Interview: 800 Years of Japanese Swords and the G-Shock
Swordsmith Sadanobu Gassan speaks.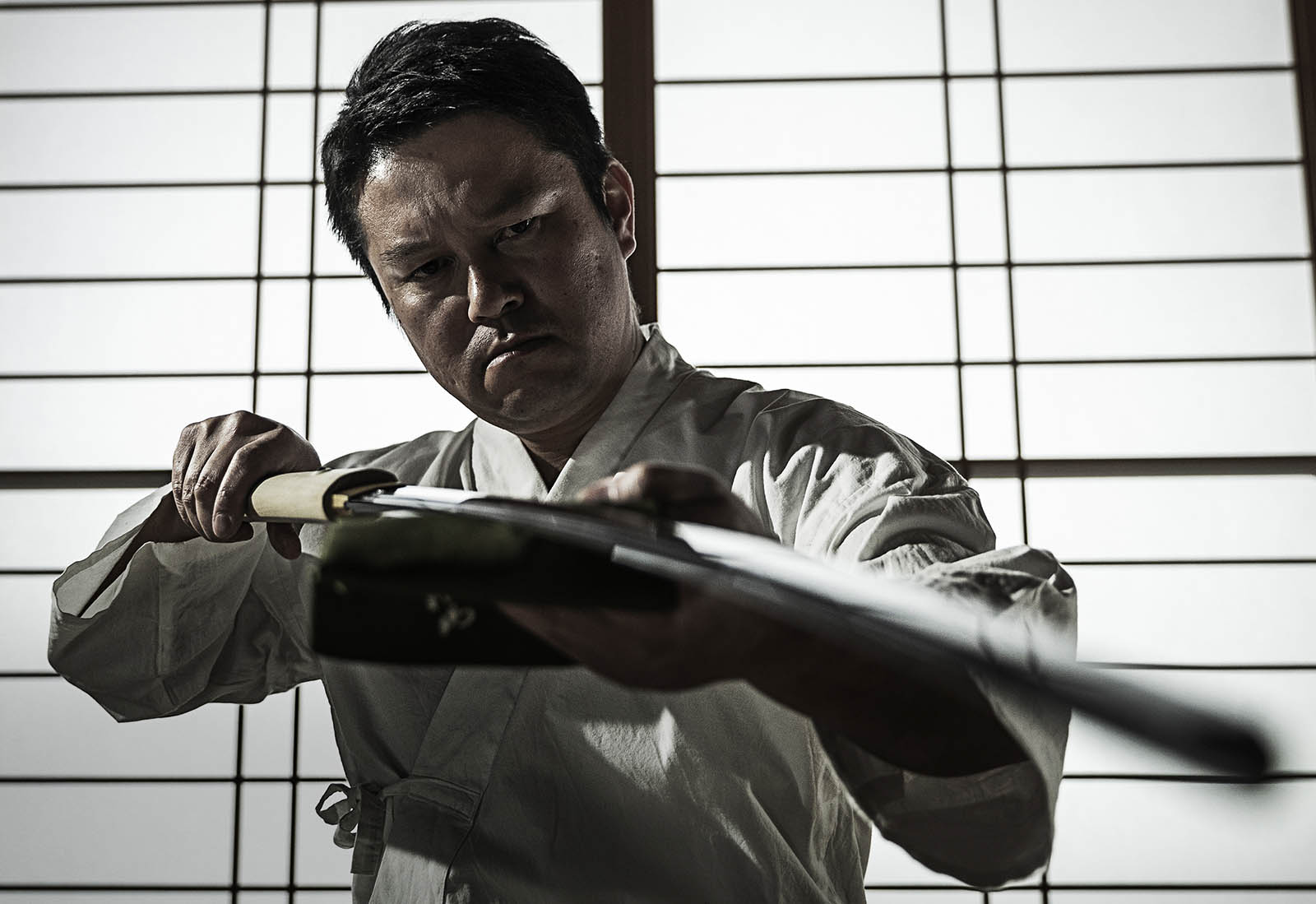
Acclaimed in ancient literature and collectible today, swords made by the Gassan school trace their lineage back centuries, as is only possible in Japan. The school originated some 800 years ago, dating back to the early Kamakura period, approximately the 13th century.
It started at the base of Mount Gassan, the highest of a trio of sacred mountains in what is now Yamagata prefecture. Though the school became dormant sometime in the 16th century, it was revived sometime in the mid 1800s by a descendant of the Gassan family in Osaka. The revival was successful and the Gassan school made swords for several Japanese emperors in the 19th and 20th century.
Six generations on, the Gassans continue their craft with Sadanobu Gassan, and his father, Sadatoshi, now based in the city of Sakurai in Nara prefecture, about six hours southwest of Tokyo.
At Baselworld 2019, Casio announced its collaboration with Sadanobu Gassan to create the G-Shock MR-G “Gassan” MRG-G2000GA, which has key parts of the case and bracelet finished by Mr Gassan himself in his workshop. In essence, it links the Gassan family’s eight hundred centuries of tradition with the latest in Japanese timekeeping technology.
We got in touch with Mr Gassan to discuss his work for G-Shock, and also the state of his ancient craft. The interview has been edited and condensed.
The G-Shock MR-G “Gassan” MRG-G2000GA
What made you want to continue in your family’s footsteps?
At a young age, I witnessed my grandfather Sadaichi and my father Sadatoshi in their bladesmithing process and I began to harbour the dream of becoming a swordsmith someday.
However, my grandfather was unable to manufacture Japanese swords in post-WW2 Japan. Similarly, being a swordsmith himself, my father endured a lot of hardship, for he lived in an era with a lack of tamahagane, the steel used for making swords. Therefore, given the difficulties faced by both my grandfather and father in their professions as swordsmiths, neither of them mentioned passing the family tradition down to me.
That being said, my childhood dreams of becoming a swordsmith remained; when I was of age and my peers were entering university or beginning work, I decided to begin training to be a swordsmith under my father, Gassan Sadatoshi.
The Gassan school has inherited about 800 years of traditional craftsmanship techniques and today, the Gassan family is the bearer of traditional sword-making techniques and sword-forging techniques.
Sadanobu Gassan at work
In your own opinion, how are Gassan nihontō [Japanese swords] different from other houses?
Since ancient times, the notable, unique quality of the Gassan nihonto has been the forged blade surface with “rolling waves pattern”, otherwise known as the Ayasugi hada [or “Gassan hada”]. The resulting magnificent craftsmanship is the distinguishing factor of Gassan nihonto from others.
What was the biggest difference when working on the metal for the G-Shock MRG-G2000GA than working on a traditional sword?
The Kanji character 鍛 is inscribed on the bracelet of the G-Shock MRG-G2000GA in a similar way to the engraved signature found on the blade base, or nakago. While there is a huge difference in the inscription on the G-Shock, as opposed to one at the base of the sword, the decoration added to the bracelet link expresses spirit of the engraved signature.
Moreover, the kanji character 鍛 infuses the spiritual mindset of the art of sword-making into the bracelet link itself. Along with its beautiful appearance inspired by traditional Japanese swords, the MRG-G2000GA-1A is one of the most technologically advanced G-Shock watches.
Engraving the “nakago”
Many traditional Japanese crafts, like maki-e for example, lack young craftsman and also young customers. How do you stay relevant and ensure that the craft continues?
It is important for more people to be exposed to and appreciate the aesthetic value and appeal of nihonto. Recently, there have been increased opportunities for collaborations with Japanese anime events as well as other exhibitions to showcase Japanese swords. Consequently, thanks to these collaborations, many people who previously had no interest have begun to attend the exhibitions and appreciate nihonto.
While public attendance at these exhibitions do not necessarily result in on-the-spot purchases, over time, say five to ten years, hopefully such events that educate professionals and consumers about nihonto will result in an increased awareness and appreciation for this craft. I think that the collaboration with G-Shock is part of the effort to slowly inculcate into the public the appeal of Japanese nihonto.
Swordsmiths overseas are also producing high quality Japanese What do you think of this development?
I am very happy that the culture of making nihonto has spread widely in the world today.
To become a licensed swordsmith in Japan, one must accumulate at least five years of training experience under the guidance of an professional as well as pass a practical training assessment. Such intensive training is for the purpose of correctly transmitting traditional Japanese sword-making techniques As a Japanese traditional swordsmith myself, I am not only forging swords, but I am constantly pondering over the importance of “tradition” when I engage in my craft.
While I acknowledge that it is not a problem for Japanese nihonto to be made overseas with an understanding of the essential skills and techniques, I hope imitations and counterfeit products would not precede traditional sword-making techniques.
Forging a blade
The membership of the All Japan Swordsmith Association has been declined in recent decades. How do you think the art of making nihonto can be preserved?
We are not necessarily looking for a lot of craftsman. I think it is necessary to create an environment where anyone with the passion and determination can train as a swordsmith in many aspects, including all other areas craftsmanship regarding Japanese swords. Besides being a swordsmith, these people can be exposed to other types of craftsmanship surrounding sword-making, such as kenshi, satoshi and shiroganeshi [crafts of the blade, sheath and guard respectively].
First and foremost, just like how I just described above, many people must have the opportunity to appreciate the value and beauty of nihonto from a swordsmith who is passionate and skilled in various aspects of Japanese sword-making.
Though Japanese sword production has been said to have a thousand years of history, and while the traditional craftsmanship and techniques of bladesmithing is very much appreciated, swordsmiths today must continue to challenge and innovate on these techniques inherited from our forefathers.
Of all the swords you have made, which one is the most memorable or special?
I regard the next sword I will forge as the best sword I will create.