In-Depth: Greubel Forsey Hand Made 1 Tourbillon
Exceptional execution.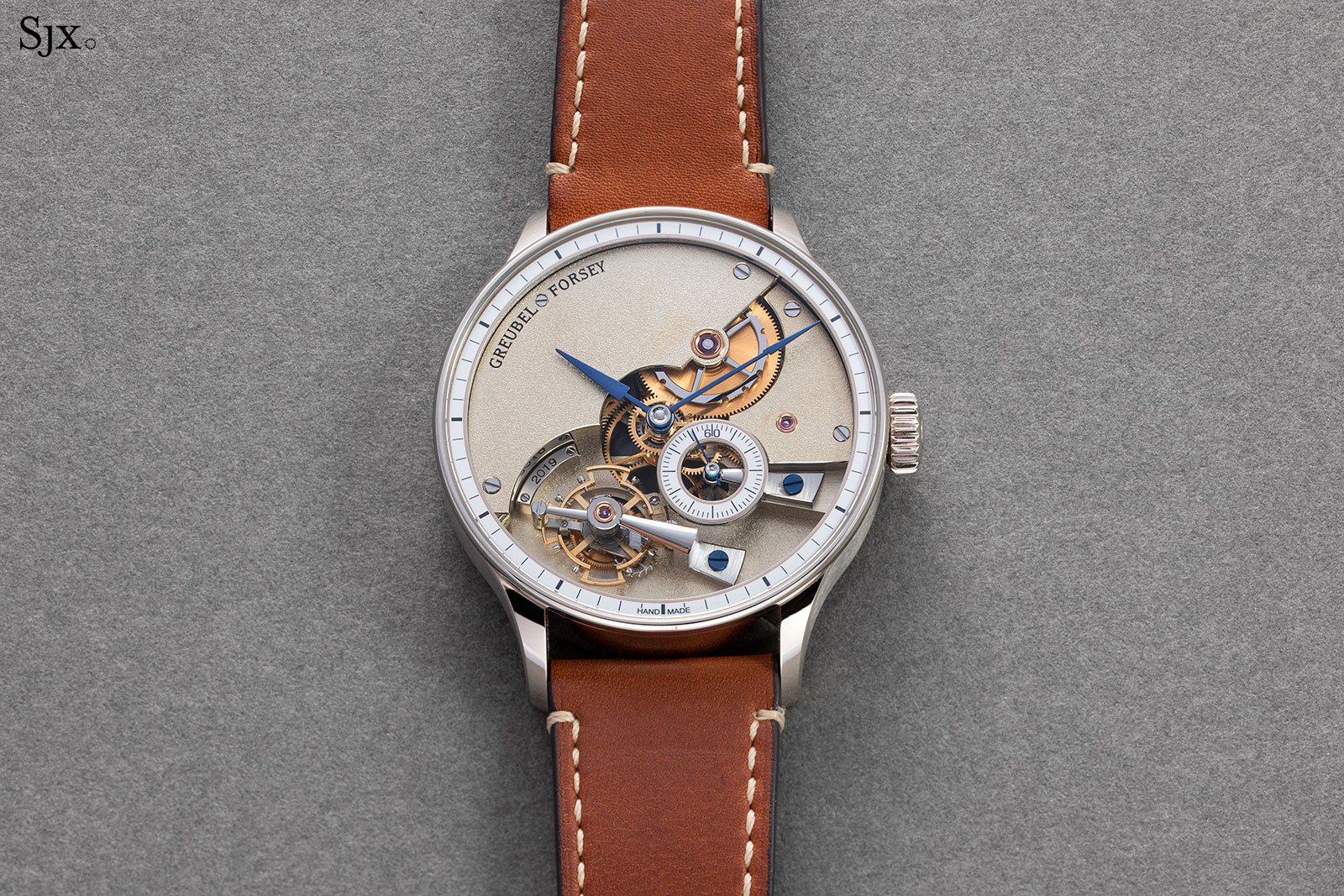
Greubel Forsey unexpectedly debuted the Hand Made 1 in 2019, but the watch has recently been in the headlines because Facebook founder Mark Zuckerberg was wearing one while announcing the elimination of Meta’s fact-checking policy. So it’s an opportune time to revisit the Hand Made 1, especially since its successor may be on the horizon.
More classical in style than the typical Greubel Forsey, the Hand Made 1 gets its name from the fact that entire watch, including the case, is “95%” produced “using only hand-operated tools”, but finished to the requisite high standards of the brand. “Robert and myself wanted to bring the level of reliability and performance of a modern watch, so we have imposed the tolerances of a Greubel Forsey timepiece on a hand-made watch,” explains Stephen Forsey, cofounder of Greubel Forsey.
Initial thoughts
Highly regarded for its elaborately-finished and often elaborately constructed watches, Greubel Forsey surprised with the Hand Made 1. While still equipped with a tourbillon regulator, the Hand Made 1 is simple relative to the brand’s usual fare, which is focused on inclined regulators and multi-axis tourbillons.
While the Hand Made 1 is different from most Greubel Forsey offerings, it is similar in possessing a sheen of perfection. This is immediately apparent with the watch in hand. Every edge and surface in the movement looks perfect, even under magnification. This sets it apart from the average “hand made” watch, which usually reveals the imperfections that inevitable with manual production.
That’s because the Hand Made 1 is comprised of components made by hand, and then finished in the typical Greubel Forsey manner. The result is near-perfect decoration, but also near-perfect tolerances and interchangeability of parts – neither of which is a given in traditional hand-made movements.
According to Greubel Forsey, each Hand Made 1 requires 6,000 hours of work – equivalent to three years – an extraordinary length of time even when considering some of it is marketing. The number, however, is reasonable given that George Daniels is though to have taken about 3,000 hours to complete one of his hand-made watches, which were essentially prototypes and not decorated to the same level (or at all, depending on how you see it).
While such artisanal watches are typically made by single-man outfits or small-scale independents, Greubel Forsey is a company with about 100 employees.The combination of hand-made and Greubel Forsey techniques means the Hand Made 1 is extremely expensive, even by the standards of ultra-high-end horology.
The price tag of US$900,000 is a result of Greubel Forsey’s institutional scale, associated costs, and margins for retail channels. A talented individual watchmaker operating out of a home-based workshop selling direct to consumer could – presumably – produce something similar for a lower price, since the cost is primarily labour and time.
The Hand Made 1 also demonstrates the limitations of “hand made”, especially with the case. While the case is of impeccable quality, it is simple in form and finish because it was hand made. The complex, oddly shaped cases employed by other Greubel Forsey watches cannot be hand made with the same techniques.
The Hand Made 1 is an impressive watch in all tangible respects. I can’t find any flaws in the execution. I also believe Greubel Forsey’s claims of the time and effort required to produce the watch; each Hand Made 1 is unquestionably a tedious, labours undertaking.
That said, I don’t find it as interesting as Greubel Forsey’s more conventional creations. Those watches are quintessential Greubel Forsey in having unusual regulators and oversized cases with the occasional bulge. The Hand Made 1, in contrast, impressively hand made and finished, but not uniquely Greubel Forsey.
On a philosophical level, the Hand Made 1 also raises the question: what is ideal? The combination of hand made, quality, and complexity, then the resulting aesthetic, price, and appealing. The Hand Made 1 answers that by taking hand made and quality to the extreme, along with the price.
Made by hand
At a distance, the Hand Made 1 doesn’t really resemble a Greubel Forsey. It’s relatively compact, just 43.5 mm wide and 13.5 mm high, with a clean, classical silhouette.
Up close, it does reveal the three-dimensional face that is something of a Greubel Forsey signature. Though the movement is simple in mechanical terms, it has been constructed for a layered, intricate appearance on the dial.
One of the classical elements that stands out is the visible Maltese cross gear on the barrel that serves as a stop-work mechanism for the mainspring. This prevents the mainspring from being overwound or wound to the maximum, but it is equally a design element with its black polished face and chamfered spokes.
According to Michel Nydegger, Greubel Forsey’s chief executive, one of the fundamental challenges in creating the Hand Made 1 was its conception.
“Because we became quite used to designing with [computer-aided design], we forgot about the constraints of traditional making,” says Mr Nydegger, “From the foundations of the construction, it was developed to show off finishing and be able to be hand made”.
“We started with sketches on paper,” continues Mr Nydegger, “It wasn’t the idea to remake an existing calibre using hand-made tools, but to apply our own criteria of reliability, performance, finishing, but doing it with hand-made tools.”
The Hand Made 1 is “95%” fabricated with “only hand-operated tools”, including the case, crown, and strap. Mr Forsey defines that as:
“First, any part that is hand made does not have any CNC machine intervention. Second, finishing has been done by hand. Third, it should be assembled and adjusted by one watchmaker. Fourth, the watch needs to be 90% at least hand made, either numerically or by numbers of hours.”
Examples of “hand made” parts are screws turned individually on a lathe, gears cut manually, while the bridges and case parts produced on a manual pantograph, which is essentially a hand-operated milling machine. Even the hairspring is rolled by hand, progressively getting flatter until it reaches the required thickness.
In fact, Greubel Forsey states that the only components not made that way are the “sapphire crystals, the case gaskets, the spring bars, the jewels, and the mainspring”. Notably, some of the components, like the hairspring and escape wheel, are made by external specialists, most of whom worked for Greubel Forsey in the past.
Engraving the plate bearing the year of manufacture with a hand-operated pantograph. Image – Greubel Forsey
The engraving is then filled with black lacquer and then decorated with concentric brushing and chamfering
The balance wheel was particularly challenging according to Mr Forsey.
“There are two ways to make a balance wheel, on a precision lathe, or on a jig borer,” explains Mr Forsey, “Most of this was done on the jig borer, which enabled us to get the balance wheel more precise, as we were able to offset the possible imprecision of the hand making process against having the advantage of machining it at one go.”
“Serially made balance wheels are stamped out on a press,” he adds, “But even for those you have some that are few thousandth of a millimetre out of centre.”
Turning the balance wheel. Image – Greubel Forsey
Mr Nydegger cites “the barrel bridge with scalloping is easy to do with CNC milling, but when done by hand it requires several different operations as each scallop has to be centred on a jig borer and then the scallop cut.”
Screws are another example. The Hand Made 1 consists of 24 types of screws, totalling 83 screws. “Nobody wants to make the screws,” says Mr Nydegger, “Screws are challenging, small and fiddly, and there are 12 operations to finish one screw – it’s almost a punishment for the watchmaker!”
Stacked escape wheel blanks prior to teeth cutting. Image – Greubel Forsey
The escape wheel after teeth cutting. Image – Greubel Forsey
A raw escape wheel before the faces of the teeth are polished. Image – Greubel Forsey
Producing the components with manual methods is so time-consuming that two-thirds of the 6,000 hours required to complete a Hand Made 1 is sole for fabrication of parts, with the remaining 2,000 for decoration.
Such “hand made” techniques, however, are not novel. At small artisanal watchmakers such techniques can be the norm, but at big watch brands, these methods are only employed to create prototypes and practically never used for serially produced watches. “Stephen [Forsey] and Robert [Greubel] hand-made prototype parts 21 years ago [when the brand was established, but they] couldn’t find people with the skills to make sufficient parts for serial production,” says Mr Nydegger.
According to Mr Nydegger, the hand-made approach meant the Hand Made 1 was developed and produced in “more collaborative” manner, and tapped on expertise gained from Naissance d’Une Montre and Time Aeon, past projects dedicated to traditional watchmaking crafts that Greubel Forsey supported.
“Watchmakers and micro-mechanics [specialists with[ experience from Naissance d’Une Montre and TimeAeon.. came forward asking to do similar work [with the Hand Made 1]”, he adds.
Prototyping for testing and development doesn’t result in a proper watch fit for sale, which dictates superior tolerances and finishing. Consequently, the components that make up a Hand Made 1 are hand made, but executed to a higher level, akin to the standard found on Greubel Forsey’s “standard” watches. This results in a high rejection rate for the parts: the movement and case of a Hand Made 1 are comprised of 308 parts, but over 800 components are produced and the rest discarded, according to Greubel Forsey.
The precision and tidiness that results from this approach is evident when examining the movement up close. It certainly doesn’t look a hand made watch of the old school, of the sort produced by George Daniels for example, which were all one-offs and essentially prototypes.
The Hand Made 1 takes it a step further with top-class decoration, once again done by hand, but once again in the Greubel Forsey style.
The tourbillon cock, for example, is milled on a pantograph, then rounded and chamfered by hand, before finally being polished by hand to a mirrored finished. Similarly, anglage is done with a series of files, resulting in gently rounded, polished bevels.
The raw tourbillon cock (left), and after it has been rounded and chamfered, but not yet polished. Image – Greubel Forsey
Unsurprisingly, the decoration is exemplary. Every element, down to the smallest detail, appears to be perfect. The high level of finishing, however, does not appear to superior to that in Greubel Forsey’s “standard” movements. So even though the technique employed are more artisanal, the resulting decoration is very, very similar.
More novel is the gratté pattern found on the base plate. While the rest of the movement is clearly traditional in style and detail, the brushstroke-like gratté finish is almost artistic.
According to Greubel Forsey, this surface decoration was developed for the Hand Made 1. “The gratté finish on the case-back side is actually inspired by the scraping done one some bench lathes or other traditional machines to get a perfectly even surface,” explains Mr Nydegger.
The German silver base plate is first flat polished on zinc plate with abrasive paste, and then finished with a tool that resembles a hand scraper. This process repeats, alternating between scraping and flat polishing, creating a progressively smoother and flatter surface. “If the black polish is not done [before scraping], then the marks will show the scratches and machining marks underneath”, explains Mr Nydegger.
From start to finish, namely from a raw German silver blank to the gratté plate, requires 70-80 hours of work according to Mr Nydegger, making it the single most time-consuming part of the watch.
Concluding thoughts
In nominal terms, the Hand Made 1 is astronomically priced at about US$900,000. But it is produced in tiny numbers – two a year – and mostly by hand, which justifies the price to a large degree. The execution of the Hand Made 1 is clearly next level, and the tangible appeal of the intrinsic quality is obvious.
Key facts and price
Greubel Forsey Hand Made 1
Case diameter: 43.5 mm
Height: 13.5 mm
Material: 18k white gold
Crystal: Sapphire
Water resistance: 30 m
Movement: Hand Made 1
Functions: Hours, minutes, seconds, and one-minute tourbillon
Frequency: 21,600 beats per hour (3 Hz)
Winding: Hand-wound
Power reserve: 60 hours
Strap: Calfskin with white gold pin buckle
Limited edition: Two to three produced annually
Availability: At Greubel Forsey retailers
Price: Approximately US$900,000
For more, visit Greubelforsey.com.
Back to top.