In-Depth: The Rolex Chronergy System
The final frontier of mechanical efficiency.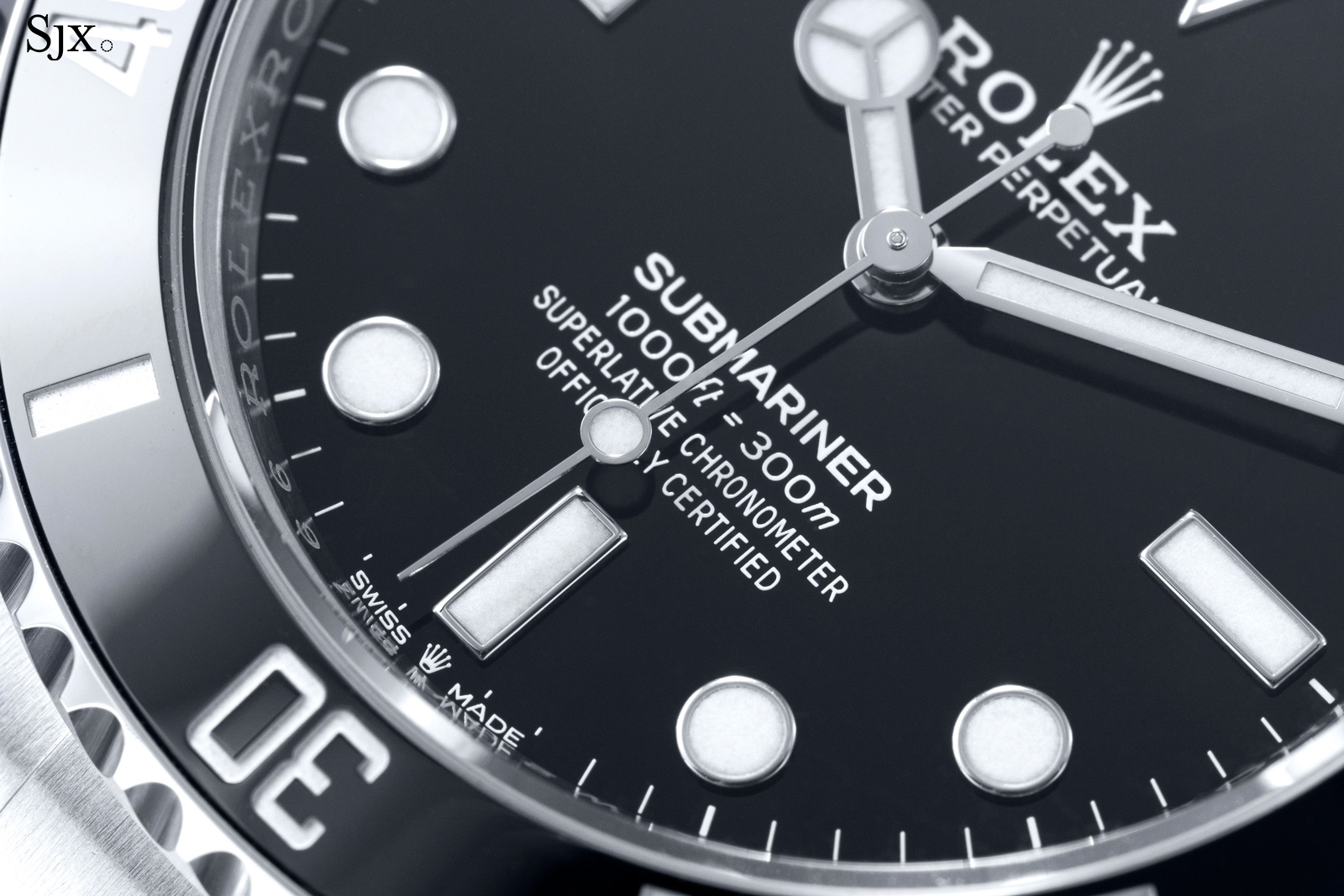
Rolex launched Chronergy – essentially a mechanical ecosystem for optimal mechanical performance – with the cal. 3255 in the top-of-the-line Day-Date 40 that made its debut in 2015.
Six years on, Rolex has upgraded practically its entire line up with latest-generation, Chronergy-equipped cal. 32XX family, including its most affordable offerings. Chronergy movements are found in the Datejust (cal. 3235) and Oyster Perpetual (cal. 3230), and also the entry-level sports watches, like last year’s Submariner ref. 124060 (cal. 3230).
Chronergy is made up of 14 patents covering every aspect of a movement from power source to regulator, but a fundamental element is its escapement. And the Chronergy escapement actually continues a long-forgotten journey that began some fifty years ago on the other side of the world.
Still sound at 300 years old
Invented in the mid 1750s by Thomas Mudge (1715-1794), the lever escapement was arguably the necessary iteration of the deadbeat escapement once it was miniaturised for a watch. Having been conceived by George Graham (1673-1751) as a refinement of the anchor escapement in pendulum clocks, the deadbeat escapement was unsuited to the delicacy of watch proportions.
In the lever escapement, impulse is provided to the balance via a lever, which is in turn propelled by the force of the escape wheel teeth contacting the pallet jewels of the lever. And the lever escapement is a detached escapement, meaning the escape wheel locks free of the balance after energy has been delivered through the impulse jewel, leaving the balance free during all of its supplementary arc of travel.
The straight-line layout of the lever escapement that persists today – the balance wheel, lever, and escape wheel are laid out linearly – is actually several centuries old, dating to 1786 with a construction attributable to Jean Moïse Pouzait (1743-1793).
Shaped like a club foot, the escape-wheel teeth as we know it now seems to have surfaced in approximately 1860, quickly became the de facto geometry. Subsequently, it became practically blasphemous for makers to deviate from the prescribed geometry laid out in the industry bibles of the time, like Claudius Saunier’s Treatise on Modern Horology in Theory and Practice (1887) or Théorie général de l’horlogerie (1950) by Leopold Defossez.
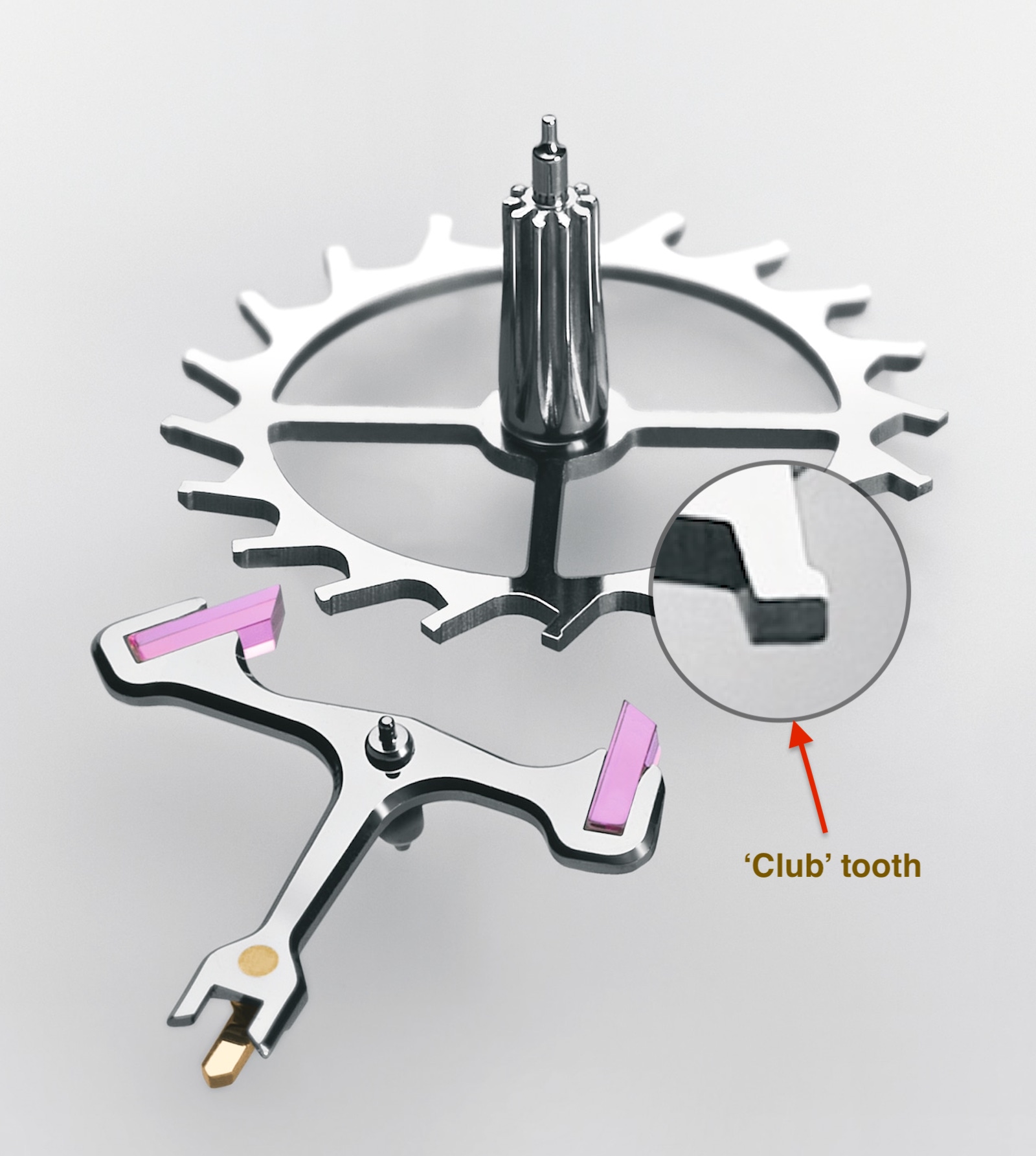
A conventional Rolex escapement with wide pallets and thin ‘club foot’ teeth. Image – Rolex
The lever escapement has proven to be robust, reliable, as well as easy to manufacture at scale, resulting in it becoming the dominant escapement for wrist- and pocket watches. However, the lever escapement is far from perfect, especially with the effects of frictional changes at its pallets, leading to many attempts at improved or novel escapements over the centuries.
In the last couple of decades there has been experimentation with new materials such as diamond-like coatings and silicon carbide to mitigate the changes in friction over time, but there has been little fundamental development, specifically in optimising the geometry of the escapement parts. The famous co-axial escapement invented by George Daniels (1926-2011) is the only new escapement to achieve series production. However, it has been mass produced by only one brand, Omega.
While the diversity of new escapement designs are welcome developments, what was crucial was a revisiting of the basics, particularly since technology has become a genuine aid in technical development. Modern mechanical dynamic modelling, computer-powered analytical techniques, and high frame rate photography allow insight and optimisation previously impossible.
The purpose of escapement development has also evolved from the days of Graham and Pouzait. In a world where an average daily rate of within five seconds is now consistently achieved on an industrial scale by brands like Omega, and slightly better at Rolex, escapement development is less about timekeeping and more about extending power reserve.
We have discussed the trade-offs in movement design, showing that given a fixed amount of energy, balance power and power reserve vary inversely to one another. The easy solution to extend the running time would be to just back off on the balance wheel power, but at the expense of potentially compromising timekeeping ability. The alternative is to improve the efficiency of energy transmission, which starts with the escapement.
The first steps in adjusting geometry
It was perhaps only during the hotly-contested observatory trials of the mid to late 1960s that designers began to question and tweak the geometry of the lever escapement. As beat frequencies began to rise in the pursuit of greater balance wheel inertia, it was found that the efficiency of energy transmission in the escapement declined.
Specifically, it was discovered that when movements were made to run above the widely-accepted standard for balance-wheel frequency, namely 18,000-21,600 beats per hour (bph), and increased to what was typically known as “high beat”, or 28,800-36,000 bph, the transmission efficiency of the conventional club-tooth escape wheel dropped from approximately 40% to 30%. The result was a reduction in balance wheel amplitude – an undesirable outcome for stable timekeeping.
Several solutions were mooted: either the mainspring torque could be increased to maintain amplitude, the lower amplitude could be accepted, or the balance inertia could be reduced.
None of these were desirable for their own reasons. Higher mainspring forces increase wear in the going train, while amplitude losses increase the positional timekeeping errors. On the other hand, reducing the balance inertia to achieve good amplitude while having a less efficient power supply would mean a reduction in balance power as well as power reserve, given a fixed mainspring size.
The first published work I could find that examined the issue holistically from the ground up – specifically the ideal geometry based on higher frequencies and the effect of friction – was conducted by an engineer at a watchmaker that was then an industry outsider, or even upstart. It was Kenji Abe of Suwa Seikosha, one of the operating companies of Seiko, who was granted United States patent US3628327A in 1971 for a “clubtooth lever escapement”.

Challenging the established geometry.
Sometime in the late 1960s – the patent was filed in 1970 – Abe performed a first-principles, static analysis of the geometry of the contact between an escape wheel tooth and pallet, considering the effect of friction on the balance of the moments of forces created.
An oft-omitted fact when explaining the operation of the lever escapement is that after the pallet unlocks, there are two different types of impulses. The first action (impulse A) is where the locking beak of the escape tooth pushes against and along the impulse face of the pallet.
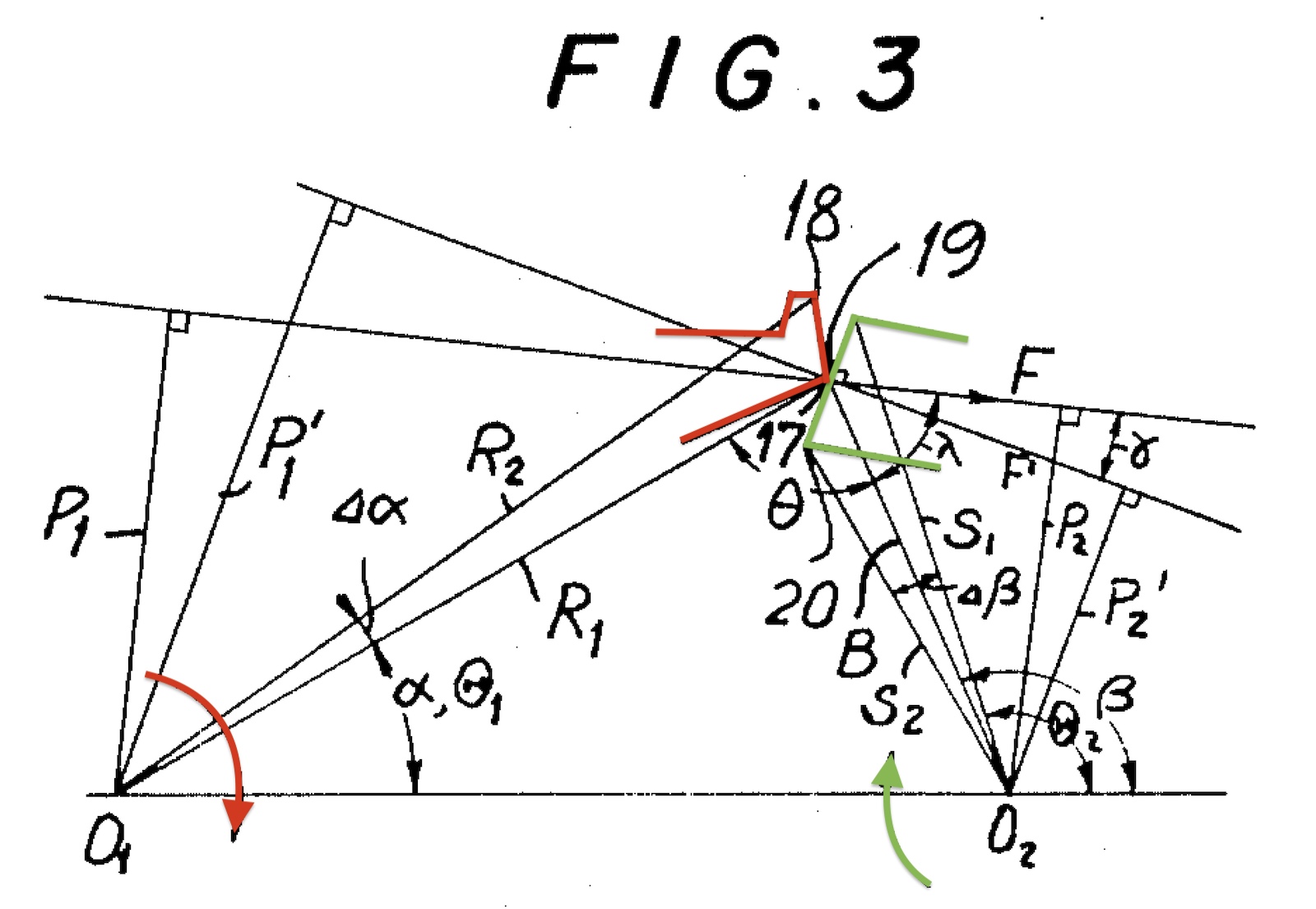
Abe’s analysis of impulse A where the escape tooth impulse beak (in red) pushes on the impulse plane of the pallet (in green)
This type of interaction continues until the locking beak reaches the end of the pallet (impulse beak). Then the impulse plane of the escape tooth pushes against the impulse beak of the pallet (impulse B).
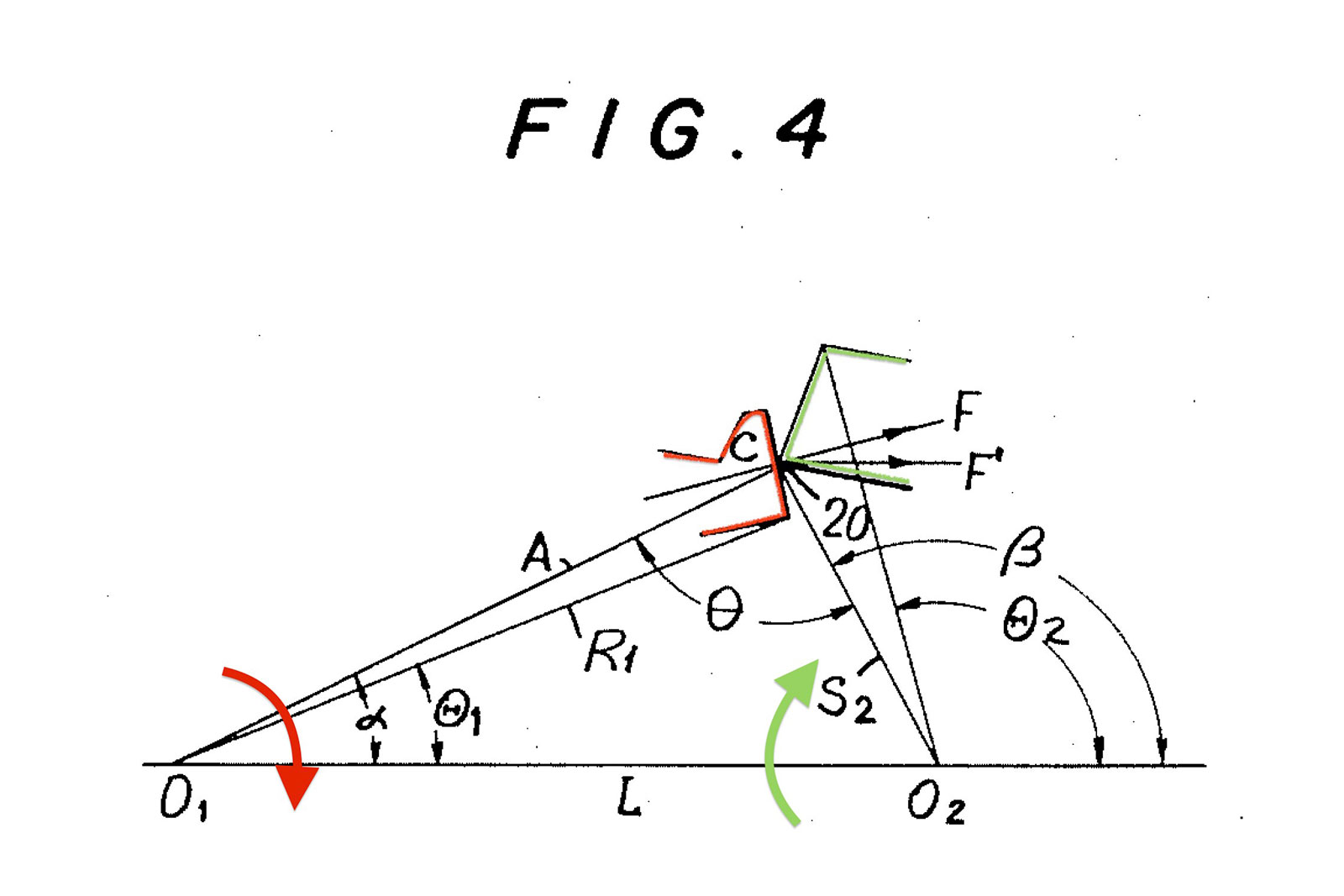
Abe’s analysis of impulse B where the escape tooth impulse plane (in red) pushes on the impulse beak of the pallet (in green).
Abe examined the cases of both types of impulse and for both entry and exit pallets. He found that the ratio of the integral (or the sum) of the moments multiplied by their angle travelled on either side of the contact for both was key.
He further discovered – and this was Abe’s most notable finding – the highest transmission efficiency would be obtained when the face length of the escape wheel tooth was either the same or up to double the length of the pallet. This compared to the more typical proportions where the escape wheel tooth was between half and four-fifths the length of the pallet. This demonstrates that a benefit is derived from longer-than-usual club feet on the teeth and shorter-than-usual pallets – entirely contrary to the horological testament of Defossez.
Abe’s findings on geometry appear never to have made it to Seiko’s serially-produced movements, while also being discovered too late for movements destined for observatory chronometer trials, which were all cancelled after 1968 when Japanese watches swept the board. Perhaps it was simply the advent of quartz technology, which meant that throwing resources at pursuing ever more accurate mechanical escapements was deemed commercially pointless.
Interestingly, despite the renaissance of mechanical watches and the more recent pursuit of accuracy, modern-day Grand Seiko Hi-Beat movements eschew Abe’s approach and instead rely on conventional geometry of the escapement, albeit with low-inertia features, namely the skeletonised escape wheel and lever produced by a lithography technique known as MEMS.
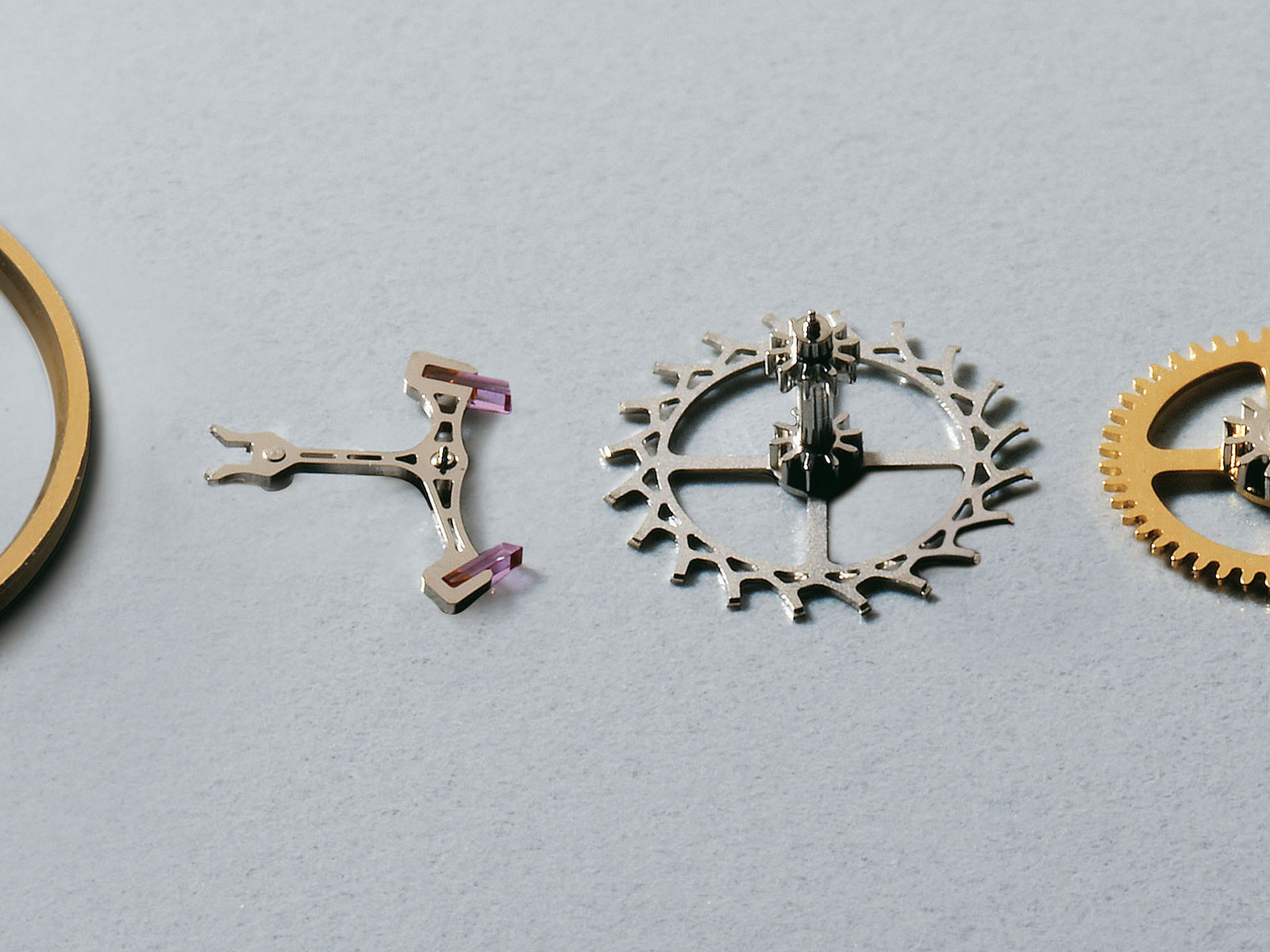
The nickel-phosphorus escapement produced via MEMS – the pallet lever (left) and escape wheel (right) – found in the Grand Seiko Hi-Beat movements, made up of parts skeletonised to minimise inertia, while also having recesses in the escape wheel teeth to retain lubricants. They are otherwise conventional in geometry, with short thin teeth and long wide pallets. Image – Grand Seiko
Escapement and more
His findings seemingly forgotten, Abe doubtlessly embarked on his research as part of Seiko’s quest to beat the Swiss at precision mechanical timekeeping. Ironically, Abe’s approach appears to have been recently rediscovered by the Swiss, reemerging in the work of Raphael Cettour-Baron and Alexandre Chiuve at Rolex.
The escapement invented by the duo has been brought to market as part of Chronergy. Citing Abe’s work, Cettour-Baron and Chiuve experimented with escapement components manufactured with modern technology, rediscovering and adapting the benefits of Abe’s research. The pair have also reaped the advantages of high-frame rate imaging and computer-supported dynamic analysis in their development of the escapement.
Though it’s been a few years now since Rolex launched Chronergy, but for multiple repetitions of the press release, I have seen only one considered review of it by a watchmaker, which was published in Horological Journal, the magazine of the British Horological Institute.
My purpose here is to describe what I believe are the significant differences in the Chronergy escapement against a conventional lever escapement. While Rolex uses long teeth and short pallets, its escapement differs from Abe’s invention with the use of two distinct impulse planes on each escape wheel tooth.
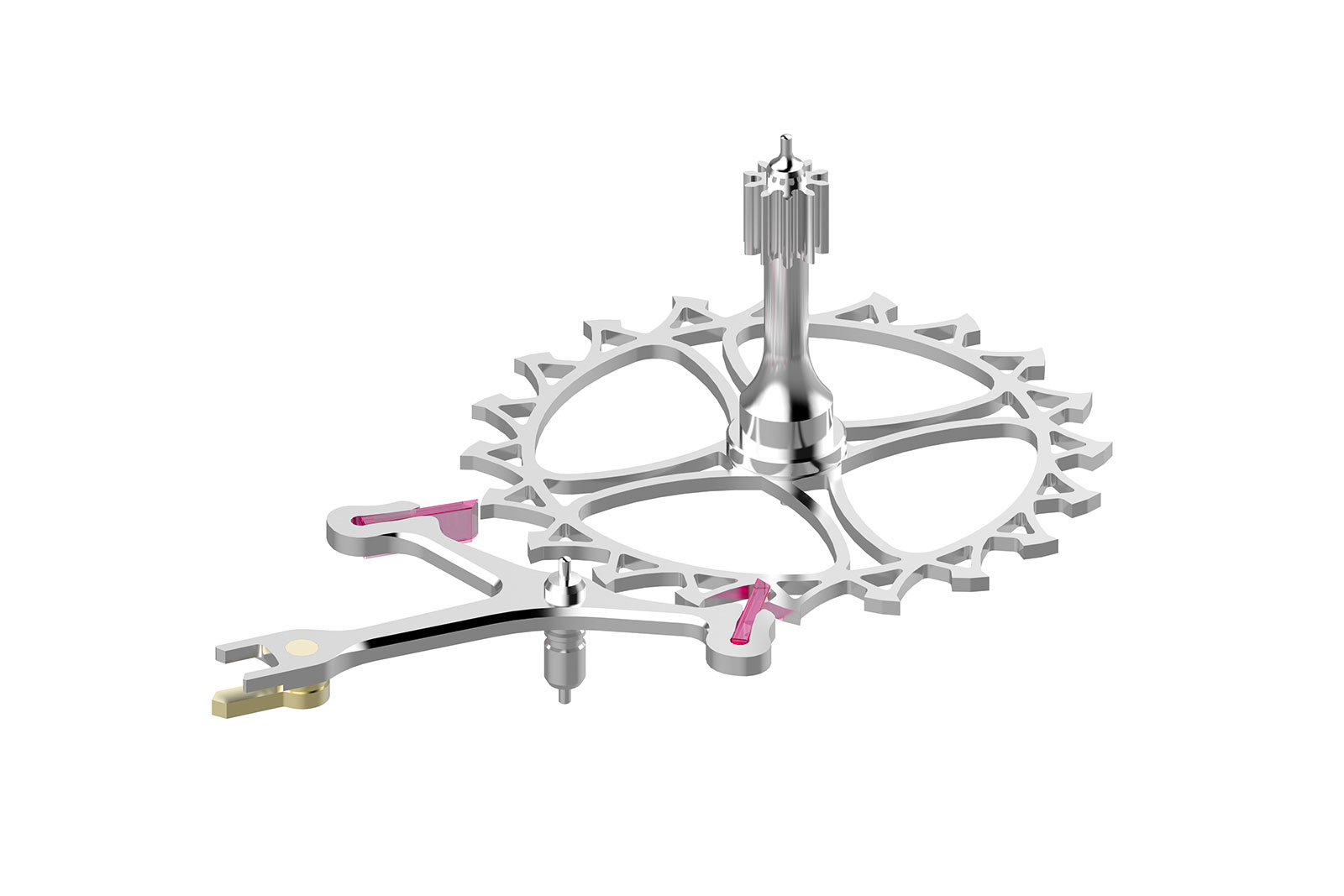
Chronergy with its thin pallets and wide teeth, with the asymmetrical lever a function of packaging and not relevant to efficiency; note that the number of teeth on the escape wheel pinion and escape wheel remain otherwise identical to the conventional variant shown at the start of this article. Image – Rolex
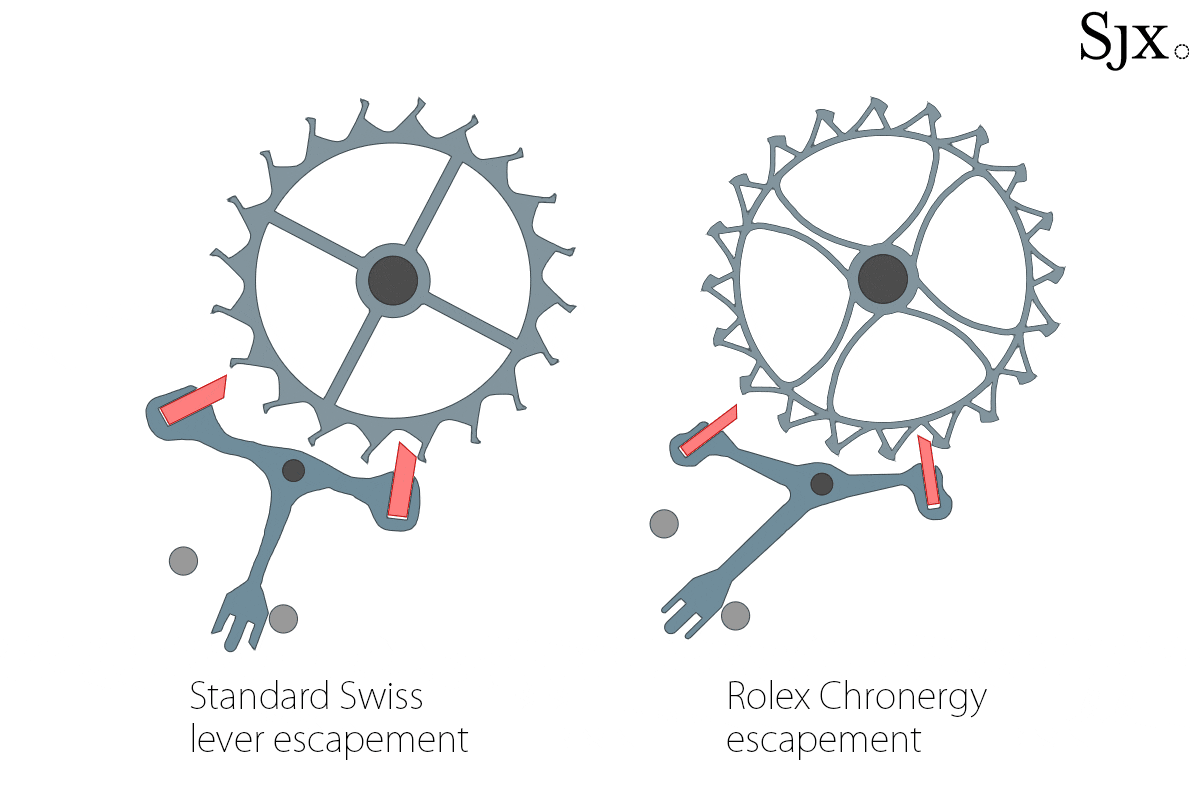
The Rolex Chronergy escapement next to a standard Swiss lever escapement – observe that the Chronergy escapement has relatively thin pallets and a wide, sloped club foot
Impulse – a change of gear
Rolex has taken Abe’s work further by including the dynamic effects of the redesigned escapement; Abe’s work was a static analysis. A key thing to consider is that the inertia of the escape wheel and lever all have a part to play when the escapement is in motion. More specifically, timekeeping benefits from an escapement with low inertia, in contrast to the balance wheel, where high inertia is desirable all things being equal.
The balance wheel has a roller jewel on its arbor, which impulses the pallet lever at the middle of its swing. This is what unlocks the escape wheel, causing motion of the geartrain to the next beat. Notably, around this point of impulse with the balance wheel at mid swing, the balance wheel is rotating at its fastest speed.
The angle through which this impulse is delivered, as measured at the balance, was historically known as the “escaping angle” or more commonly today, the “lift angle”. In his day, Mudge’s lever had a lift angle of around 80 degrees. The higher this value, the less detached the balance swing is.
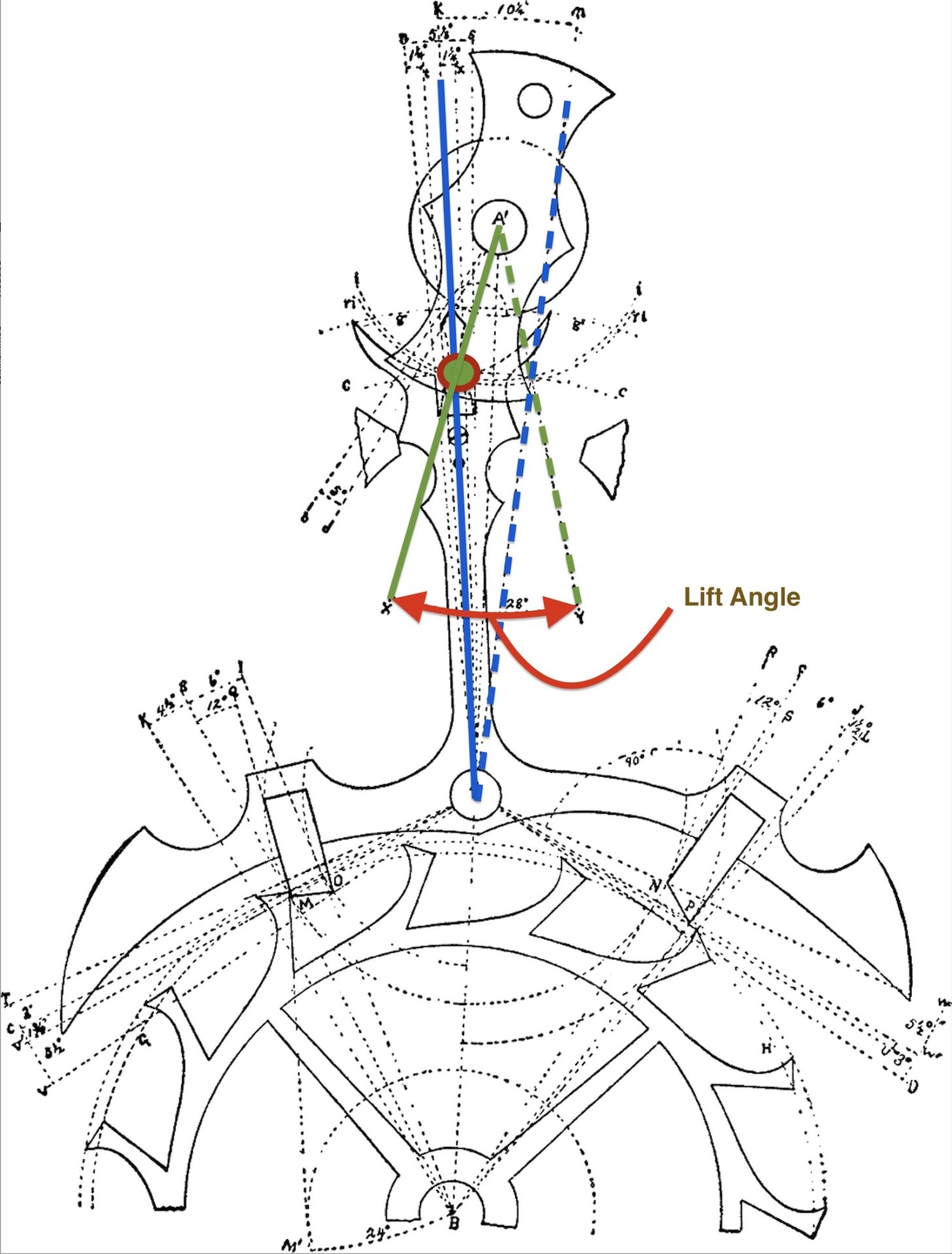
Lift angle (measured at the balance wheel) is the angular distance the roller jewel is given impulse by the pallet fork from the escape wheel. Image – H.R. Playtner with annotations by the author
It follows that the ideal value would be zero – a lower lift angle theoretically results in better isochronism, which means less variation of timekeeping as balance amplitude changes. Modern wristwatch escapements typically have a lift angle of 40-58 degrees, with many mass-produced movements having a lift angle of 52 degrees, including the majority of ETA and Rolex calibres for instance.
These values have been arrived at through gradual refinement with what can be reliably achieved in large-scale manufacturing. Achieving lower lift angles comes at the cost of higher forces being required to impart the energy needed in a smaller time window. In addition, tighter tolerances would be required throughout the design especially at the safety roller and guard pin.
One of the characteristics of the balance wheel’s oscillation (as a simple harmonic motion system) is that it is at more than 99.7% of its maximum angular velocity for the industry common 52 degrees of lift (equal to 26 degrees of balance amplitude shown in the graph as dashed orange line either side of its central rest position).
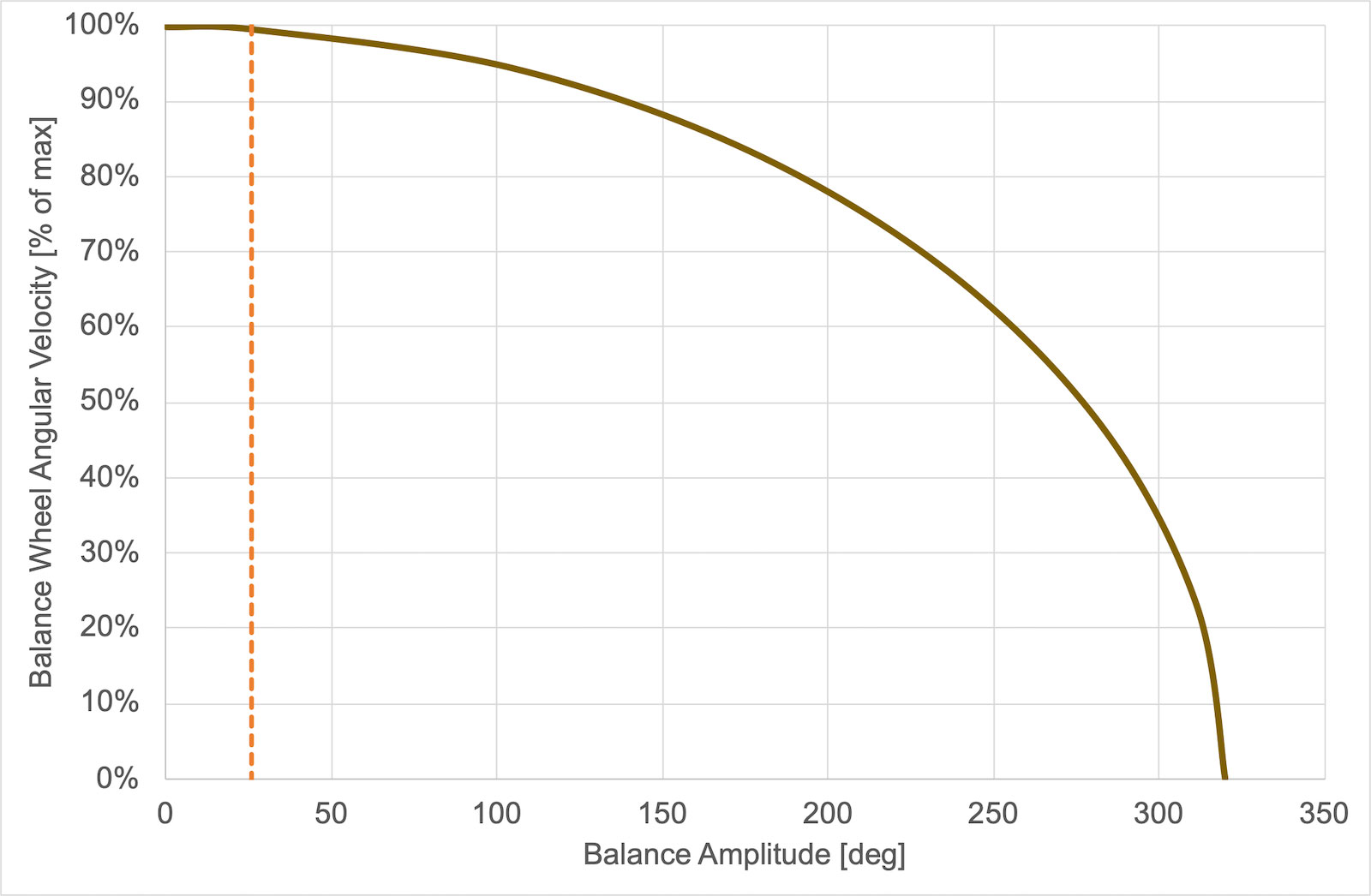
Balance wheel velocity as a function of its position from rest, with the typical lift timing of 26 degrees in orange
As the escapement becomes attached via the impulse roller action and the lever unlocks, the challenge is how to mate the power available in the stationary going train with the balance wheel, which is travelling at nearly maximum speed relative to the stationary train.
To impart any energy to the balance, the escape wheel has to be accelerated from rest and also overcome the inertia of the pallet lever, which is akin to pushing a child on a swing but only at the point when the child is nearest the ground. In this scenario, the lighter your arm, the more chance you have of successfully pushing, since a lot of energy will be spent simply trying to accelerate up to the speed needed to get the child swinging.
At the very start of this point in the escapement motion just after the lever unlocks, the impulse jewel is taking energy from the balance to help the lever accelerate. It takes some time for the going train to impart any net impulse. Thus, it is beneficial to use an escape wheel and pallet with the lowest possible inertia, so as to allow the fastest rotational acceleration of the escapement parts.
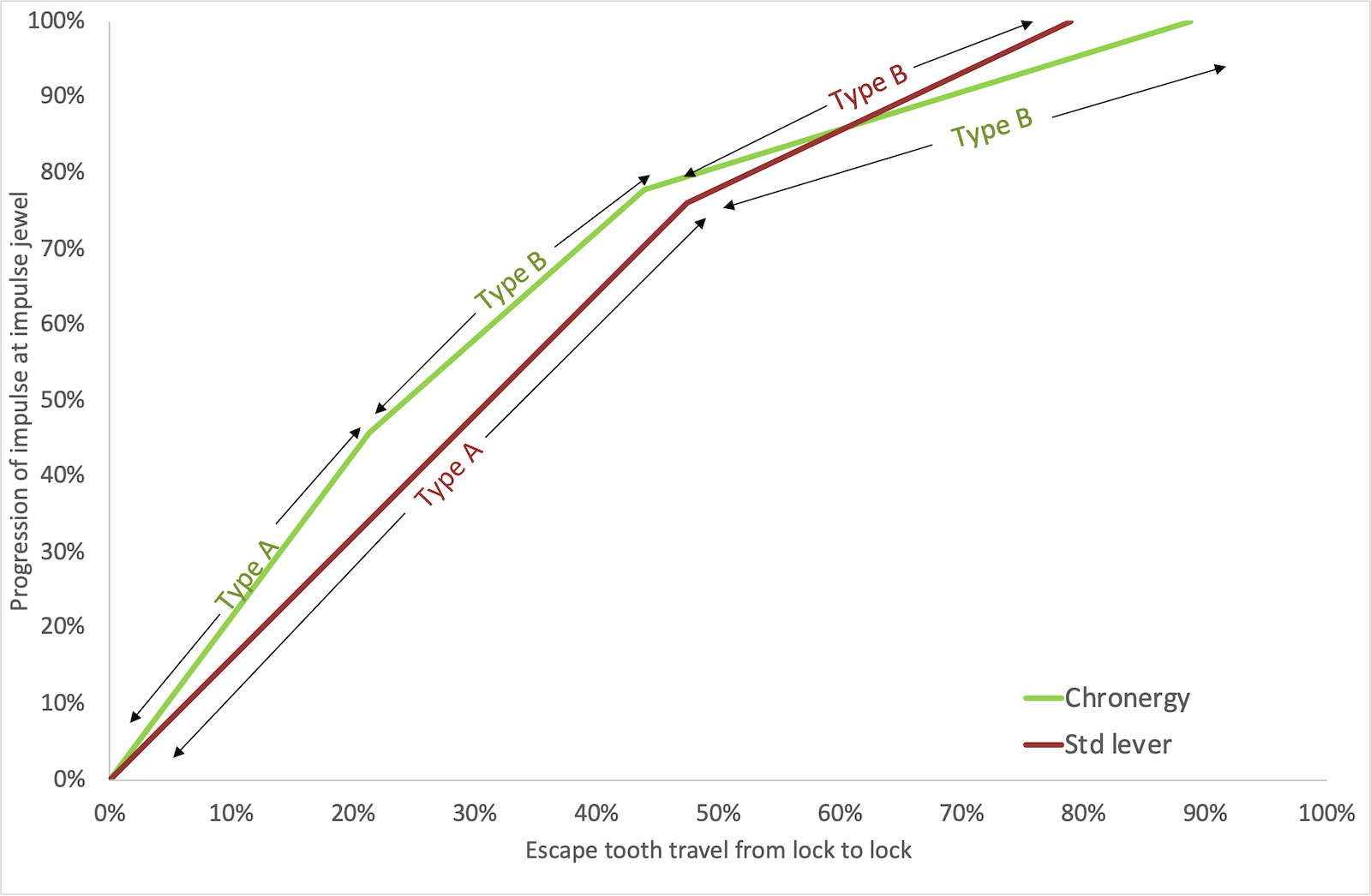
Comparing between the standard Swiss lever and Chronergy escapements in Rolex movements by charting the relationship between the travel of a single tooth of an escape wheel to the effective lift angle at the impulse jewel lever for an exit pallet
As unlocking completes, the first part of operation is the impulse beak of the tooth travelling along the impulse plane of the pallet, undergoing an impulse A. The difference with Chronergy is that the steep incline of the pallet tip provides a higher increase in lift of the lever given a small rotation of the escape wheel when compared to a conventional escapement; up to around 45% of the total lift angle is provided in the first 20% or so of escape wheel’s rotation.
Next, the pallet beak slides on the tooth as an impulse B as noted by Abe. The key here is the Chronergy tooth has two angled impulse faces of different slopes – creating something resembling a curved surface. The starting incline of this tooth in Chronergy is similar to conventional geometry, but with the second impulse plane it then differs greatly from a normal escape wheel and even the work of Abe. The second plane is angled to have lower impulse than a conventional design, but goes on longer and later than a conventional escapement.
With the escape wheel accelerating from rest, an effectively higher gearing in the first phase of lift is better able to match the balance speed. The sooner the escape wheel can get up to speed, the sooner a net impulse can be provided to the balance.
Its design is also likely to have been optimised to reduce the chaotic bouncing that occurs between impulse jewel and lever, as well as pallet and tooth. There is also reduced angular drop as the escape wheel moves to lock on the following pallet.
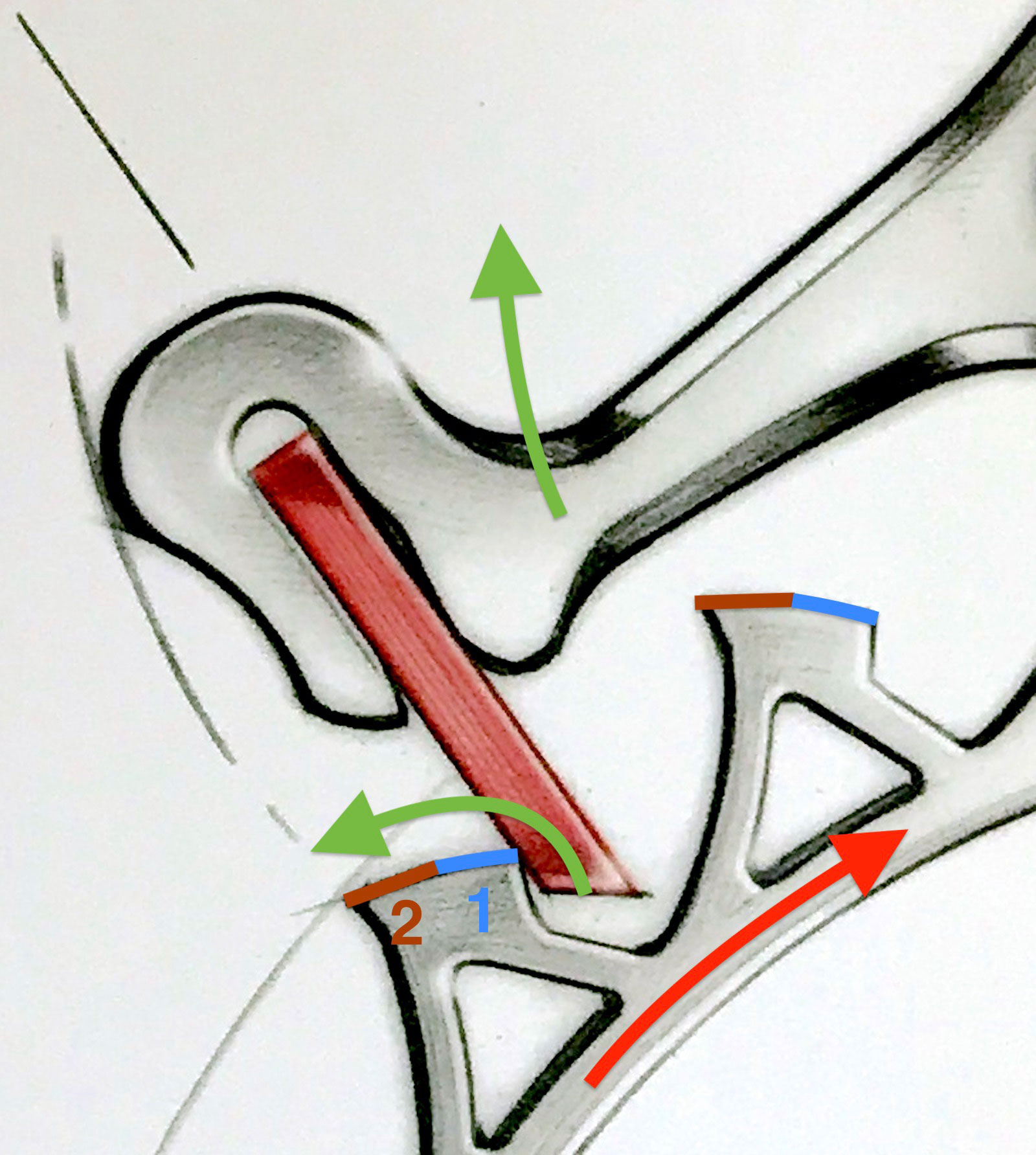
Chronergy close-up – thin pallets and two stage tooth angle of the escape wheel, with annotations by the author. Image – Rolex
We are not privy to any other changes found in the Chronergy escapement relative to Abe’s work or details surrounding its development. That might include changes in draw, clearances at the balance wheel, dynamic analyses, or high-speed photography for instance. As a matter of policy, Rolex neither divulges any detail in its announcements nor comments when asked, so we have to make do with what we have. Some details, however, can be inferred.
By its nature of long teeth and thin pallets, the Chronergy escapement spends a large amount of its lift in impulse B. Notably, this is an area of some difference of opinion.
Other escapement constructions, most famously Patek Philippe’s Pulsomax, have sought to maximise impulse A. This was achieved with escapements designed with short teeth and long pallets.
Referring to Abe’s work in their patent application, Patek Philippe state, “This approach, however, ignores the fact that during the portion of the impulse where the impulse beak of a pallet slides over the impulse face of a tooth, performance is generally not very good.”
It continues, “In the usual constructions, the performance is better during the first part of the impulse where the impulse face of the tooth slides on the impulse beak of the pallet than during the second part where the impulse beak of the pallet slides on the impulse face of the tooth.”
Despite the successful application of the Pulsomax escapement in the Ref. 5550 Advanced Research, which saw the power reserve of the cal. 240 extended from 48 to 70 hours, the technology has not achieved mass adoption across the Patek Philippe range.
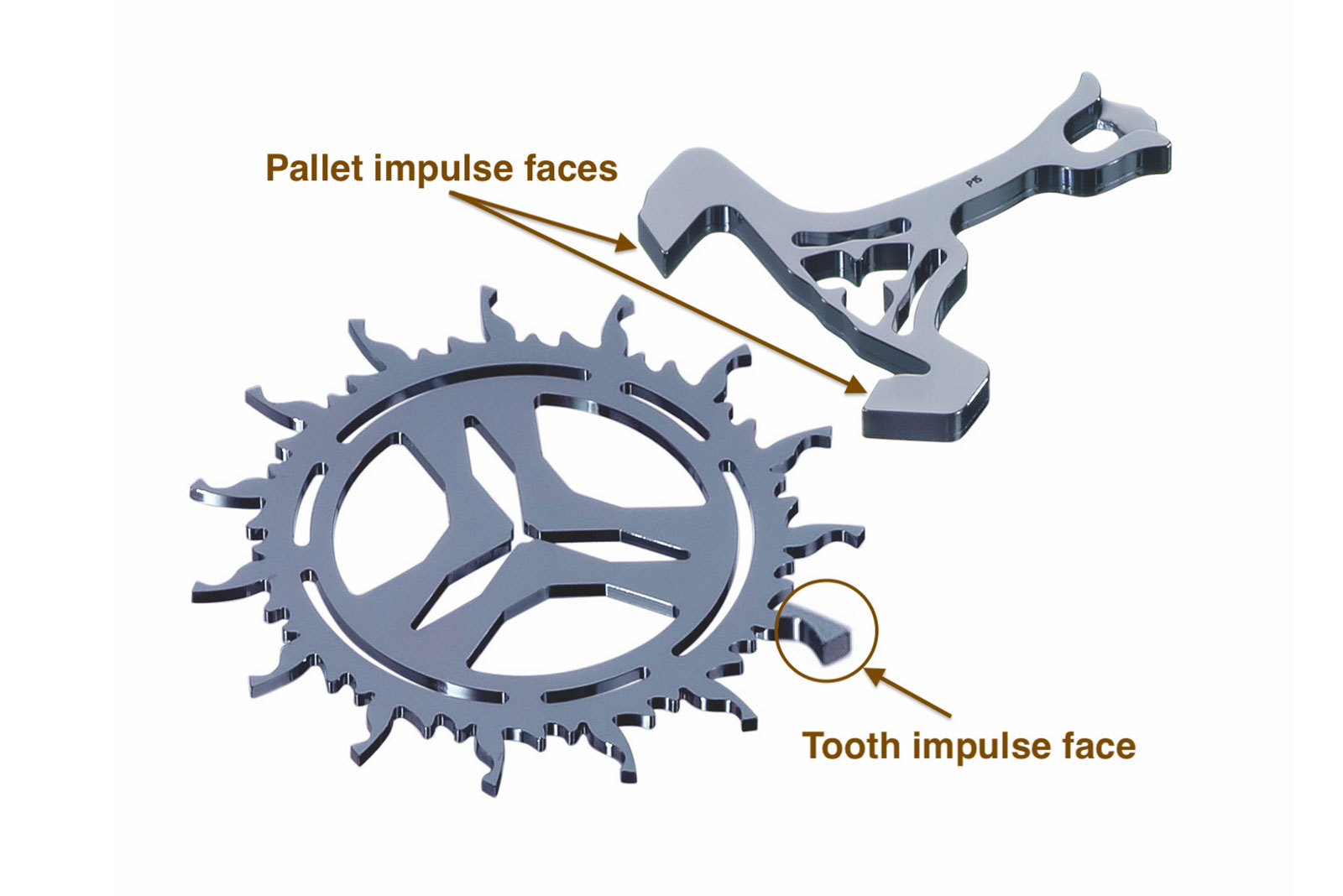
Patek Philippe Pulsomax – a totally opposite philosophy seeking the same goal with long pallets face length. Image – Patek Philippe
Chronergy’s improvements claim an improvement in escapement efficiency of 15%. This has two benefits, one being the torque needed to drive the escape wheel can be reduced, which means a less powerful mainspring made up of thinner metal ribbon. That leads to the second benefit, which is a longer power reserve contained the same barrel, since a longer and thinner spring can be accommodated in a given volume.
Working back with the calculations we already examined in our HDF analysis, we can estimate the Chronergy escapement adds approximately 7.5 hours of power reserve for the same barrel size and balance maintaining power (assuming same balance inertia, amplitude, and Q factor).
Drop – cutting the vampire loss
Drop is the distance travelled by the escape wheel from the end of impulse on one pallet to the point of locking on the other. During this process, the mainspring unwinds and advances the hands but transmits no energy to the balance, essentially achieving nothing.
This is often misconstrued as lost power or inefficiency, but it is in fact worse. The process is simply spring tension lost with no effect; the “vampire loss” in a mechanical movement. As a result, reducing drop to the absolute minimum is an immediate opportunity for a longer power reserve.
In Chronergy, as the pallet is shorter and less steep, the drop can be reduced for pallet clearance behind the tooth. As far as can be determined from the geometries shown, I estimate the reduction in drop is considerable, from roughly 2 degrees to about 1.4 degrees, which may amount to three hours of improvement in power reserve.
There is potentially a relationship between drop and lift angle, whereby reduced drop results in increased angular rotation of the escape wheel, leading to a larger lift angle. But because Rolex does not provide details on the escapement, its lift could simply be controlled by the leverage ratio of the pallet fork.
Inertia – lighter, faster, better
The inertia of the escape wheel is important because although the whole train has to start and stop with each tick and tock, the escape wheel is the last wheel in the going train. Its inertia is multiplied by the number of times the escape wheel turns for every one revolution of the fourth wheel, often by 10 times. That multiplication means that although the escape wheel is usually a light and small, its inertia has the highest effect of all the wheels of the going train.
My calculations determined that the plan-view rim area of the Chronergy escape wheel is two thirds of a conventional wheel. Based on the density of nickel-phosphorus being similar to or slightly higher than steel alloys and assuming comparable thickness, there will be a corresponding reduction in inertia.
I estimate the Chronergy escape wheel inertia is, at worst, 78% of the inertia of a standard wheel. Based on the torque delivered to the balance being 15% lower due to the escapement efficiency, the Chronergy escape wheel can still accelerate some 11% more rapidly than a conventional wheel.
In the absence of more information, it’s not possible to fully quantify the benefit of the Chronergy escape wheel – the effect may have already been bundled into Rolex’s claim of a 15% improvement in escapement efficiency – but a lower inertia is always a step in the right direction.
Locking – better symmetry
The distance from the lever’s pivot to the locking faces of the entry and exit pallet jewels can be set to provide either equal locking or equal impulse but not both – the reason being the width of the pallets. The wider the pallets, the more of a compromise must be struck between equal locking of the pallets and their equality of impulse.
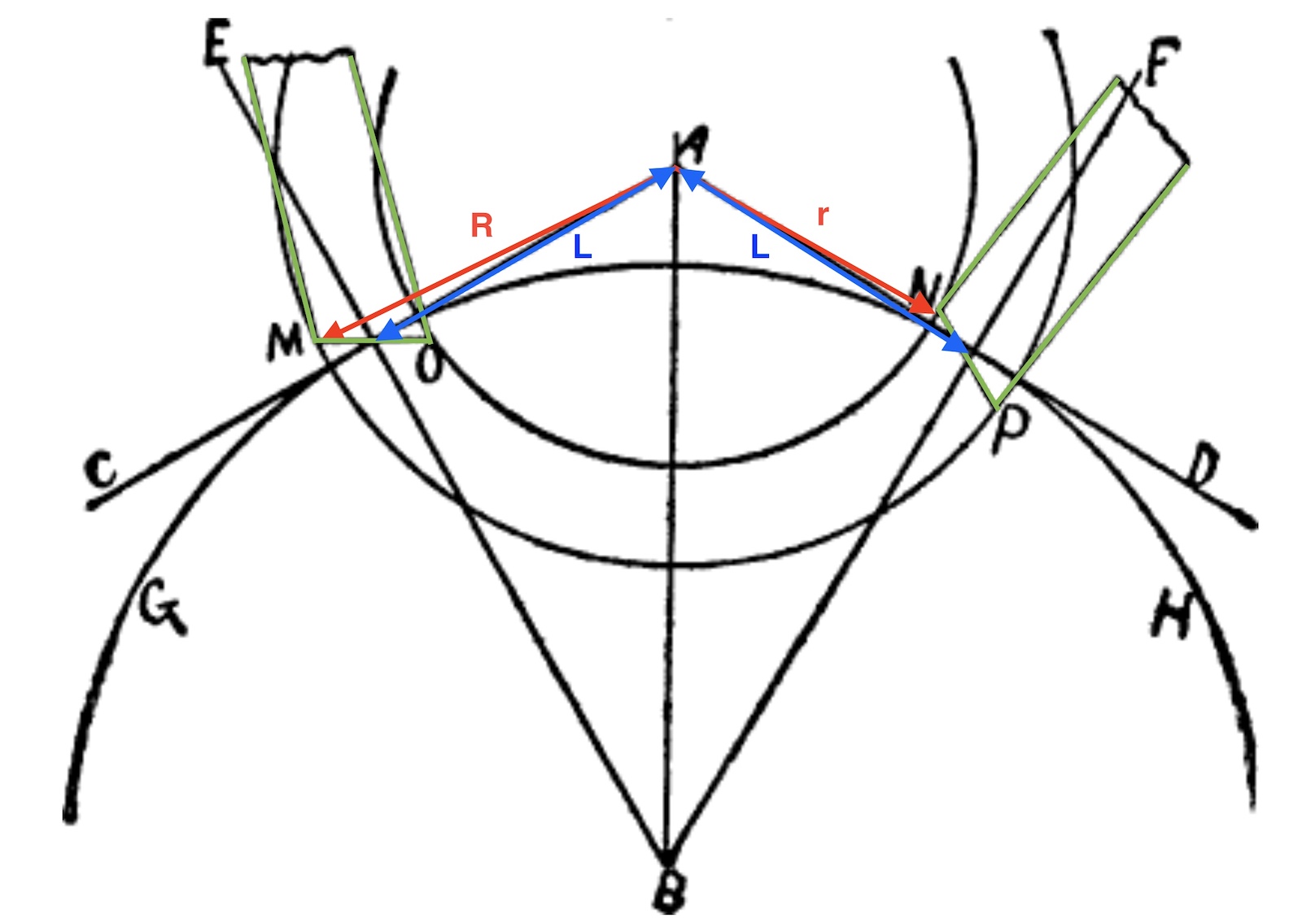
The above figure shows the case of ideal equal impulse (L is the same length on both sides) but unequal locking (lengths R > r). As the pallet face distance is reduced (as in the case of Chronergy) lengths M-O and N-P shrink. Hence R tends to reduce to L and r increases to L.
Unequal locking will mean that one of the pallets will absorb unnecessary power from the balance during unlocking (often referred to as ‘draw’) . Like a playground seesaw with the pivot off-centre, unequal impulse is also not ideal. The usual design is a compromise between the two requirements.
Compared to the standard escapement (with an exit to entry locking ratio of ~80%), Chronergy is more equidistant at ~92%. The narrower pallets of Chronergy allow closer to ideal equality of performance for both locking and impulse – like a perfectly balanced seesaw.
The benefit of this set up is impossible to quantify, but it is nonetheless clearly positive for performance. This may also explain why the press release for Chronergy notes the “escapement system is no longer in alignment but slightly offset, thus multiplying the lever effect.” Most people interpreted that as referring to the asymmetrical anchor, an incorrect assumption.
The kinked anchor has no effect on efficiency whatsoever, and is instead meant to free up real estate within the movement to more easily accommodate the longer lever. As an aside, the bent-anchor geometry is often used for escapements within tourbillon cages for the same reason of space constraints.
Mainspring barrel – the unsung hero
The barrel is the unsung hero of Chronergy. While we usually like to concentrate on the escapement – the sexy bit of a movement – the humble barrel’s contribution to timekeeping is huge.
The barrel in the earlier generation cal. 313x movements had a minute-hand ratio of 5:1, which meant that 46-50 hours of power reserve required 9.2-10 rotations of the barrel. The Chronergy movement appears to be based on a ratio of 98:16 – 70 hours of running time calls for 11.4 barrel revolutions. In short, the mainspring unwinds about 20% slower per hour in Chronergy.
Despite the its escapement requiring reduced torque, the Chronergy barrel actually requires a higher torque because the overall gearing is so much higher. By my calculations the barrel torque needs to increase 6.5% in Chronergy.
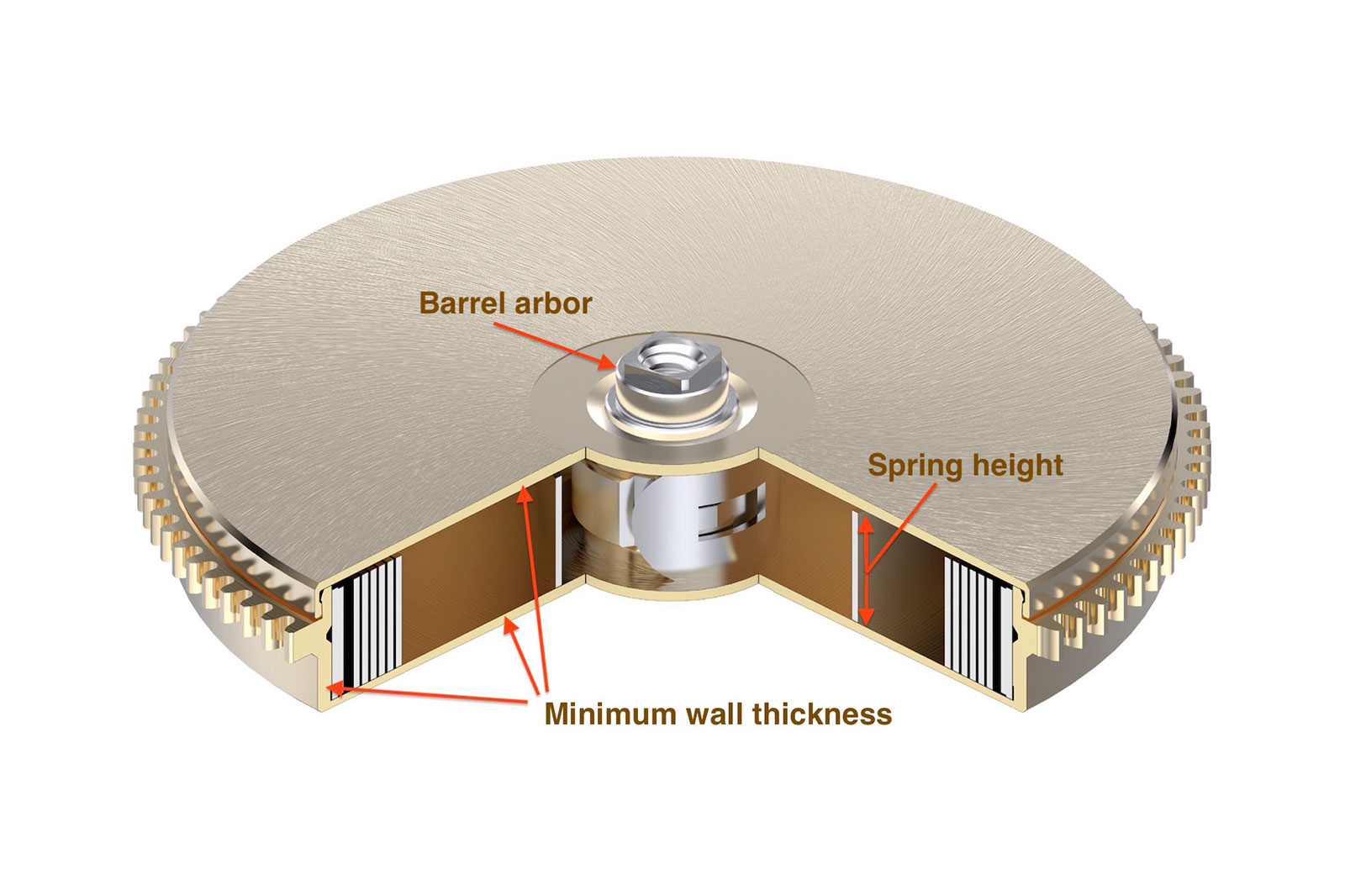
Rolex states the barrel design gives the Chronergy movement 10 hours power reserve improvement due to “reducing the thickness of its walls by half”. Image – Rolex
The diameter of the arbor cannot be reduced without risk of putting the spring into yield, which would result in a fatigued and eventually broken mainspring under continual operation. The only options are to increase the height or thickness of the mainspring ribbon. Of course, the same can be achieved with an entirely new mainspring material with higher strength, but I am assuming that Rolex are already at the top of the mainspring-alloy game.
The torque of the mainspring goes up with the square of the thickness, but only in proportion to height, which means thickness is given up as a last resort. But the thickness of the mainspring is dictated by the available space between the arbor diameter to the inner diameter of the barrel.
The remaining torque increase then has to come from the spring height. Looking at size of the barrel, it is possible to squeeze this extra turn-and-a-half in by shaving the barrel walls down but also by reducing spring thickness by some 9%.
However, the top and bottom of the barrel becomes exceptionally thin. The reduction in wall thickness can provide enough spring capacity to achieve the 10 hours of power reserve improvement, but at the expense of the the top and bottom of the barrel that have been reduced to the thickness of one and a half sheets of printer paper.
The barrel is further tapered between arbor and outer circumference, which is purely an efficient use of material thickness that makes it flexible enough for the snap fit of the barrel cover.
Compromise – performance versus serviceability
Engineering success is often compromise between reliability, durability, ease of maintenance, and the ability to mass produce. Rolex has clearly pushed each of these as far as practically achievable; the tolerances in Chronergy are certainly tight. It appears that something had to give here, and in this case it’s ease of service.
According to the Chronergy article in Horological Journal, only complete barrel assemblies are available during servicing or repair. The thinness of the barrel walls probably means the risk of buckling, bending, or other damage is deemed too high if the barrel is taken apart.
As a result, traditional steps in servicing a mainspring – disassembly, polishing, spring replacement, lubrication and reassembly – are likely not possible on a typical watchmaker’s bench, at least within an acceptable margin of safety.
It is difficult to quantify the benefit of the barrel’s construction, but in Chonergy, the going train is arranged in a direct line from the barrel to escape wheel using a centre wheel layout. The earlier cal. 313x family of movements had the timing train separate from those of the hands, where a minute pinion was directly connected to the barrel at the movement’s centre.
Chronergy removes the drag of one extra pinion on the barrel – an advantage, but with a potential height penalty. This seems to have been overcome by redesigning the automatic winding system, reducing its height by incorporating a one-piece rotor riding on bearings. Again, this at the expense of complete replacement rather than repair, since the rotor has to be replaced as a single unit.
A modular-replacement approach to servicing has already been adopted by other watchmakers at all levels of the price spectrum. Factory-wound barrels are already common as drop-in replacements, while some H. Moser & Cie. movements feature modular balance assemblies that can be swapped out during an overhaul.
This approach is acceptable as long as the replacement units are perfect substitutes, especially in that the substitute parts do not create a servicing issue in the future. However, there are subtle nuances to consider in terms of collecting philosophy for the hardcore watch enthusiast. We don’t want dial and hands replaced, so should you get to retain “your” barrel assembly?
Bravo Abe-san and chapeau Rolex
The combination of all its features gives Chronergy-equipped movements a 40-50% gain in autonomy over previous-generation calibres, an improvement entirely consistent with Rolex’s assertion of “approximately 70 hours” of power reserve in Chronergy movements.
Based on our metric of Horological Density Factor, and assuming the same balance power as the cal. 313x movements, the Chronergy-equipped cal. 323x family breaks the 25000 kJ/m3 barrier – a great performance (that handily beats Omega’s flagship Master Co-Axial cal. 8500, perhaps the most comparable alternative).
But beyond the performance gains in Chronergy, it is pleasing to see that there is still the ability to enhance the traditional lever escapement. Equally satisfying is the fact that the key advancements in Chronergy originate some half a century ago, in the research of an upstart Japanese watchmaker that was already at the tail end of its quest for mechanical accuracy.
Now those ideas have been thoughtfully revisited and taken further with clever enhancements, before being ultimately adopted as the new normal by the masters of high-quality mass production – Rolex.
Back to top.