In-Depth: The MB&F LM Perpetual and Stephen McDonnell’s Innovation
A unique calendar explained.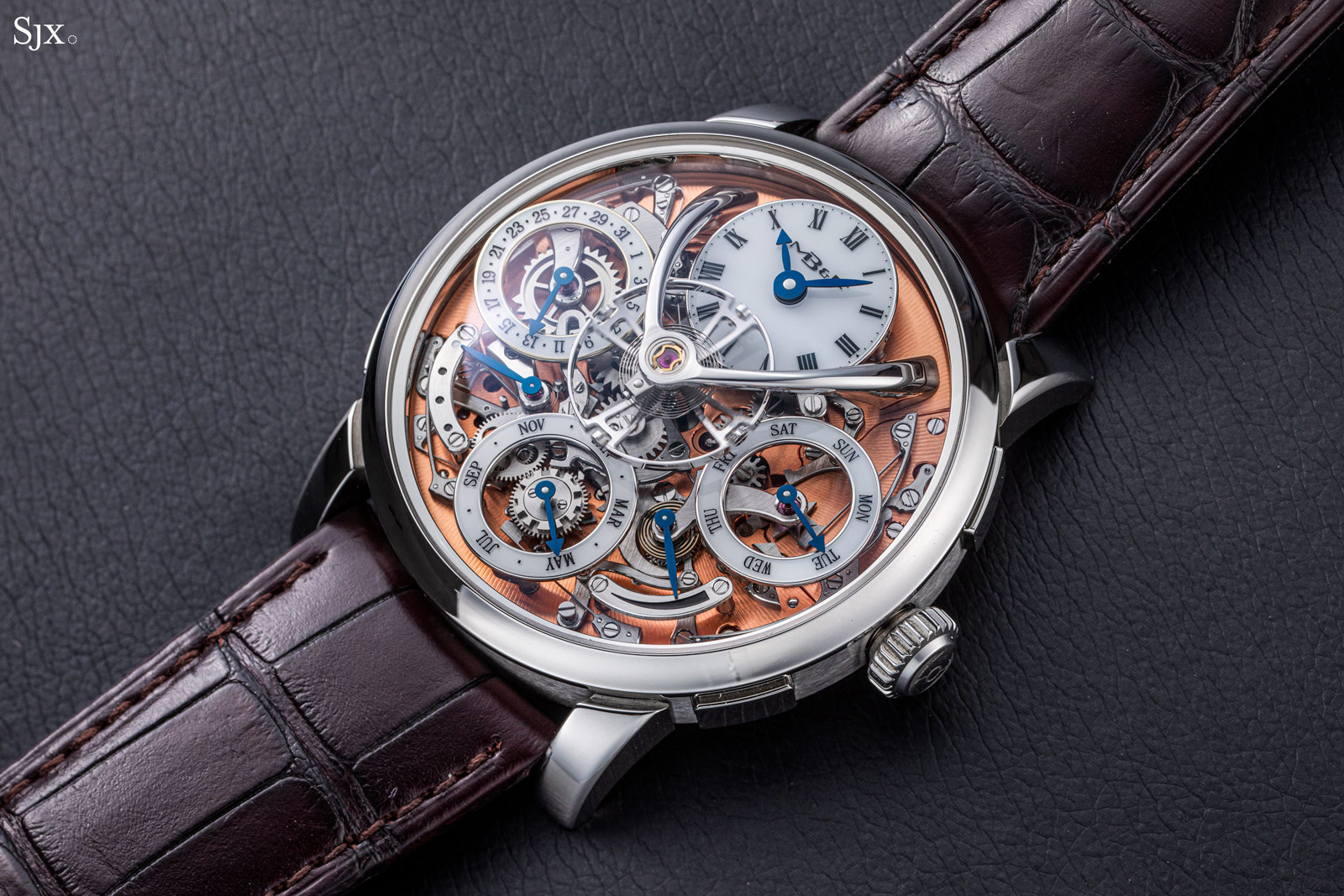
When it comes to perpetual calendars – perhaps the most objectively useful complication – the MB&F Legacy Machine Perpetual, or LM QP for short, sits neatly between classical architecture and iconoclastic construction.
Now almost a decade old having been launched in 2015, the LM QP is a mechanical marvel coming from the mind of Stephen McDonnell. The LM QP’s beauty lies in Mr McDonnell’s rethinking of the perpetual calendar complication while integrating historical concepts.
Rethinking the QP
A perpetual calendar, or quantième perpétuel (hence “QP”), is a complex and layered mechanism, which makes it a challenging complication to implement in watches. Naturally, not all perpetual calendars are created equal, some being more innovative and others more classical in their construction.
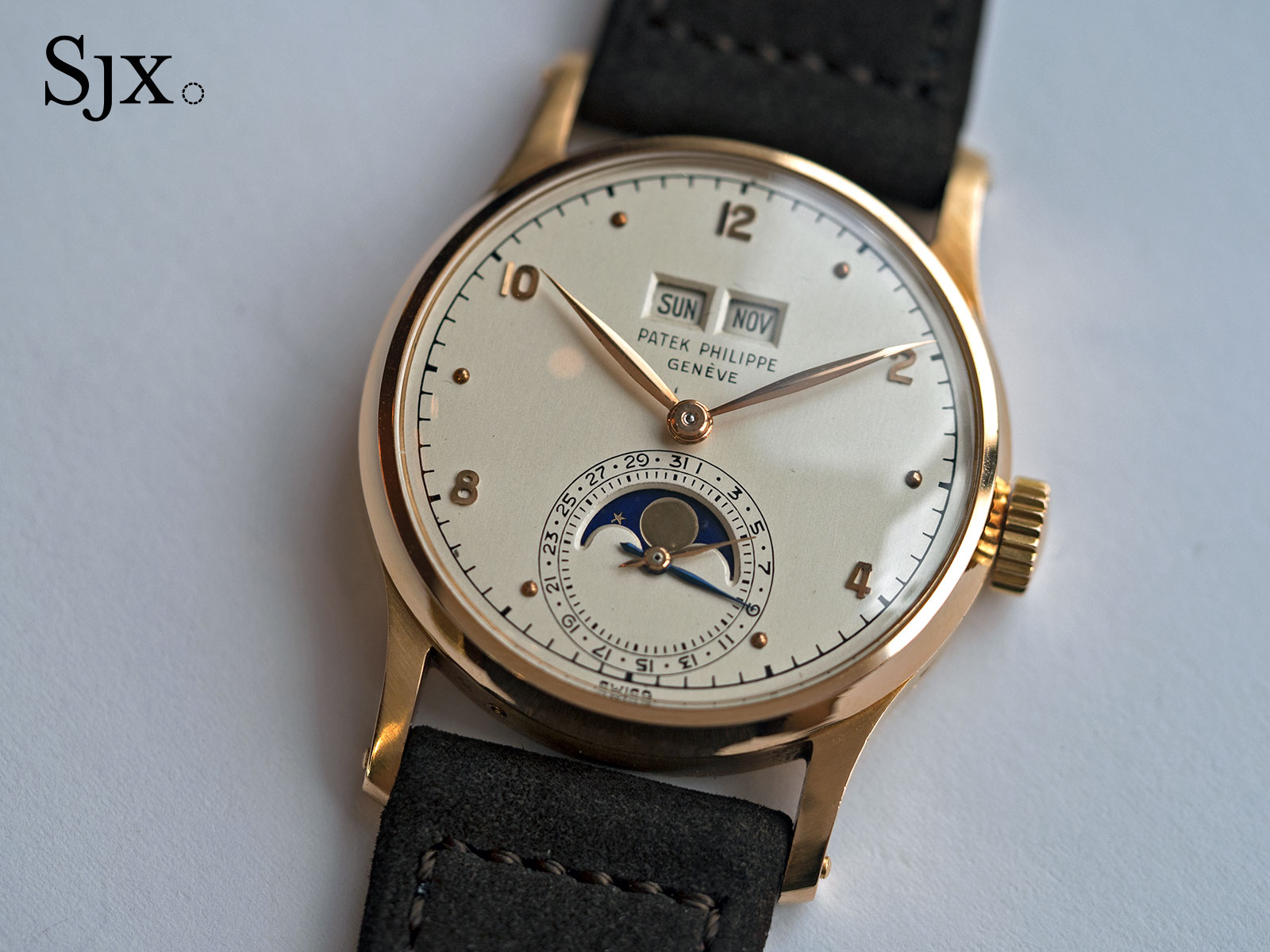
The first-ever serially produced perpetual calendar wristwatch, the Patek Philippe ref. 1526 that debuted in 1940; the basics of the perpetual calendar mechanism would remain largely unchanged for decades after
The issue with classical calendar constructions is their vulnerability to wear and tear, shock, or careless operation by the user. Ironically, the most forward-thinking of perpetual calendar mechanisms try to solve these problems, but sometimes suffer from reliability issues rooted in the radical concepts employed.
Mr McDonnell’s construction of the LM QP smartly manages to eliminate traditional weaknesses while avoiding new problems. The result is a reliable and innovative perpetual calendar that paradoxically retains a fairly conventional foundation.
The “grand lever”
Before delving deeper into the LM QP, we must first understand the classic perpetual calendar construction and its main weaknesses. While perpetual calendars are often considered a “smart” complication, their actual functioning requires little-to-no mechanical processing.
A conventional perpetual calendar displays the Gregorian calendar, which has a quirk of the leap year cycle comprising four years – three common years of 365 days each and one leap year with an additional day. Each year contains 12 months, a full leap-year cycle totals 48 months, but each month has a different number of days. However, the cycle repeats and monthly differences are fixed, so all that information can be physically encoded on a disc with 48 notches of different depths.
This disc is known as the 48-month cam, a distinctive component of the perpetual calendar. It makes a full rotation during a leap year cycle, advancing by one step each month, for 48 steps in an entire cycle. The month cam works in conjunction with the grand levier, which translates as “grand lever”.
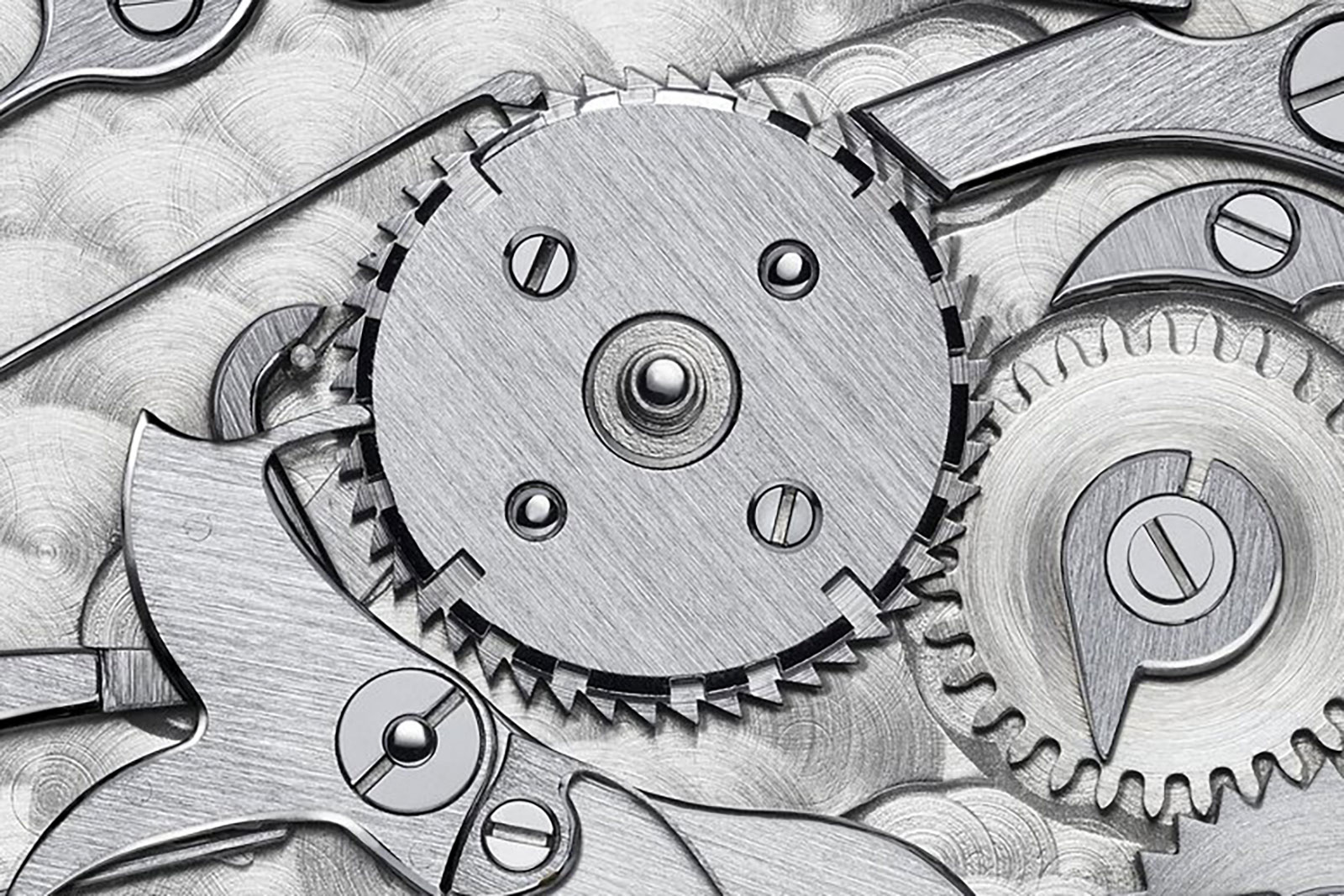
An example of conventional 48-month cam and grand lever
The classic perpetual calendar construction is plenty complex, but its working can be reduced to the process diagram in Fig. 1. The base movement provides the time indication, which in turn actuates the grand lever once every 24 hours.
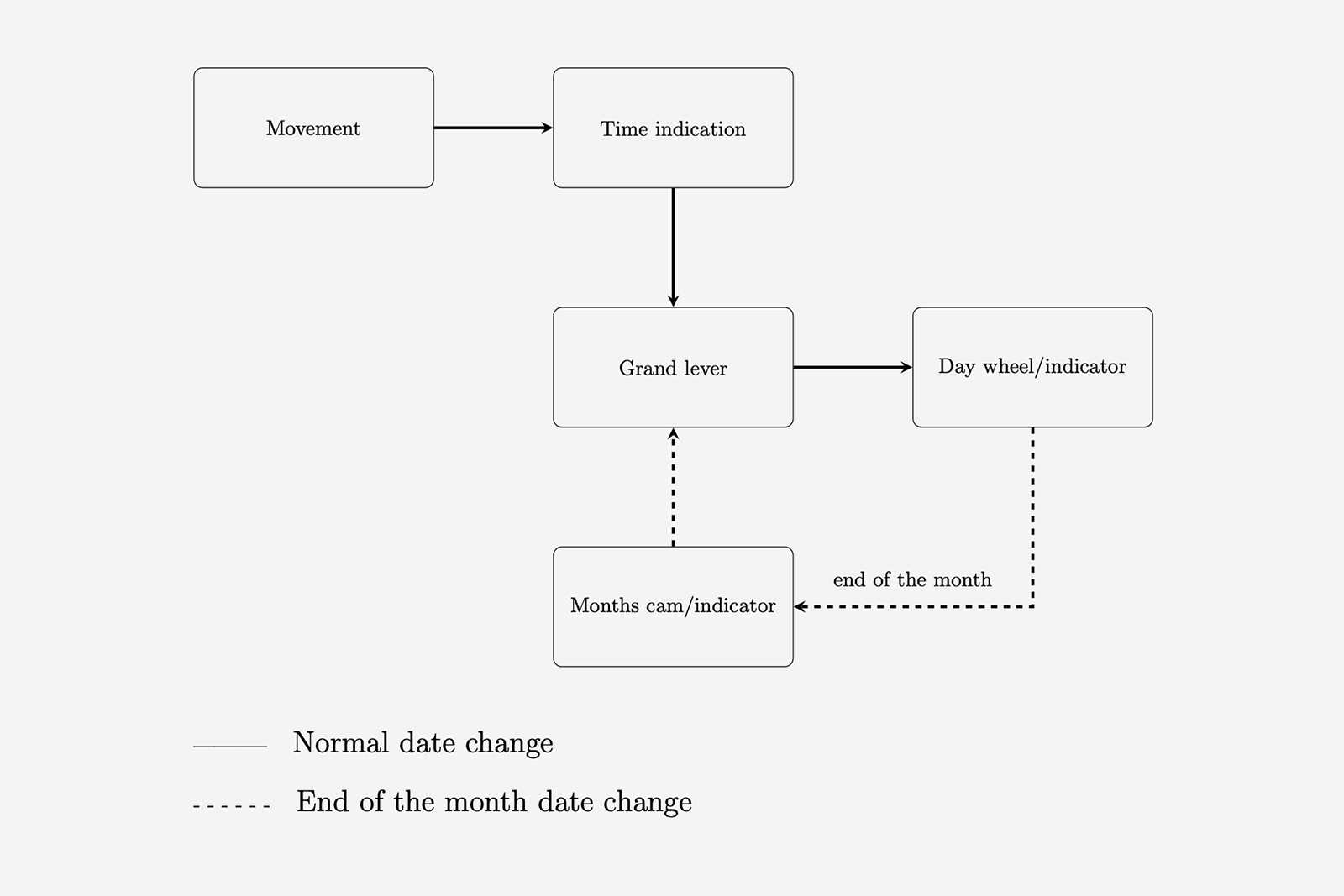
Figure 1. Process diagram of a conventional perpetual calendar
At each month’s end, the beak of the grand lever “reads” the depth of a notch on the 48-month cam. Depending on the distance the beak sinks into the notch, the grand lever will skip one, two or three days, starting from the base month model of 31 days. A dedicated pawl on the grand lever works with a 31 toothed gear and skips over one, two or three teeth, depending on how far the 48-month cam allows it to swing.
A dedicated pawl on the lever normally makes the day wheel advance by one tooth. Over the course of the month, a snail cam slowly forces part of the lever to touch the months cam. The feeler reads the notches in the cam and at the end of the month makes the lever pivot amply enough so its pawl can skip the adequate number of days. The day wheel then acts back on the months cam, advancing it by one step.
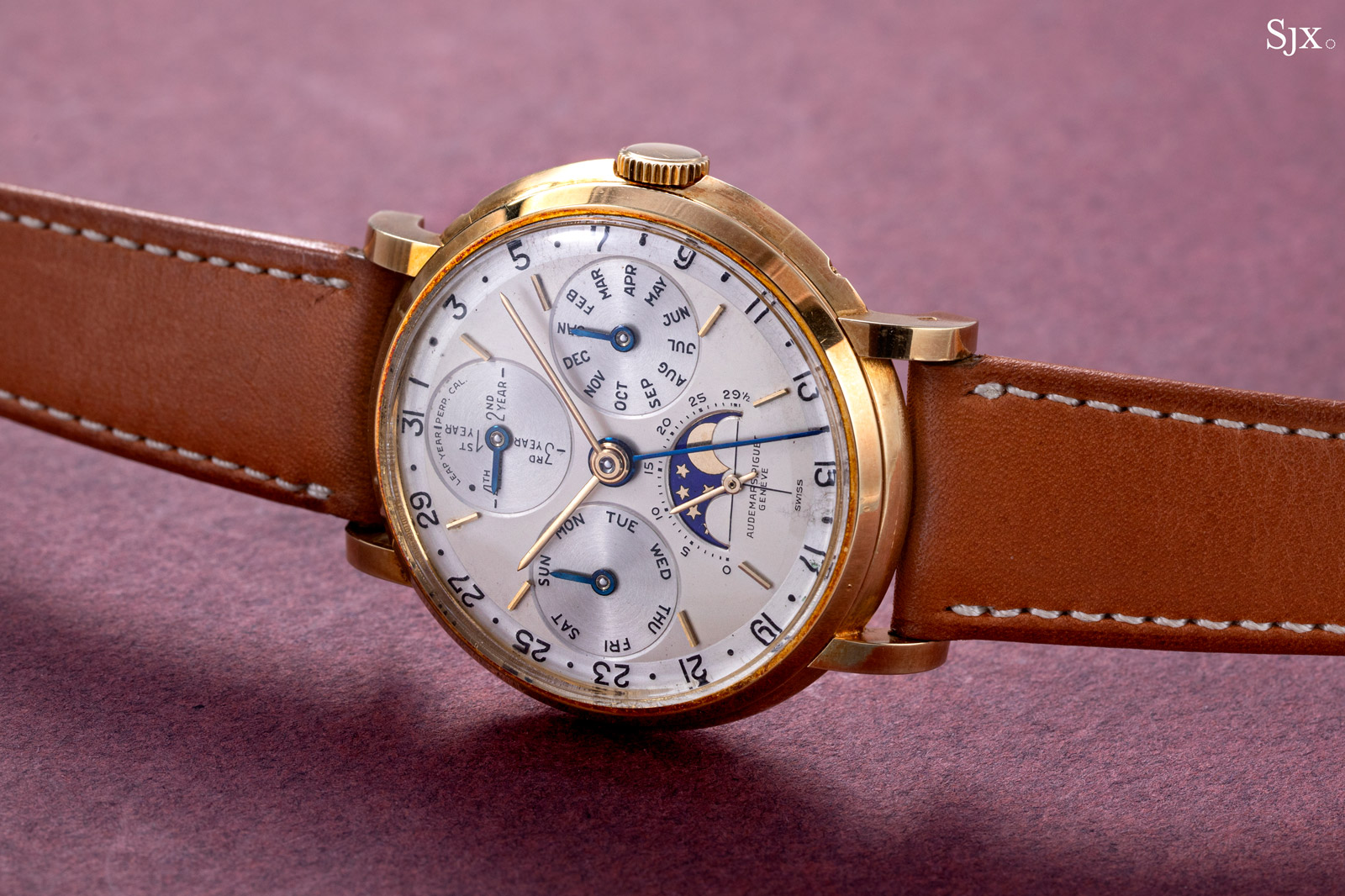
The Audemars Piguet ref. 5516 that was launched in 1955 as the first-ever serially produced perpetual calendar with leap year indicator; its visual similarity to recent perpetual calendars demonstrates how little changed over the decades
The skipping process takes place at the very end of the month and is strenuous for the components involved. The date change leaves the mechanism vulnerable to any outside influences during the skipping timeframe.
The energy consumption is considerable and on rare occasions the grand lever can fail on its own, without any outside disturbance. Moreover, some components can bind together slightly even after the date change, making any manual adjustments perilous for a while after the date switch.
Efforts have been made over the years to refine and improve the “grand lever” perpetual calendar, though most have addressed the interface rather than the fundamental operation of the mechanism. One example is the famous IWC calendar module developed by Kurt Klaus that’s based on a grand lever and 48-month cam architecture, but reworked to be set exclusively through the crown for a more straightforward user interface.
As an aside, some perpetual calendar mechanisms replace the 48-month cam with a 12-month cam and a satellite gear for the leap year. The 12-month cam revolves once per year, with the satellite geared to rotate every four years, fulfilling the role of the leap year slot.
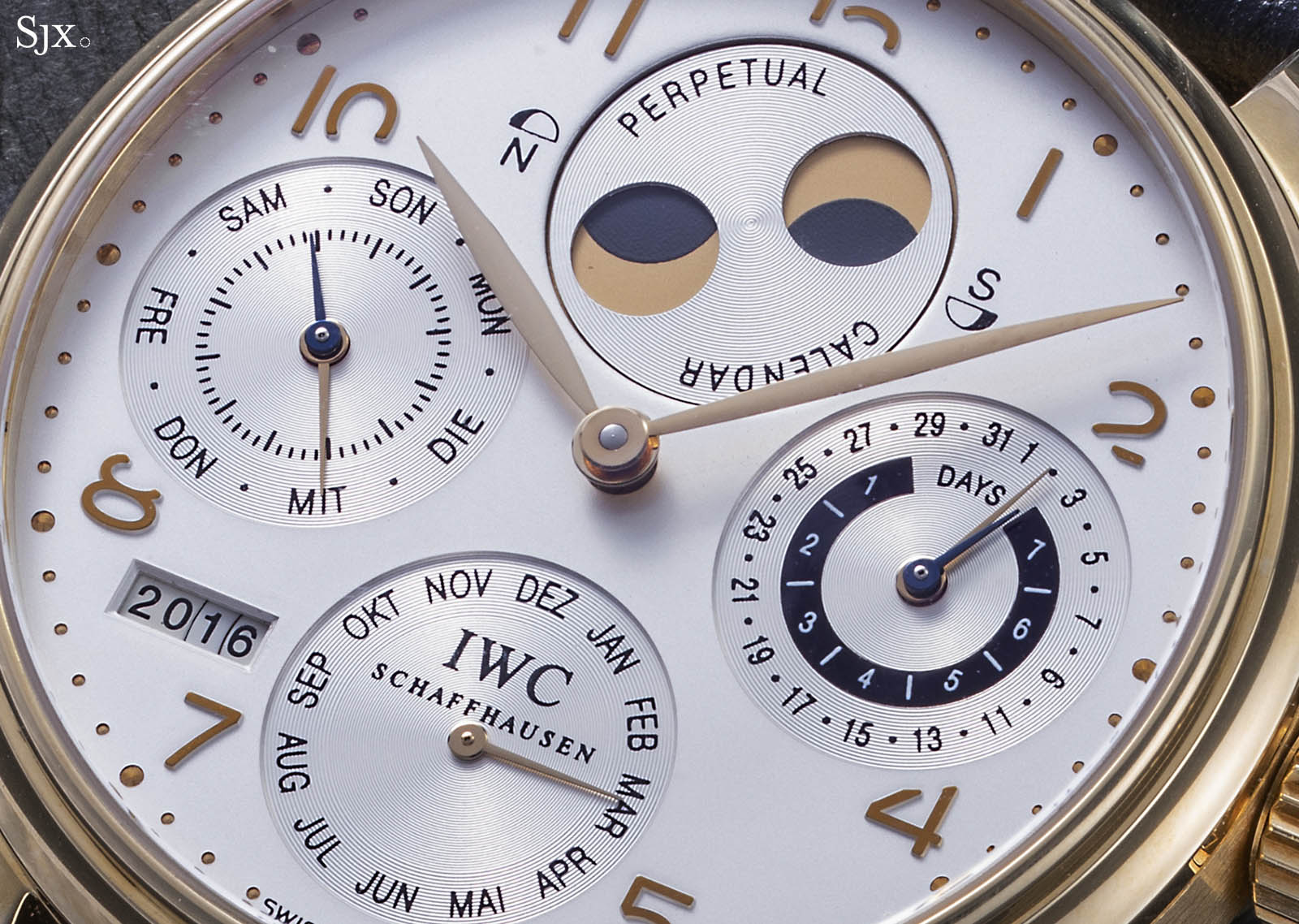
Featuring a distinctive four-digit year display, the IWC perpetual module uses a modified grand lever
Thinking different
One of the issues with classical perpetual calendars stems from the way the month lengths are computed: the assumption is that every month is 31 days, with one, two or three days subtracted as needed.
For the LM QP, Mr McDonnell took a vastly different approach: he started from the premise that each month has at least 28 days. So his base model is in fact 28 days, with an appropriate number of days added for each month.
At first, it might seem counterintuitive. A 28-day month comes occurs in three out of every four years in a leap year cycle, so out of the 48 months of the entire cycle, 45 would need days added. In comparison, the classical 31-day model operates on a common scenario – 28 out of the 48 months have 31 days, meaning only the remaining 20 need correction.
On a purely intellectual basis, the classical architecture appears more efficient, since such a perpetual mechanism only has to make 20 corrections during the leap cycle, while the LM QP has to make 45.
In practice, however, the McDonnell system is more streamlined and relies on a monthly self-programming process. Its key strength lies in the way the monthly corrections are made, which ultimately make the MB&F a fundamentally better system.
The constituent parts of the LM QP
The McDonnell perpetual system introduces a new component to the conventional calendar mechanism, one that is truly novel in terms of utility and value. Described as a “mechanical processor” by Mr McDonnell, it is the crucial piece of the puzzle that makes the LM QP what it is.
While subtracting days in a conventional calendar is just a matter of skipping gear teeth, adding days to a base month model is an entirely different affair. Because a gear is a solid component, its tooth count is fixed. This is where the mechanical processor comes into play – it acts as a variable command gear, with a tooth count that can vary and adapt.
The mechanical processor
The mechanic processor is essentially a stack of gears, with active and passive levels incorporating sections without teeth. The processor is directly engages with the day indicator and can interact on occasion with additional slides and levers. The fully assembled processor is depicted in Fig. 2c.
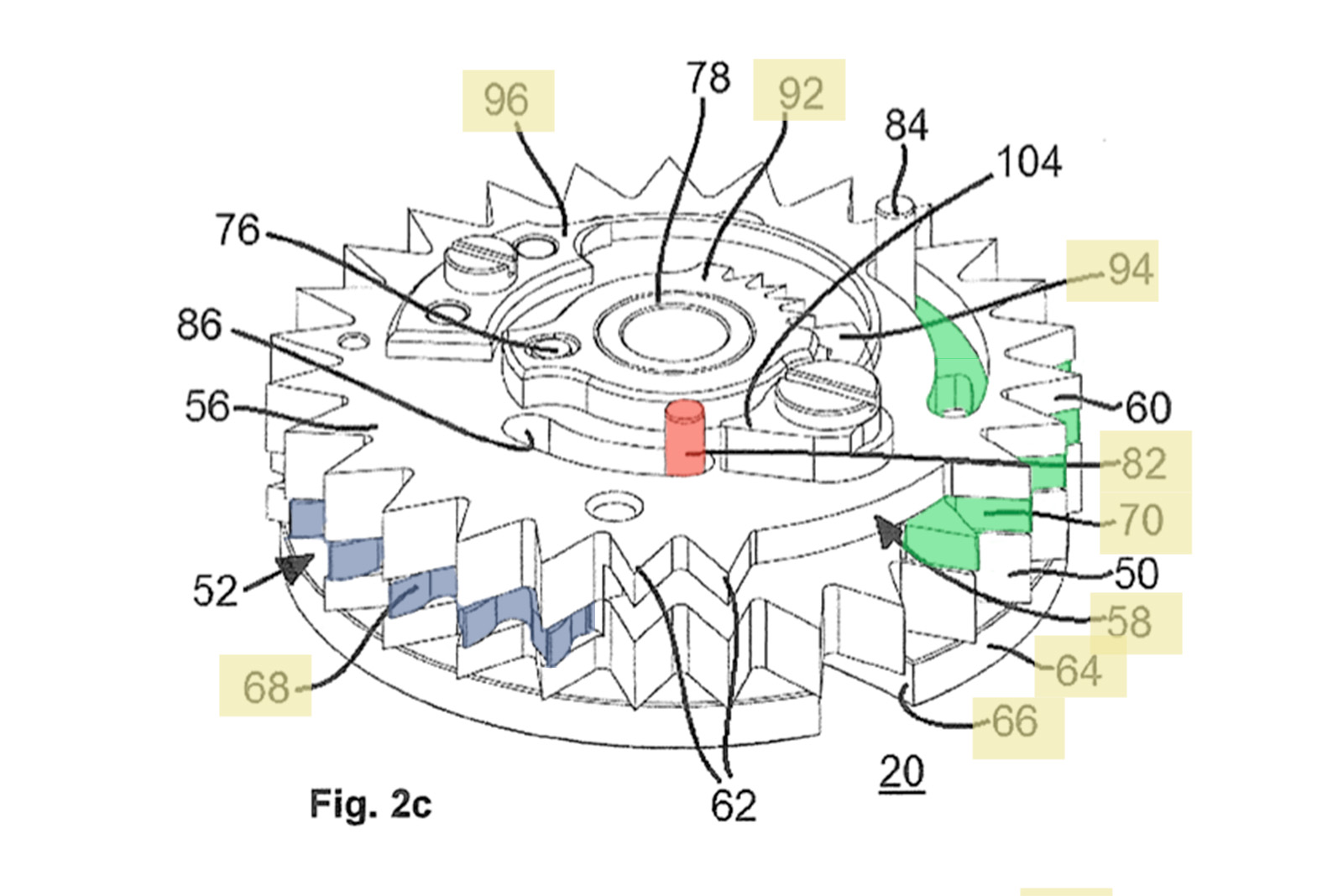
Figure 2c. Source – patent CH 711 679 A2
The processor is able to perform several functions as it is composed of several parts; the exploded view is shown in Fig. 2a. Sandwiched between two gears is a two-part pivoting rack featuring two sets of teeth. The rack has a certain degree of freedom, being able to slide and bank along apertures in the gears (for example notch 102 in Fig. 2a).
The two sets of five teeth of the rack (blue 68 and green 70) can pivot around a central axis between the two gears. The movement of the upper and lower gears are restricted by a click assembly (92, 94 and spring 96) mount on the top of the processor.
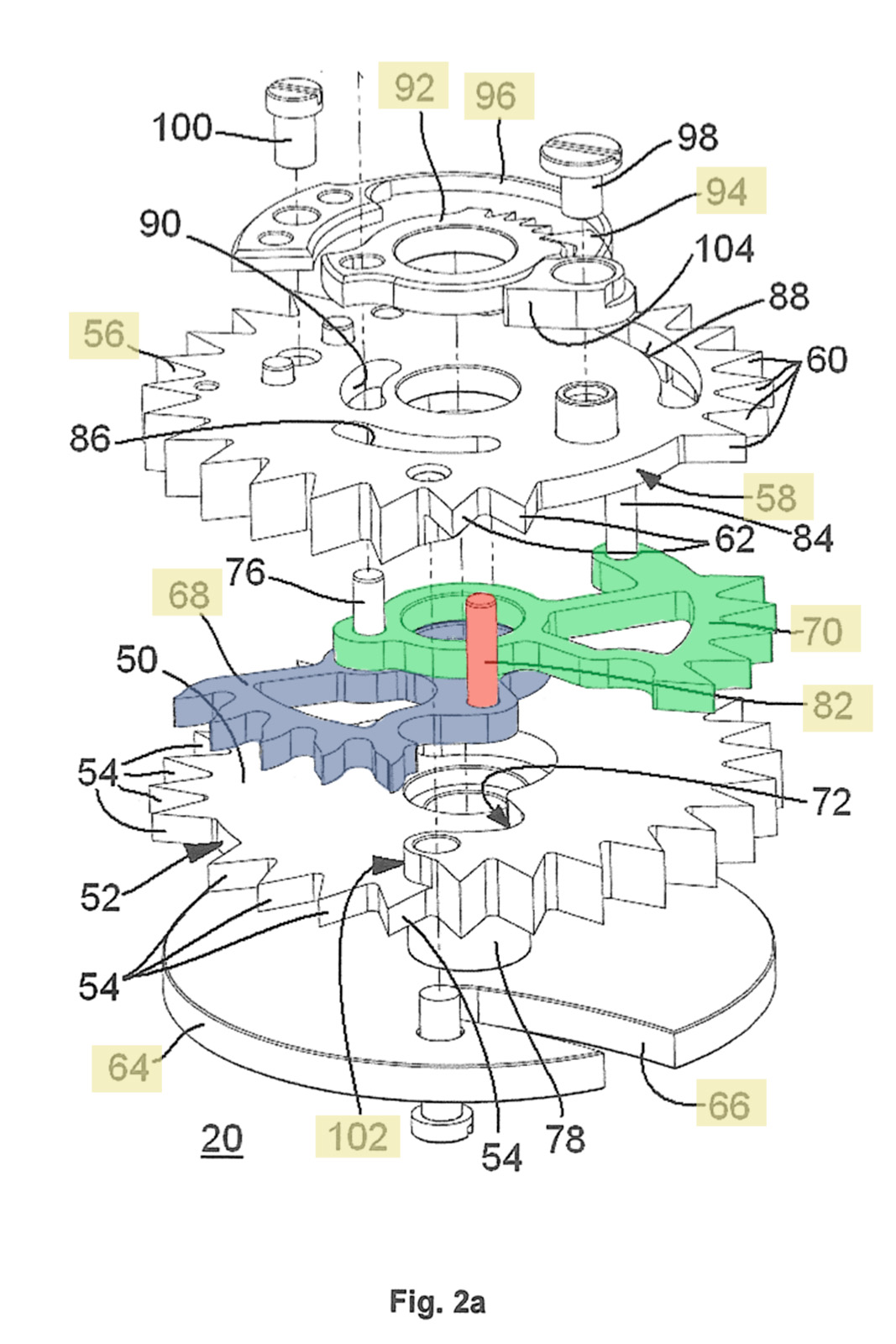
Figure 2a. Source – patent CH 711 679 A2
The pivoting sectors of the gears can be indexed in position and kept secure by the click. The click allows the toothed rack to take on four possible positions, depending on the length of the month. The topmost gear 56 has 24 teeth with a smooth sector 58 equal to three teeth spacings. One level below on the rack is sector 70 that always shows three teeth, regardless of its indexed position. This makes a total of 27 teeth between the upper gear and rack.
The mechanical processor is kept in place by a strong jumper spring. The spring not only assures the correct indexing of the processor, but also of the day indicator, whose special construction makes it impossible for it to have its own jumper.
During normal date changes – namely from the 1st to the 27th of each month – the mechanical processor works like any intermediary gear, simply passing motion from the lever to the day indicator. First a finger on the main lever engages the mechanical processor at midnight, advancing it by one step each time. The mechanical processor in turn advances the day indicator by one step.
A secret retrograde display
The day indicator itself is worth a digression. Usually, the 31 numerals representing the dates of a month are crammed into a tiny sub dial, with only odd-numbered dates in numbers and the even-numbered days represented by dots in order to maximise legibility. The typography method is useful, but ultimately makes for an awkward transition from “31” to “1”, which have no dot between them and can end up resembling “311”.
In comparison, the LM QP boasts a more legible date register, which curiously features a dot between “31” and “1”. In an ordinary perpetual calendar display, this would indicate the 32nd day of a month. Naturally, this is not the case because the indicator is not conventional, but rather a cleverly integrated retrograde system that allows for the aesthetically-pleasing arrange of the date scale with the dot between “31” and “1”.
Retrograde indicators are commonly associated with semi-circular scales where the hand jumps back to its starting position when reaching the end of the time indication.
On the other hand, the LM QP date display is circular with no breaks in the scale. The retrograde action is concealed: when switching from the end of the month (be it the 28, 29, 30, or 31) to the first of the next month, the date hand doesn’t advance forwards, but rather jumps backwards all the way, instantaneously making a near-complete counterclockwise turn back to “1”.
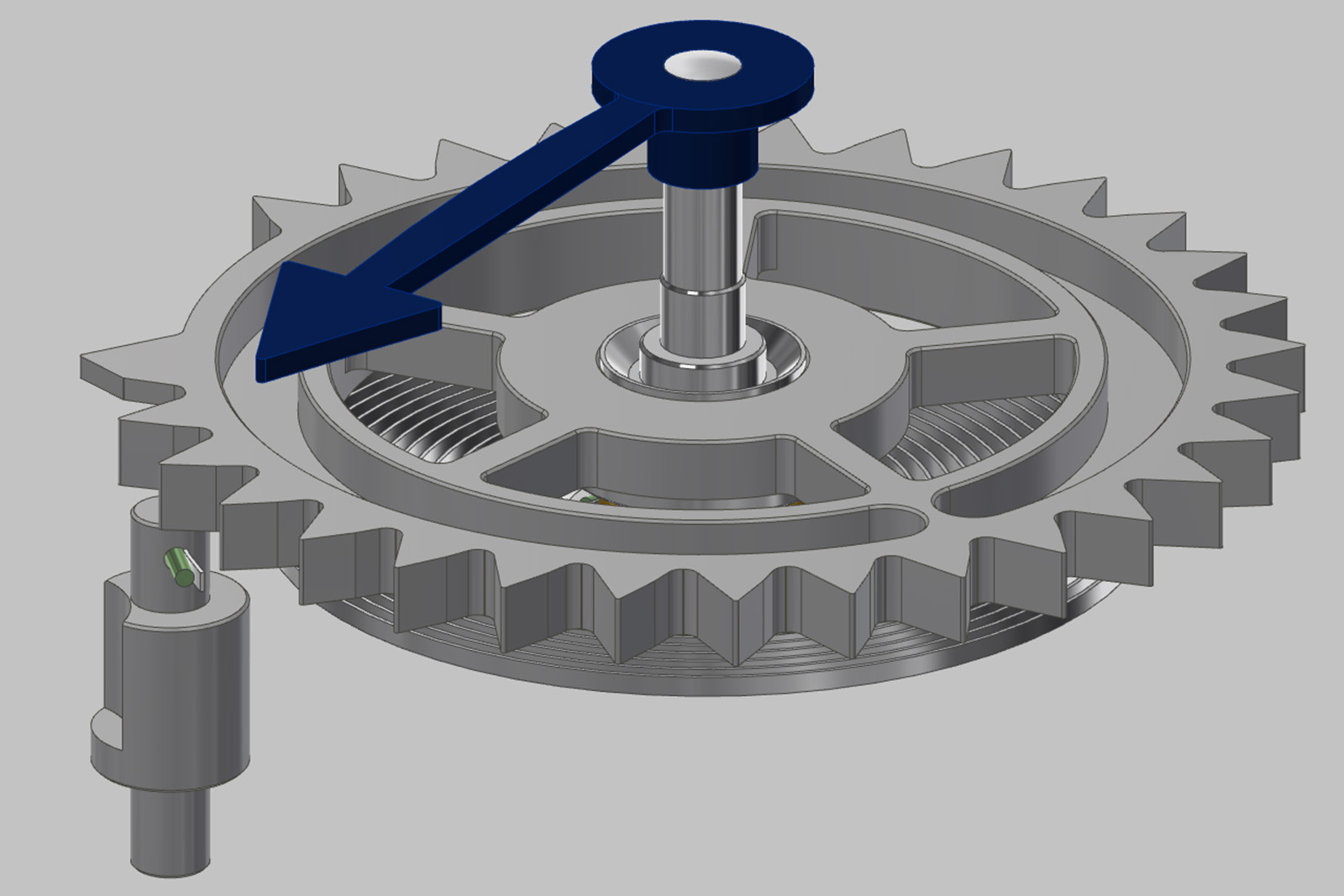
The LM QP date indicator assembly viewed from the dial
Like many retrograde displays, the date is driven by a spring – an unusually long, coiled spring, that resembles a hairspring.
With each date change during a month the coiled spring is tensioned little by little, thus arming the retrograde system. At the month’s end, the tensioned hairspring unwinds swiftly, snapping the hand back to its starting position at “1” on the date scale.
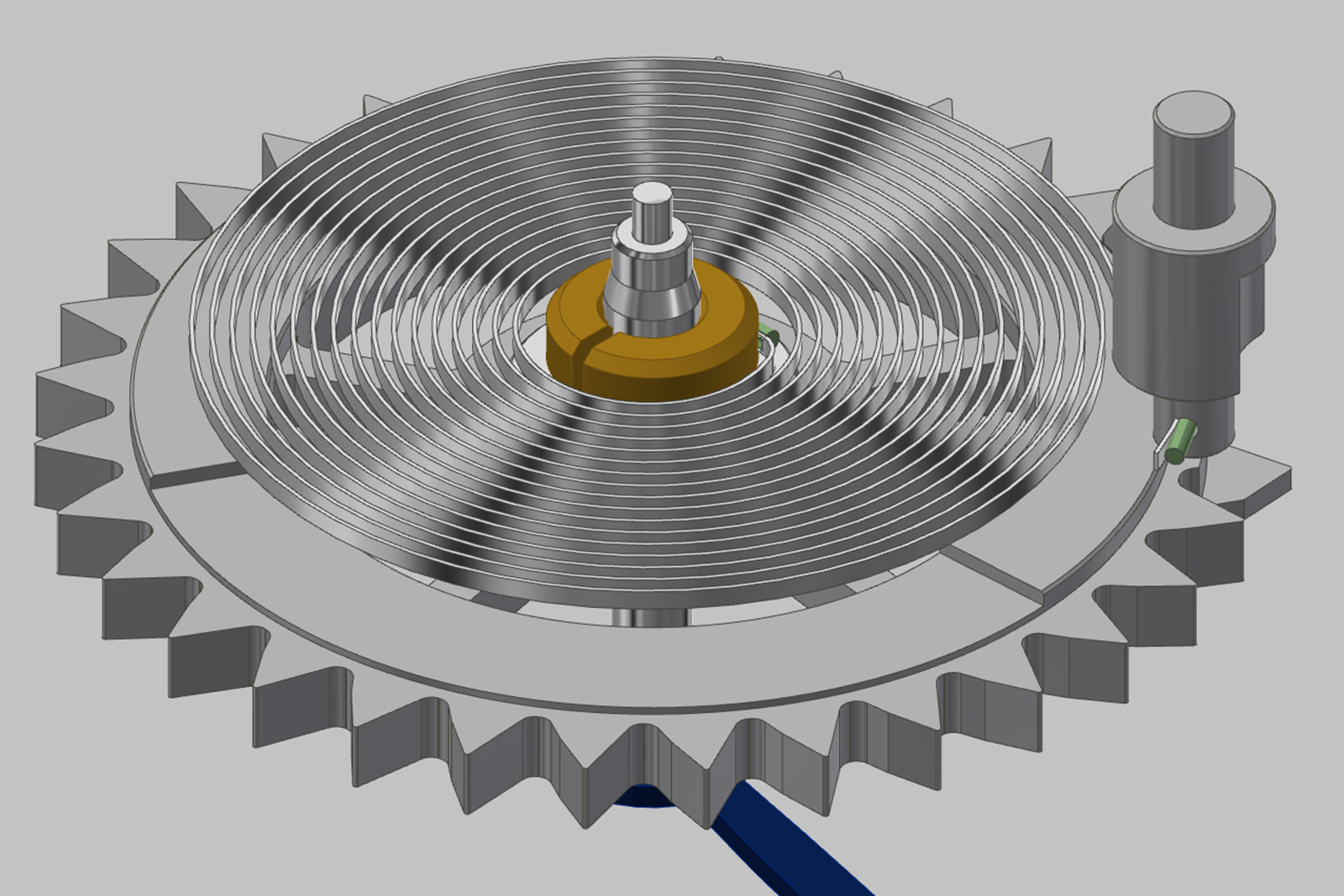
As seen from the back, showing the hairspring-like component that drives the retrograde date
Programming, reprogramming
With its unique mechanical processor, the LM QP relies on a programming process absent in other perpetual calendars that involves a fairly conventional 12-month cam and leap year satellite, a number of racks and levers, and the mechanical processor itself. The programming takes place on the 25th of each month in a process outlined in the Fig. 3.
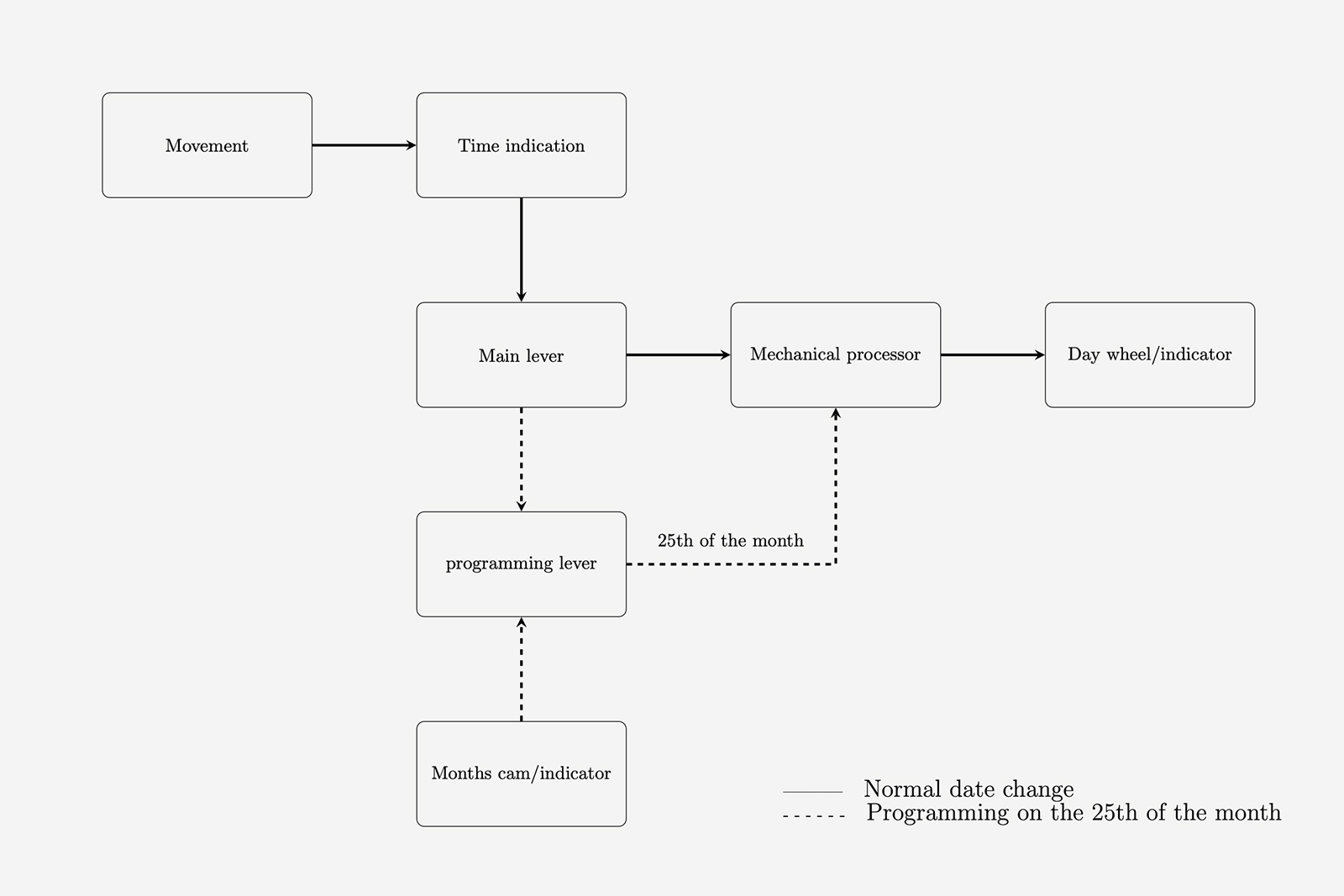
Figure 3. Process diagram for the MB&F LM QP
During the programming process a system of two levers interact in a manner reminiscent of a traditional grand lever: one lever reads the current month length from the month cam, while the other passes the information to the mechanical processor. The two levers engage with each other via distinctive toothed racks.
Over the course of a month, the main lever 16 makes small daily jumps, each advancing the mechanical processor (and subsequent the day indicator) by one step, via the former’s finger 114. As observed in Fig. 4, the lever makes the daily jumps in a clockwise direction.
Absent in Fig. 4 but crucial to the system is an auxiliary return spring that forces lever 16 towards the mechanical processor.
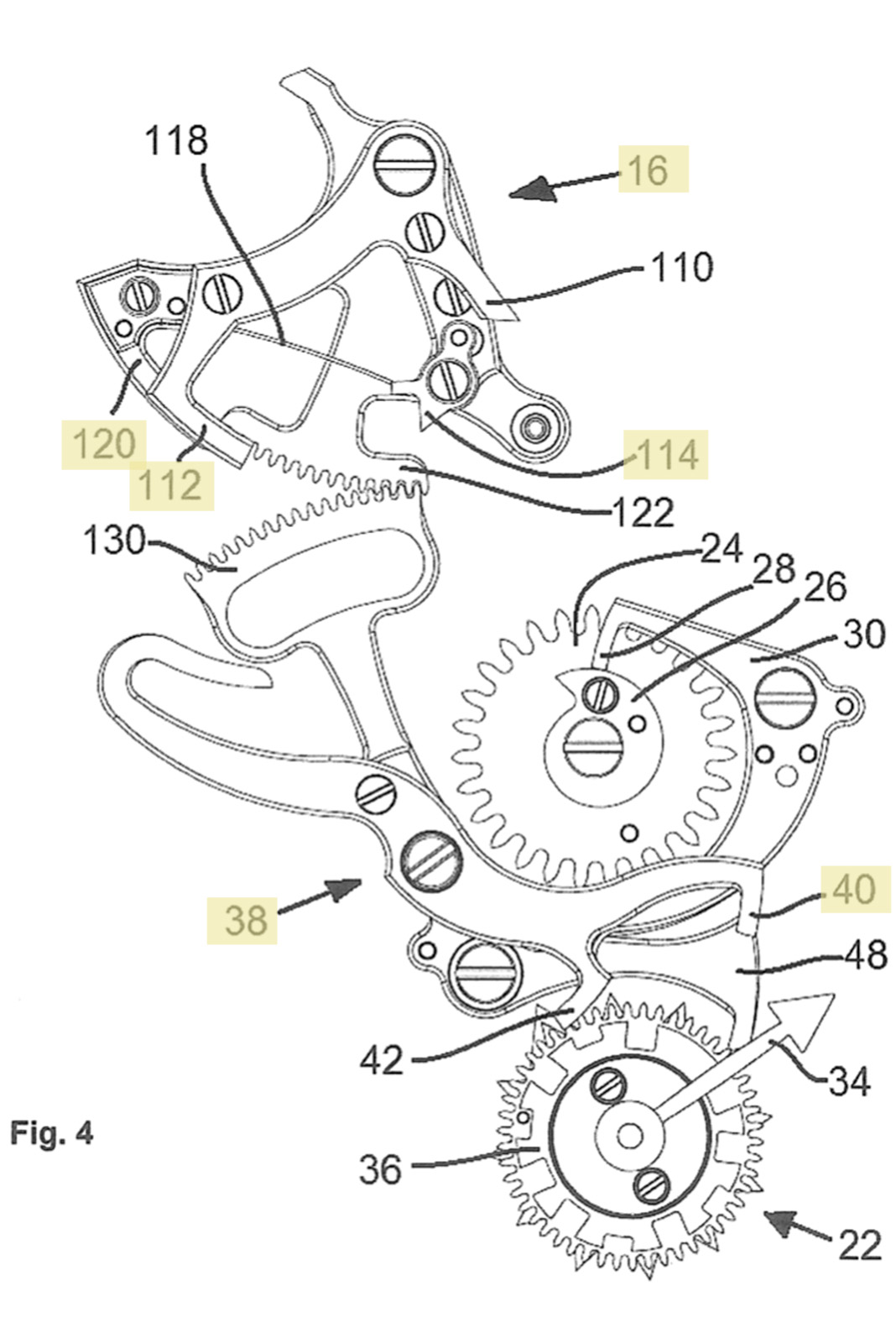
Figure 4
The lowermost portion of the mechanical processor works as a banking surface for the main lever. Beak 120 is in constant contact with the circular surface 64 of the mechanical processor.
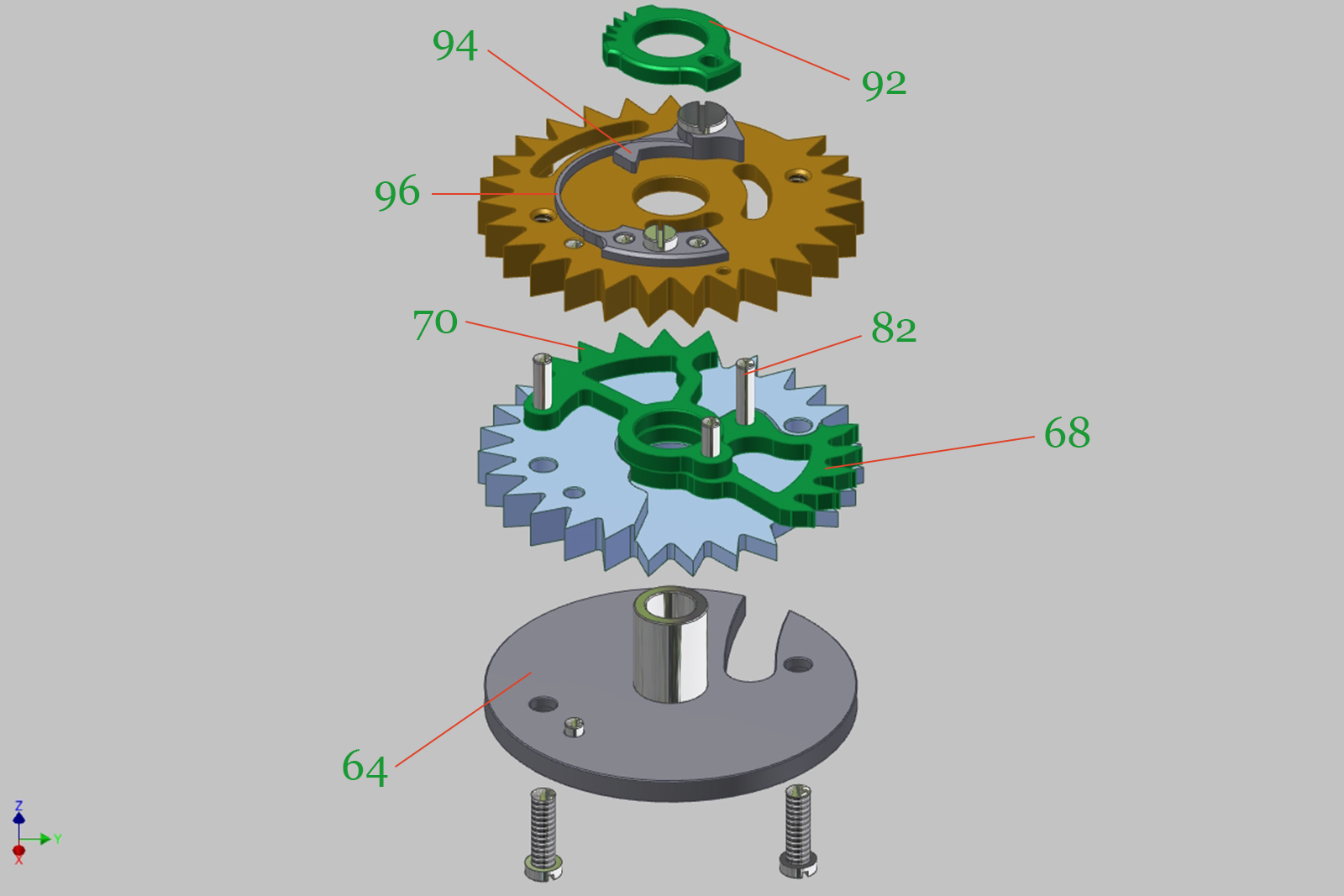
Exploded view of the mechanical processor. Beak 120 banks on the circular surface 64
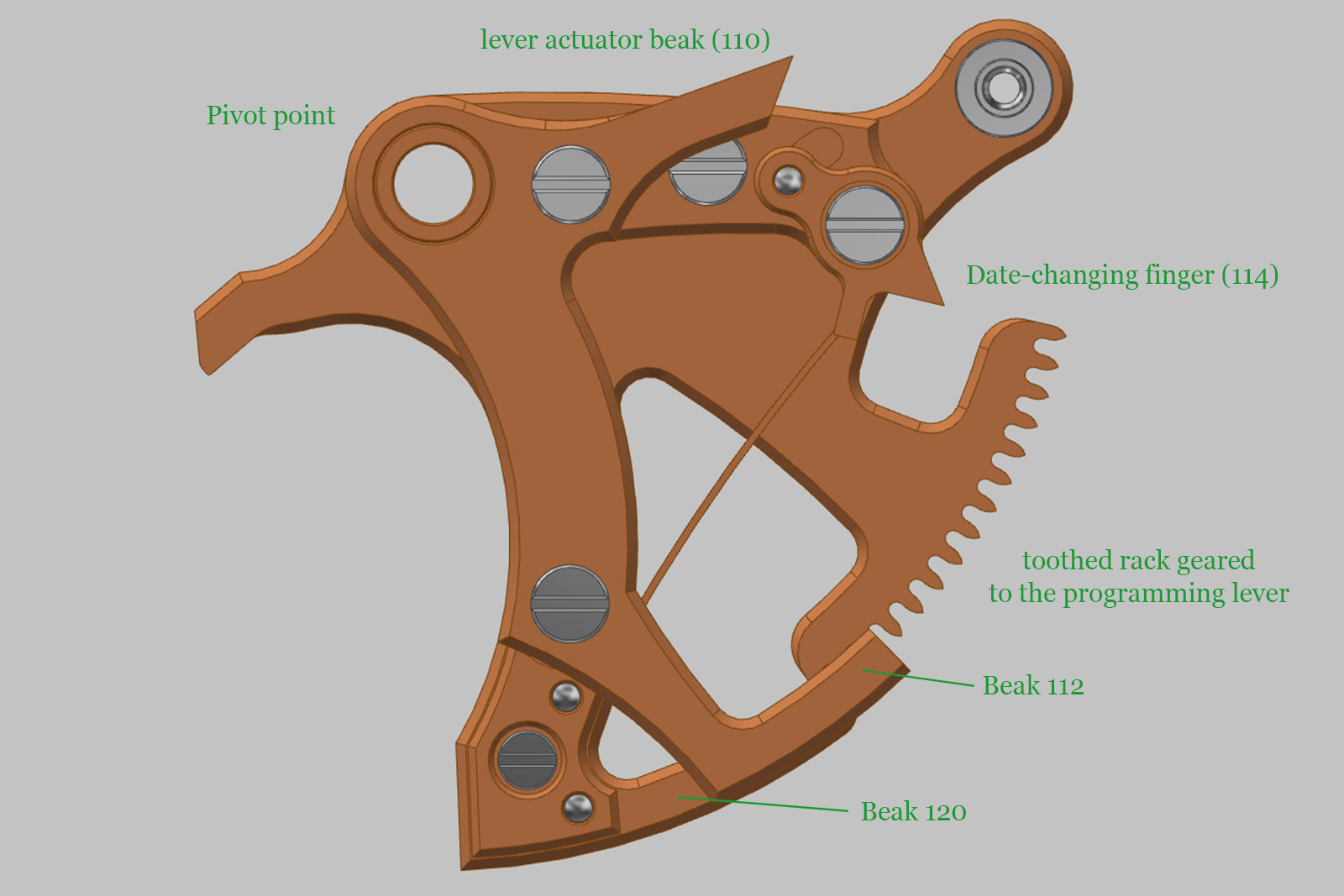
A rendering of the main lever 16 shows the layered and complex construction
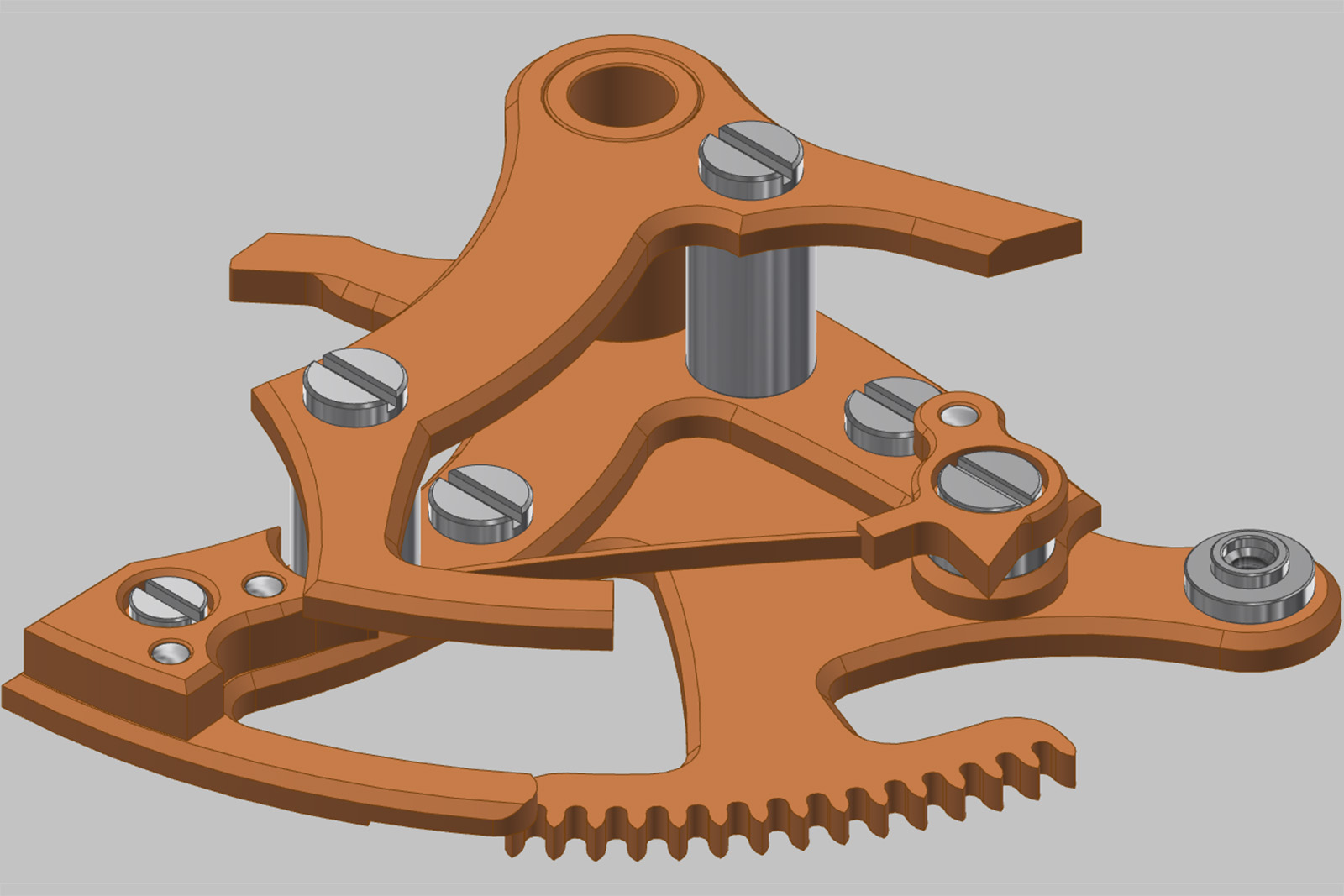
Main lever 16 as seen from an angle
After the date change between the 24th and 25th of a month, a cutout 66 in disc 64 aligns with the beak 120, allowing the beak into the cutout. This marks the start of the programming sequence.
As lever 16 is free to pivot counterclockwise and advance into cutout 66, it drags the programming lever 38 along, by its toothed rack. The motion’s amplitude is limited by the month cam 36. The month cam has an unusual shape; the deepest notches represent 31-day months and allow the widest degree of movement for programming lever 38.
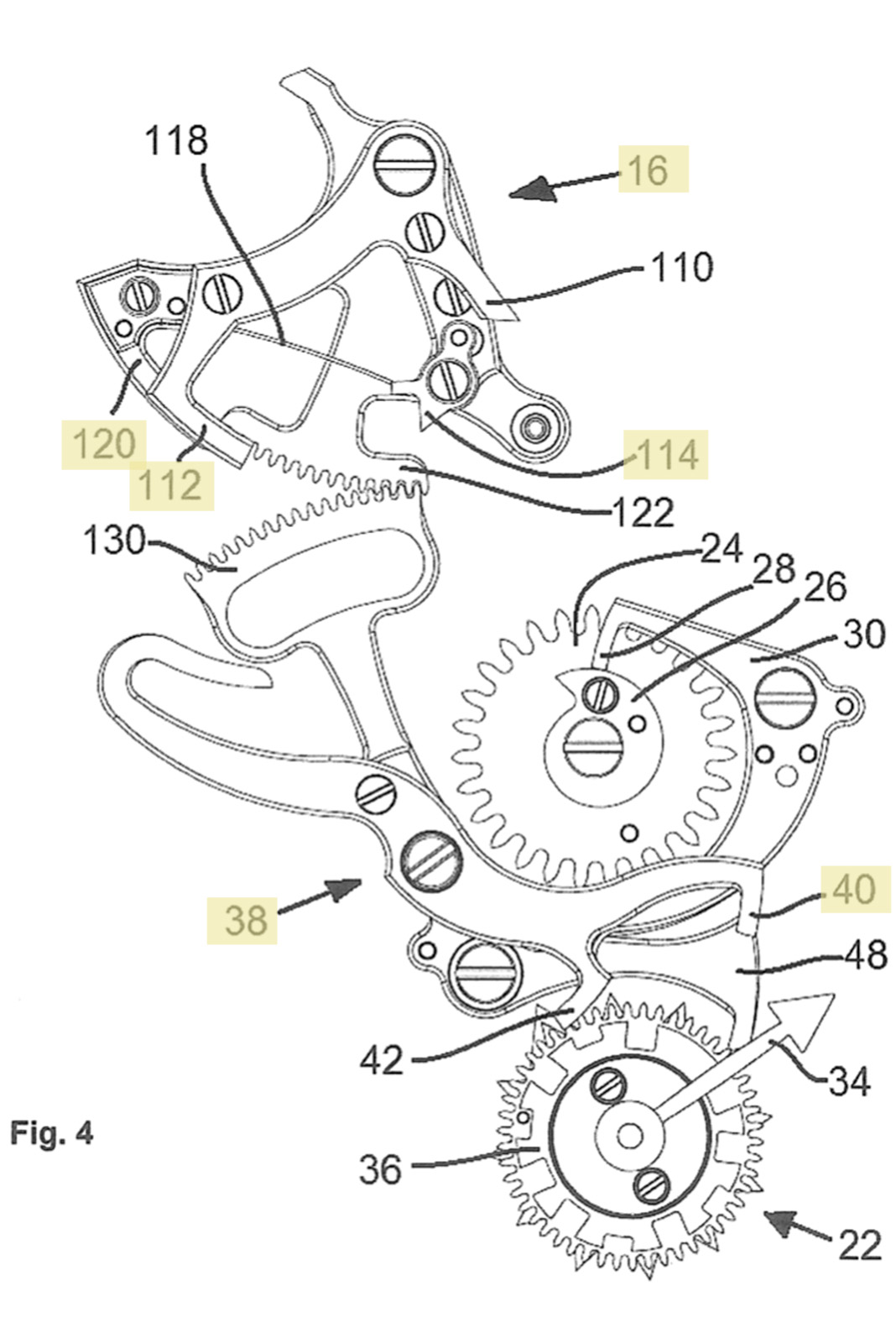
Information is transmitted from the months cam all the way to the mechanical processor
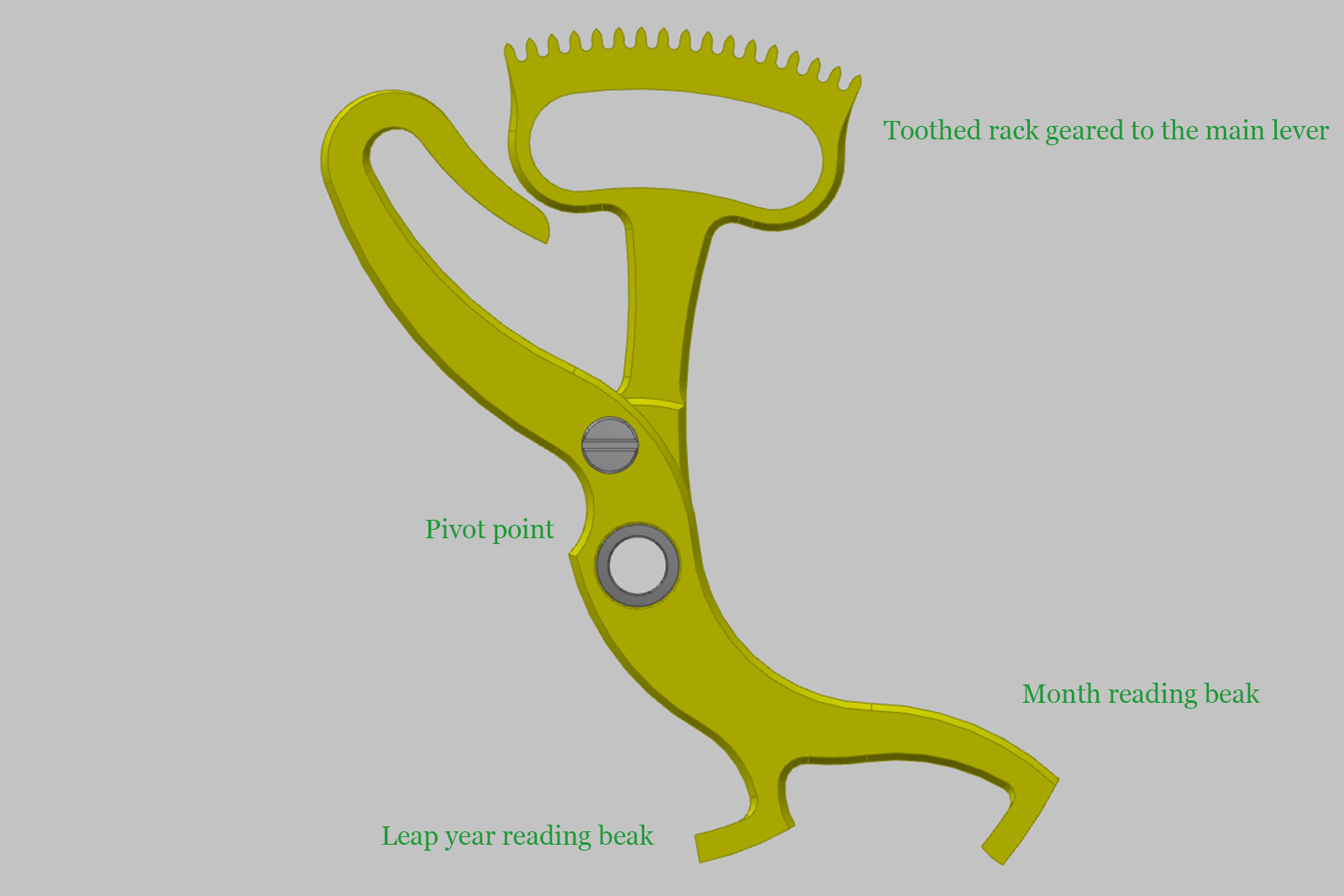
The programming lever
Say the current month has indeed 31 days and the mechanical processor needs to be programmed accordingly. As the beak 120 is inserted into the base of the mechanical processor, another beak 112 acts on the top of the processor. As mentioned, the processor’s movable teeth are kept in place by a conventional click, much like the kind which keeps mainsprings from unwinding. When the programming begins, the sectors are indexed precisely as in Fig. 2c, at the furthest position the click allows.
Beak 112 works directly with the click during the programming. First, the click is momentarily disengaged by the beak, allowing the two sectors to move unimpeded in a clockwise direction. Secondly, the flat face of the same beak 112 pushes on pillar 82 (red), setting it into a new position. The distance travelled by pillar 82 (along with the sectors) depends on the degree pivoted by main lever 16, which in turn depends on the information read by the programming rack from the month cam via feeler 40. This transmits the information from the month cam to the mechanical processor.
For a 31-day month, the levers are allowed a maximum degree of motion, which brings the click to an extreme position. The sectors can now advance four possible steps, the equivalent of four teeth. If the month had 30 days, the lever would have pushed the click over three teeth; if it had 29 days, over two teeth and for the occasional 28-day month, over only one tooth.
This is the outline of the programming process. The programming itself takes place swiftly after midnight on the 25th, but the main lever 16 remains inserted into the mechanical processor for longer. It then is slowly extracted by the 24-hour finger over the course of the following evening. The date jump between the 25th and 26th takes place normally, as soon as the beak 120 is extracted and the mechanical processor is cleared to move.
At month’s end
Freshly programmed, the mechanical processor is now able to correctly compute the month length. Towards the end of the month, the mechanical processor reaches a standstill. More precisely, any prospective date changes between the 27th and 31st of any month are managed by the programmed tooth sectors.
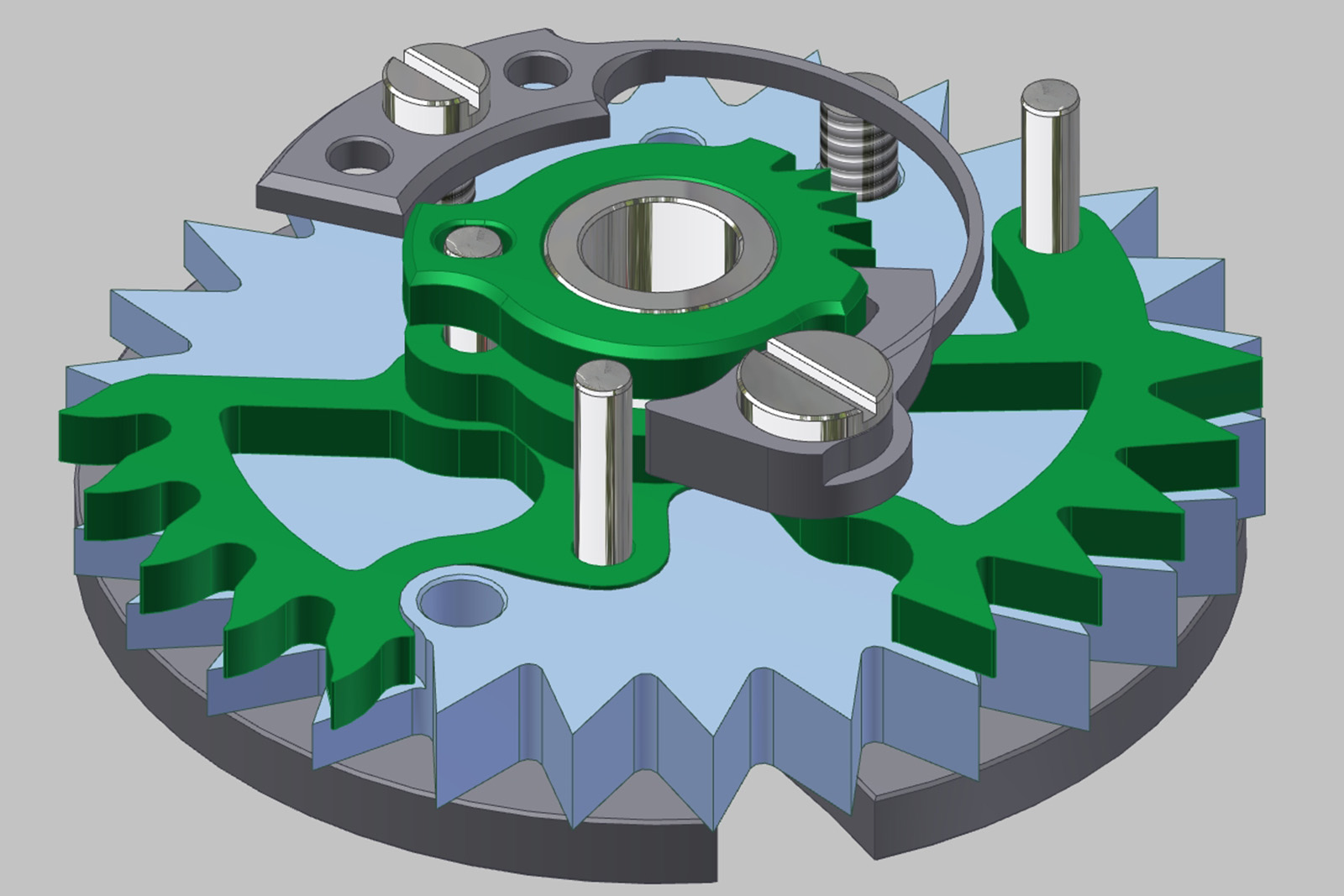
A partially dismantled mechanical processor with the upper gear removed. The sectors are indexed like in Fig. 2c
As mentioned, the uppermost gear of the mechanical processor has a section with missing teeth. Up until the 27th of each month, sector 70 acts like an immovable part of the processor, which itself acts like a common gear.
After the 27th, the command of the date indicator is passed to the tooth sector 70. Sector 68 is conveniently positioned towards the main lever so they can make contact during the date change.
At midnight, when the 24-hour finger engages the lever, instead of the entire mechanical processor jumping forwards, only the two sectors advance by one definite step, limited by the click 92.
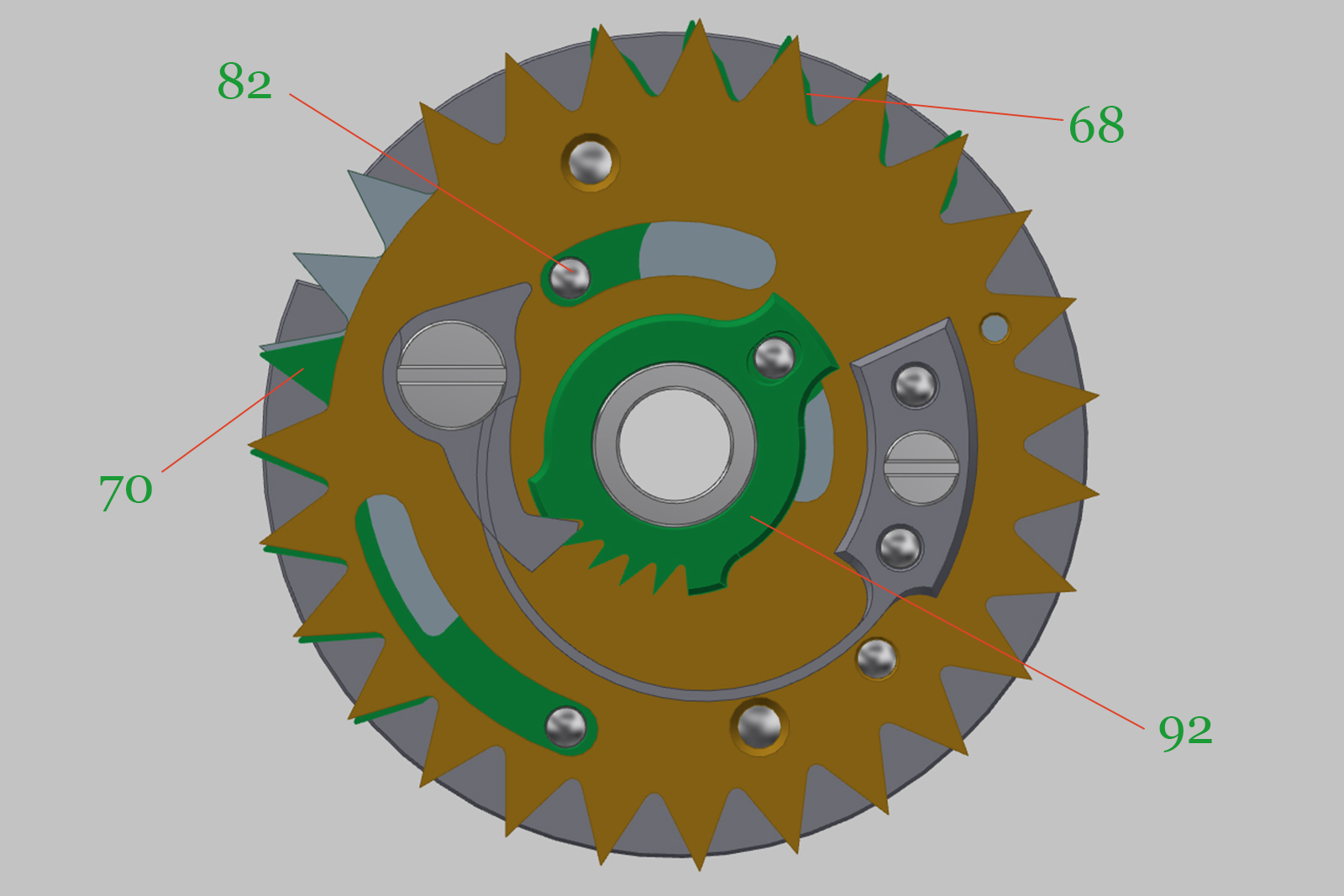
Overhead view of the mechanical processor in the position from fig. 2c
Depending on the programming of the processor, sector 70 can advance between one (for a 28-day month) to four steps (for a 31-day month). As long as the sector is free to advance, the date indicator advances accordingly.
At some point however, the sector assembly reaches its maximum position, arriving in the position in Fig. 2c, which marks the last day of the month. The next date jump forces the entire mechanical processor to advance, as the sectors are slotted and can no longer move on their own. The inactive space frees the retrograde date indicator, allowing it to fly back and indicate the first of the next month.
The action described above is admittedly difficult to grasp, but the trick to understanding it lies in the ability of the mechanical processor to advance sufficiently on its own while the main calendar module remains still. It’s akin to a gear sprouting additional teeth.
Because of this peculiar action, it is crucial that the main processor jumper and click spring are carefully calibrated during assembly so the former is always stiffer than the latter, which ensures the processor doesn’t inadvertently move along with the sectors.
An intermediate month gear, complete with a snail cam, is geared to the processor. The lever (in brown) follows the cam and at the end of the month its beak suddenly drops, advancing the month cam and indicator by one step.
Safety implements
During the programming process a thoughtful safety subassembly locks the calendar pushers on the case band, ensuring the movement is protected from the wearer fiddling with the pushers.
Apart from the inherently-disabled date corrector (as the mechanical processor is kept locked in place by the programming lever), two separate levers lock the year and month correctors. The day of the week corrector, on the other hand, is never locked since it is not involved in the programming process, so can be adjusted without fear at any time.
Each month on the 25th, a special cam on the lowest level of the intermediary month wheel engages the primary safety lever (pink). As the intermediary month wheel slowly rotates in daily steps, the cam’s profile remains in engagement with the primary safety lever over the course of a few days comprising the 25th and a bit after. In turn, the primary safety lever engages two separate systems that disable the month and year correctors during that time.
One beak of the primary safety lever arches around the power reserve indicator and blocks the month corrector. When it’s unlocked, the corrector transmits the user’s adjustments to the month cam-and-indicator assembly via the purple finger. When it’s locked, any adjustment is impossible, as the case correctors remain fixed in position and unresponsive.
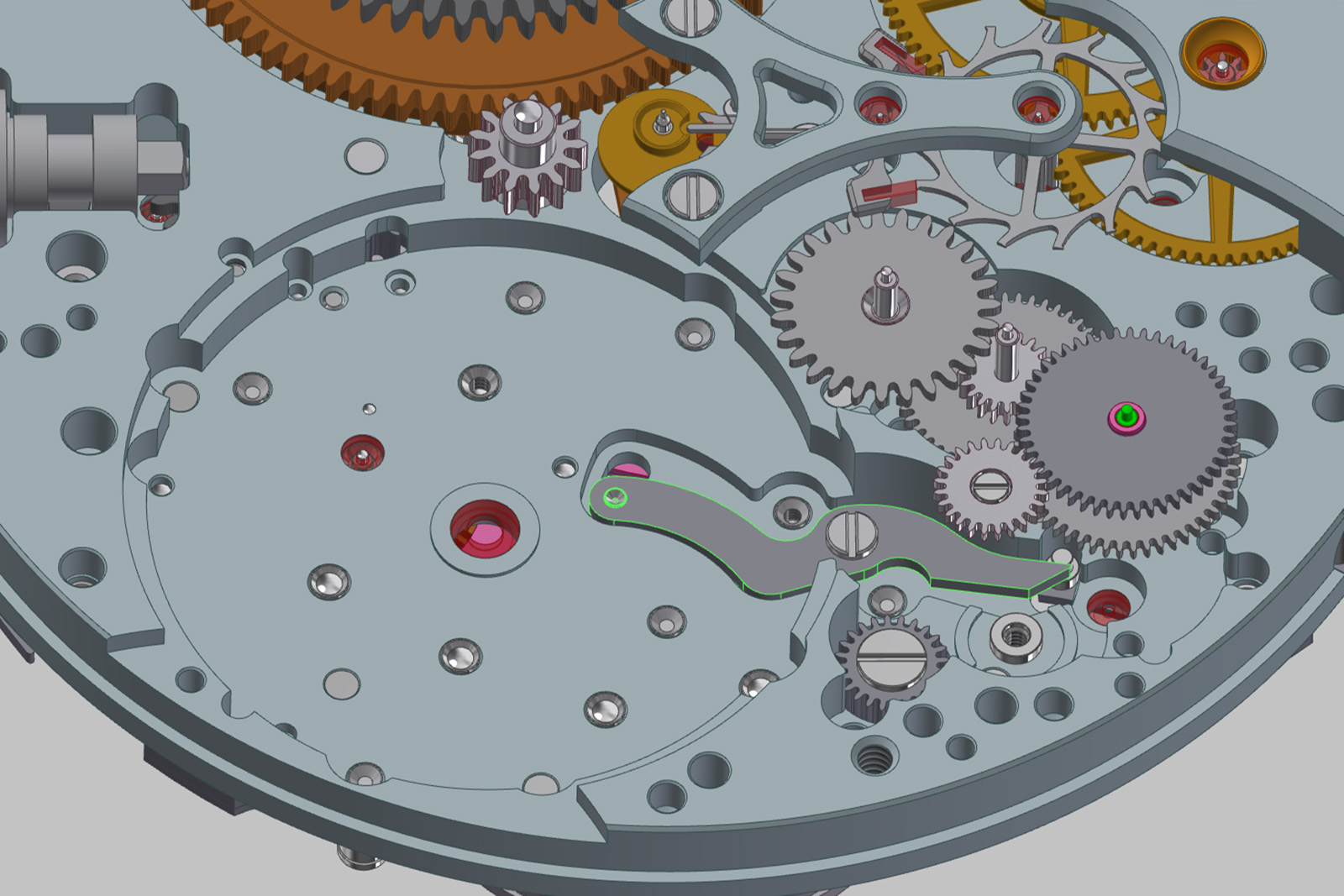
The year corrector safety lever in green
The disabling lever for the leap year corrector is located deeper in the movement. The small lever in green is located under one of the barrels. On the dial side the pink master lever engages a pin, thus pivoting the safety lever. A dedicated beak then blocks the year corrector.
After the 1st of the following month, the pink master lever ceases to engage any of the safety systems, effectively unlocking the correctors. As every lever is individually sprung, everything falls back into place.
An unlikely British connection
The novel construction of the LM QP, particularly its concealed retrograde date function, brings to mind an especially important pocket watch.
Retrograde perpetual calendars are uncommon, but part of the catalogue for several important brands, including Patek Philippe and Vacheron Constantin. Interestingly, adding a retrograde function to a date display (and it is usually the date indicator that is retrograde), is straightforward and can be done without affecting the main calendar works, leaving the rest of the calendar mechanism entirely conventional, with a 48-tooth disc and grand lever. In other words, retrograde indications generally do not have anything to do with the computing of months.
In comparison, the LM QP’s concealed retrograde display actively works with the mechanical processor to calculate the lengths of each month. This is one of the movement’s unique traits, but it has a notable historical precedent.
Another important timepiece with a perpetual calendar that incorporates a retrograde date actively involved in the mechanical computation of the calendar is the George Daniels Grand Complication pocket watch.
Although best known for inventing the co-axial escapement, Daniels also quietly reimagined several classical complications, amongst them the perpetual calendar. However, he only equipped one watch, the Grand Complication, with his unusual perpetual calendar mechanism.
Not unlike the MB&F LM QP, the Daniels perpetual mechanism takes advantage of the retrograde date’s ability to jump back to its starting position. In Daniels’ invention, the retrograde hand can be triggered before reaching the 31st of the month, if it is a month with less than 31 days, by a simple lever and a fairly conventional 12-month cam.

The Daniels perpetual calendar with the retrograde mechanism at the right of the main plate. Image – Roger W. Smith
The operation of the mechanism is similar to the LM QP, although less refined in execution (which is perhaps unsurprising since most of Daniels’ pocket watches were akin to a one-off prototype). The LM QP’s operation is more streamlined and secure, requiring little to no adjusting during assembly. Its mechanical processor acts as a convenient buffer between the months cam and month indicator, while Daniels’ system is as straightforward as possible and even slightly crude.
Daniels’ approach is laudable conceptually, but is too bulky for a wristwatch. Although Daniels realised his innovative perpetual calendar system only once, American watch and clockmaker David Walter adapted it for use in table and standing clocks.
Concluding thoughts
The LM QP is clearly an exceptional timepiece, even on the surface. The recognisable aesthetic and high quality decoration have made it a staple in modern independent watchmaking. But beyond its styling, the LM QP is arguably a revelation in terms of mechanics.
The calendar mechanism system is sufficiently elegant and well put together that it almost becomes art in engineering. Though its complexity makes it difficult to fully comprehend and even more difficult to explain, the LM QP captures a stroke of genius.
Stephen McDonnell should be remembered in the horological hall of fame as an original thinker who mastered the perpetual calendar. The fact that his creation echoed one of the late George Daniels’ only proves that great minds think alike.
This was brought to you in partnership with The Hour Glass, the MB&F retailer in Southeast Asia and Oceania.
Back to top.