Explained: The Rolex Parachrom Hairspring
The relevance of alloy hairsprings in a silicon world.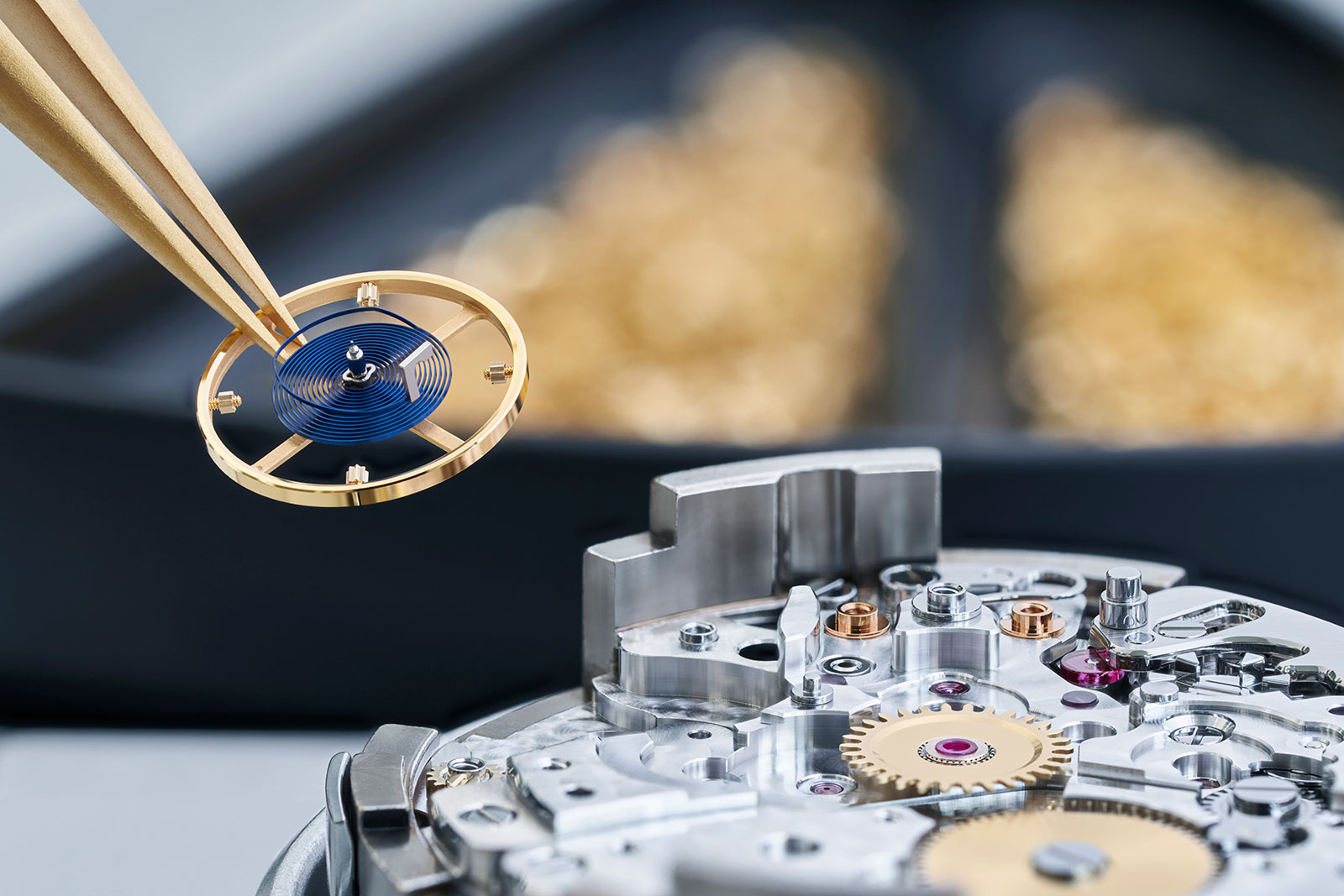
Over the last decade, metal alloy hairsprings seem to fallen out of favour across watchmaking, with even conservative, haute horlogerie brands like Breguet and Patek Philippe turning to silicon balance springs. Not to mention large-scale makers of sporty watches like Omega and Tudor, which already transitioned to silicon balance springs.
Rolex, however, stands out. The Geneva marque continues to employ a hairspring fabricated of its proprietary blue alloy – the Parachrom hairspring.
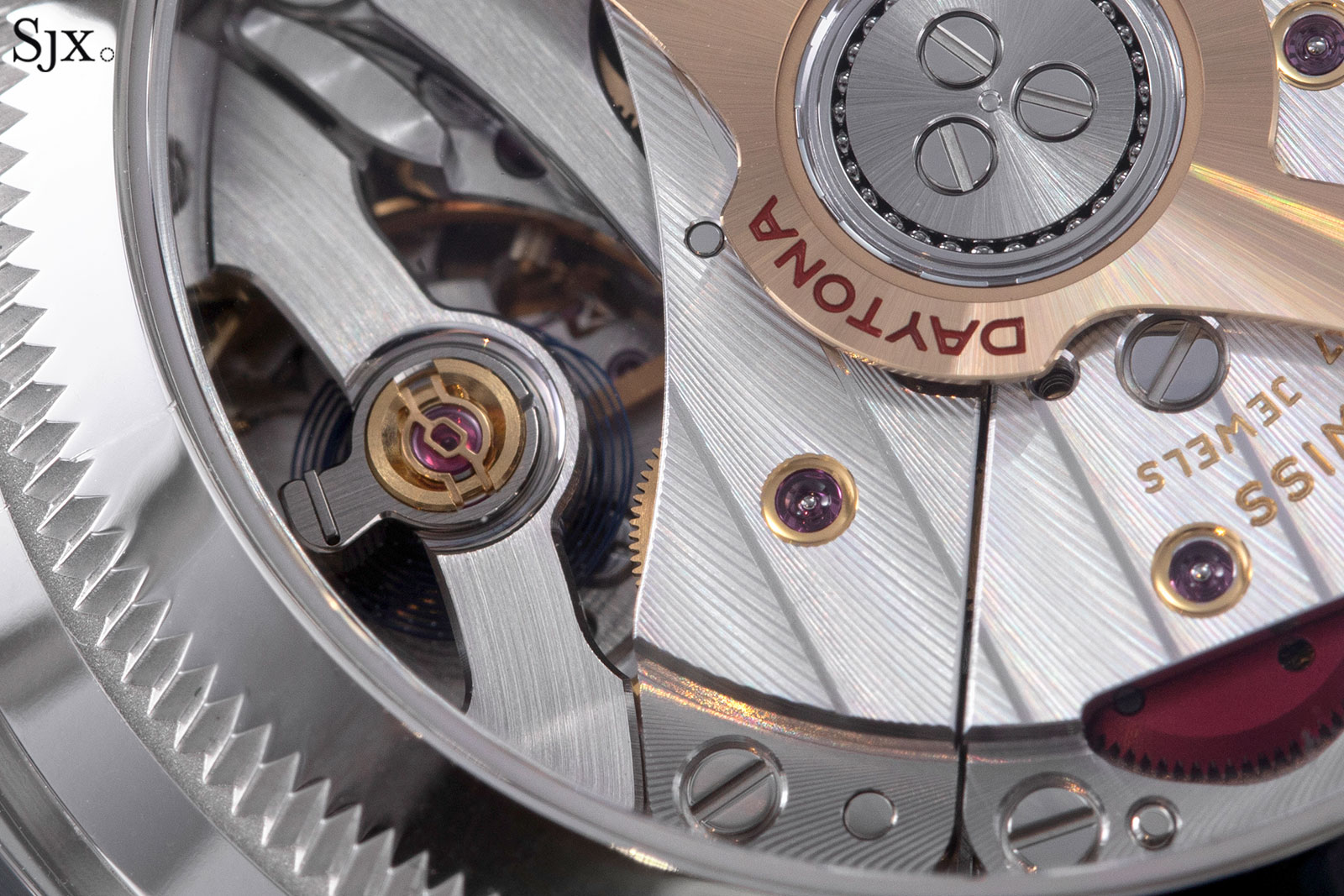
The Parachrom hairspring inside the cal. 4131 of the Cosmograph Daytona
The advantages of alloy
The use of blue Parachrom is rooted in the simple fact that the right metal alloy boasts performance that is at least on par with its silicon counterpart – while offering some distinct advantages missing in silicon.
Alloy hairsprings are traditionally made of Nivarox (and its family of related alloys), a special alloy that neither oxidises nor change its dimensions with variations in temperature. Invented in 1933 and almost a century old, Nivarox is a mix of nickel and iron, making it a ferromagnetic alloy, thus susceptible to influence from magnetic fields.
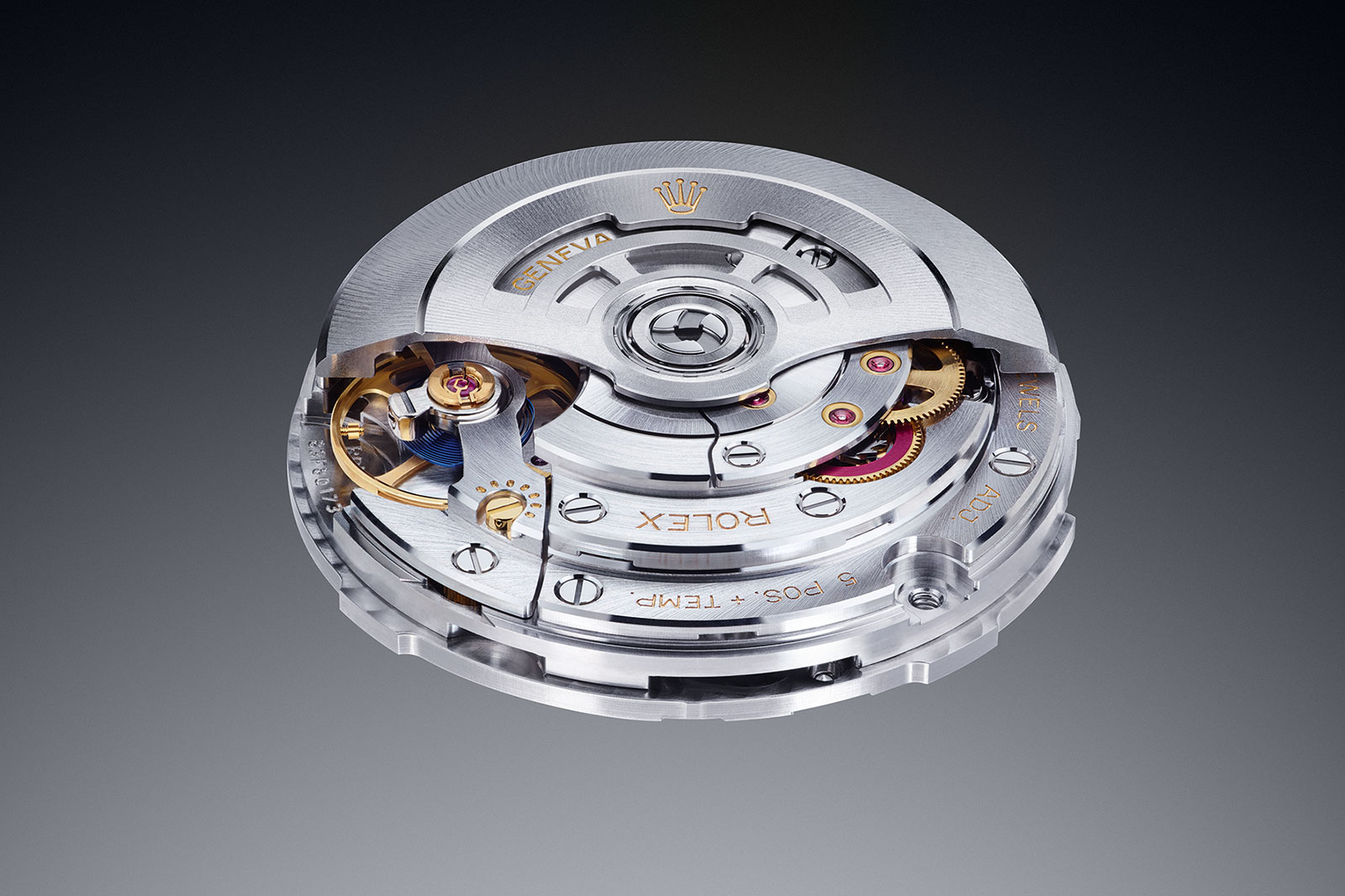
The cal. 3255 of the Day-Date 40 is equipped with a Parachrom hairspring. Image – Rolex
In order to make its hairsprings more resistant to magnetism and to bypass the Swatch-imposed monopoly on Nivarox hairsprings (Nivarox-FAR being one of the key companies of Swatch Group), Rolex set out to develop its own hairspring alloy in the early 2000s.
This resulted in Parachrom, a patented alloy of niobium and zirconium (Nb-Zr), with traces of titanium, vanadium and tantalum, that boasts excellent paramagnetic properties. Formulating a hairspring alloy from the ground up posed its own unexpected challenges, like an increased “shift” in the hairspring frequency as well as the need for innovative heat treatment.
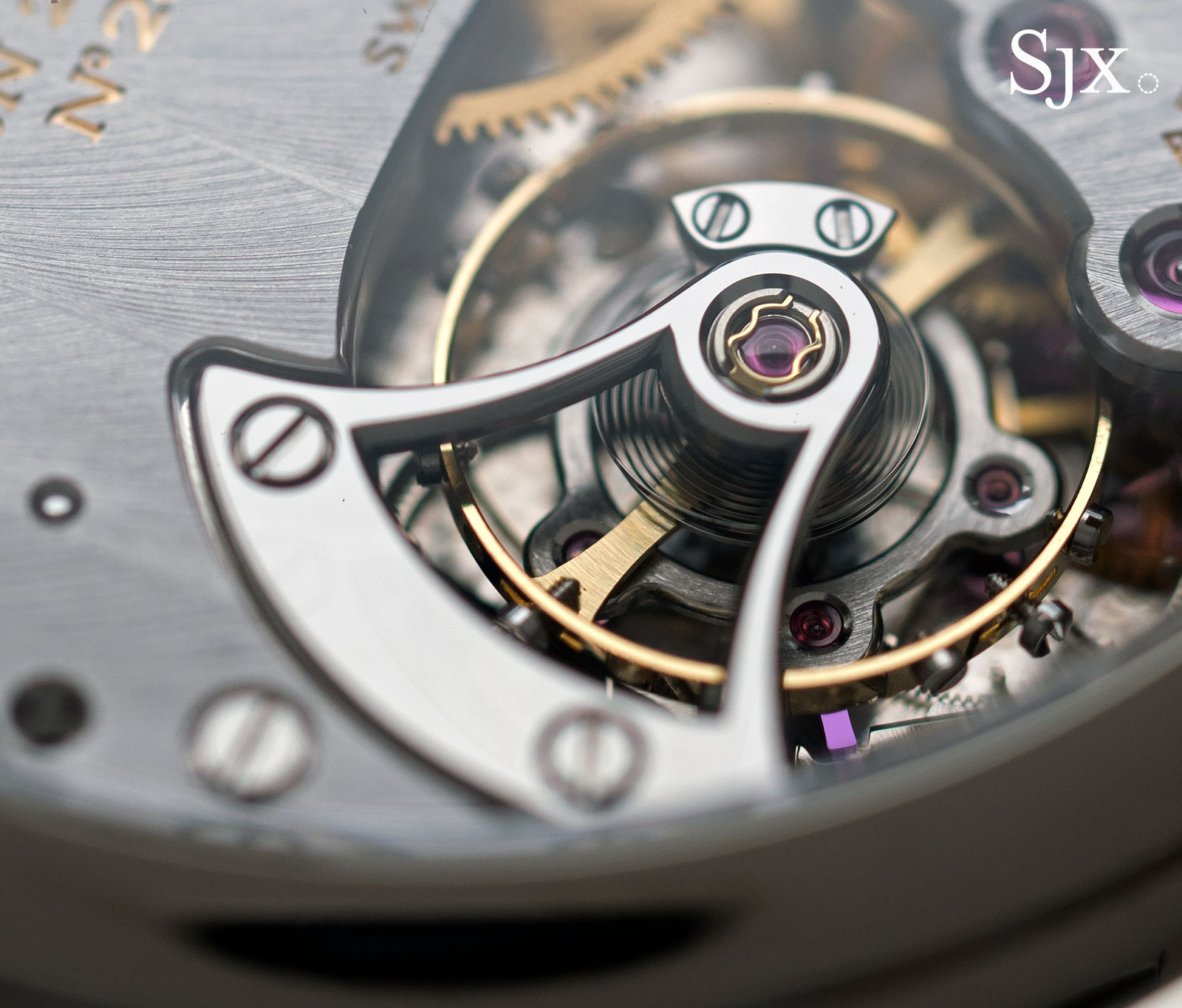
A classic Nivarox hairspring produced by Precision Engineering found in the Laurent Ferrier Galet Micro Rotor
Frequency shift
Well known to watchmakers is the phenomenon known as frequency shift. Over time, metal hairsprings shift their natural frequencies due to slow, gradual changes at a molecular level. The shift of an untreated ferromagnetic hairspring can result in a 10-second daily variation after just one year.
This is caused in part by the manufacturing process, like rolling and coiling, all of which cause a permanent plastic deformation, leaving the molecular structure of the alloy if ever so slightly disturbed. Molecules are “dislodged” during the processes, then tend to slowly diffuse and return to their equilibrium position over time, which results in changes to the Young’s modulus of the spiral, or simply put, its elasticity and flexibility. This causes the shift in the frequency of the spring.
The solution takes the form of heat treatments for rolled hairsprings, which basically speeds up the diffusion of the “dislodged” molecules and “locks” the particles in place. Such treatments can drastically lower frequency shift to under a second’s deviation after one year.
During the development of Parachrom (Nb-Zr), the frequency shift phenomenon was discovered to be even more accentuated compared to conventional hairspring alloy. Moreover, conventional heat treatments proved largely ineffective in solving the problem. The shift rate of an untreated Nb-Zr hairsprings is plotted in Fig I, which is adapted from US patent US6503341B2 filed by Rolex in 2001.
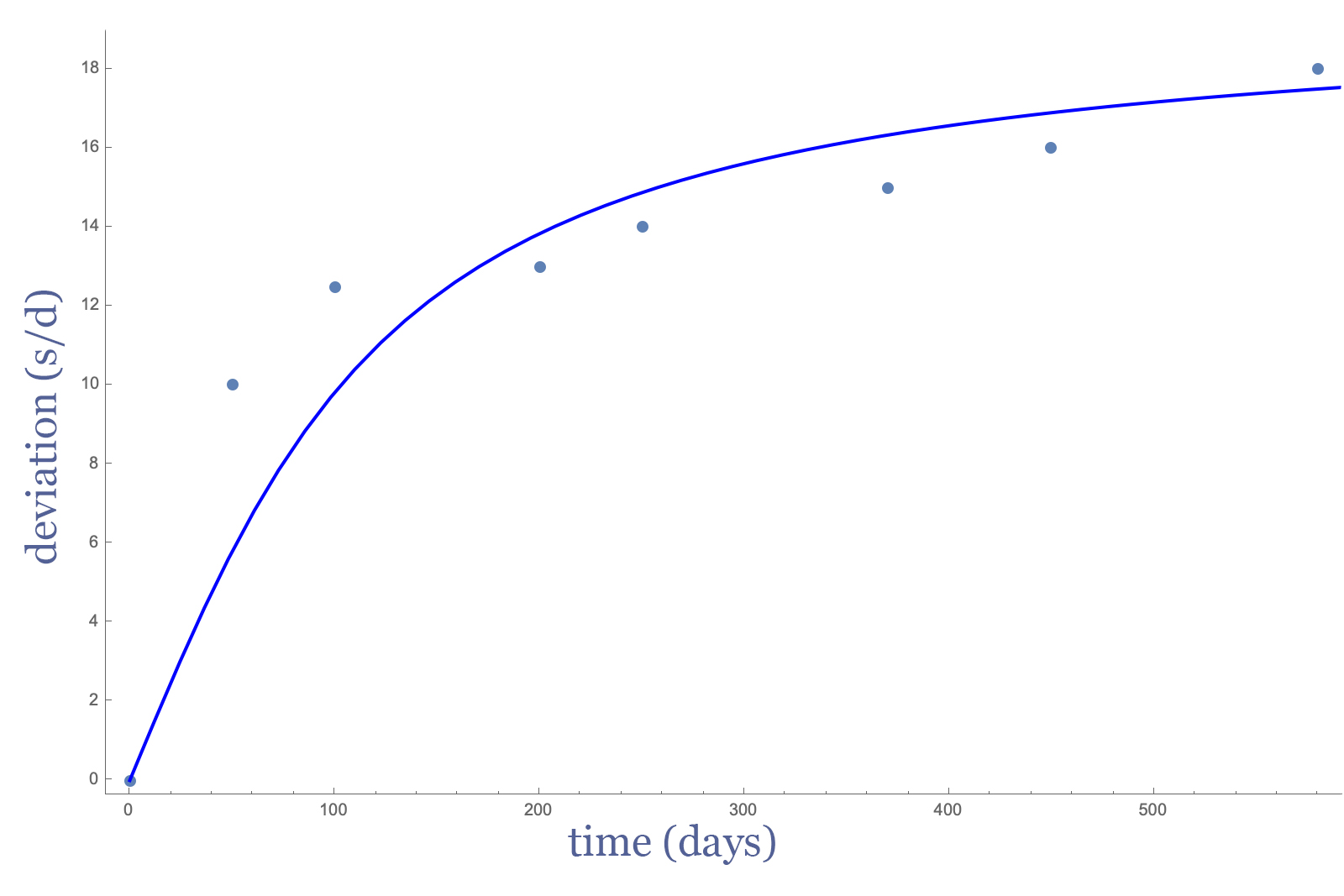
Fig. I – Frequency shift rate for untreated Nb-Zr hairsprings. Source – Patent US6503341B2
Alternative treatments
Rolex engineers surmised that molecular defects alone could not have been responsible for the high rate of frequency shift, and deduced there was another factor at play, namely oxidisation. Nivarox alloys are intrinsically resistant to oxidisation in normal conditions of room temperature and ambient air interaction, and the oxygen in the atmosphere does not bind to the metal.
Nb-Zr alloys, however, are susceptible to developing a thin oxide film over their surface over time, which binds to the alloy. The layer itself is minuscule (a few nanometers at most) but it forms inconsistently and changes over time, resulting in variations in the spring’s restoring torque, thus altering its frequency.
The solution for this unexpected issue render Parachrom hairsprings unique in the industry. In order to prevent the metal from oxidising, the raw hairsprings are coated with a protective layer through an anodising process.
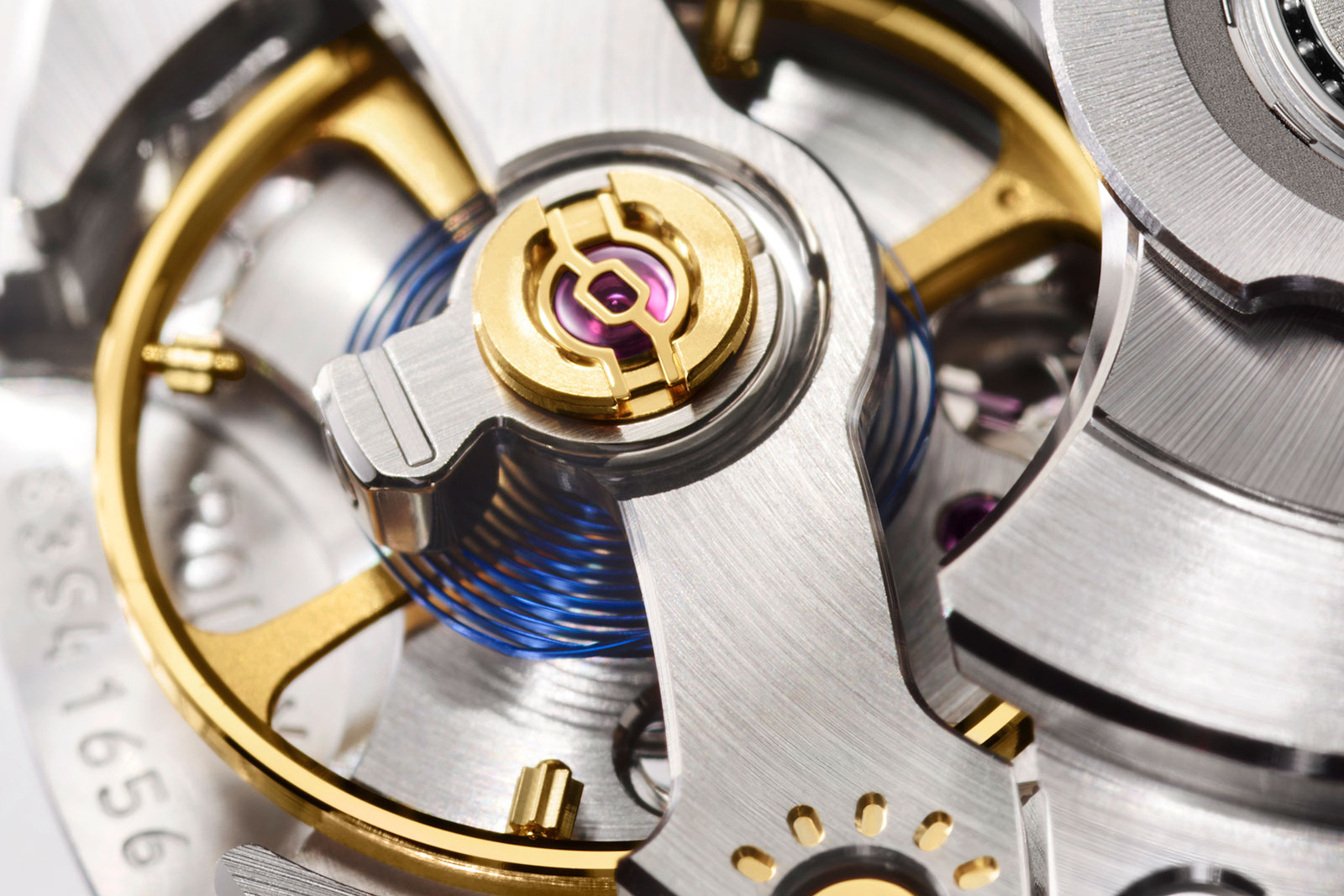
The Parachrom hairspring in a cal. 3230. Image – Rolex
Anodising is a classic electrolytic passivation process used for coating certain metals with a regular oxide layer. In doing so, it guarantees that the metal will not corrode or further oxidise on its own, as the coating forcibly binds oxygen to the metal. During the electrolysis-like process the oxide layer’s thickness can be finely tuned to very precise tolerances. The metal mostly associated with anodising treatments is aluminium. For example, aluminium watch bezels are anodised in order to make them more wear and corrosion resistant.
Rolex discovered the anodising process was perfectly suited to its very specific need: the forced oxide layer on Parachrom is uniform, with the layer’s thickness easily adjusted. The oxide layer has a set thickness of approximatively 50 nanometers.
Moreover, the layer doesn’t interfere with the alloy’s molecular structure and is perfectly reproducible over large batches, making it advantageous for mass production. However, this additional step of coating is not required for ferromagnetic alloy springs (like those in Nivarox), which adds to the cost and complexity of the Parachrom hairspring.

The cal. 4131 found in the current generation Cosmograph Daytona features a Parachrom hairspring. Image – Rolex
Anodising gives Parachrom hairsprings their trademark blue hue, explaining why the material was originally referred to as “Parachrom bleu”. The colour can actually be varied by changing the voltage during the electrolytic process. Early Parachrom hairspring prototypes had greenish hues, before the process was ultimately perfected.
After the anodising process, the hairsprings also pass through an oven for heat treatment at about 200°C, which takes care of the basic molecular imbalance. The end result can be observed in Fig. II, which shows the daily variation of the treated hairsprings caused by residual frequency shift over time. The results ignore position or escapement-induced deviations, and only consider the natural frequency shift phenomenon.
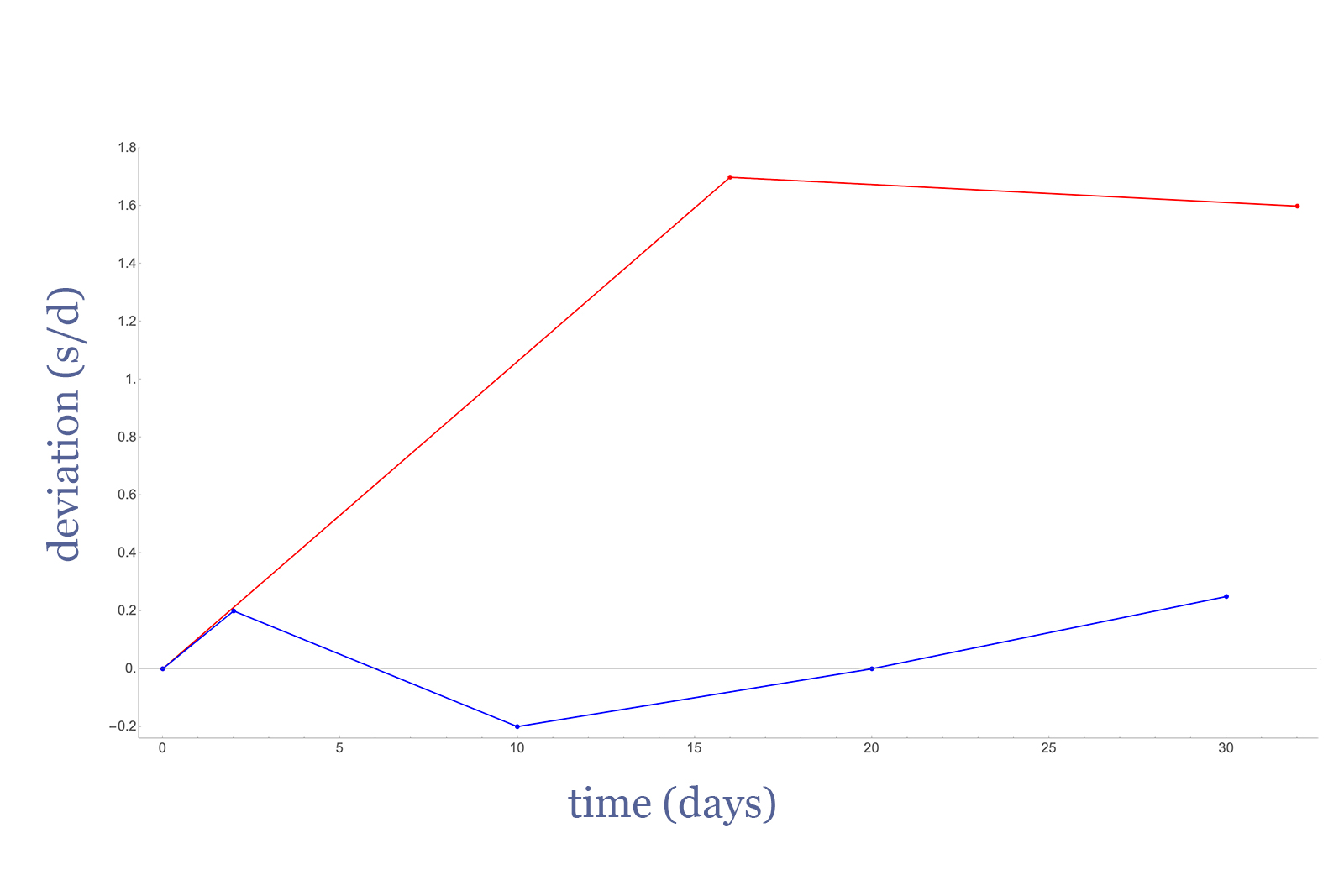
Fig. II – Frequency shift for a fully treated Parachrom spring and a heat-treated-only Nb-Zr spring. Source – Patent US6503341B2
The graph shows two plots: the blue line represents an anodised and heat-treated hairspring, while the red line represents the shift for a hairspring that is only heat-treated and without anodisation. For a fully treated hairspring (namely anodised and heated) the shift is very close to nil and in fact, the result implies the hairspring is self-compensating. Comparatively, the spring that is only heat-treated still exhibits a noticeable shift after just a month.
Ironically, the high-tech nature of Parachrom has an uncanny historical parallel: the colour of Parachrom hairsprings is reminiscent of the traditional heat-blued hairsprings found in high-grade chronometer watches of the 19th and 20th centuries that were a discreet mark of quality, just as the proprietary alloy is today.
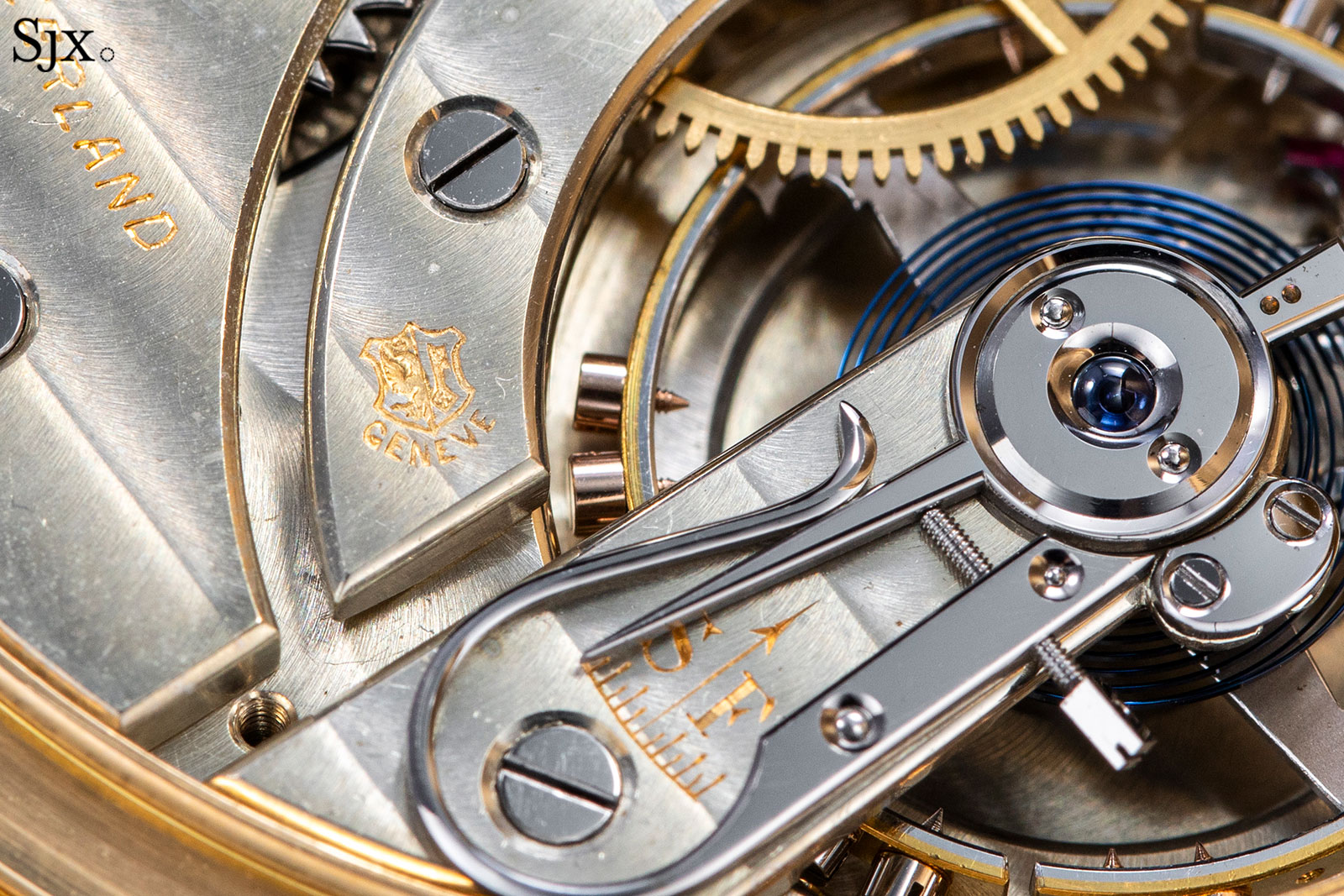
A 1920s Patek Philippe observatory chronometer pocket watch with a heat-blued hairspring
The silicon comparison
From its inception, Parachrom was meant to diminish a movement’s susceptibility to magnetic influence. The niobium-zirconium alloy is indeed highly resistant to magnetic fields, but it is not quite as impervious as silicon, which is akin to glass.
Silicon hairsprings possesses several other advantages, including being easier to manufacture, allowing them to be conveniently shaped into inherently isochronous geometries. So why does Rolex still rely on the costly Parachrom alloy hairspring, when it could comfortably pivot to silicon hairsprings across its stable of movements?
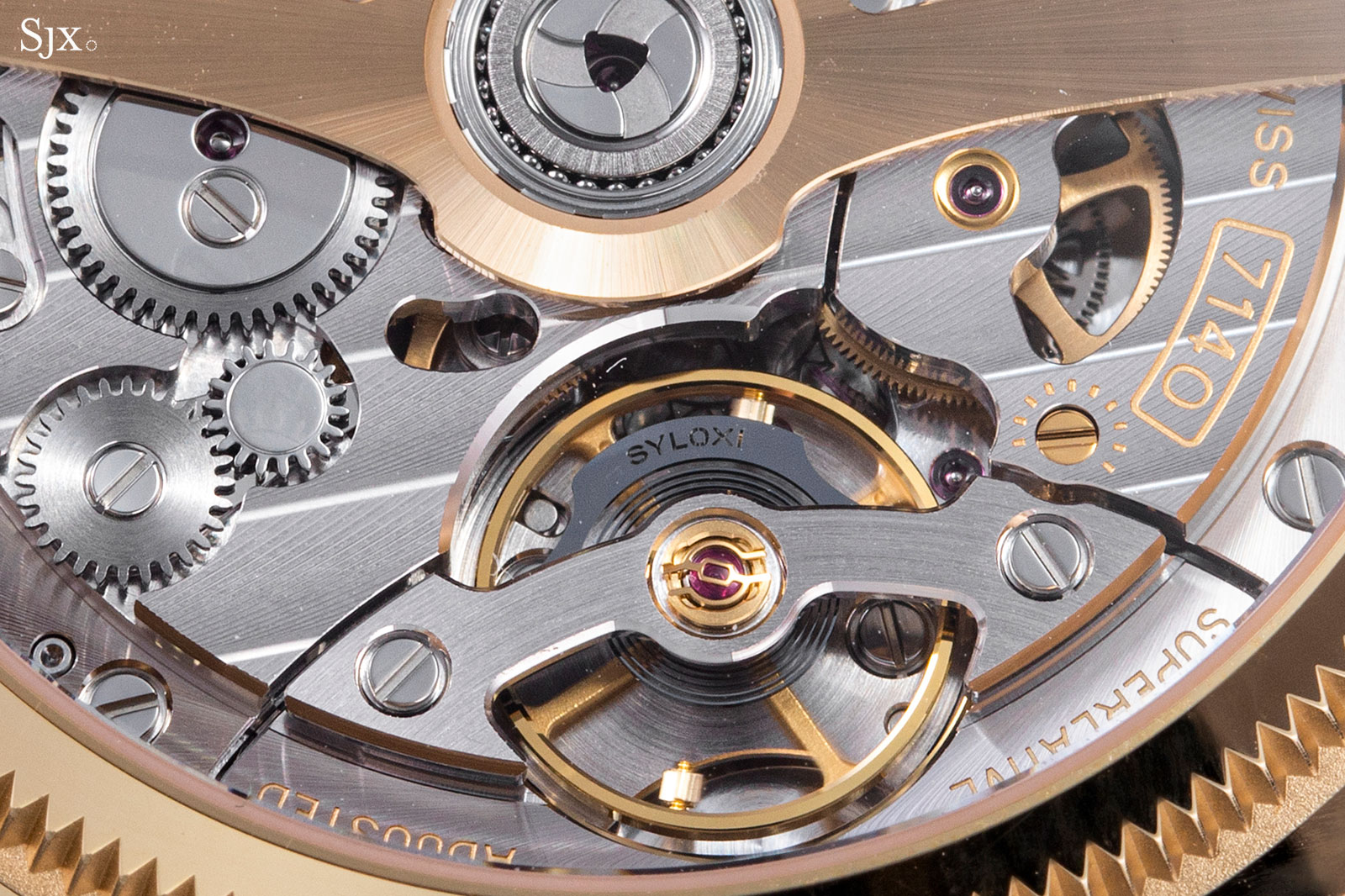
The Rolex Syloxi silicon hairspring in cal. 7140 of the Perpetual 1908
The answer arguably lies in robustness and timelessness.
A silicon hairspring is more prone to breaking when subjected to strong shocks, which is unsurprising given the brittle nature of the material. In fact, a silicon hairspring can be snapped in two by pulling it apart vertically, which can happen with a careless watchmaker.
Once broken, a silicon hairspring requires replacing as silicon cannot be mended. With the large-scale production of perfectly-formed silicon hairsprings, replacement is not a problem today, but who can tell if this availability will continue into the distant future?
In contrast, an alloy hairspring would just bend slightly on impact, which can be easily undone by a skilled watchmaker. Even a badly deformed alloy hairspring can be fixed, albeit by a much, much more skilled watchmaker, and at considerable time and expense.
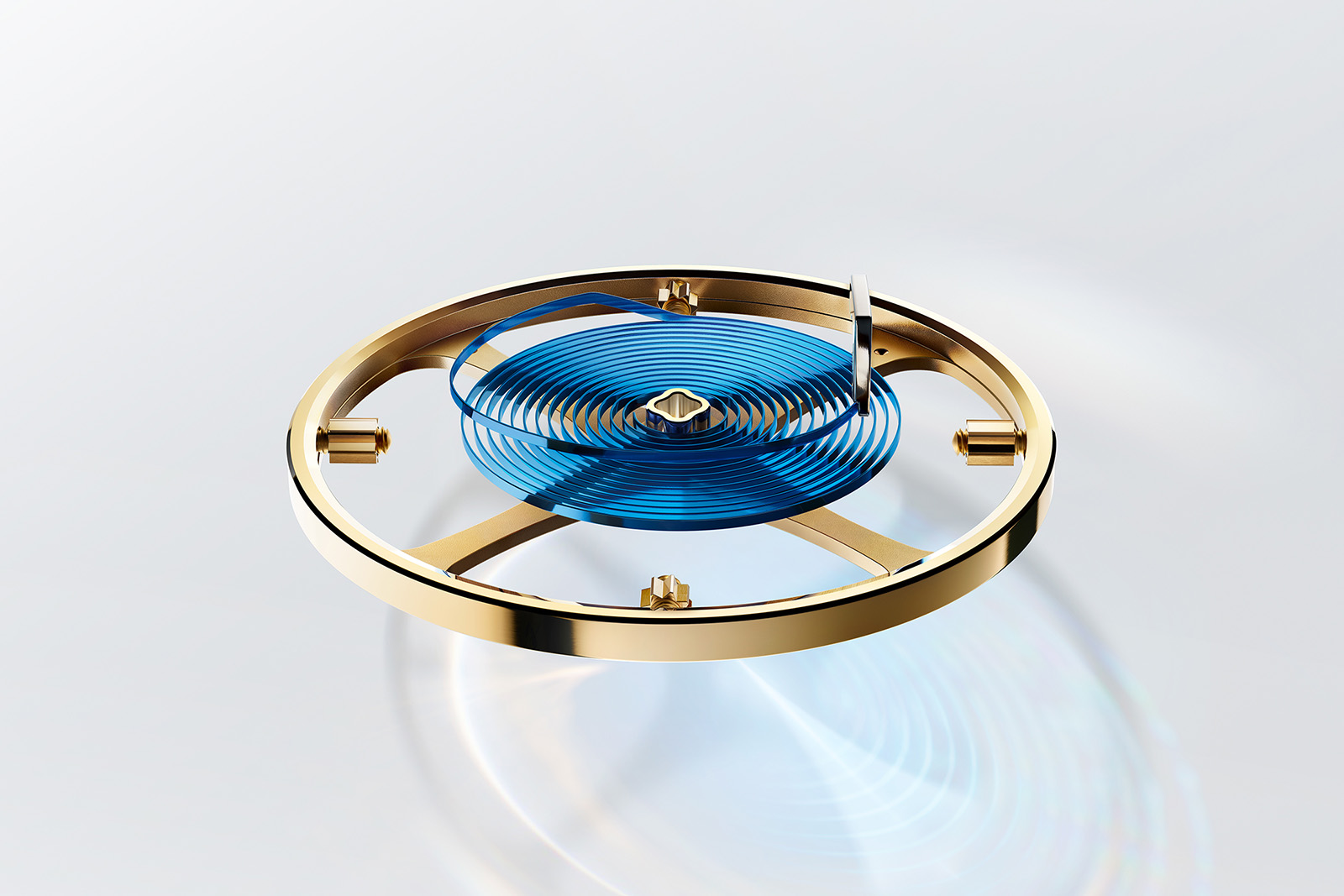
A Parachrom hairspring fitted to a variable inertia balance with Microstella regulating weights. Image – Rolex
Equally, Rolex appears philosophically inclined towards classical watchmaking. If anything, the brand has gone further in this direction in recent years, as exemplified by guilloche dials and display backs for decorated movements. With its blue sheen and Breguet overcoil, the Parachrom hairspring evokes traditional chronometers and hints at a bygone era of precision timekeeping, which complements the Rolex philosophy.
Unique in watchmaking and expensive to develop, Parachrom is also a safe bet, especially compared with alternatives that might prove problematic on the long run – this chimes with the generally conservative and prudent approach of Rolex.
To date, Parachrom has proven its worth, being undoubtedly essential to the impressively tight -2/+2 seconds daily variation dictated by the Rolex Superlative Chronometer certification that’s now standard across the Rolex catalogue. Parachrom has shown itself to perform at least as well as silicon, and perhaps better in some respects, which should assure its position in Rolex movements for a long time to come.
Back to top.