Insight: High-Tech LIGA Within the Rolex Daytona Cal. 4130
Incremental improvements for exceptional longevity.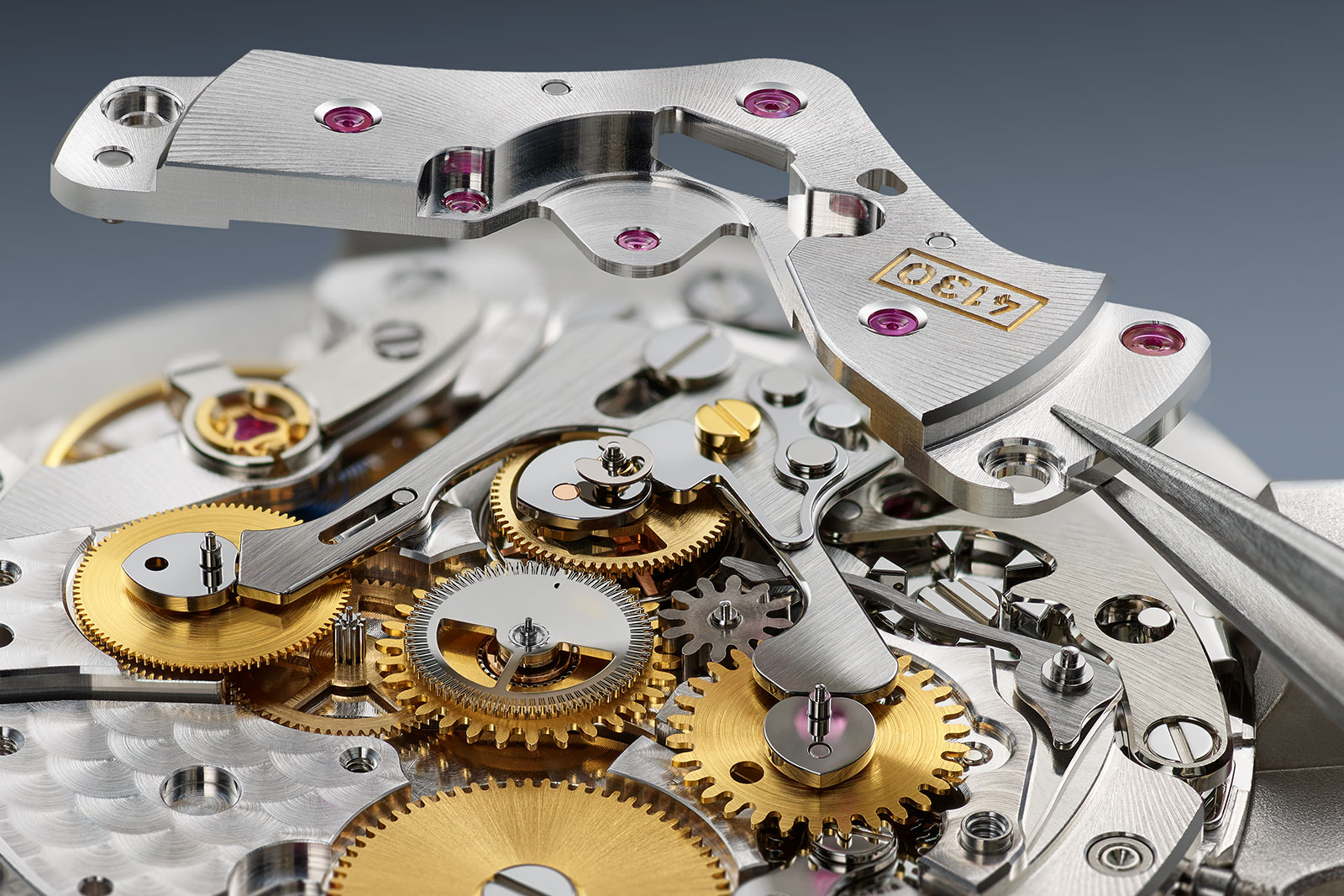
In-house movements are common in modern watchmaking, and practically the norm at the biggest brands. But new movements are usually developed to replace existing calibres, making 21st century movements with lifespans of decades fairly uncommon. Such mechanical longevity, on the other hand, is only possible with consistently implementing incremental but significant technical upgrades.
Perhaps more than others, Rolex has perfected the art of carefully engineered movements that remain in production for many, many years thanks to incremental upgrades. The sheer scale of Rolex as a manufacture doubtlessly plays a big role in making that possible.
Producing close to a million watches a year, according to estimates by banks Vontobel and Morgan Stanley – and owning almost all of its distribution and after-sales service network – Rolex certainly possesses tremendous data on the performance of its movements over prolonged, real-world use. Such information would be invaluable boosting the performance of its movements as well as extending the longevity of the calibre designs.
The Cosmograph calibre
One such long-lived movement is the cal. 4130 that debuted inside the Cosmograph Daytona in 2000. Over its two decade production run, the chronograph calibre – featuring both a column wheel and vertical clutch – has undergone four key technical updates according to Rolex, all of which are found in the cal. 4130s produced today.
[And any Daytona with earlier versions of the cal. 4130 returned for servicing may have the upgrades swapped in, if the part in question “doesn’t meet Rolex requirements” says Rolex.]
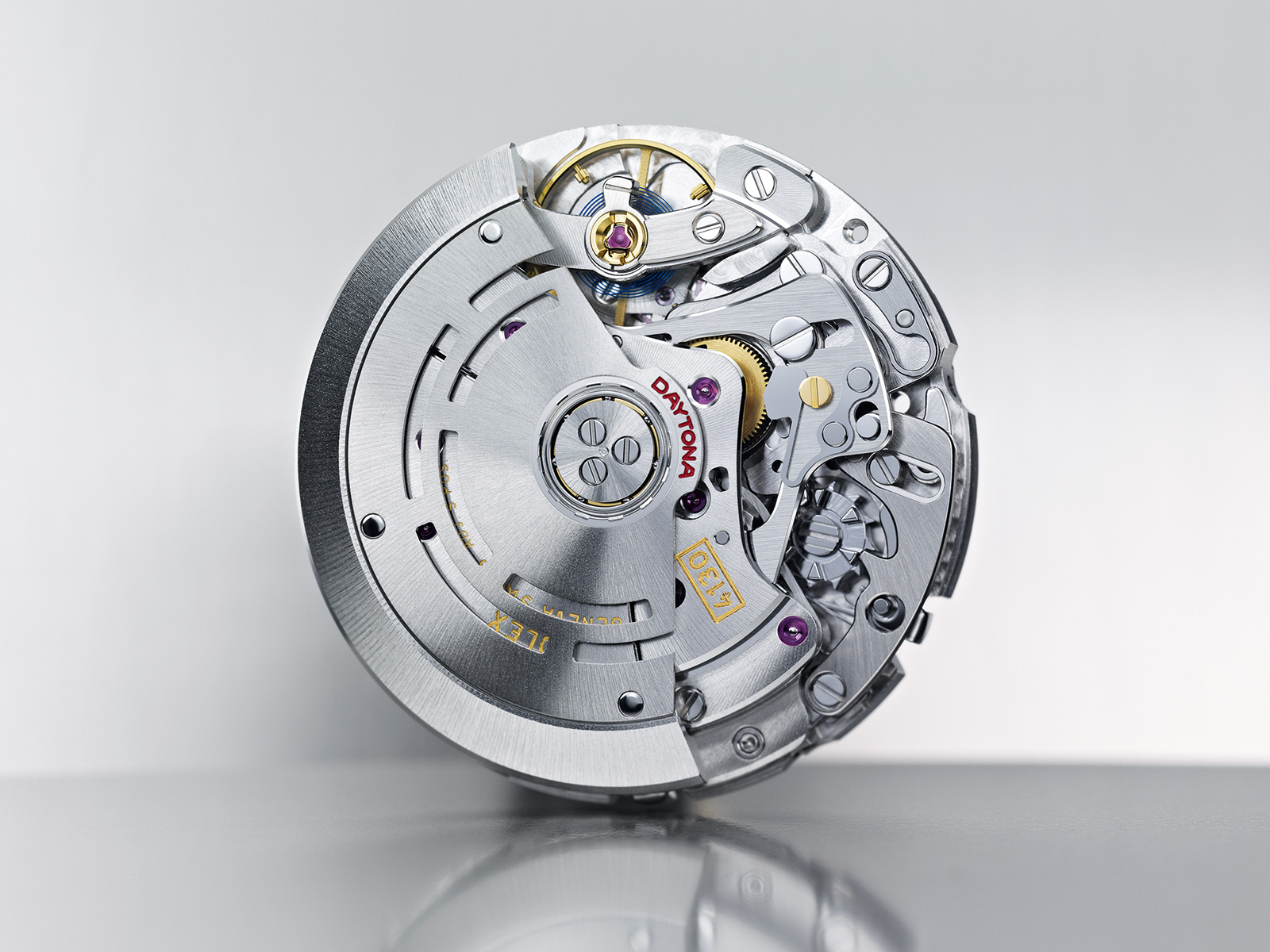
The cal. 4130
One of the more recent upgrades to the movement is an unusual wheel that drives the chronograph seconds. Hidden under the automatic-winding bridge, the wheel is not visible to anyone except for the watchmaker, but it is intriguing. Featuring finely-skeletonised teeth, the wheel has a curious, almost organic appearance.
While such skeletonised wheels are not unique to Rolex – the technology used to fabricate it is available to most of the watch industry – the wheel in the cal. 4130 is especially intricate, with each tooth made of three parts. On a broader level, it is also worth delving into why such wheels are increasingly found in watches, despite traditional gear teeth having been eminently functional for centuries.
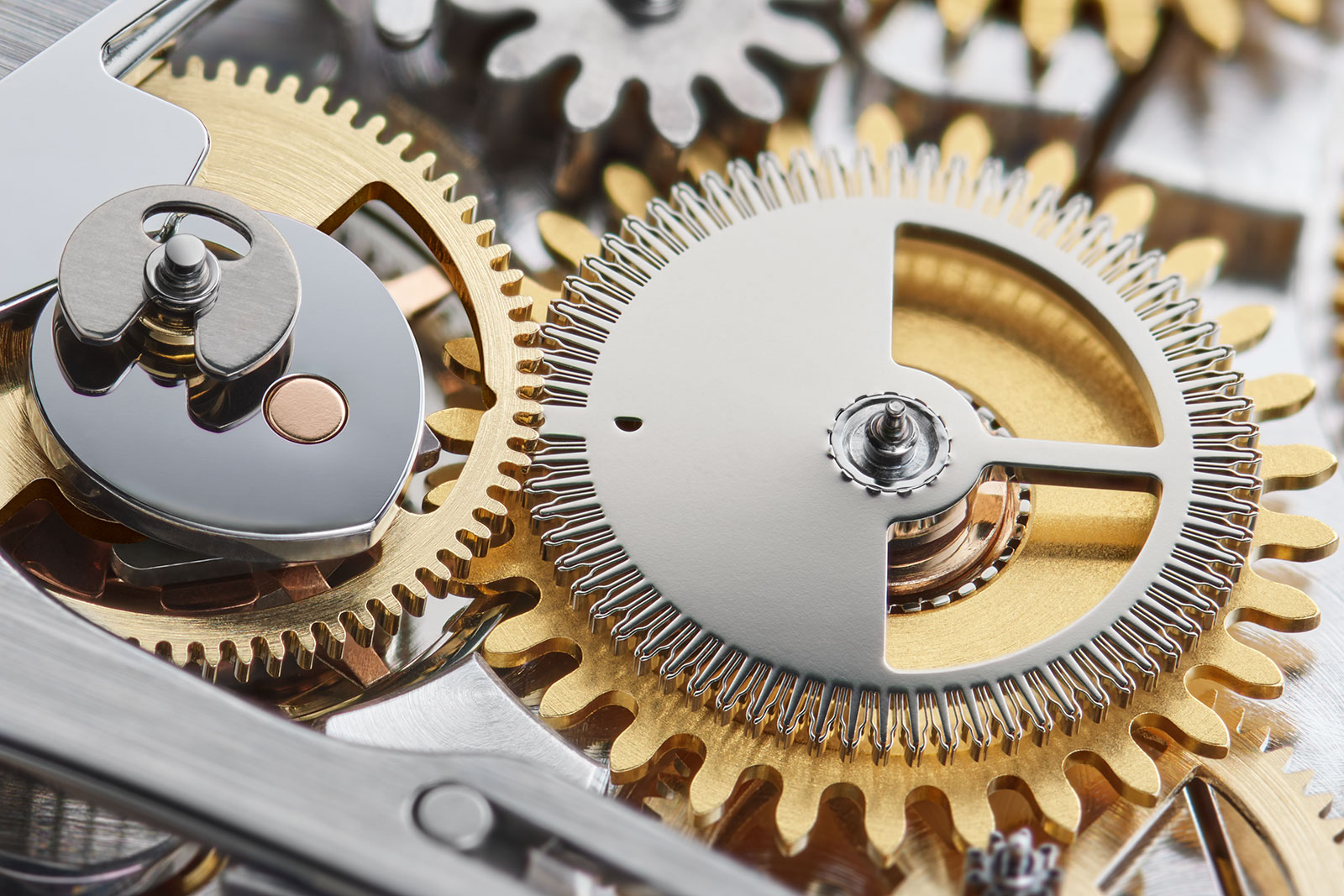
The curious wheel (right)
High tech, micro sized
The chronograph seconds wheel in the cal. 4130 has individual teeth made up of cantilevered springs, which flex inwards when the wheel meshes. Each of the sprung teeth fill any possible gaps between the meshing teeth of the wheels, ensuring full surface contact with no play or backlash during the chronograph’s operation.
Its incredible shape is the product of a modern fabrication technique known as micro-electro-mechanical systems (MEMS). Unavailable until fairly recently in terms of watchmaking history, MEMS developed alongside the evolution of semiconductor technology starting in the 1960s.
As the name suggests, MEMS is the study of microscopic mechanical and electronic components, with the micro-mechanical aspect being most relevant in watchmaking. The MEMS process known as LIGA, the German acronym for Lithographie, Galvanoformung, Abformung (“lithography, electroplating, moulding”) is responsible for the intricate wheel in the cal. 4130.
An additive fabrication process, LIGA grows metallic parts galvanically on a disc within tiny resin moulds. Starting with a precise mould, equally precise metallic parts with complex planar geometries can be formed, several dozen at a time, making the process perfect for manufacturing gears, which are flat, planar, and required in sizeable numbers.
The process starts with the production of a precise mask of the required parts (each mask will result in several dozen identical parts). Laid on top of a thin layer of resin on a disc, the mask is then exposed to either X-rays or ultraviolet light. UV exposure is more practical and common when producing watch parts, which is why the process is commonly known as UV-LIGA in horology.
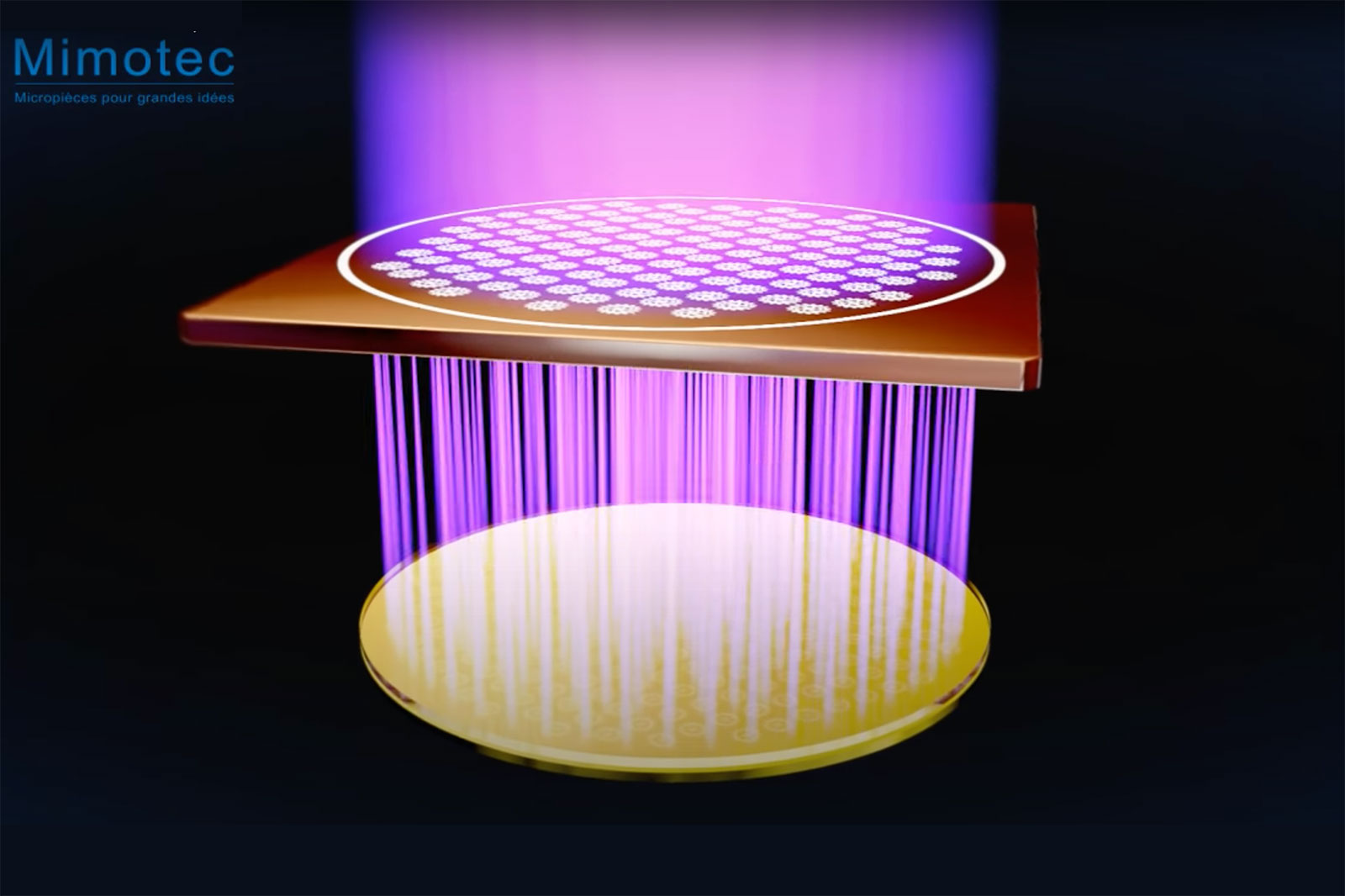
Creating the individual resin moulds with UV light. Image – Mimotec
The mask acts as a stencil for the UV light, which penetrates the portions not covered by the mask, hardening the exposed resin via polymerisation. The remaining, soft resin is then dissolved with a solvent, leaving only the hardened resin as a miniature mould of the desired part.
Then the mould is immersed in a galvanic bath – a chemical mixture used for electroplating – and metal, often a nickel alloy, is deposited into the cavities of the mould. Layer of metal are plating into the cavities, building up the parts. Once complete, the disc is lapped, or polished, to reduce its height to the desired thickness. Finally, the resin mould is dissolved, leaving the finished metal components with perfect geometries and tolerances, meaning no hand finishing or adjustment is needed.
[A video of the process courtesy of UV-LIGA specialist Mimotec is instructive and can be found here.]
A surprisingly complex process for tiny components, UV-LIGA’s ability to create impressively intricate micro structures is well illustrated by the seconds wheel of the cal. 4130. Components with this level of intricacy are impossible to fabricate with traditional manufacturing processes like stamping or wire erosion.
Consequently, wheels with built-in springs have only been realised in recent years in watchmaking, thanks to UV-LIGA and MEMS. While such specialised wheels are found in movements beyond the cal. 4130, it is particularly useful in the cal. 4130, which is a chronograph movement with an inventive construction.
Vertical clutches
The UV-LIGA wheel in the cal. 4130 is the chronograph seconds wheel – making one revolution a minute when the chronograph is engaged.
With the chronograph seconds hand mounted on the wheel, the wheel has to function in a precise manner, such that the chronograph seconds hand starts, travels, and halts smoothly, in order to facilitate spot-on reading of the elapsed seconds. There cannot be any any “play” or backlash in the motion of the wheel, which would result in stutter or misalignment of the seconds hand against the markers on the dial.

The UV-LIGA seconds wheel (bottom left), and the vertical clutch just above it
Alignment and motion of the seconds hand is routinely cited as a key reason for having vertical clutch in a chronograph. Essentially a mechanism that engages in order to transmit power from the base movement to the chronograph mechanism, the vertical clutch eliminates seconds hand “stutter”, a crucial advantage over its predecessor, the horizontal clutch.
As the name indicates, the horizontal clutch meshes two gears laterally on the same plane, which may cause the teeth of one or both gears to slip when meshing, causing the chronograph seconds hand to jerk forward, or “stutter”, when the chronograph is started.
The vertical clutch, on the other hand, functions much like the clutch of manual transmission in a car. It consists of two stacked wheels that can rotate independently from one another. One wheel is continuously driven by the movement, while the other powers the chronograph seconds hand and is stationary when not in use.
The operation of the vertical clutch is straightforward: pressing the chronograph start button causes pincers to release the spring-loaded clutch, resulting in the spring pressing the clutch downwards. The clutch then contacts the face of the continuously-driven wheel, and friction of the mating faces causes both to rotate together. Because the chronograph seconds wheel is part of the clutch, the seconds hand starts turning as well – the chronograph is in operation.
A vital step in that process is the engagement of the two faces. Since no teeth mesh when it starts or stops – the two are seamlessly coupled and then driven by friction – there is no “stutter” during the engagement process.
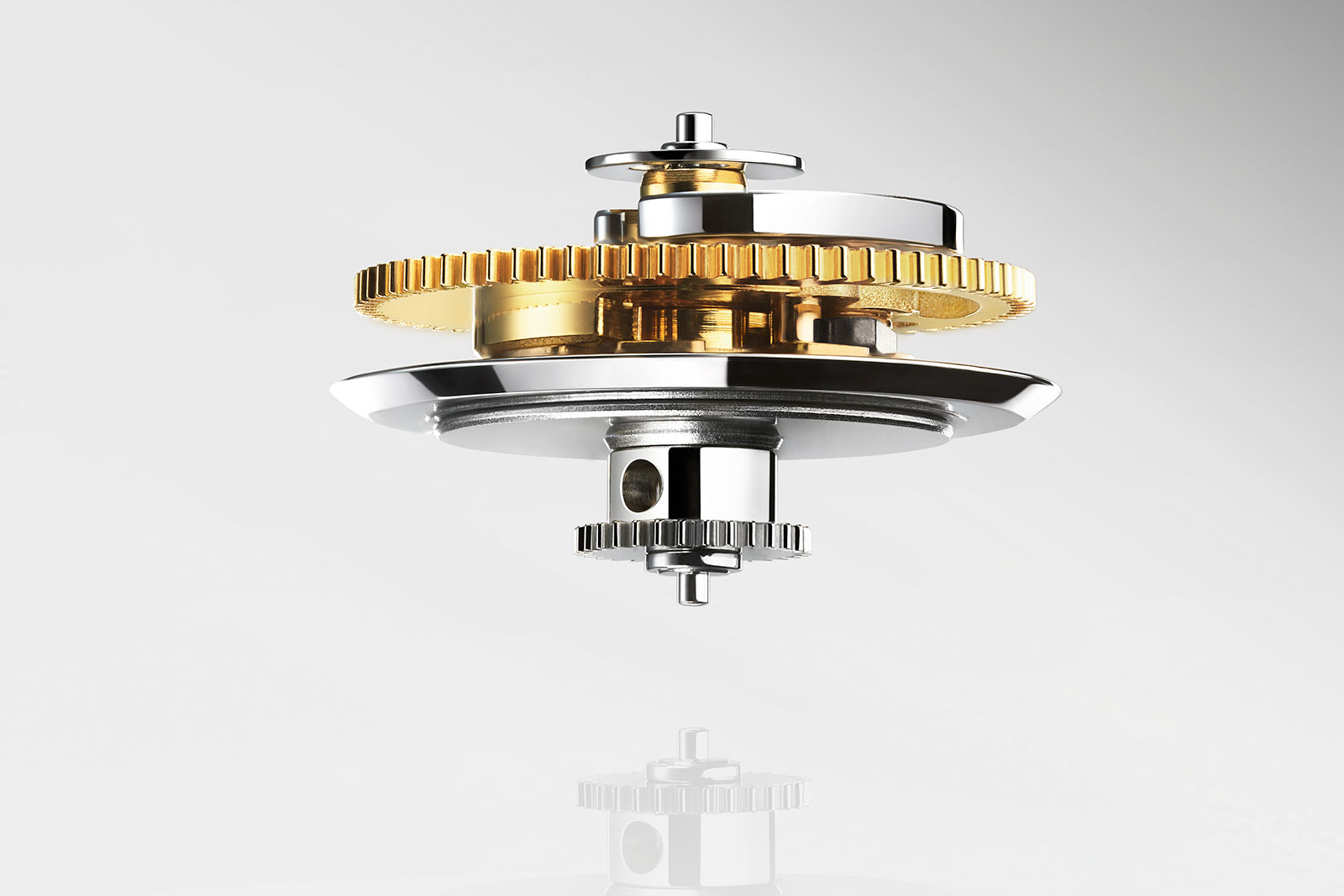
The vertical clutch of the cal. 4130 with the gilded chronograph seconds wheel on top, and the continuously-driven wheel below. Photo – Rolex/Joël von Allmen
Vertical-clutch configurations
Why then, does the cal. 4130 require the stutter-eliminating UV-LIGA wheel if a vertical clutch chronograph doesn’t suffer from the problem in the first place?
The answer lies in the novel construction of the cal. 4130. Despite being a chronograph, the timekeeping going train of the cal. 4130 is arranged as it would be in a conventional movement. Its subsidiary seconds is at six o’clock and directly driven by the going train. This is achieved by having the fourth wheel – which is connected to the constant seconds hand and rotates once every 60 seconds – located exactly under the the sub-seconds register.
In contrast, most vertical-clutch chronographs have the fourth wheel right in the centre of the movement, which is the de facto standard since the fourth wheel makes one revolution a minute, allowing it to directly drive the seconds hand. In such constructions, the fourth wheel is integrated into the vertical clutch assembly.
Though common, this configuration comes with a caveat: if a subsidiary seconds is needed, as is convention with chronographs, then additional gearing is needed to relocate the seconds from the centre to a sub-dial. In short, the simpler chronograph mechanism is accompanied by the extra complexity of the indirect seconds.
The designers of the cal. 4130 took the decision to position the fourth wheel at six o’clock in order to have a directly-driven subsidiary seconds. But at the same time, the chronograph seconds is indirectly driven, since the fourth wheel is far from the centre of the movement.
One possible reason behind the unconventional layout was efficient use of space. Placing the fourth wheel at six o’clock leaves the central portion of the movement free for the chronograph minutes and automatic winding mechanism, resulting in a calibre that’s as slim and compact as possible.
The construction of the cal. 4130 has its vertical clutch driven indirectly via a secondary gear train sitting just above the fourth wheel. The vertical clutch, in turn, drives the chronograph seconds wheel when it is engaged.
These additional wheels can result in play between the teeth when they mesh, which may result in “stutter” of the chronograph seconds hand – which is where the UV-LIGA wheel steps in to save the day. The wheel makes it possible to have a secondary going train and an indirect seconds with zero “stutter”, which would have been unimaginable without UV-LIGA parts.
Another upside of the UV-LIGA wheel is doing away with the tensioner spring for the chronograph seconds wheel. Traditionally installed to keep a modest amount of force on the wheel, the tensioner spring prevents “flutter” or jerking, caused by backlash when the wheel rotates. While the tensioner spring allows for crisp motion of the wheels and hands, it generates friction, creating wear and energy loss.
Since UV-LIGA wheels eliminate backlash, the tensioner spring is unnecessary, which then reduces the frictional load on the movement and unnecessary wear under the wheels. That said, UV-LIGA wheels do operate with marginally greater friction due to the tighter meshing of the sprung, skeletonised teeth. But the increase in friction is minuscule, and does not impact the power reserve of the movement.
Progressive innovation
Invisible, incremental upgrades like the UV-LIGA wheel are testament to Rolex’s commitment to the longevity of its movements that need only the occasional nip and tuck as new technology emerges to make them better. Rolex excels at this, in part due to the large pool of watches sold and serviced, as well as the company’s institutional culture of planning for the very, very long term.
As many of its peers roll out new movements on a regular basis, it is almost a certainty that Rolex has rolled out similar upgrades across all its longstanding movements, albeit in the discreet manner that is a hallmark of the company. As to why incremental upgrades instead of an entirely new calibre, the age-old adage comes to mind: if it ain’t broke, why fix it?
Back to top.