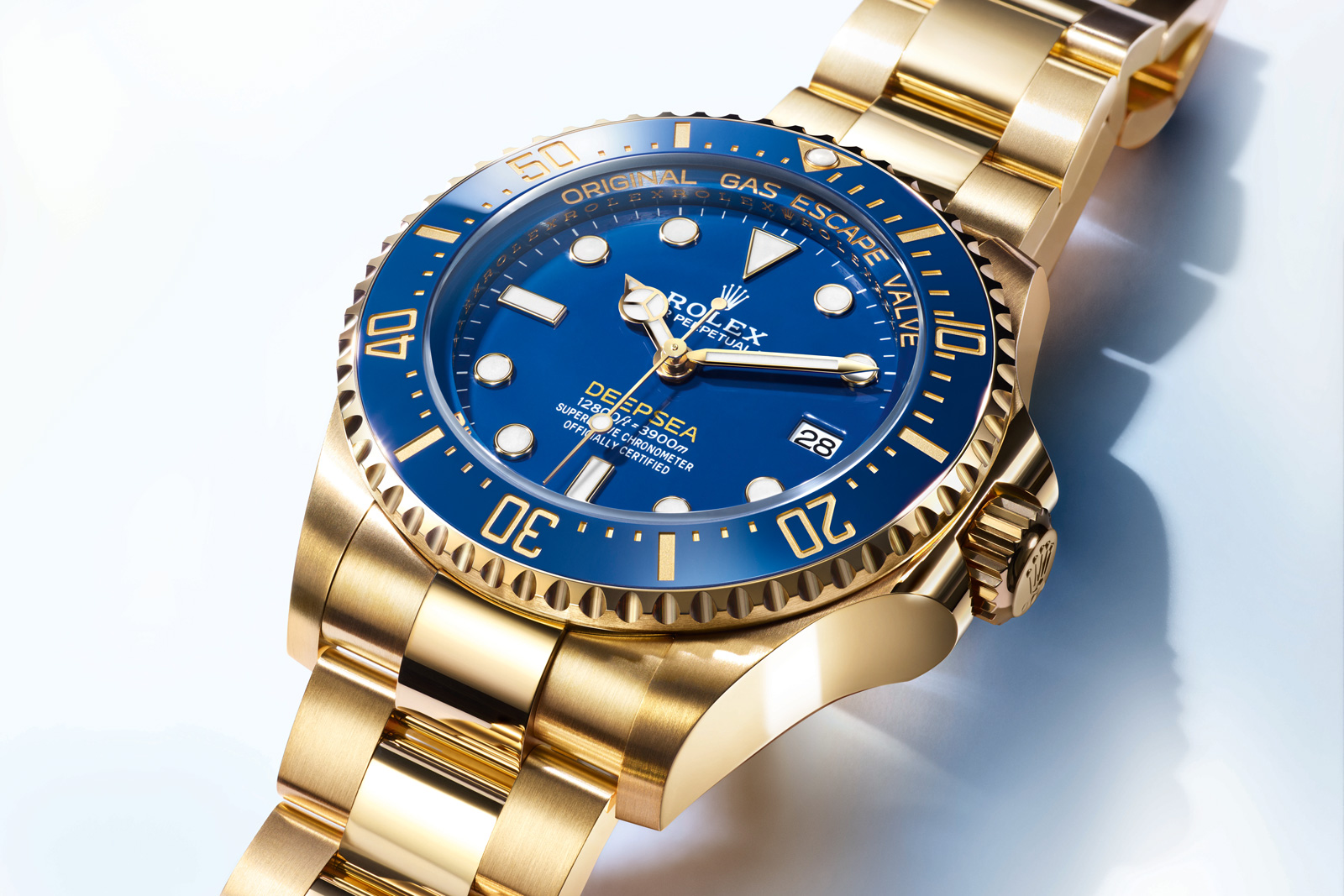
The Oyster Perpetual Rolex Deepsea with a blue lacquered dial
PVD is a process employed for coating surfaces with a thin protective film that is usually metal-based. The technique is useful for both protective and decorative coatings.
During the PVD process, the film coating briefly evaporates, going from a solid to a vapour state, allowing it to be sputtered on the treatment surface. The vapour then almost instantaneously becomes solid, creating the treatment surface with a thin film. At Rolex, PVD dials are coated with metal alloy-oxide or nitride blends, which form a film of about one nanometer on the dial plate.

A dial blank with sunray finish applied after PVD treatment
PVD has advantages over electroplating, including being more hard-wearing and allowing for a wider range of brighter colours. Varying the colour of the dial is a matter of changing the composition of the thin film, resulting in an almost endless range of finishes.
The more colourful dials in the Rolex line-up are most likely finished with PVD. Such dials still have a metallic finish but also a glossy finish evoking lacquer because the PVD surface is coated with a layer clear protective varnish.
Finally, electroplating is used to create dials in metallic shades — namely silver, gold, or rosé — that are most often found in precious metal models, like the Day-Date for example. The electrolysis process of electroplating also lends itself well to the radially brushed sunray pattern that is commonly employed as a surface finishing in such dials.

A champagne-tone dial of a Day-Date 40
Multi-component dials
For aesthetics or technical considerations, dials are sometimes composed of several parts. This is usually the case with complicated models. The Oyster Perpetual Cosmograph Daytona dial, for example, has separate discs for each of the chronograph registers.
A multi-part construction not only gives a dial layering and depth, but also creates the opportunity to use different materials for the sub-dials.
The most complicated model in the Rolex catalogue, the Oyster Perpetual Sky-Dweller also has a special dial. The Sky-Dweller dial is made up of two concentric plates that create an aperture for the 24-hour disc of the GMT function.

The Sky-Dweller dial in mint green
Such a two-part construction poses a particular challenge, since the two plates need to be exactly the same colour in order to create the illusion of that the dial is a single whole. This gets even more complicated for the Sky-Dweller models with solarised dials that are radially brushed. With such a prominent finish, the brushing on both dial plates need to match up perfectly in order to maintain the optical effect of a one-piece dial.
The finishing touch
Rolex is one of the very few watchmakers to consistently use 18k gold applied hour markers on all dials, even those in entry-level models like the Oyster Perpetual.
Such gold appliqués, which often includes the famous crown emblem, are the finishing touch on the dial. The text and minute track are pad-printed before the appliqués are individually applied.

Applying the coronet emblem to the dial
The process of setting the appliqués is a patient, precise one that is done by hand. Especially delicate handling is required to avoid marring the solid gold appliqués, which sometimes even requires paper-covered tweezers to pick up each appliqué.
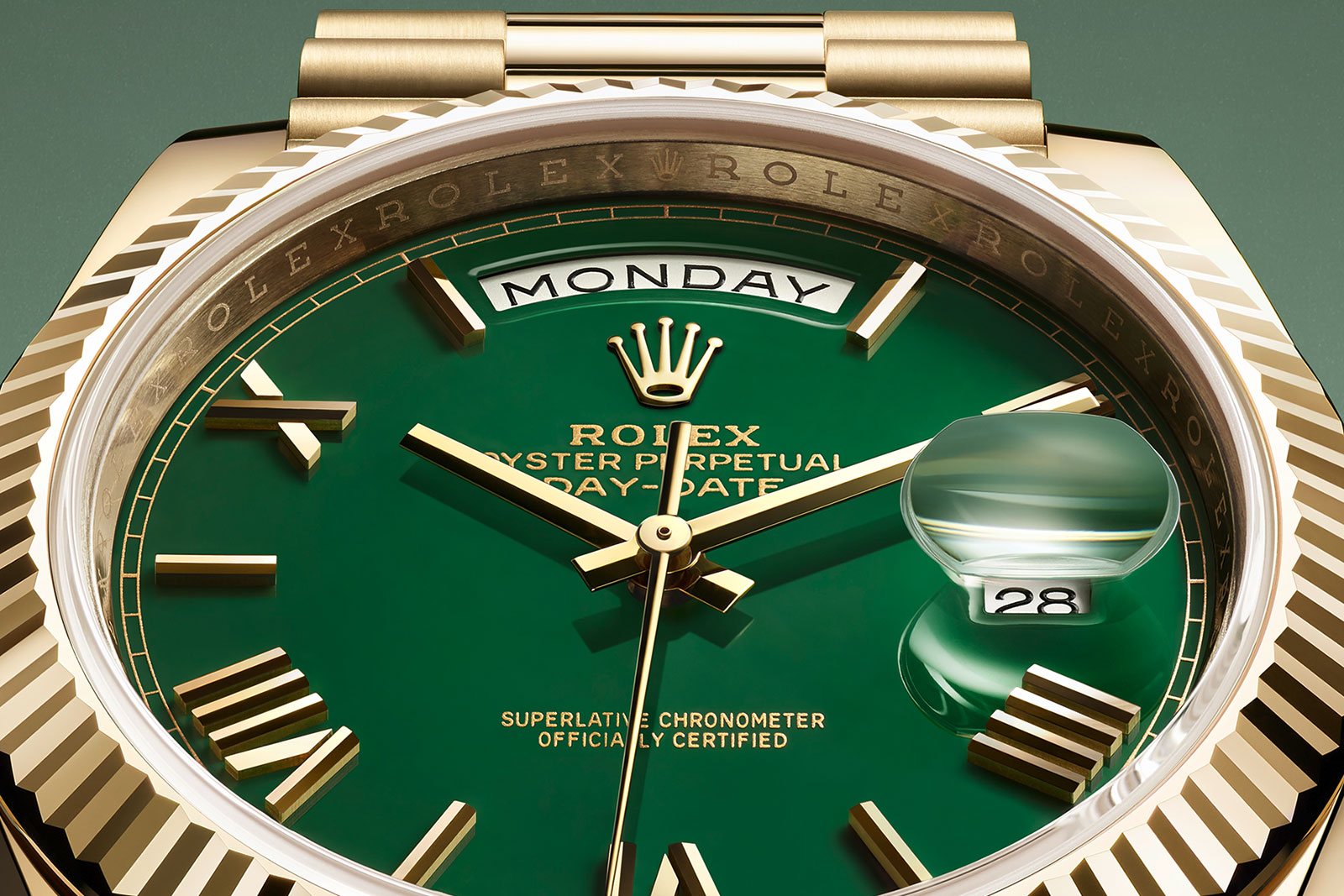
The Oyster Perpetual Day-Date 40 with a green lacquered dial
Despite the delicate nature of the applied gold elements, they are fixed permanently and securely to the dial. The appliqués have feet, which are pressed and riveted on the back of the dial plate.
Testing is done to ensure this: random samples of dials are drop- and impact-tested in order to ensure the indices remain firmly in place even in cases of shocks. After tests and final inspections, the finished dials are ready for final assembly at the brand’s Acacias facility in Geneva.
This was brought to you in partnership with Rolex authorised retailer The Hour Glass. For more, visit Thehourglass.com.
Back to top.